工艺管道焊接方案.docx
《工艺管道焊接方案.docx》由会员分享,可在线阅读,更多相关《工艺管道焊接方案.docx(30页珍藏版)》请在冰点文库上搜索。
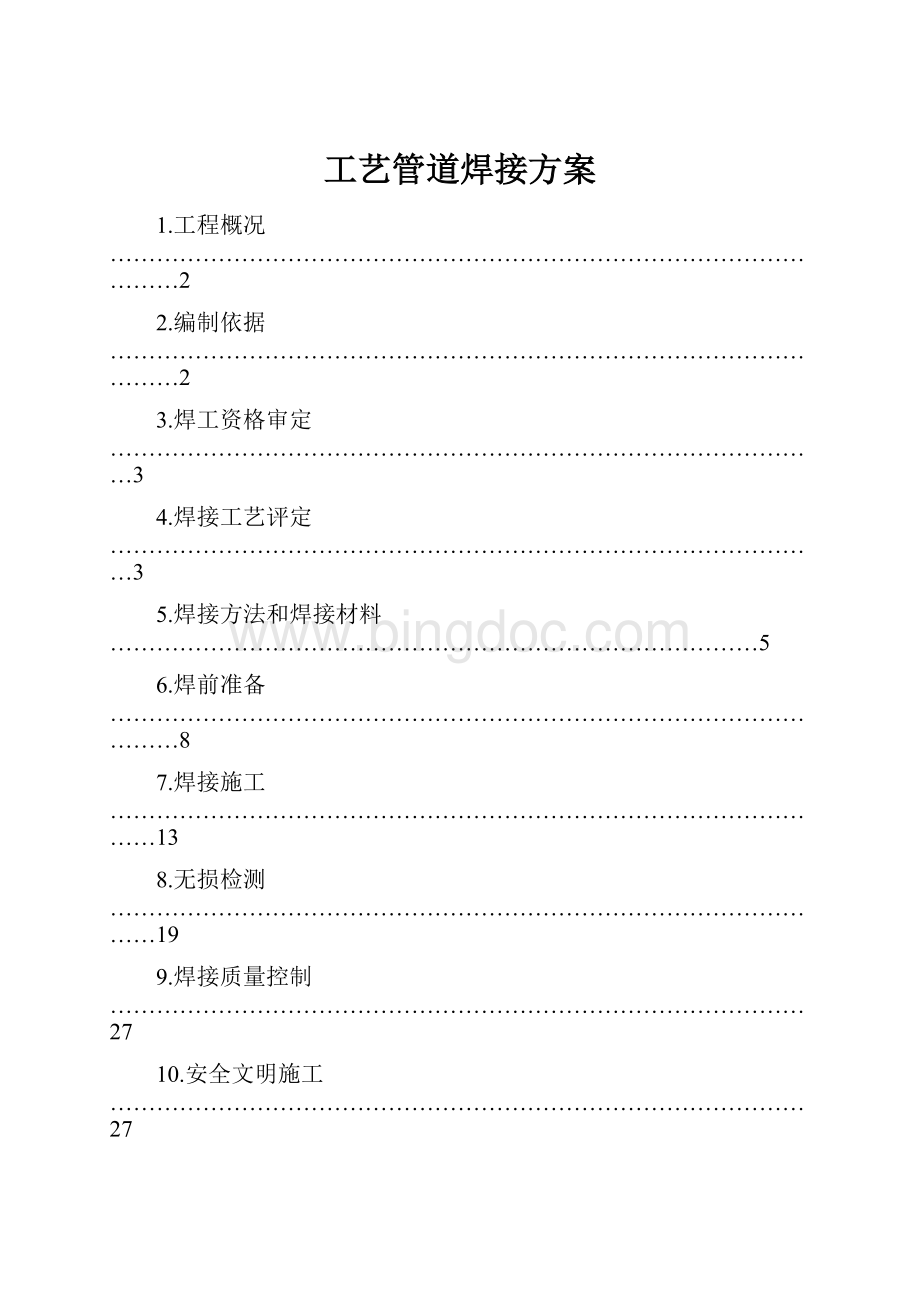
工艺管道焊接方案
1.工程概况………………………………………………………………………………………2
2.编制依据………………………………………………………………………………………2
3.焊工资格审定…………………………………………………………………………………3
4.焊接工艺评定…………………………………………………………………………………3
5.焊接方法和焊接材料…………………………………………………………………………5
6.焊前准备………………………………………………………………………………………8
7.焊接施工……………………………………………………………………………………13
8.无损检测……………………………………………………………………………………19
9.焊接质量控制………………………………………………………………………………27
10.安全文明施工………………………………………………………………………………27
一、工程概况
PE项目是一个新建项目,本工程具有管道焊接工作量大;低温和耐腐蚀的管道多;管壁厚、管径大;焊接质量要求高,需要焊工技术好、数量多;无损检测数量巨大,射线检测(RT)片子数量大;现场焊接条件较差、温度低、冬季时间长等特点。
针对本项目实际情况,为满足焊接施工质量技术要求和对焊接施工过程、焊接检验等进行严格控制,特编制此通用焊接施工方案。
本工程主要管道材质清单如下:
序号
材料类别
ASTM编号
1
碳钢管道、低温钢
A333-6
2
不锈钢
A312-TP304、304L、316、316L
3
双相不锈钢
S31803
二、编制依据
1、ASMEB31.3《工艺管道》;
2、ASMEB31.1《动力管道》;
3、ASMESec.Ⅸ《焊接评定》;
4、ASMESec.Ⅴ《无损检测》;
5、现场设计图纸及施工技术要求;
三、焊工资格审定
焊工考试必须按俄罗斯当地法律规范,获取当地焊工合格证,才能现场施工;
