8D培训教 材.pptx
《8D培训教 材.pptx》由会员分享,可在线阅读,更多相关《8D培训教 材.pptx(64页珍藏版)》请在冰点文库上搜索。
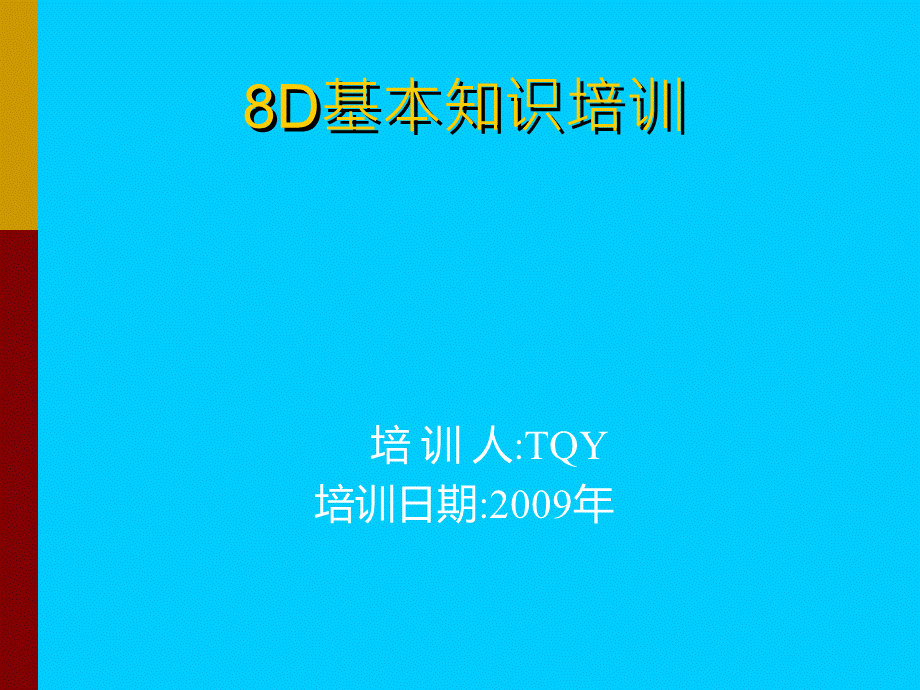
8D基本知识培训,培训人:
TQY培训日期:
2009年,8D(8Disciplines)工作方法简介,8D又称团队导向问题解决方法、8D问题求解法(8DProblemSolving)是福特公司处理问题的一种方法,亦适用于制程能力指数低於其应有值时有关问题的解决,它提供了一套符合逻辑的解决问题的方法,同时对於统计制程管制与实际的品质提升架起了一座桥梁。
8D:
8DisciplinesofProblemSolving步骤解决问题的8个步骤8D是解决问题一种工具,通常是客户所抱怨的问题要求公司分析,并提出永久解决及改善的方法比改善行动报告(CorrectiveActionReport)更加地严谨,8D工作方法的起源,二战期间,美国政府率先采用一种类似8D的流程“军事标准1520”,又称之为“不合格品的修正行动及部署系统”。
1987年,福特汽车公司首次用书面记录下8D法,在其一份课程手册中这一方法被命名为“团队导向的问题解决法”(TeamOrientedProblemSolving)。
当时,福特的动力系统部门正被一些经年累月、反复出现的生产问题搞得焦头烂额,因此其管理层提请福特集团提供指导课程,帮助解决难题,8D适用范围,该方法适用于解决各类可能遇到的简单或复杂的问题;8D方法就是要建立一个体系,让整个团队共享信息,努力达成目标。
8D本身不提供成功解决问题的方法或途径,但它是解决问题的一个很有用的工具;亦适用于过程能力指数低于其应有值时有关问题的解决;面对顾客投诉及重大不良时,提供解决问题的方法。
8D法是美国福特公司解决产品质量问题的一种方法,曾在供应商中广泛推行,现已成为国际汽车行业(特别是汽车零部件产家)广泛采用来解决产品质量问题最好的、有效的方法。
8D的目标,提高解决问题的效率,积累解决问题的经验;提供找出现存的与质量相关的框架;杜绝或尽量减少重复问题出现;8D格式的原则上针对出现的问题,找出问题产生的根本原因,提出短期,中期和长期对策并采取相应行动措施;8D法可跨部门建立小组来加强部门间的协调,推进问题有效解决,从而改进整个过程的质量,防止相同或类似问题的再发生,以保证产品质量。
8D工作方法的运用,不合格的产品问题。
顾客投诉问题。
反复频发问题。
需要团队作业的问题。
8D工作方法的8个步骤,8D是解决问题的8条基本准则或称8个工作步骤,但在实际应用中却有9个步骤:
D0:
征兆紧急反应措施D1:
小组成立D2:
问题说明D3:
实施并验证临时措施D4:
确定并验证根本原因D5:
选择和验证永久纠正措施D6:
实施永久纠正措施D7:
预防再发生D8:
小组祝贺,D0:
征兆紧急反应措施,目的:
主要是为了看此类问题是否需要用8D来解决,如果问题太小,或是不适合用8D来解决的问题,例如价格,经费等等,这一步是针对问题发生时候的紧急反应。
关键要点:
判断问题的类型、大小、范畴等等。
