换热器用铜管企业标准.docx
《换热器用铜管企业标准.docx》由会员分享,可在线阅读,更多相关《换热器用铜管企业标准.docx(20页珍藏版)》请在冰点文库上搜索。
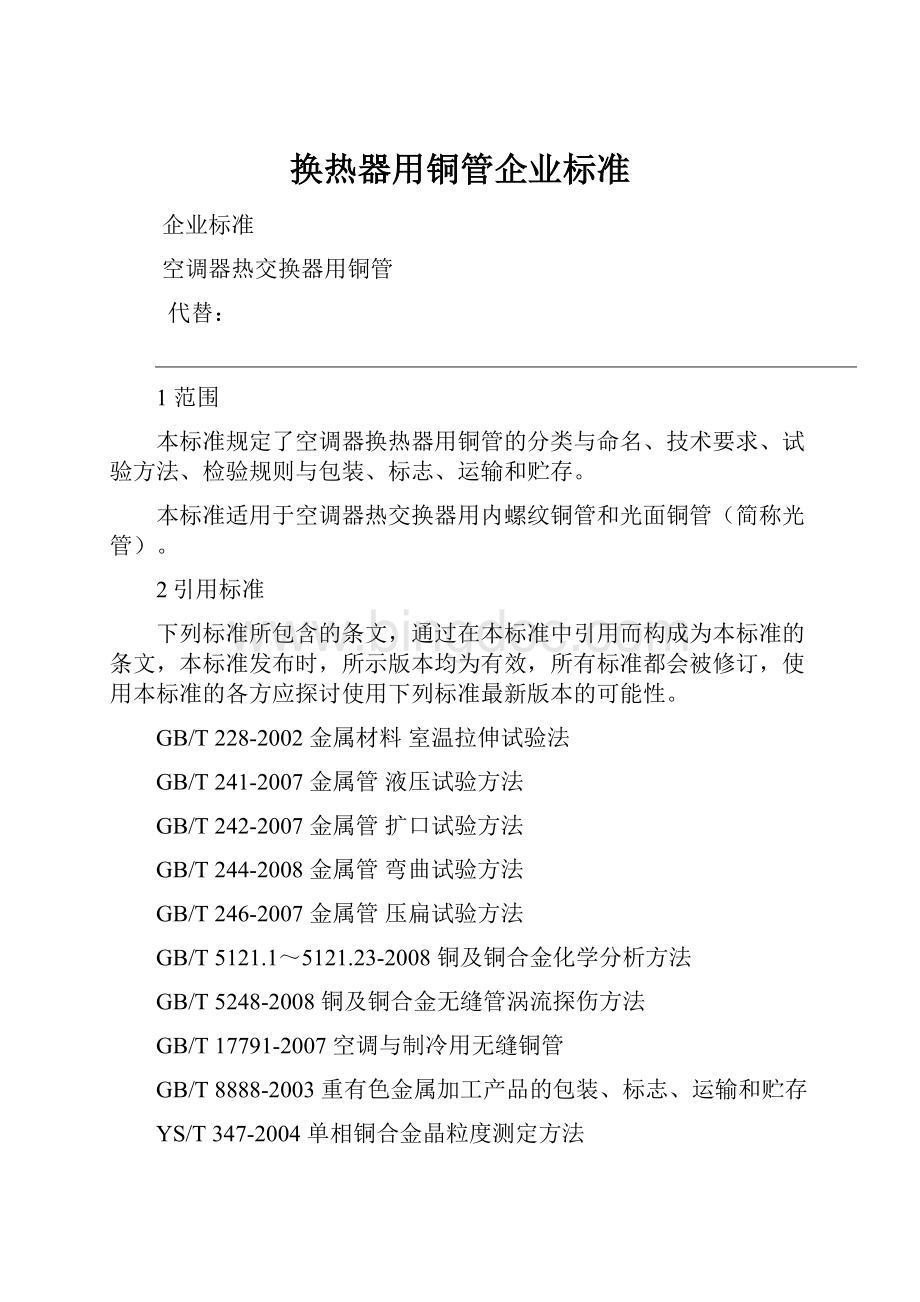
换热器用铜管企业标准
企业标准
空调器热交换器用铜管
代替:
1范围
本标准规定了空调器换热器用铜管的分类与命名、技术要求、试验方法、检验规则与包装、标志、运输和贮存。
本标准适用于空调器热交换器用内螺纹铜管和光面铜管(简称光管)。
2引用标准
下列标准所包含的条文,通过在本标准中引用而构成为本标准的条文,本标准发布时,所示版本均为有效,所有标准都会被修订,使用本标准的各方应探讨使用下列标准最新版本的可能性。
GB/T228-2002金属材料室温拉伸试验法
GB/T241-2007金属管液压试验方法
GB/T242-2007金属管扩口试验方法
GB/T244-2008金属管弯曲试验方法
GB/T246-2007金属管压扁试验方法
GB/T5121.1~5121.23-2008铜及铜合金化学分析方法
GB/T5248-2008铜及铜合金无缝管涡流探伤方法
GB/T17791-2007空调与制冷用无缝铜管
GB/T8888-2003重有色金属加工产品的包装、标志、运输和贮存
YS/T347-2004单相铜合金晶粒度测定方法
3术语
3.1圆度
管材任一端面上测量的最大直径与最小直径的差值。
3.2内螺纹铜管
管材外表面光滑,内表面具有一定数量、一定规则螺纹的铜管。
3.3光面铜管(又称光身铜管,简称光管)
管材内外表面光滑的铜管,又称光身铜管,简称光管
3.3名义壁厚
内螺纹铜管按每米克重理论值计算出相应公称外径的无缝光面铜管的壁厚值。
3.4直管(定尺管)
直条状管材。
3.5盘管
绕成一系列相邻圈的整根管子。
4分类与命名
4.1产品分类
空调器热交换器用铜管一般分为光面铜管(简称光管)和内螺纹管。
4.2管材的牌号、状态和供货形状
管材的牌号、状态和供货形状应符合表1的规定。
表1产品的牌号、状态各供货形状
牌号
状态
供货形状
TP2
轻软(M2)、软(M)
直管(定尺管)
盘管
4.3标记方法与示例
标记方法如下:
××
铜管的生产执行标准
盘管用C来表示,直管为铜管长度
铜管的名义壁厚(光管用壁厚表示,螺纹管表示
底壁厚+齿高—螺旋角)
铜管的外径
铜管的牌号
铜管的种类
标记示例:
示例1:
外径为9.52mm,壁厚为0.35mm、牌号为TP2M,生产标准为Q/ZGJZ2-2009的光管,长度为1645mm,标记为:
光管TP2Mφ9.52×0.35×1645Q/ZGJZ2-2009
示例2:
外径为7.00mm,底壁厚为0.28mm、齿高为0.15mm、螺旋角为18º、牌号TP2M、生产标准为Q/ZGJZ2-2009的内螺纹铜盘管标注为:
内螺纹TP2Mφ7.00×0.28+0.15—18º×CQ/ZGJZ2-2009
5技术要求
5.1结构尺寸
5.1.1内螺纹铜管尺寸及偏差:
内螺纹铜管的齿形图示见图1
热交换器用内螺纹铜管的尺寸及允许偏差应符合表2的规定,表3为本标准推荐规格。
表2尺寸及允许偏差
名称
尺寸
允许偏差
平均外径D,mm
5≤D<9
±0.04
