加氢精制及制氢联合装置技术方案.docx
《加氢精制及制氢联合装置技术方案.docx》由会员分享,可在线阅读,更多相关《加氢精制及制氢联合装置技术方案.docx(22页珍藏版)》请在冰点文库上搜索。
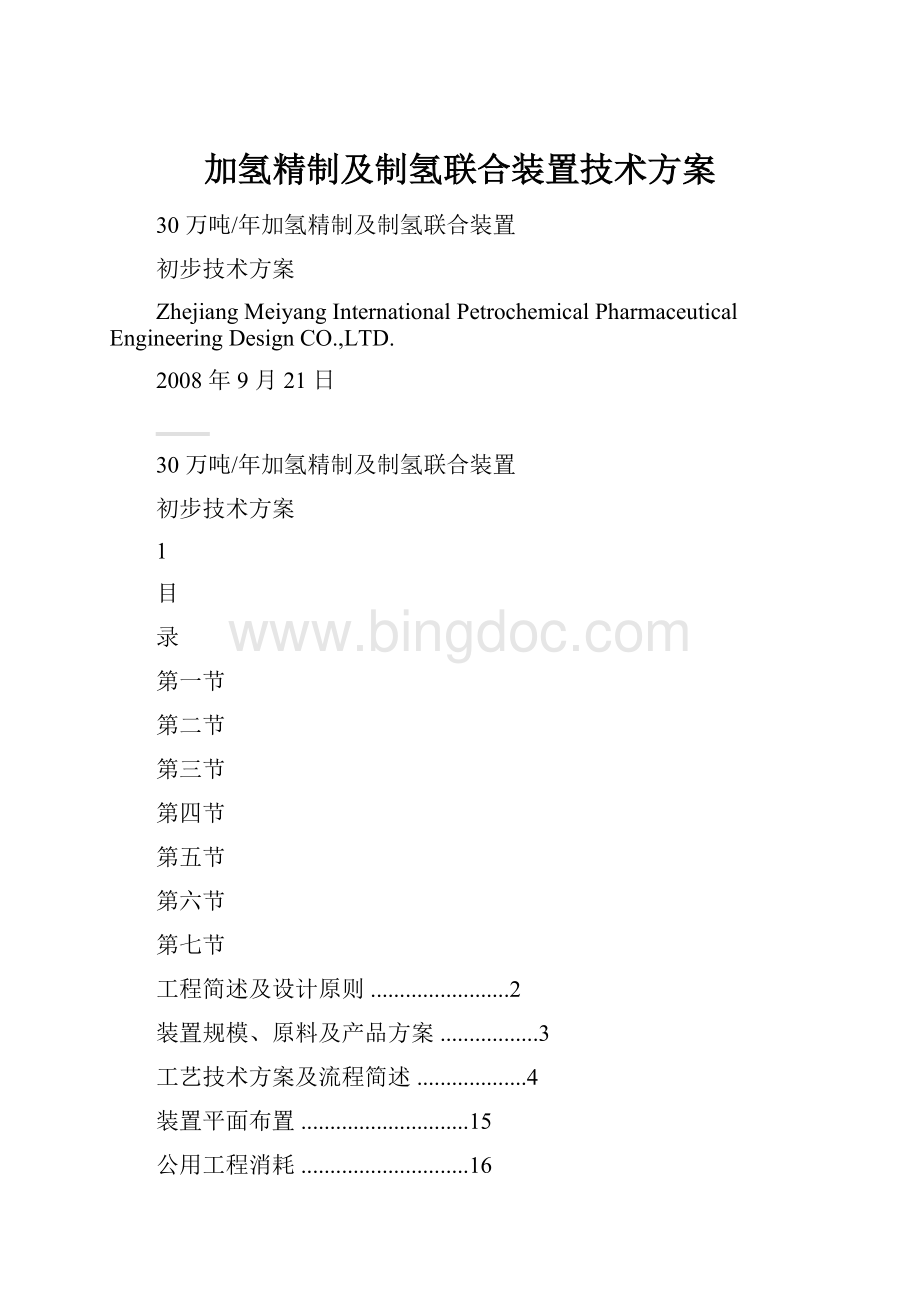
加氢精制及制氢联合装置技术方案
30万吨/年加氢精制及制氢联合装置
初步技术方案
ZhejiangMeiyangInternationalPetrochemicalPharmaceuticalEngineeringDesignCO.,LTD.