与D3不同,D0是针对问题发生的反应,而D3是针对产品或服务问题本身的暂时应对措施。
D1:
小组成立,目的:
成立一个小组,小组成员具备工艺/产品的知识,有配给的时间并授予了权限,同时应具有所要求的能解决问题和实施纠正措施的技术素质。
小组必须有一个指导和小组长。
关键要点:
成员资格,具备工艺、产品的知识目标分工程序小组建设,D2:
问题说明,目的:
用量化的术语详细说明与该问题有关的内/外部顾客抱怨,如什么、地点、时间、程度、频率等。
“什么东西出了什么问题”方法:
质量风险评定,FMEA分析关键要点:
收集和组织所有有关数据以说明问题问题说明是所描述问题的特别有用的数据的总结审核现有数据,识别问题、确定范围细分问题,将复杂问题细分为单个问题问题定义,找到和顾客所确认问题一致的说明,“什么东西出了什么问题”,而原因又未知风险等级。
D3:
实施并验证临时措施,目的:
保证在永久纠正措施实施前,将问题与内外部顾客隔离。
(原为唯一可选步骤,但发展至今都需采用)方法:
FMEA、DOE、PPM关键要点:
评价紧急响应措施找出和选择最佳“临时抑制措施”决策实施,并作好记录验证(DOE、PPM分析、控制图等),D4:
确定并验证根本原因,目的:
用统计工具列出可以用来解释问题起因的所有潜在原因,将问题说明中提到的造成偏差的一系列事件或环境或原因相互隔离测试并确定产生问题的根本原因。
方法:
FMEA、PPM、DOE、控制图、5why法关键要点:
评估可能原因列表中的每一个原因原因可否使问题排除验证控制计划,D5:
选择并验证永久纠正措施,目的:
在生产前测试方案,并对方案进行评审以确定所选的校正措施能够解决客户问题,同时对其它过程不会有不良影响。
方法:
FMEA关键要点:
重新审视小组成员资格决策,选择最佳措施重新评估临时措施,如必要重新选择验证管理层承诺执行永久纠正措施控制计划,D6:
实施永久纠正措施,目的:
制定一个实施永久措施的计划,确定过程控制方法并纳入文件,以确保根本原因的消除。
在生产中应用该措施时应监督其长期效果。
方法:
防错、统计控制关键要点:
重新审视小组成员执行永久纠正措施,废除临时措施利用故障的可测量性确认故障已经排除控制计划、工艺文件修改,D7:
预防再发生,目的:
修改现有的管理系统、操作系统、工作惯例、设计与规程以防止这一问题与所有类似问题重复发生。
关键要点:
选择预防措施验证有效性决策组织、人员、设备、环境、材料、文件重新确定,D8:
小组祝贺,目的:
承认小组的集体努力,对小组工作进行总结并祝贺。
关键要点:
有选择的保留重要文档流览小组工作,将心得形成文件了解小组对解决问题的集体力量,及对解决问题作出的贡献必要的物质、精神奖励。
对8D工作方法的评价,1.优点发现真正肇因的有效方法,并能够采取针对性措施消除真正肇因,执行永久性矫正措施。
能够帮助探索允许问题逃逸的控制系统。
逃逸点的研究有助于提高控制系统在问题再次出现时的监测能力。
预防机制的研究有助于帮助系统将问题控制在初级阶段。
2.缺点8D培训费时,且本身具有难度。
除了对8D问题解决流程进行培训外,还需要数据挖掘的培训,以及对所需用到的分析工具(如帕累托图、鱼骨图和流程图,等等)进行培训。