9≤D<16
±0.05
内径d,mm
—
±0.03
名义壁厚T,mm
0.30~0.45
—
圆度,mm
—
--
底壁厚TW,mm
0.25~0.35
±0.03
齿高Hf,mm
0.15~0.28
±0.02
齿顶角α,(º)
30~60
±5
螺旋角β,(º)
7~30
±2
槽底宽W,mm
0.10~0.20
±0.03
0.20~0.30
±0.04
螺纹数n
40~75
0
每米克重,g/m
—
±2
注:
1表中内径d=D-(TW+Hf)×2;
2每米克重理论值由供需双方认可;
3如有特殊要求由供需双方协商确定。
表3推荐规格名义尺寸
序号
规格,mm
外径D
内径d
底壁厚TW
齿高Hf
总壁厚TWT
螺旋角β
齿顶角α
螺纹数n
平均壁厚
米克重
mm
mm
mm
mm
mm
(º)
(º)
条
mm
g/m
1
Φ5.00×0.20+0.15-18º
5
4.3
0.2
0.15
0.35
18
40
40
0.25
33
2
Φ6.35×0.25+0.15-18º
6.35
5.55
0.25
0.15
0.4
18
40
45
0.295
50
3
Φ7.0×0.25+0.10-15º
7
6.3
0.25
0.1
0.35
15
35
65
0.28
53
4
Φ7.0×0.25+0.18-18º
7
6.14
0.25
0.18
0.43
18
40
50
0.3
57
5
Φ7.0×0.27+0.15-18º
7
6.16
0.27
0.15
0.42
18
53
60
0.32
62
6
Φ7.0×0.28+0.15-18º
7
6.14
0.28
0.15
0.43
18
50
60
0.33
62
7
Φ7.94×0.28+0.15-18º
7.94
7.08
0.28
0.15
0.43
18
53
60
0.35
72
8
Φ7.94×0.25+0.18-18º
7.94
7.08
0.25
0.18
0.43
18
35
60
0.305
65
9
Φ9.52×0.28+0.15-18º
9.52
8.66
0.28
0.15
0.43
18
53
60
0.33
85
10
Φ9.52×0.27+0.16-18º
9.52
8.66
0.27
0.16
0.43
18
30
70
0.32
82
11
Φ9.52×0.28+0.12-15º
9.52
8.72
0.28
0.12
0.4
15
50
65
0.305
80
12
Φ9.52×0.30+0.20-18º
9.52
8.52
0.3
0.2
0.5
18
50
60
0.36
93
13
Φ12.7×0.41+0.25-18º
12.7
11.38
0.41
0.25
0.66
18
35
75
0.485
166
14
Φ15.88×0.45+0.30-18º
15.88
14.38
0.45
0.3
0.75
18
53
74
0.56
239
5.1.2光管的尺寸及偏差
光铜管的结构示意图见图2
热交换器用光管的尺寸及偏差应符合表4的规定
表4单位:
mm
检验项目
尺寸规格(外径×壁厚)
外径偏差
壁厚偏差
直管
φ7×0.35
±0.05
±0.03
φ7.94×0.35
φ9.52×0.35