2008年9月21日
30万吨/年加氢精制及制氢联合装置
初步技术方案
1
目
录
第一节
第二节
第三节
第四节
第五节
第六节
第七节
工程简述及设计原则........................2
装置规模、原料及产品方案.................3
工艺技术方案及流程简述...................4
装置平面布置.............................15
公用工程消耗.............................16
投资估算.................................18
技术保证.................................19
3
3
30万吨/年加氢精制及制氢联合装置
初步技术方案
2
第一节
工程简述及设计原则
一、工程简述
xx公司拟建设30万吨/年汽柴油加氢精制装置,原料组成为15万吨/年催化柴油,11~12万吨/年焦化柴油,3~4万吨/年焦化汽油,根据加氢精制装置的生产规模及产品方案,需配套5000mn/h制氢装置。
(年操作时数为8000小时)。
二、设计范围及原则
1、30万吨/年汽柴油加氢精制装置、5000mn/h制氢装置按联合装置布置,制氢装置只为汽柴油加氢精制装置供氢。
设计范围为联合装置边界线以内,主要内容包括:
加氢的反应、分馏部分,制氢的转化造气、变换和PSA部分,以及联合装置的变配电室和中心控制室。
加氢精制装置的含硫气体送至催化的产品精制装置与催化干气一起脱硫。
脱硫后的气体作为制氢装置的主原料,石脑油作为辅助原料。
2、加氢精制装置的目的以脱硫、脱氮和烯烃饱和为主,不考虑加氢改质。
采用国内催化剂、设备和工艺技术。
3、制氢装置造气单元采用催化干气蒸汽转化制氢专有技术;净化单元采用国内变压吸附(PSA)技术。
4、按年开工8000小时计算小时加工量。
5、严格执行国家有关工程建设质量管理法规,确保装置安全、稳定、长周期运行,减少维护维修的工作量,从而提高整体的经济效益。
6、认真贯彻国家关于环境保护和劳动保护的法规和要求。
认真贯彻安全第一预防为主的指导思想。
对生产中易燃易爆有毒有害物质
3
30万吨/年加氢精制及制氢联合装置
初步技术方案
3
设置必要的防范措施。
三废排放要符合国家现行有关标准和法规。
7、装置工艺过程控制采用DCS,以提高装置的自动化水平。
8、为节约外汇,主要设备和材料均立足于国内供货。
第二节
装置规模、原料及产品方案
一、加氢精制装置
1、生产规模及实际加工量
生产规模为:
30万吨/年。
其实际加工量应为:
30万吨/年。
2、原料组成
催化柴油15万吨/年;
焦化柴油11~12万吨/年;
焦化汽油3~4万吨/年。
3、燃料
以脱硫气体为燃料,不考虑使用重质燃料油。
4、产品方案
以脱硫、脱氮和烯烃饱和为主,不考虑加氢改质。
生产低硫、低氮、安定性较好的汽、柴油调和组分。
二、制氢装置
1、生产规模及实际加工量
根据加氢精制装置的生产规模及产品方案,制氢装置的实际产氢量应为:
0.30~0.36万吨/年。
其生产规模应确定为:
5000mn/h工业氢。
(年操作时数为8000小时)。
30万吨/年加氢精制及制氢联合装置
初步技术方案
4
2、原料
以脱硫后的催化干气、加氢干气(或焦化干气)等气体作为制氢装置的主原料,石脑油作为辅助原料。
原来的规格要求如下:
脱硫气体:
总硫含量<50ppm。
石脑油:
烯烃<1%mol,芳烃含量<13%,环烷烃<36%,干点<180℃,总硫含量<100ppm。
3、燃料
装置正常生产时,燃料主要由PSA的解吸气提供,不足部分由脱硫气体补充。
4、产品方案
装置主要产品为工业氢,副产的变压吸附(PSA)解吸气作为转化炉的燃料。
工业氢规格:
组成:
组分V%
H
2
≥99.99
CH
4
≤5ppm
CO≤10PPm
CO
2
≤5PPm
H
2
O≤10PPm
∑
100.00
30万吨/年加氢精制及制氢联合装置
初步技术方案
5
第三节
工艺技术方案及流程简述
一、加氢精制装置
(一)工艺技术方案
根据原料的组成,焦化汽油的量较少,不宜单独进料,因此考虑采用与柴油混合进料的加工方式,有利于降低装置的投资。
汽柴油加氢精制的工艺和工程技术非常成熟,其核心是加氢精制催化剂。
目前,北京石油化工科学研究院和抚顺石油化工研究院分别开发了各自的加氢精制技术和加氢精制催化剂RN-1或RN-10和FH-5A或FH-98,采用上述加氢精制技术可以提高原料储存安定性及热安定性,同时可少量提高十六烷值(1-3个单位),降低硫含量。
FH-98与参比剂-2、参比剂-3加氢活性比较**
催化剂
FH-98
参比剂-2
参比剂-3
油品名称
原料油
精制油
精制油
精制油
氮含量,µg/g
1226
98
135
126
脱氮率,m%
92.0
87.5
89.7
**工艺条件:
氢分压6.0MPa、体积空速2.0h
-1
、氢油体积比500:
1、反应温度:
350°
C
推荐加氢精制催化剂为FH-98,以取得高收率。
操作条件如下:
反应器主要操作条件
反应器
加氢精制
(保护剂段/精制段)
反应器入口氢分压力,MPa
6.4
体积空速,h-1
20.0/2.0-2.2
反应器入口气油体积比
500
30万吨/年加氢精制及制氢联合装置
初步技术方案
6
*精制段温度根据原料量及氮含量变化调整。
所采用技术方案的特点如下:
1、采用国产催化剂:
采用抚顺石油化工科学研究院的FH-5A或FH-98或北京石油化工科学研究院RN-10或其他性能相当的国产催化剂。
催化剂再生按器内再生考虑。
2、氢气和原料油混合后与反应流出物换热以提高换热器的传热效率,然后经加热炉升温,以降低原料油在加热炉炉管内的结焦程度。
3、采用技术成熟的双壳程换热器,提高换热器传热效率。
4、装置内原料油缓冲罐采用燃料气保护,使原料油与空气隔离,控制原料油氧含量,减轻高温部位结焦程度。
5、采用热壁型式和新型内部构件的反应器,使进入催化剂床层的物流分配和催化剂床层的径向温度分布均匀。
6、采用三相(油、气、水)分离的立式高压分离器。
7、在反应流出物空冷器上游侧设置软化水注入点,以防止低温部位铵盐析出。
8、柴油汽提塔采用水蒸汽汽提,塔顶设注缓蚀剂设施,以减轻塔顶流出物中硫化氢对汽提塔顶系统的腐蚀。
9、为了充分利用热量,减少高压换热器台数,设计考虑汽提塔进料先与汽提塔底柴油换热,然后再与反应流出物换热至入塔温度。
10、新氢压缩机和循环氢压缩机均采用电动往复式,各设一台备机。
11、催化剂预硫化采用气相硫化方法。
催化剂再生采用氮气-空气
30万吨/年加氢精制及制氢联合装置
循环再生方式,并设置相应设施。
初步技术方案
7
12、再生过程的注碱系统采用碱液循环流程,降低碱耗,减少污染。
(二)工艺流程简述
1、反应部分
自罐区来的四路原料油在原料油缓冲罐液面和流量控制下,通过原料油过滤器除去原料中大于25微米的颗粒后,进入原料油缓冲罐,原料油缓冲罐用燃料气气封。
