基于Proe的航空接头注塑模设计及有限元分析Word格式.docx
《基于Proe的航空接头注塑模设计及有限元分析Word格式.docx》由会员分享,可在线阅读,更多相关《基于Proe的航空接头注塑模设计及有限元分析Word格式.docx(32页珍藏版)》请在冰点文库上搜索。
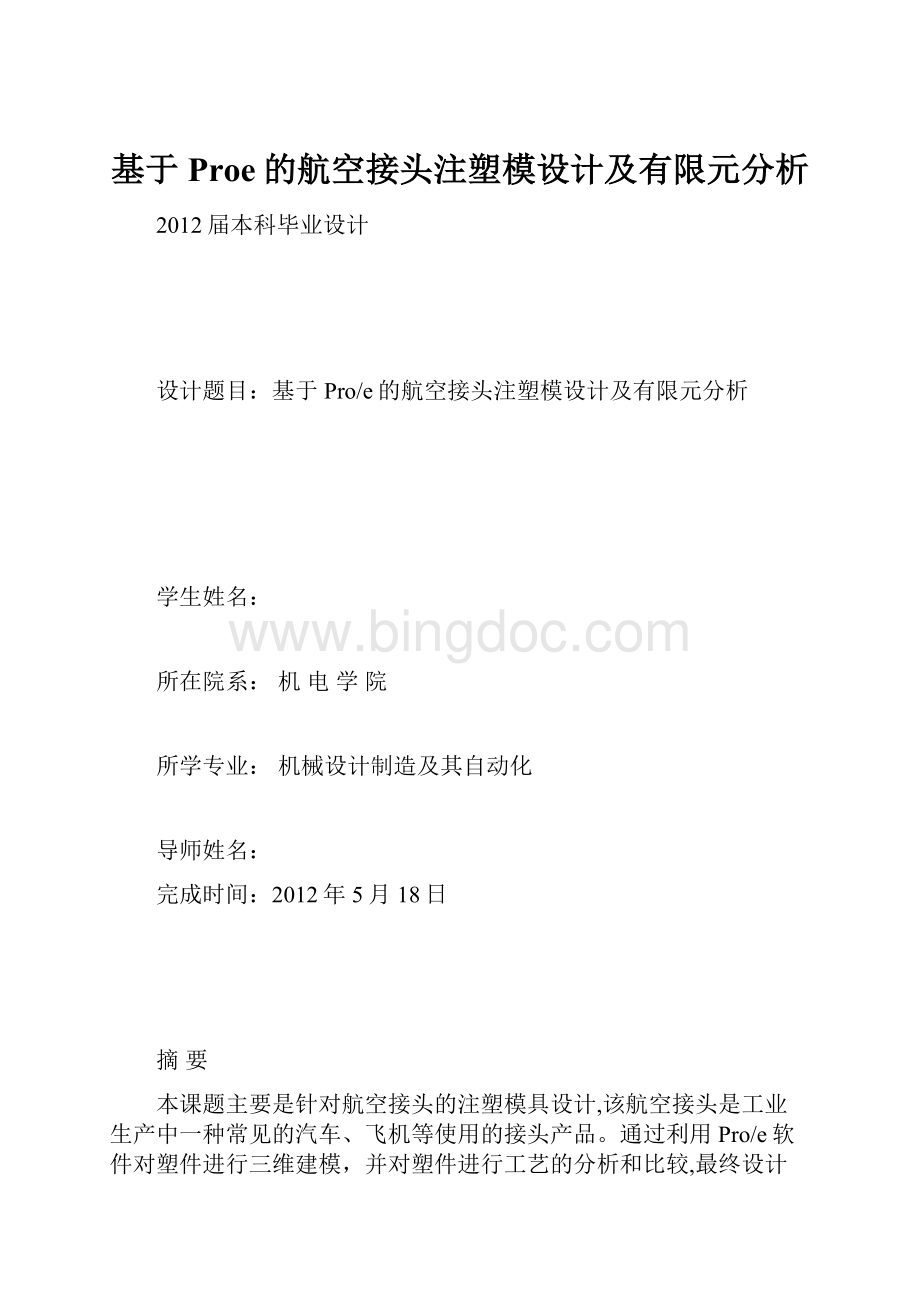
Pro/e;
三维建模,有限元分析。
Abstract
Themaintopiccoveredforaairconnectorofinjectionmolddesign,theairconnectoriscommonlyfoundinindustrialproductionofaprotectivecoverproducts.weshouldmakethethreedimensionalmodelingusethePro/e,Throughtheprocessofplasticpartsforanalysisandcomparison,thefinaldesignofaninjectionmold.Theproductmixfromtechnologyissues,andspecificmoldstructureofthecastingmoldsystem,moldformingpartofthestructure,sidepumpedbody,topofthesystem,coolingsystem,thechoiceofinjectionmoldingmachineandrelatedcalibrationparametersaredetaileddesign,atthesametimeanddevelopedasimpleprocessdies.Designedinaccordancewiththesubject'
smaintaskistobuildaairconnectorplasticinjectionmolddesign,thatis,thedesignofaninjectionmoldtoproduceplasticproductsinordertoachieveautomationtoincreaseproduction.Last,wemakethefinite-elementanalysisfortheplasticproductsusethePro/e.Finiteelementanalysisofstructuralanalysisisthemostcommonlyusedfield,isMechnicamajoranalysisfunctions.TheMechnicaincludesastaticanalysis,modalanalysis,bucklinganalysis,fatigueanalysisandvibrationanalysis,theanalysisfunctiontodrawthestructureofstrength,stiffness,stabilityandothercharacteristics,exceptforacontactanalysisanddeformationanalysis,allanalysesarelinearanalysis.Inthispapertheplasticmoldforstaticanalysis,modalanalysisandfatigueanalysis.