φ7×0.30
±0.05
±0.02
φ7.94×0.30
φ9.52×0.30
5.1.3定尺管的长度尺寸及偏差,管材的定尺或倍尺长度应在不定尺范围内,倍尺长度应加入锯切量,每一锯切量为5mm,直管定尺允许偏差应符合表5的规定。
表5直管定尺允许偏差单位:
mm
长度
允许偏差
400~600
+1
0
>600~1800
+1
0
>1800~4000
+2
0
>4000~10000
+5
0
5.1.4圆度
铜管的圆度应符合表6的规定
表6铜管的圆度公差单位:
mm
公称外径
圆度
5
≦0.14
7
≦0.21
7.94
≦0.23
9.52
≦0.28
12.7
≦0.37
15.88
≦0.48
5.2化学成分
管材的化学成分应符合表7的规定。
表7管材的化学成分
牌号
主要成分,(%)
杂质成分,不大于,(%)
TP2
Cu
P
S
Bi
Sb
As
Fe
Ni
Pb
Sn
Zn
O
≥99.90
0.015~0.040
0.005
0.001
0.002
0.002
0.005
0.005
0.005
0.005
0.005
0.01
5.3外观质量
5.3.1内外表面质量
管材的内外表面应清洁、光亮、无针孔、裂缝、起皮、气泡、粗拉道、夹杂、铜粉、积碳层、绿锈、脏污、水珠和严重的氧化膜(内螺纹铜管内表面齿形均匀)。
不允许存在明显的划伤、凹坑和斑点等影响使用的有害缺陷。
内外表面颜色要求不能呈(灰)黑色、蓝色、紫红色。
呈轻微灰黑色时不能被擦除,不能有油污流出。
用气吹内外表面不得有粉沫,且吹后表面不得变成白色。
5.3.2管材质量
管材不应有分层和明显呈暗裂状粗燥感。
端部应锯切平整,允许有轻微的毛刺。
5.4性能要求
5.4.1压扁试验
观察压扁后的试样,试样不应有肉眼可见的轻微裂纹。
5.4.2清洁度
铜管内表面残留物应不大于28mg/m²。
5.4.3室温力学性能与晶粒度
铜管力学性能与晶粒度应符合表8的规定。
表8
牌号
材料状态
抗拉强度(Mpa)
延伸率δ(%)
平均晶粒度(mm)
TP2
M、M2
220~255
≧43
0.015~0.040
5.4.4扩口性能
采用60º的冲锥,扩口率为30%,扩口后试样不应产生肉眼可见的裂纹或裂口。
5.4.5弯曲试验
试验铜管在弯心直径为铜管公称外径1.5倍的条件下,弯曲180°一次不应产生皱折和裂纹。
5.4.6水压试验
铜管经表压为5.0Mpa(50Kgf/cm2)的水压,历时保压5min的试验后,铜管外表面不应有任何渗漏现象,并且试验后铜管不应有产生永久变形(膨胀),然后缓慢加压至13.0Mpa(表压)以上,保压1min,不得破裂但允许产生永久变形(膨胀)。
5.4.7涡流探伤
5.4.7.1直管应在探伤设备信号装置上不发出报警信号。
盘管的报警信号允许次数为每盘5次以内;报警信号深色标记长度不小于300mm。
喷墨标记必须清晰可见。
喷墨沿铜管圆周分布,且不少于2/3圆周
5.4.7.2涡流探伤检测时,标准样管人工缺陷为通孔,其孔径应符合表9的规定。
表9标准样管人工缺陷孔径单位:
mm
管外径
钻孔直径
5.00~9.00
0.3
>9.00~13.00
0.4
6试验方法
6.1外观质量
以目测进行检验。
6.2结构尺寸
结构尺寸用相应精度的工具进行检验。