四、焊接工艺评定
1、在焊工考试和工程焊接施工前均应对被焊接材料进行焊接工艺评定,以保证用于实际产品施焊的焊接工艺的可靠性;
2、焊接工艺评定执行ASMESec.Ⅸ《焊接评定》;
3、焊接工程师根据工程项目情况确定焊接工艺评定的项目,并根据业主要求在现场从新做焊接工艺评定试验;
4、焊接工程师应事先制定“焊接工艺评定试验方案”,并填写“焊接工艺规程”;
5、由本公司合格焊工按“焊接工艺规程”的要求进行试件的焊接;并由焊接检查员准确填写施焊过程中的原始记录;
6、焊接结束后,进行试件的外观检查、无损检测(RT)、试样的加工和试验等,并作好相应记录和取得相关试验报告;
7、需要进行焊后热处理的试件,试样加工应在热处理和硬度检查合格后进行;
8、如果试验结果不符合要求,则应分析原因重新进行评定。
若不合格的原因是由于工艺参数的问题,则应修改“焊接工艺规程”,调整工艺参数,重新进行评定;
9、焊接工艺评定试验结束后,由焊接责任师根据原始记录和检查、试验报告填写“焊接工艺评定报告”,焊接工艺评定报告由项目总工程师审核,交由公司总工程师批准执行;
10、焊接工艺评定报告原件交公司压力容器办公室保管和存档,各施工项目所需的焊接工艺评定报告由公司压力容器办公室提供复印件。
五、焊接方法和焊接材料
如果设计文件和图纸资料对焊接方法和焊接材料无具体规定,则按下列原则选用焊接方法和焊接材料。
1、碳钢管道及低温碳钢管道
⑴对于一般碳钢管道,如循环水、废水、污水等管道,采用手工电弧焊(见图表1)。
图表1一般碳钢管道焊接方法和焊接材料
PNo.
组号
管道材质
焊接方法
焊接材料
根层
填充及盖面
根层
填充及盖面
1
1
C.S
GTAW或SMAW
SMAW
ER70S-2/3/6
(AWS、打底专用)
E7015/16/18(AWS)
焊接方法及焊接材料标准说明
焊接方法GTAW-手工钨极氩弧焊
SMAW-手工电弧焊
焊接材料ER70S-2/3/6、E7015/16/18-AWS标准编号
⑵对于所有蒸汽、气体和工艺液体介质管道,对接接头的根部焊道采用手工钨极氩弧焊,填充和盖面层采用手工电弧焊(见图表2)。
小直径管道(DN≤2″)所有对接焊缝全部采用氩弧焊
图表2重要碳钢管道焊接方法和焊接材料
PNo.