8D和6的差异,8D和6都是用于解决质量问题的有效工具,但两者之间又存在一定的差别。
1、关于工作步骤8D解决问题的8个工作步骤和6解决问题的DMAIC过程大致可以分为4个部分,如表。
表8D和6对照表,1)第1部分对于一个未知原因的问题,8D质量方法的第一步是成立一个交叉功能小组。
小组成员应具备有关工艺、产品知识以及解决问题和采取措施的技能。
小组应指定1人为小组长以组织协调小组工作,并对小组的工作进度及成效负责。
问题说明就是陈述“什么东西出了什么问题”。
6也是依靠小组解决问题的方法。
6和8D都需要成立项目组,不同之处是8D小组长是在小组成员中指定1人担任,而6项目组长由黑带绿带担任。
对于6来说,不是所有的问题都适合用6方法解决。
在选择6候选项目时,应该考虑以下问题:
是否是反复出现的事件?
范围是否狭窄?
是否存在测量尺度?
是否能在合理时间内确定测量系统?
是否能对过程进行控制?
项目是否提高了顾客满意度?
如果以上所有问题的答案是“是”,那么这是一个顾客导向6的良好候选项目。
8D和6的差异,在确定阶段,需要采用适当的步骤来明确所选6项目是否符合以上要求。
项目小组首先要通过调查研究以确定顾客抱怨什么,抱怨的程度如何,并且将顾客的抱怨转化成关键质量特性(CTQ),即从顾客角度确定对顾客最重要的产品和服务特性。
并对该特性进行量化,确定该特性“好”到什么程度顾客才满意,从而编制出关键质量特性的可操作性定义。
在确定阶段6还提供了过程流程图、鱼骨刺图、因果矩阵等细化项目范围的工具,帮助项目小组对项目范围进行细化,以确保项目范围足够狭窄,使项目在较短的时间内(一般黑带项目为6个月)能够关闭。
2)第2部分8D在问题说明后,下一步就是确定和实施临时措施。
而6在确定问题后,并不急于立即采取措施,而是进行测量,用数据进行分析。
首先要对顾客抱怨的输出进行测量,以确定目前的输出处于什么水平,从而建立一个“基点”。
还要对产生输出的过程以及输入进行测量。
在这一步骤中,虽然8D确定了要寻找并确定根本原因的一个原则,并建议可以用鱼骨图等分析工具,但可操作性不强。
但6却提供了一整套完整的测量和分析方法如过程能力分析、柏拉图、运行图、方框图、散点图等,并提供了专用的分析软件工具,使我们能够寻找和论证影响输出的根本原因。
8D和6的差异,3)第3部分8D在验证并确定永久纠正措施时,容易凭经验判断而缺少数据支持。
有些公司通过用户的反馈信息来验证改善措施,不但耗费时日,而且效果也难以保证。
所以难免发生永久措施实施后问题却没有改善的情况。
6在改善阶段提供了头脑风暴法、试验设计(DOE)等工具帮助确定改善方案。
改善方案确定后并不立即投入生产,而是要在一个小范围内试行。
并且用在测量阶段建立的测量系统对改善后的输出进行测量和分析,然后与“基点”进行对比,用数据证明改善措施是否确实改善了输出。
只有确实有效的改善措施,才能够在生产中施行。
4)第4部分8D和6都需要采取措施巩固小组取得的成果。
8D要求将与问题有关的管理系统、操作系统、工作惯例、设计与规程进行调整或修改,以防止这一问题和所有类似问题重复发生。