内表面螺纹尺寸及偏差的测量方法按附录A(标准的附录)的规定进行。
6.3性能试验
6.3.1化学成分分析
管材的化学成分仲裁分析方法按GB/T5121规定进行。
6.3.2压扁试验
截取试样或在管上直接进行将铜管夹在两平板之间,并连续施加压力,直至两平板间距为管壁厚的3倍。
铜管的压扁试验按GB/T246的规定。
6.3.3清洁度试验
铜管的管内清洁度试验按附录B的规定。
6.3.4力学性能
铜管的力学性能按GB/T228的规定。
6.3.5晶粒度
铜管的晶粒度按YB/T347规定。
6.3.6扩口试验
铜管的扩口试验按GB/T242规定进行。
6.3.7弯曲试验
铜管的弯曲试验按GB/T244的规定。
6.3.8水压试验
铜管的水压试验按GB/T241的规定。
6.3.9涡流探伤
涡流探伤试验按GB/T5248的规定。
6.3.10拉伸试验
管材的拉伸试验按GB/T228-2002的规定进行,其拉伸试样按GB/T6397-1986试样规定进行。
6.3.11管材的氢脆试验方法按附录C(标准的附录)的规定进行。
7检验规则
7.1检验与验收
7.1.1管材应由供方技术监督部门检验,并保证产品质量符合本标准的要求和填写质量证明书。
7.1.2需方对收到的产品应进行复检,当复检结果与本标准规定不符合时,应在收到产品之日起三个月内向供方提出,由供需双方协商解决。
7.2组批
管材应成批提交验收,每一批应由同一牌号、状态、规格和加工方法组成,每个批号的重量不大于10000kg。
7.3检验项目
7.3.1每批管材应进行化学成分、外形尺寸及允许偏差、外观质量、力学性能、扩口试验、弯曲试验、压扁试验、水压试验、晶粒度、清洁度的检验。
7.3.2管材应逐根进行涡流探伤及外表面质量检查。
7.4取样数量
7.4.1化学成分的检验每批取一个试样进行检验。
7.4.2其他项目每批取两个试样进行检验。
7.5重复试验
在外形尺寸及允许偏差、力学性能、扩口试验、晶粒度、清洁度的检验中,只要有一个试样的试验结果不合格时,也应从原抽样批中再取双倍试样进行不合格项目的重复试验,重复试验结果作为判定依据。
7.6检验结果判定
各项检验结果符合本标准要求时判为合格。
7.6.1化学成分分析、晶粒度检验、清洁度试验不合格时,则按批判不合格,其中清洁度试验不合格时,允许返修后重新交验。
7.6.2拉伸试验、扩口试验、尺寸偏差检验不合格时,则按批判不合格,对于盘管允许同批逐盘进行检验,合格者判定为单件合格。
7.6.3涡流探伤外外观质量不合格时,按实际数量判不合格。
8标志、包装、运输、贮存
标志、包装、运输、贮存应符合GB/T8888的规定。
8.1标志
8.1.1在检验合格的管材标签上应标注如下标志。
a)供方技术监督部门的检印;
b)合金牌号;
c)规格;
d)供应状态;
e)批号;
f)缺陷数(探伤报警);
g)净重;
h)执行标准;
i)生产日期。
8.1.2管材的包装箱标志应符合GB/T8888的规定。
8.2包装
铜管应按照规定的要求进行包装
8.2.1盘管应固定在两法兰之间,外围防护材料,层叠置于托盘上并固定后方可供货。
8.2.2直管包装应符合GB/T8888的规定。
8.3运输
铜管在运输的过程中不受雨、雪的影响及受潮。