组号
管道材质
焊接方法
焊接材料
根层
填充及盖面
根层
填充及盖面
1
1
C.S
GTAW
SMAW
ER70S-2/3/6(AWS)
E7016(5)(AWS)
1
1
C.S(A333-6)
GTAW
SMAW
ER70S-2/3/6(AWS5.18)
E7018-1(AWS)
3、奥氏体不锈钢管道(图表3)
⑴对接接头的根部焊道采用氩弧焊,禁止使用手工电弧焊。
⑵填充和盖面层采用手工电弧焊。
⑶小直径管道(DN≤2″),所有焊道全部采用氩弧焊。
⑷根据不同的铬镍奥氏体不锈钢管材而选用相应的焊丝和焊条。
图表3一般奥氏体不锈钢管道焊接方法和焊接材料
PNo.
组号
管道材质
焊接方法
焊接材料
根层
填充及盖面
根层
填充及盖面
8
1
A312TP304、304L
GTAW
SMAW
ER308/ER308L(AWS)
E308L-16(AWS)
8
1
A312TP316、316L
GTAW
SMAW
ER316/ER316L(AWS)
E316L-16(AWS)
4、奥氏体不锈钢与碳钢异种管材的焊接(图表4)
(此工程中,异种管材的焊接较多,但主要为奥氏体不锈钢与碳钢管道的对接)。
⑴对接接头的根部焊道采用氩弧焊,禁止使用手工电弧焊。
⑵填充和盖面层采用手工电弧焊。
⑶小直径管道(DN≤2″),所有对接焊缝全部采用氩弧焊。
图表4SS与CS异种管道焊接方法和焊接材料
PNo.
组号
管道材质
焊接方法
焊接材料
根层
填充及盖面
根层
填充及盖面
8+1
1
S.S+C.S
GTAW
SMAW
ER309(L)(AWS)
E309-16(AWS)
5、双向不锈钢管道(见图表5)
⑴对接接头的根部焊道及第一、第二填充层采用氩弧焊,严禁使用手工电弧焊。
⑵其余焊层均采用手工电弧焊。
⑶小直径管道(DN≤2″),所有对接焊缝全部采用氩弧焊。
图表5双向不锈钢焊接方法和焊接材料
PNo.
组号
管道材质
焊接方法
焊接材料
根层
填充及盖面
根层
填充及盖面
45
1
双相不锈钢
GTAW
SMAW
ER2209
E2209-16
六、焊接前准备
1、碳钢管材的切割和坡口加工采用氧-乙炔焰方法或机械加工。
不锈钢管材的切割和坡口加工采用机械方法和等离子弧方法;坡口型式型式图(见图表6)。
如采用氧-乙炔焰和等离子弧热加工方法加工坡口后,必须除去坡口表面的氧化皮、熔渣及影响接头质量的表面层,并应将凹凸不平处打磨平整。
2、组对前应将坡口及其内外表面不小于10mm范围内的油、漆、垢、锈、毛刺及镀锌层等清除干净,且不得有裂纹、夹层等缺陷。
3、焊件组对时应垫置牢固,并应采取措施防止焊接和热处理过程中产生附加应力和变形。
4、除设计规定需进行冷拉伸或冷压缩的管道外,焊件不得进行强行组对。
5、不锈钢焊件坡口两侧各100mm范围,在施焊前应采取防止焊接飞溅物沾污焊件表面的措施。
6、焊接材料
焊接材料是保证焊接质量的一个重要因素,因此必须加强焊接材料的管理。
图表6碳钢、合金钢和不锈钢坡口型式图
焊接材料管理执行公司企业标准-压力管道安装作业指导书《焊接材料管理工作程序》(QG/CC-7.PP.0503.021-00)。
⑴验收入库
一般要求焊材-检查焊材牌号、规格、批号和质量证明书等。
特殊要求焊材-验收入库后还必须对焊材进行复验。
⑵焊材保管(一级库和二级库)
库房要求:
通风良好,配备防潮去湿设施,保证室内温度不低于5℃,相对湿度不大于60%。
堆放要求:
焊材堆放在货架上,且按种类、牌号、规格和批号等分类放置,并挂牌。