自原料油缓冲罐来的原料油经加氢进料泵增压后,在流量控制下,经反应流出物/原料油换热器换热后,与混合氢混合进入反应流出物/反应进料换热器,然后经反应进料加热炉加热至反应所需温度,进入加氢精制反应器。
该反应器设置两个催化剂床层,床层间设有注急冷氢设施。
自加氢精制反应器出来的反应流出物经反应流出物/反应进料换热器、反应流出物/低分油换热器、反应流出物/原料油换热器依次与反应进料、低分油、原料油换热,然后经反应流出物空冷器及水冷器冷却至45℃,进入高压分离器。
为了防止反应流出物中的铵盐在低温部位析出,通过注水泵将脱氧水注到反应流出物空冷器上游侧的管道中。
冷却后的反应流出物在高压分离器中进行油、气、水三相分离。
高分气(循环氢)经循环氢压缩机入口分液罐分液后,进入循环氢压缩机升压,然后分两路:
一路作为急冷氢进反应器;一路与来自新氢压缩机的新氢混合,混合氢与原料油混合作为反应进料。
含硫、含氨污水自高压分离器底部排出至酸性水汽提装置处理。
高分油相在液位控制下经减压调节阀进入低压分离器,其闪蒸气体排至工厂燃料气管网。
30万吨/年加氢精制及制氢联合装置
初步技术方案
8
低分油经精制柴油/低分油换热器和反应流出物/低分油换热器分别与精制柴油、反应流出物换热后进入柴油汽提塔。
入塔温度用反应流出物/低分油换热器旁路调节控制。
新氢经新氢压缩机入口分液罐经分液后进入新氢压缩机,经两级升压后与循环氢混合。
2、分馏部分
从反应部分来的低分油经精制柴油/低分油换热器、反应流出物/低分油换热器换热至275℃左右进入柴油汽提塔。
塔底用1.0MPa过热蒸汽汽提,塔顶油气经汽提塔顶空冷器和汽提塔顶后冷器冷凝冷却至40℃,进入汽提塔顶回流罐进行气、油、水三相分离。
闪蒸出的气体排至燃料气管网。
含硫含氨污水与高分污水一起送出装置。
油相经汽提塔顶回流泵升压后一部分作为塔顶回流,一部分作为粗汽油去稳定塔。
从汽提塔顶回流罐来的粗汽油经稳定汽油(精制石脑油)/粗汽油换热后进入汽油稳定塔。
稳定塔底用精制柴油作稳定塔重沸器热源,稳定塔塔顶油气经稳定塔顶水冷器冷凝冷却至40℃,进入稳定塔顶回流罐进行气、油、水三相分离。
闪蒸出的气体排至燃料气管网。
含硫含氨污水与高分污水一起送出装置。
油相经汽提塔顶回流泵升压后作为塔顶回流。
为了抑制硫化氢对塔顶管道和冷换设备的腐蚀,在塔顶管道采用注入缓蚀剂措施。
缓蚀剂自缓蚀剂罐经缓蚀剂泵注入塔顶管道。
塔底精制柴油经柴油泵增压后与低分油换热至80℃左右,然后进入柴油空冷器冷却至50℃,经柴油脱水罐脱水后出装置。
3、催化剂预硫化流程
为了使催化剂具有活性,新鲜的或再生后的催化剂在使用前都必
30万吨/年加氢精制及制氢联合装置
初步技术方案
9
须进行预硫化。
本设计采用气相硫化方法,硫化剂为二甲基二硫化物(DMDS)。
催化剂硫化前先用硫化剂泵把DMDS抽入硫化剂罐中。
硫化时,系统内氢气经循环氢压缩机按正常操作路线进行循环。
DMDS自硫化剂罐来,经计量后与来自反应流出物/反应进料换热器的氢气混合后,进入反应进料加热炉,按催化剂预硫化升温曲线的要求升温,通过反应器中催化剂床层进行预硫化。
自反应器来的流出物经换热器和空冷器冷却后进入高压分离器进行分离。
气体自高压分离器顶部排出,大部分进入循环机进行循环,小部分排至装置外。
催化剂预硫化过程中产生的水从高压分离器底部间断排出。
4、催化剂再生流程
催化剂在运转过程中将逐渐失去活性,为了使失活的催化剂恢复活性,本装置设置了催化剂器内再生设施,催化剂再生采用氮气-空气循环再生方法。