而6则通过防错策略控制输入并对生产产品或提供服务的过程进行持续监控以确保同样的问题不再发生。
另外,6强调预防的事先性,要求将生产产品或提供服务的过程设计或改造成能生产出6质量的产品或服务的过程,以防止缺陷产品或服务的产生。
8D一般是用于解决已出现的问题。
8D和6的差异,2、关于改进目标,8D方法提出小组通过8个步骤改善问题,但没有明确提出改进的目标。
6的目标非常明确,即追求零缺陷。
当然,6的目标并不是只通过1个6项目就能达到,而是通过一个又一个6项目,持续改进,不断地向目标迈进。
3、关于理念与文化,6不只是一种质量改进方法,而且是一种新的理念和文化。
6认为质量不只是某个部门的事情,而是公司每个员工的工作。
公司要求员工“拥有”他工作的质量,强调全员参与及行为的无边界性。
追求完美成为公司每个员工的行为,从而相互协作,形成共同的目标和价值观。
因此,在某种意义上,6不单纯只是质量改进活动,更多的是一种业务活动。
公司的所有员工都有责任学习和贯彻6方法。
换句话说,6使公司的需求、顾客的需求和个人的需求相统一,从而克服了其他质量方法部门之间相互脱节、员工之间相互推诿、公司目标和顾客需求不一致的缺点。
同时,6引导公司的各项活动的决策、分析和改进必须基于对经过量化的客观数据作为事实而进行,更加强调科学性和客观性。
8D还没有上升到一种理念和文化。
6不仅可以用于质量改进,而且可以用于组织各个方面的改进。
管理、设计、采购、制造、市场、维修、服务等各个领域都可以应用6方法进行改进。
而8D则主要是用于质量改进。
4、关于实施要求,6的实施比8D具有更高的组织构架要求和人员资格要求。
在组织构架方面,8D并没有提出特殊的要求。
而6有一整套严密的组织构架,由高层执行领导、指导、高级黑带、黑带、绿带组成。
在人员资格方面,8D要求小组成员具备工艺、产品知识,而6比8D具有更高的要求。
黑带候选人需要具备相应的专业知识背景,即要具备相关专业知识,更要具备统计学知识,一般经过至少4个月的黑带课程培训并完成2个黑带项目,然后申请参加并通过黑带资格考试,才能取得正式黑带资格。
正式黑带经过高级黑带课程培训才能成为高级黑带。
绿带需要经过至少1个星期的绿带课程培训。
而且黑带和绿带需要向所有项目小组成员教授6知识,使每个小组成员都能够用6的思维方法思考问题,用6工具解决问题。
5、关于成效要求,用8D方法解决问题没有明确提出成效要求,而6则提出了明确的成效要求。
6作为质量改进工具,不是单纯为了质量而追求质量,6只有在能够为顾客和企业带来价值时才追求质量。
如福特汽车公司要求每个黑带每年完成4至6个6项目,每个项目完成后要将缺陷率降低70,平均每个项目至少要收益250000美元(包括:
实际的税前年利润,TGW的降低带来的销售收入等)。
8D与其他工具方法,5W2H法DMAIC改进模型、七步骤法PDCA循环QC手法品质改善事例QC成果CFT1QC成果(日)2,掌握“問題”之要領,1)什麼是“問題”?
問題是實際與理想之間的差距(Gap).2)什麼是問題的型態?
1.異常性問題(s太大)2.結構性問題(Xbar太低)3)如何發掘問題?