⑶焊条烘烤(烘烤条件见图表7)
焊接责任师根据有关规定和技术要求编制焊条烘烤条件(如果到货焊条烘烤条件与图表不一致,则按实际到货焊条烘烤温度为准),焊材库管员严格按此条件对焊条进行烘烤和保温。
烘箱应有自动恒温装置,测温仪表要按时校验,烘箱定期维修,确保设备完好。
图表7电焊条烘烤条件
AWS标准
烘烤温度(℃)
恒温时间(H)
E7015/16/18
300~350
1
E7018-1
300~350
1
E308L-16
200~250
1
E309-16
200~250
1
E316L-16
200~250
1
双向不锈钢
焊条烘烤前应检查外观质量,去除药皮开裂、脱落、偏心与受潮严重的焊条。
不同牌号和规格的焊条在同一烘箱烘烤时应放在烘箱内的不同部位。
烘烤时焊条堆放不宜过厚,以使焊条干燥均匀。
烘烤好的焊条存放在保温箱中待用。
⑷焊材发放
焊工凭焊接工程师签字的“领料单”领用焊材。
焊条应放置在焊条保温筒内,焊条在保温筒内不得超过4小时,否则需重新烘烤后使用。
⑸焊材回收
焊工应将当天未使用完的焊条交回焊材库。
回收的焊条应重新按烘烤条件进行烘烤后发放,重新烘烤的次数不得超过两次。
⑹焊丝使用前应清除其表面的油污,锈蚀等。
⑺手工钨极氩弧焊采用铈钨棒或钍钨棒。
⑻氩弧焊所用氩气的纯度不低于99.96%(铝合金焊接用氩气的纯度应不低于99.99%)。
7、焊接工艺规程
施焊前,焊接责任师根据焊接工艺评定编制“焊接工艺规程”。
8、焊前预热和焊后热处理要求见(图表8)和设计文件。
图表8预热和热处理要求
材料
预热
热处理温度范围
热处理保温时间
硬度(HB)
壁厚范围(mm)
预热温度(℃)
壁厚范围(mm)
热处理温度(℃)
公称壁厚(min/mm)
最小时间(h)
C.S
<25
15
-
-
-
-
-
C.S
≥25
100
>20
593~630
2.4
1
SS
-
-
-
-
-
-
-
注:
上表与设计文件有冲突时,以设计文件为准。
⑴预热温度应用测温笔、热电偶高温计或其它合适方法进行校验,以保证在焊接前和焊接过程中达到和保持WPS中规定的温度;
⑵有不同预热要求的异种钢焊接时,预热温度应基于较高等级的钢种;
⑶如果焊接中断时,冷却速率应予以控制,或采用其它措施以防止对管道造成有害影响。
恢复焊接前应进行WPS中规定的预热温度;焊前和焊接过程中应保持所要求的预热温度。
⑷预热宽度应为4倍管壁厚度,但不少于100mm。
⑸大尺寸的厚壁管,应采用电加热。
9、热处理
⑴母材组件用焊接连接时,热处理要求所采用的厚度应是接头处较厚组件的厚度,下列情况除外:
a、在支管连接时,作为补强用的金属(不是指焊缝),不论它是管件的一人整体或是补强板还是鞍件,在确定热处理要求时均不应考虑。
但是,在整个支管的任何平面内穿过焊缝的厚度大于要求热处理的材料厚度两倍时,尽管接头处各组件的厚度不大于要求热处理的最小厚度,仍需进行热处理。
b、对平焊法兰、承插焊法兰、DN50及更小管道接口的角焊缝,DN50及更小的管道上螺纹接的密封焊缝以及装在各种尺寸管子外表面的非受压部件,如吊耳或其它管道支承件,只要在任一平面内穿过焊缝的厚度超过需热处理的最小材料厚度两倍时(即使组件在结合处的厚度小于此最小厚度),就需要进行热处理,但下述情况除外:
①对于P-No.1的材料,当焊缝厚度小于或等于20mm,不管母材料的厚度多少,都不需要进行热处理(设计文件要求的除外);