催化剂再生时,反应系统充入氮气,由循环机进行循环,催化剂再生烧焦过程中所需的非净化压缩空气由新氢压缩机供给。
催化剂再生流程中采用了注氨、注碱措施。
液氨由液氨罐经液氨泵升压后注入到反应器出口管道中。
新鲜碱液由槽车经注碱泵升压后注入到混合器上游侧。
碱液与再生气经混合器充分混合后进入高压分离器。
高压分离器气体一部分排入大气,大部分在反应系统内部进行循环。
高压分离器底部碱液一部分作为废碱液经减压后送出装置。
另一部分碱液经碱液循环泵与碱液泵出口新鲜碱液混合进行碱液循环。
附图1
加氢装置反应部分工艺流程图。
30万吨/年加氢精制及制氢联合装置
初步技术方案
10
附图2
加氢装置分馏部分工艺流程图。
二、制氢装置
(一)工艺技术方案
以轻烃为原料制取工业氢,国内外均认为蒸汽转化法为最佳方案。
经过多年的生产实践,目前已积累了许多成功的工程设计与操作经验。
该装置亦采用蒸汽转化法制氢。
轻烃蒸汽转化制氢装置所配套的净化工艺主要可分为两种,即化学净化法(常规净化法)和变压吸附净化法(PSA净化法)。
由于以催化干气为原料,其中有较多的惰性气体,为保证氢气产品的纯度,该装置须采用变压吸附净化法(PSA净化法)。
典型的催化干气组成如下:
序号
组成
催化干气
摩尔分率(干基)
1
H2
26.7535
2
C1
27.4549
3
C2
10.4208
4
C3
0.7014
5
IC4
1.3026
5
NC4
0.1002
7
IC5
0.3006
8
C2H4
13.2265
9
C3H6
1.8036
10
CO2
2.7054
30万吨/年加氢精制及制氢联合装置
初步技术方案
11
11
N2
14.2285
12
O2
1.0020
主要工艺过程操作条件1、加氢反应器
介质
管程
原料气
壳程
热载体
入口温度℃250250出口温度℃380350入口压力MPa(abs)3.200.6出口压力MPa(abs)3.180.65
加氢催化剂装量m
3
4
2、脱硫反应器
入口温度℃370出口温度℃360入口压力MPa(abs)3.17出口压力MPa(abs)3.15
脱硫剂装量m
3
5.0
3、转化炉辐射段
入口温度℃500出口温度℃820入口压力MPa(abs)3.0出口压力MPa(abs)2.75
30万吨/年加氢精制及制氢联合装置
初步技术方案
12
碳空速h-1862水碳比mol/mol3.5
催化剂装量m
3
2.4
4、中温变换反应器
入口温度℃360出口温度℃415入口压力MPa(abs)2.72出口压力MPa(abs)2.70
空速(干)h
-1
2400
催化剂装量m
3
3.1
5、PSA单元操作条件
入口温度℃40
入口压力MPa(G)2.5
产氢压力MPa(G)2.4
主要工艺技术特点
1、采用催化干气作为装置原料,和轻石脑油作为制氢装置的原料相比,提高了原料产氢率,降低了原料和燃料消耗。
2、优化装置设计,合理选择工艺参数,采用较高的转化出口温度(820℃),增加转化深度,提高单位原料的产氢率,从而降低原料和燃料消耗;选用较低的水碳比(3.5),进一步降低转化炉的燃料消耗。
3、原料精制部分烯烃饱和反应放出的热量采用热载体取热方案,既省掉一台固定床反应器,又能控制加氢反应器出口温度在
30万吨/年加氢精制及制氢联合装置
初步技术方案
13
350~380℃,保证了ZnO脱硫温度要求。
4、在原料气的预热方面,采用开工加热炉和原料预热炉二合一的方案。