把問題視作一座冰山(使用工具:
5Why,親和圖法,關連圖法.),先提昇製程水準(Xbar)還是降低異常(s),变异很小,但卻却不准确,准确,但变异却很大,Cpk=0.816,把问题想像成一座冰山,現在,看得到的,可感覺,可測量,問題,緊急處理,一次因(近因),治標對策(暫時),n次因(遠因),治本對策(永久),真因,真因,真因,真因,真因,why,why,why,why,why,過去,現象,5Why1H工具,丰田生产方式:
“反覆提出五次为什么”垂直式思考,针对问题一层又一层地深入通常第一个答案不会是真正的答案5Why可以找出真正的原因找原因用5Why+想方法用1How简单的案子可能4W,3W或2W即找出rootcause,但复杂的或许要5Why,6Why,7Why最后要加1H,Howtofixit.,5Why範例:
為何停機,問1:
为什么机器停了?
問2:
为什么机器会超載?
問3:
为什么軸承会潤滑不足?
問4:
为什么潤滑帮浦会失靈?
問5:
为什么潤滑帮浦的輪軸会耗損?
答1:
因为机器超載,保險絲燒斷了答2:
因为軸承的潤滑不足答3:
因为潤滑帮浦失靈了答4:
因为帮浦的輪軸耗損了答5:
因为雜質跑到裡面去了,5Why的分佈層次,現在,看得到的,可感覺,可測量,問題,緊急處理,一次因(近因),治標對策(暫時),n次因(遠因),治本對策(永久),真因,真因,真因,真因,真因,why,why,why,why,why,過去,現象,改善行動,防呆設計,为什么机器停了?
为什么机器会超載?
为什么軸承会潤滑不足?
为什么潤滑帮浦会失靈?
为什么潤滑帮浦的輪軸会耗損?
5Why&關連圖,ONHOLDLOT太多,工程師未作處置,HoldYield太高不合理,客戶ReleasegoodHoldreject,待客戶新程式,客戶一直未回覆,客戶要求作工程分析,工程師太忙沒時間處理,PC/MFG滿載排不上線測試,工程師待客戶指示,產品待重測,L/B,P/C,TesterHander問題,工程師出差受訓或請假,工程師不知有HoldLot,工程師忘記有HoldLot,工程師未被通知,系統通知到別的工程師,平面度不佳關聯圖解析,平面度良率不佳,人員疏失,設備問題,方法缺失,BUYOFF檢查動作不確實,職前訓練不足,疏忽,規格認識不夠,Loading過多,加班,精神不佳,模具異常,產品定位不良,機台操作不熟悉,材料問題,TRAY設計不良,QA未執行分散抽樣,打帶動作不確實,工作不專心,熬夜,磨損,Rework產品未確實check,PDCA的介紹,何謂管理?
P-D-C-A,企劃Plan-實行Do-檢核Check-行動Action是課題達成型QC改善歷程是一種對新的作業標準不斷挑戰,修正,並以更新的標準替代的過程運用PDCA改善前,應以SDCA來做標準化四個步驟是一體的,連續的.由相同人或單位所負責,否則常会導致無法銜接改善行動要有“有效性”驗証,7.效果維持,8.反省及今後計劃,6.效果確認,3.方策擬定,2.課題明確化與目標設定,1.主題選定,4.最適策追究,5.最適策實施,P管理人員,D作業人員,A管理人員,C檢驗人員,PDCA循環輪,C-A-P-D-C-A,檢視現狀-再對策-企劃-實行-檢核-行動是問題解決型QC改善歷程注重在已發生問題的處理在PDCA循環注重在Do,故Do的內部尚有小型的PDCA循環,直到問題改善為止小規模的改進,非大刀闊斧的改革,3.要因解析,2.現況的把握,1.主題選定,6.效果確認,5.對策實施,4.對策擬定,8.反省及今後計劃,7.效果維持,PPlan,D,AAction,CCheck,CA-PDCA循環輪,S-D-C-A,標準化Standardization-實行-檢核-行動所有製程在開始運作時都会不穩定,在這個階段,穩定製程使產量固定是很重要的待標準建立了並且穩定了,PDCA則是用來改變製程提昇水準.但是一旦製程一改變,又会馬上變得不穩定,需要以SDCA加以穩定化,A,C,P,D,A,C,P,D,A,C,S,D,A,C,S,D,屬於兵力的維持(將製程穩定化),屬於兵力的提昇(提昇製程的能力),PDCA與SDCA,PDCA,CA-PDCA與SDCA,列出問題點,GAPAnalysis,(-),(+),1.