对于铁素体材料,当其焊缝不是用空冷硬化的填充金属焊成时,不需进行热处理。
奥氏体焊接材料可用于铁素体材料的焊缝,操作条件的作用不致于对焊件产生有害的影响;
⑵采用热电偶高温计或其它合适的方法检查热处理温度,以保证符合WPS规定要求;
⑶焊缝的硬度试验目的是校核所进行的热处理是否令人满意。
硬度范围适用于焊缝及热影区,热影响区的硬度试验应尽可能接近焊缝的边缘。
a、硬度检测,按设计要求执行;
b、不同金属材料焊接时,每种材料均应达到标准中母材和焊接材料规定的硬度范围。
⑷若有不同热处理要求的异种铁素钢,焊后热处理条件应基于较高等级的钢种。
⑸焊后热处理最小加热宽度:
以焊缝为中心,每边超出焊缝边缘25mm(即焊缝的宽度+50mm)。
⑹热电偶数量及放置位置(见图表9)。
图表9热电偶数量及放置位置
管子位置
热电偶数量
热电偶放置位置
水平
2
管底和管顶
其他
2
管两侧各一
≥2
均匀分配
七、焊接施工
㈠、一般规定
1、焊接环境要求:
⑴焊接的环境温度应能保证焊接所需的足够温度和焊工技能不受影响,对于环境温度低于0℃时,必须采取防护措施确保焊接环境高于0℃,比如采用临时取暖棚,内部采用电取暖提高环境温度,对于焊件温度低于0℃,焊缝左右100mm位置,必须保证焊缝预热到10℃,对于碳钢,低温钢和耐热钢,可以采用烤把预热。
不锈钢焊接环境温度不能低于-10℃,不能采用烤把的形式预热。
⑵焊接时的风速不应超过下列规定,当超过规定时,应有防风设施。
手工电弧焊:
8m/s手工钨极氩弧焊和气体保护焊:
2m/s
⑶焊接电弧1m范围内的相对湿度不得大于90%。
⑷当焊件表面潮湿、覆盖有冰雪或在下雨刮风期间,焊工及焊件无保护措施时,严禁进行焊接作业。
2、定位焊
⑴焊接定位焊缝时,应采用与根部焊道相同的焊接材料和焊接工艺,并应由合格焊工施焊。
⑵定位焊缝的长度、厚度和间距,应能保护焊缝在正式焊接过程中不致开裂。
⑶在焊接根部焊道前,应对定位焊缝进行检查,当发现缺陷时应处理后方可施焊。
⑷与母材焊接的工卡具其材质宜与母材相同或同一类别。
拆除工卡具时不应损伤母材,拆除后将残留焊疤打磨修整至与母材表面齐平。
3、焊前准备
(1)焊接设备的电压表、电流表、气体流量计等仪表,仪器规范参数调节装置应完好无损,焊接设备要安排人员经常检查。
(2)管道组对
①预制的管段组对前要进一步核实各管段的尺寸、方向,下料后要用记号笔在管段两端标注与轴测图相一致的焊缝编号,并严格按照轴测图所标焊缝编号进行组对。
②管道组对前应把坡口及其内外侧表面不小于20mm范围内的油、漆、垢、锈、毛刺等清除干净。
合理安排焊口预制口和现场安装口的位置,环焊缝距支、吊架净距不应小于50mm。
③所有设备接口的配管法兰与管段为点焊。
④管道组对时,不能强力组对,以免应力集中。
⑤主管上分支管线开孔。
孔径需与支管接头的内径相平,组对间隙为2-3mm。
钢制管道坡口型式和尺寸如图10:
图10
管子对口时,应在距接口中心200mm处测量平直度(如下图11所示)。
图11
当管子公称直径小于100mm时,允许偏差值α为1mm;当管子公称直径大于或等于100mm时,允许偏差值α为2mm;但全长的偏差值不得超过10mm。
有缝钢管组对时要特别注意,纵向焊缝应置于易检修的位置,且不宜在底部;
(1)直管段在组对时,纵向焊缝相对位置应满足如下图12所示的要求:
图12
(2)当主管上开支管时,焊缝相对位置应满足如下图13所示的要求:
图13
主管线上的开孔应在预置阶段完成,当安装的仪表嘴,放空阀、排凝阀未能安装时,应及时用塑料膜,透明胶布封堵孔口。