不仅增加了原料预热温度调节的灵活性,又增加了中压蒸汽的产量。
5、为了提高装置的可靠性,确保装置长周期安全运行,转化催化剂选用齐鲁化工研究院研制生产的蒸汽转化催化剂Z402/Z405。
6、一氧化碳变换部分仅采用中温变换流程,不采用低温变换流程,以降低装置投资,简化制氢流程,缩短开工时间。
7、采用三合一的产汽流程(即烟道气、转化气、中变气的产汽系统共用一台汽包),简化了余热回收流程,降低了装置投资。
8、优化换热流程,合理利用余热能位,提高有效能效率。
1利用转化炉烟道气高温位余热预热原料气,利用烟道气和转化气的高温位余热发生3.5MPa中压蒸汽。
所产蒸汽一部分作为工艺用汽,多余部分减温减压外输至低压蒸汽管网。
2利用中变气高温位余热预热锅炉给水,以增加中压蒸汽产量。
⑶利用烟道气低温位余热预热燃烧空气,以降低转化炉的燃料用
量。
⑷在维持合理传热温差的前提下,降低排烟温度,提高转化炉、原料预热炉的热效率,以降低燃料消耗。
9、回收工艺冷凝水,减少装置脱盐水用量。
在变换气冷却过程中将产生大量的冷凝水,这部分冷凝水如直接排放,将会污染环境或增加污水处理场负担。
本设计将工艺冷凝液经汽提塔汽提后直接进入除氧器,除氧后作为锅炉给水。
这样既保护了环境,又减少了脱盐水用量。
10、采用U型管双壳程换热器,加深换热深度,提高热效率。
30万吨/年加氢精制及制氢联合装置
初步技术方案
14
11、采用PSA净化工艺,简化了制氢流程,提高了氢气质量,降低了装置能耗。
(二)工艺流程简述
1、进料系统
原料气由装置外进入原料气缓冲罐,然后经压缩机压缩后进入原料气脱硫部分。
2、烯烃饱和及脱硫部分
进入烯烃饱和及脱硫部分的原料气经原料气加热炉预热至250℃左右,进入列管式加氢反应器中发生烯烃饱和及有机硫转化反应。
烯烃饱和反应是强放热反应,反应放出的热量通过壳程的热载体取热,并控制出口温度为350~380℃。
经过烯烃饱和以及有机硫转化为无机硫后进入氧化锌脱硫反应器脱除硫化氢。
精制后的气体硫含量小于0.2PPm,烯烃含量小于1%,然后进入转化部分。
3、转化部分
精制后的原料气按水碳比3.5与3.5MPa水蒸汽混合,再经转化炉对流段予热至500℃,进入转化炉辐射段。
在催化剂的作用下,
发生复杂的水蒸汽转化反应。
整个反应过程是吸热的,所需热量由分布在转化炉顶部的气体燃料烧嘴提供,出转化炉820℃高温转化气经转化气蒸汽发生器换热后,温度降至360℃,进入中温变换部分。
4、变换部分
来自转化气蒸汽发生器约360℃的转化气进入中温变换反应器,
30万吨/年加氢精制及制氢联合装置
初步技术方案
15
在催化剂的作用下发生变换反应,将变换气中CO含量降至3%左右。
中变气经锅炉给水第二换热器、锅炉给水第一换热器、脱盐水预热器进行热交换回收大部分余热后,再经中变气水冷却器冷却至40℃,并经分水后进入PSA单元。
5、PSA单元
来自造气单元压力约2.5MPa(G)、温度40℃中变气进入界区后,自塔底进入吸附塔中正处于吸附工况的塔(始终同时有两台),在其中多种吸附剂的依次选择吸附下,一次性除去氢以外的几乎所有杂质,获得纯度大于99.99的产品氢气,经压力调节系统稳压后送出装置。
当吸附剂吸附饱和后,通过程控阀门切换至其它塔吸附,吸附饱和的塔则转入再生过程。
在再生过程中,吸附塔首先经过连续四次均压降压过程尽量回收塔内死空间氢气,然后通过顺放步序将剩余的大部分氢气放入顺放气罐(用作以后冲洗步序的冲洗气源),再通过逆放和冲洗两个步序使被吸附杂质解吸出来。