主題選定,PDCA,活動計劃的製作,CA-PDCA,活動計劃的製作,2.現況把握,2.課題明確化,3.方策擬定,3.要因分析,6.效果確認,5.最適策實施,4.最適策追究,7.效果維持,5.對策實施,4.對策擬定,8.反省及今後計劃,適用何種QCSTORY的判定,PDCA與CA-PDCA實施步驟,1.主題選定,PDCA,活動計劃的製作,CA-PDCA,活動計劃的製作,2.現況把握,2.課題明確化,3.方策擬定,3.要因分析,6.效果確認,5.最適策實施,4.最適策追究,7.效果維持,5.對策實施,4.對策擬定,8.反省及今後計劃,適用何種QCSTORY的判定,PDCA與CA-PDCA實施步驟,最適策.由Plan開始即多角度去尋求解決問題的對策,與CA-PDCA的邊尋找對策處理問題有所不同,解決問題的QCStory種類,1.課題達成型QCStory:
著重PDCA2.問題解決型QCStory:
著重CA-PDCA3.8D及異常一覽表:
著重在於預防再發,改善範例,兩種不同類型的良率損失,異常良率損失Excursions:
良率損失的獨立跳昇,由突然且嚴重的良率損失所引起,影響範圍導致特別低良率的有限批數水準不足良率損失Chronics:
良率水準不足。
發生眾多批數,其良率相對低於水準內的良率。
不良率的p-Chart趨勢圖,SigmaRule,異常的定義,99.73%,Excursions對整體良率的影響,Excursions的偵測,公司並非以SPC偵測出Excursions,請問公司以何機制得知Excursions.,如何管理異常良率,有效管理異常可以將干擾降低提昇Xbar水準(幫助不大,因为屬於少數)暫時管制措施是重要的第一件事就是將產品“Hold”再來才是解決問題,預防問題的再發異常管理三現:
現時,現地,現物以Problem7Steps來解決及預防問題SDCA,原文全名1/2,8-D:
Eight-DisciplinesofProblemSolvingFMEA:
FailureModes&EffectsAnalysisAPQP:
AdvanceProductQualityPlanningDOE:
DesignofExperimentsEI&PM:
EmployeeInvolvement&ParticipativeManagement,原文全名2/2,FTA:
FaultTreeAnalysisCI:
ContinuousImprovementQC:
QualityCirclesQFD:
QualityFunctionDeploymentSPC:
StatisticalProcessControl,找出問題點,現狀的把握及目標的設定,表示原因及結果的關係,要因的解析,柏拉圖,散佈圖,直方圖,A,B,C,1,2,3,4,5,查檢圖,管制圖,特性要因圖,QC7手法的應用,D,E,*,*,*,*,*,要因的解析,層別,有相關,有時間的變化,*,*,*,*,*,*,對策的檢討及實施,效果的確認,標準化(制定),效果的維持,A,B,C,D,E,A,B,C,這是期望能使用的方法,這是可以使用的方法,Plan1:
渾沌事項的整理及問題的設定,過去的QC手法,Plan2:
手段展開,Plan3:
手段以時序列的配列實行計劃作成,親和圖法(感情的),關連圖法(邏輯的),系統圖法(對目的或多段目的作系列性的手段展開),矩陣圖法(目的及手段的關連能知道),PDPC法(有不確定要素,所以在推行過程中,可隨時加入時點情報,並作最適計劃),箭圖法(主要是使確定事象系列的計劃初期效率化),統計的方法,實驗計劃法,矩陣數據解析法,魚骨圖,QC七大手法,柏拉圖查檢表直方圖散佈圖管制圖推移圖,多變量解析法,用於重大事故的預測,在有很多數量性數據時,而數量很渾沌時作為整理用可以在Plan或是Do的階段使用,Do,新QC7手法在改善所佔的角色,統計手法的應用,