在已安装的管道上开孔时,管内因切割而产生的异物,用磨光机打磨干净并清理掉渣滓、杂物。
4.焊接
⑴不锈钢管道及合金元素含量大于5%的管道,氩弧焊打底焊接时(包括定位焊时),焊缝内侧应充氩气防止内侧焊缝金属被氧化。
⑵严禁在坡口之外的母材表面引弧和试验电流,并应防止电弧擦伤母材。
⑶焊接时应采用合理的施焊方法和施焊顺序,特别对于大直径管和厚壁管更应如此,以减少焊接应力和焊接变形。
⑷施焊过程中应保证起弧和收弧处的质量,收弧时应将弧坑填满。
⑸多层焊的层间接头应错开。
⑹管道焊接时,管道开启处应堵死,以防止管内有穿堂风通过。
⑺除工艺或检验要求需分次焊接外,每条焊缝宜一次连续焊完,当因故中断焊接时,应根据工艺要求采取保温缓冷或后热等防止产生裂纹的措施,再次焊接前应检查焊层表面,确认无裂纹后,方可按原工艺要求继续施焊。
⑻需预拉伸或预压缩的管道焊缝,组对时对所使用的工卡具应在整个焊缝焊接及热处理完毕并经检验合格后方可拆除。
⑼奥氏体不锈钢的焊接要特别注意:
焊接电流一般比低碳钢时降低20%左右。
焊接时,应采用快速焊,等焊层冷却后再焊下一道,以减小焊缝过热,增强抗热裂纹的能力。
焊接过程中,应采用短弧,焊条最好不作(或稍作)横向摆动。
应尽量焊窄焊道,一次焊接成型的焊缝不宜过宽,一般不超过焊条直径的3倍。
焊接结束或中断时,收弧时要慢,弧坑要填满,这样能防止产生裂纹。
管内通氩气时使用的水溶性纸要张贴牢固,氩气档板要安装可靠,以免影响保护效果。
奥氏体不锈钢焊接施工,应使用不锈钢钢丝刷,不锈钢尖头手锤和扁铲,电动砂轮机也必须专用,严禁作为它用。
根据设计规定对奥氏体不锈钢焊缝及其附近表面进行酸洗,钝化处理。
八、无损检测
1、无损检测人员,应持有相应特种作业资格证。
2、射线照相底片由Ⅱ级射线检测人员评定。
3、由Ⅱ级检测人员填写检测报告,无损检测责任师审批签发送委托单位。
4、委托单、原始记录、检测报告、射线底片及检测统计表由试验中心存档。
5、无损检测执行下列标准(见图表14)
图表14无损检测执行标准
检测方法
检测程序
合格标准
RT
ASME第五篇第2节
ANSI/ASMEB31.3表341.3.2A
PT
ASME第五篇第6节
ASME第八篇第一分篇附录8
MT
ASME第五篇第7节
ASME第八篇第一分篇附录6
UT
ASME第五篇第5节
ASME第八篇第一分篇附录12
6、RT合格标准(见图表15)
图表15管道焊缝RT合格标准
(由ANSI/ASMEB31.3表341.3.2A整理)
RT抽查
RT100%
1.裂纹
无
无
2.未熔合
无
无
3.未焊透
深度:
≤0.8或≤0.2T,取小值
无
总长:
150焊缝长度内≤38
4.内部气孔的尺寸和分布
T≤6.4同右
见ASME规范第八篇第一分篇附录4
T>6.41.5X右
5.夹渣及条状物
单个长度:
≤2T
单个长度:
≤T/3
单个宽度:
≤3.2或≤T/2,取小值
单个宽度:
≤2.4或≤T/3,取小值
累计长度:
≤4T(150焊缝长度内)
累计长度:
≤T(12T焊缝长度内)
6.咬边
深度:
≤0.8或≤T/4,取小值
无明显缺陷
7.表面气孔和夹渣
无
无
8.根部内凹
接头总厚度,包括焊缝余高≥T
接头总厚度,包括焊缝余高≥T
9.余高和根部凸出
壁厚高度
T≤T6.4≤1.6
6.4<T≤12.7≤3.2
12.7<T≤25.4≤4.0
T>25.4≤4.8
注:
单位-mmT-壁厚(mm)
7、对焊缝无损检验时发现的不允许缺陷,应消除后进行补焊,并对补焊处用原规定的方法进行检验,直至合格。
对规定进行局部无损检验的焊缝,当发现不许缺陷时,应进一步用原规定的方法进行扩大检验,扩大检验的数量执行设计文件及相关标准。
8、规定进行局部射线检验或超声波检验的焊缝,其检验位置由质检人员指定。
没有规定进行射线检验或超声波检验的焊缝,质检人员应对全部焊缝的可见部分进行外观检查,当质检人员对焊缝不可见部分的外观质量有怀疑时,应做进一步检验。
9、射线检验或超声波检验应在被检验的焊缝覆盖前或影响检验作业的工序前进行。
10、必须在焊缝上开孔或开孔补强时,应对开孔1.5倍或开孔补强板直径范围内的焊缝进行无损检验,确认焊缝合格后,方可进行开孔,补强板覆盖的焊缝应磨平。
11、焊缝焊后热处理应在焊缝外观检查及规定的无损检验合格后进行。
焊后热处理方法和操作过程等见“焊后热处理方案”。
12、焊缝焊后热处理后通过硬度测量检查热处理效果,硬度值应符合设计文件和规范标准的规定。
13、热处理后进行返修或硬度检查超过规定要求的焊缝应重新进行热处理。
14、焊缝的强度试验及严密性试验在射线检验或超声波检验以及焊缝热处理后进行。
15、无损检测工作程序流程图:
⑴无损检测控制流程见图表16
⑵射线检测工作程序见图表17
⑶超声波检测工作程序见图表18
⑷磁粉检测工作程序见图表19
⑸渗透检测工作程序见图表20
无损检测控制流程图
图表16无损检测控制流程图
图表5.5—17:
无损检测控制流程图
射线检测工作程序
图表17射线检测工作程序
超声波检测工作程序
图表18超声波检测工作程序
检测前准备
编制工艺卡
打磨探头移动区表面
由持证人员担任检测
调试仪器测探头入射点,前沿距离
制作距离—波幅曲线
用直探头检测斜探头移动区母材缺陷
焊缝初检,对需要记录的缺陷部位作出标记
对初检标出的缺陷作详细复检
记录、储存、打印出检测结果
确定返修部位
作检测评定记录
返修后复检评定、记录
检测实施
评定缺陷等级
检测评定
记录复审
出具报告
审核、签发
磁粉检测工作程序
图表19磁粉检测工作程序
渗透检测工作程序
图表20渗透检测工作程序
九、焊接质量控制
1、所有现场焊工持有焊工相应的合格证,持证上岗。
2、所有质量活动都应在压力管道安装质量保证体系的控制下进行。
3、焊工的焊接质量控制执行公司企业标准——压力管道安装“焊工焊接质量控制程序”(QG/CC-7.PP.0503.017-00)。
⑴通过RT(射线照相检验)结果对焊工的焊接质量进行控制。
⑵初始控制
焊工考试合格后,即取得参加焊接施工的资格。
但焊工焊接要求进行射线检测(RT)的焊缝时,则不论焊缝是否属于100%射线检测(RT)或局部射线检测(RT),每个焊工的前五焊口均需进行射线检测(RT)。
如果焊口射线检测(RT)合格,该焊工可继续参加焊接工作。
如果焊口射线检测(RT)不合格,则该焊工需再焊两个焊口进行射线检测(RT)。
如果增加的两个焊口射线检测(RT)均合格,该焊工可继续参加焊接工作。
如果增加的两个焊口有一个不合格,该焊工的资格即被取消。
⑶抽透控制
抽透控制的方法按焊接施工项目设计或规范要求进行控制。
⑷累积控制
统计每个焊工每个月的RT一次合格率。
RT一次合格率大于95%的焊工可继续参加焊接工作。
对RT一次合格率大于90%但是小于95%的焊工提出警告,但该焊工仍可继续参加焊接工作。
如果RT一次合格率小于90%,则该焊工的资