8.4贮存
产品应贮存在干燥、通风良好的库房中。
8.5质量证明书
每批管材应附有质量证明书,其上注明:
a)供方名称;
b)产品名称;
c)合金牌号;
d)规格和供货形状;
e)供应状态;
f)批号;
g)净重;
h)各项分析检验结果和技术监督部门印记;
i)本标准编号;
j)包装日期。
8.6订货单内容
本标准所列材料的订货单内容包括以下内容:
a)材料名称;
b)合金牌号;
c)材料状态;
d)尺寸(名义尺寸);
e)供货形状;
f)尺寸允许偏差(有特殊要求时);
g)重量;
h)交货方式;
i)本标准编号;
j)其他。
附录A
(标准的附录)
内螺纹铜管螺纹参数测量方法
A1测量工具
显微镜,直尺,量角器,剖面放映仪等。
A2取样与制样
A2.1需要检测螺纹参数的内螺纹管应为硬态,即在螺纹成型后未退火前,所取样品没有大的变形。
A2.2对于无法得到硬态样品管时,可取软态没有大的变形的样品管。
A2.3当同一批样品管,其不同状态下的螺纹参数测量数具不一致时,以硬态为准。
A2.4取未变形的铜管一段(长度大于100mm)锯下30mm一段的铜管样,得到锯截面,在砂纸上磨制锯切面,磨制经400#、900#两道砂纸,磨制结束后,再用小毛刷清扫试样上的异物及管子内的小毛刺和卷边等,最后用酒精清洗、吹干。
A3显微镜测量方法
A3.1测量齿高、底壁厚、齿顶角
试样置于显微镜载物平台上,打开光源,初步调节X、Y方向旋钮,观察目镜,使得至少有一个较完整的齿处于视场内,任选一个齿进行测量。
a)在目镜中测量齿高和底壁厚
观测目镜,调节X、Y旋钮、旋转载物台及目镜,使齿顶与刻度线重叠并保证管的外壁与刻度线垂直,然后读出齿高和底壁厚数具。
b)在毛玻璃上测量齿高、底壁厚、齿顶角
将齿形打到毛玻璃上,齿高及底壁厚的测量方法同a);用透明纸从玻璃上描下齿形,用量角器测出齿顶角。
c)在相纸上测量齿高、底壁厚、齿顶角
为齿形拍出相片,烘干,然后用直尺在相纸上量出齿高、底壁厚,用量角器量出齿顶角。
A3.2测量齿条数
将试样置于显微镜下,放大10~40倍,直接读出其齿条数。
A3.3测量螺旋角
将管材纵向剖开,展平,找出纵向基准线,用量角仪读出螺旋角。
A3.4测量方法选择
由于测量工具及方法不同,凸筋参数测量结果与精确度各不相同,可根据不同要求选择不同的测量方法。
目镜中测量:
仅需要测量齿高和底壁厚时,应采用本方法;
毛玻璃上测量:
当需要快速测量齿顶角时,应采用本方法
相片上测量:
须精确测量齿高、底壁厚和齿顶角时采用本方法。
A3.5数据修约
A3.5.1测量齿高、底壁厚
a)在目镜中测量精确到0.004mm;
b)在毛玻璃上测量精确到0.005mm;
c)在相纸上测量精确到0.005mm。
A3.5.2测量齿顶角精确到1°。
A4剖面放映仪测量齿高、底壁厚、槽底宽和螺旋角方法
A4.1测齿高、底壁厚和槽底宽
A4.1.1将制备好的样品固定在剖面放映仪的载物台平面玻璃上,打开放映仪上底部的光源,让光线通过载物台平面玻璃底面反射至管材上。
A4.1.2调节仪器上的X、Y轴,使得至少有一个较完整的齿处于剖面仪的光屏上,调节X、Y轴,使X轴线与齿底部的投影相切,Y轴线与齿边缘相切,将X、Y轴的读数调整为0,向上平行移动X轴线与齿顶相切,读出X轴的显示数即为齿高数值。