逆放解吸气进入解吸气缓冲罐,冲洗解吸气进入解吸气缓冲罐,然后经调节阀调节混合后稳定地送往造气单元的转化炉作为燃料气。
6、热回收及产汽系统
来自装置外的脱盐水经脱盐水预热器预热后与来自酸性水气提塔的净化水混合后进入除氧器。
除氧水经中压锅炉给水泵升压后,再经锅炉给水第一预热器和锅炉给水第二预热器预热后进入中压汽包。
锅炉水通过自然循环的方式分别经过转化炉对流段的产汽段、水保护段及转化气蒸汽发生器产生中压蒸汽。
所产生的中压蒸汽在转化炉对流段蒸汽过热段过热至430℃离开汽包。
一部分蒸汽作为工艺蒸汽使用;另一部分减温减压至1.0MPa进入全厂低压蒸汽管网。
3
30万吨/年加氢精制及制氢联合装置
第四节
初步技术方案
装置平面布置
16
一、遵守的主要标准、规范
《石油化工企业设计防火规范》GB50160-92(1999年版)《爆炸和火灾危险环境电力装置设计规范》GB50058-92
《石油化工企业建筑设计规范》SHJ17-90
《石油化工企业工艺装置设备平面布置设计通则》SHJ11-89二、平面布置
根据金澳科技(湖北)化工有限公司公司30万吨/年加氢精制及制氢联合装置的规划,30万吨/年汽柴油加氢精制装置、5000mn/h制氢装置按联合装置布置,可布置在汽柴油加氢精制及制氢装置的预留地内。
三、装置占地:
见附图5总平面布置图,占地约1.62公顷(含装置周边道路面积的一半)。
第五节
公用工程消耗
一、加氢精制装置公用工程消耗
序号
项目
单位
数量
备注
1
循环水
t/h
145.30
连续
2
生活水
t/h
2
间断
3
电
Kwh/h
963.40
连续
3
3
3
3
3
3
30万吨/年加氢精制及制氢联合装置
初步技术方案
17
4
1.0MPa蒸汽
t/h
0.44
间断
5
燃料气
Mn/h
327
连续
6
净化压缩空气
Mn/h
240.00
连续
7
非净化压缩空气
mn/h
900
间断
8
软化水
t/h
1.00
9
氮气
mn
4000
间断
二、制氢公用工程消耗
序号
名称
单位
数量
备注
1
催化干气
mn/h
2315
连续(原料)
2
燃料气
mn/h
275
连续
3
循环水
t/h
205
连续
4
生活水
t/h
2
间断
5
除盐水
t/h
5.94
连续
6
电6000V
KWh/h
140
连续
380V
KWh/h
77.55
220V
KWh/h
15
照明及仪表
7
非净化压缩空气
m3n/h
200
间断
8
净化压缩空气
m3n/h
200
连续
9
1.0MPa蒸汽
t/h
-3.6
外输
1.0MPa蒸汽
t/h
5
消防及吹扫
10
氮气
m3n/h
180
间断
)
)
30万吨/年加氢精制及制氢联合装置
初步技术方案
18
第六节
一、加氢精制装置工程费用
投资估算
序号
工程或费用名称
估算价值(万元
比例%
1
构筑物工程
851
13.7
2
静止设备及安装工程
1222
19.6
3
机械设备及安装工程
1040
16.7
4
加热炉类设备及安装工程
406
6.5
5
电气设备及安装工程
670
10.8
6
自控设备及安装工程
912
14.6
7
工艺管道及安装工程(含给排水)
689
11.1
8
催化剂及化学药剂
436
7.0
合计
6226
100.0
二、制氢装置工程费用
序号
工程或费用名称
估算价值(万元
比例%
1
构筑物工程
216
6.38
30万吨/年加氢精制及制氢联合装置
初步技术方案
19
2
静止设备及安