A4.1.3将X轴复位,移动Y轴线,使之与相邻的齿边缘相切,读出Y轴显示值即为槽底宽数值。
A4.1.4将Y轴线复位,向下移动X轴线与管材的外壁相切,读出X轴的显示值即为底壁厚数值。
A4.2测量螺旋角
A4.2.1将内螺纹铜管样品沿轴向剖开压平待用。
A4.2.2将制备好的样品固定在剖面放映仪的载物台平面玻璃上,打开放映仪上底部的光源,让光线通过载物台平面玻璃底面反射至管材上。
A4.2.3调节仪器上的X、Y轴,使齿形呈清晰状,调节X、Y轴,使Y轴线与管端面相垂直,将显示仪器上的角度显示屏的任一条线调整至与X轴重合,角度显示器读数调为0,逆时针方向旋转该直线与X轴线重合,读出该角度值,用180°减去所读角度值,即为内螺纹铜管的螺旋角。
将X轴复位,移动Y轴线,使之与相邻的齿边缘相切,读出Y轴显示值即为槽底宽数值。
附录B
(标准的附录)
铜管清洁度试验方法
A1试样
管子试样长度不小于1500mm。
A2试验步骤
将待测定管材按规定长度截取,将一定量DS-3.5或其他相同性质的溶剂注入试验铜管内,充分振荡,以使彻底清洗内表面,20min后,将溶剂倒入一个充分洗净烘干并已称重量为G1的烧杯中,将烧杯置于温度为100~120ºC的控温热板上,使溶剂蒸发干为止,再将烧杯放入100~110ºC的烘箱中烘30min。
取出烧杯,放入干燥器中冷却1h,然后称出重量G2。
随同试样做空白试验,并测定空白值G0。
铜管单位内表面积上残留物重量Q—清洁度按公式(A1)计算:
Q=(G-G0)/(S×L)…………………………………………(A1)
式中:
Q—铜管清洁度,g/m²;
G—铜管残留物的重量,g;
G1—空烧杯的重量,g;
G2—清洗管子的溶剂蒸发后烧杯的重量,g;
G0—空白值,g;
S—铜管单位长度内表面积,m²/m;
L—试样长度,m。
铜管残留物的重量按公式(A2)进行计算:
G=G2-G1………………………………………………………(A2)
内螺纹铜管单位长度内表面积按公式(A3)进行计算:
S=(W+2×Hf/cos(α/2))×n/cosβ…………………………(A3)
式中:
W—槽底宽,m;
Hf—齿高,m;
α—齿顶角,(º);
β—螺旋角,(º);
n—螺旋数。
本算法将齿型看作近似三角形计算,误差≤5%。
A3溶剂用量
每1.5m长度内螺纹铜管的溶剂用量应符合表A1的规定
表A1
管子内径d,mm
注入溶剂量,ml
5≤d﹤8
30
8≤d﹤10
50
10≤d﹤13
80
附录C
(标准的附录)
氢脆试验方法
将经过清洗或除油的试样,在至少含有10%(体积)氢气的炉内于(850±25)℃下保温至少20min,然后将其在水中淬火,要尽量避免与空气接触,试样经抛光后,用普通照明在放大至少75倍的显微镜下检验该材料表面,若显示出气泡或晶界开裂等脆性特征,则表明材料存在氢脆。
附加说明:
本标准由志高两器厂提出。
本标准由志高两器厂归口。
第二次修订说明:
1、将“两器厂”改为“金属制件公司”,标准编号由“Q/ZGLQ2-2005”改为“Q/ZGJZ2-2009”;
2、完善铜管外观要求;
3、加严米克重公差要求;
4、完善弯曲试验的方法;
5、对引用标准号进行修订(按最新的标准执行,主要是国标)。