Keywords:
airconnector,Injectionmolddesign,Pro/e,Threedimensionalmodeling,Finite-elementanalysis.
1绪论
我国塑料模具工业从起步到现在,已经历经了半个多世纪,其间模具工业发生了很大的变化,也有了很大的发展,而模具水平也有了较大的提高。
在大型模具方面,已能生产出大屏幕的彩电塑壳、大容量的洗衣机塑料模具以及汽车用品和仪表板等塑料模具。
近几年,随着科学技术的发展,如今的产品用金属的越来越少了,取而代之的是塑料产品,仔细观察就会发现我们身边有很多的塑料产品,为了满足人们对塑料产品的需求,注塑成型模具应运而生,注塑成型模具就是将塑料先加在注塑机的加热料筒内,塑料受热熔化后,在注塑机的螺杆或柱塞的推动下,经过喷嘴和模具的浇注系统进入模具型腔内,塑料在其中固化成型[1]。
据有关方面预测,模具市场在将来的发展空间会越来越大,而现在模具市场的总体走向是平稳向上的,在未来的模具的市场中,塑料模具的发展速度会大大高于其他行业以及其他模具,从而在其他模具行业中的比例会逐步的提高。
相应地,对塑料模具提出越来越高的要求也是理所当然的。
因此,高精密、超大型、复杂、长寿命模具将会有更高的发展速度。
同时,由于近年来我国在高精密、超大型、复杂、长寿命模具进口数量比较大,所以,从各个角度来看,上述高档模具在市场上的份额也将逐步增大。
由于塑料成形的制品的要求越来越高,为了适应生产的高要求,今后我们应该重点提高超大型、高精密、复杂、长寿命模具的设计水平以及比例。
并且在今后的模具设计制造中我们应该全面推广应用CAD/CAM/CAE技术。
CAD/CAM技术已经发展为一项比较成熟的共性技术,随着CAD/CAM软件智能化的程度逐步提高,塑料制品的三维设计建模与成形过程的模拟分析将在我国的模具的行业会占越来越高的比例,同时也会发挥越来越重要的作用。
为了提高模具的生产率,也让模具在使用中变的越来越方便,我们在以后的模具设计中应逐步完善模具的标准化水平,我们可以先制定出一套国家标准,并严格按照标准执行生产,于此同时,我们也要逐步形成规模生产,提高商品化程度和标准件质量,降低成本,最后就是要进一步增加标准件的规格品种[2]。
通过毕业设计我了解到注塑模具设计的相关步骤,认识到一套注塑模具系统包括哪些系统和哪些成型零件,通过查阅有关模具设计的资料和书籍,我学习到关于模具设计中常用材料在各种成型过程中对模具的工艺要求,各种模具的结构特点及设计计算的方法,以达到能够独立设计一般模具的要求。
在模具制造方面,掌握一般机械加工的知识,金属材料的选择和热处理,了解模具结构的特点,根据不同情况选用模具加工新工艺。
2塑料成型工艺基础
2.1航空接头的装配图造型设计
其图形如图1、图2所示
图1航空接头装配图三维建模图
图2航空接头三维建模分解图
航空接头主要是用于汽车和相关机械上的引线接头,从航空接头的装配图和分解图中可以看出航空接头的结构组成,航空接头共由以下塑件组成:
1.两个棕色密封垫圈2.一个白色矩形垫圈3.一个引入接头4.一个引出接头5.一个联接环6.一个空心固定引导圆筒。
其中两个接头和引导圆筒上各有44个直径为3㎜的通孔。
2.2航空接头的零件造型
图3航空接头主视图及其三维图
图4航空接头右视图及其三维图
图5航空接头左视图及其三维图
2.3航空接头结构及工艺分析
航空接头结构非常复杂,它主要由三部分组成,分别是用于固定导线用的筒体,用于固定位置的正方形压板,用于连接用的螺纹部分,航空接头上有两部分螺纹,一部分是螺距为2㎜的细螺纹,另一部分是螺距为50㎜的三节螺旋大螺纹,这一部分的三节螺旋螺纹是最有难度的,这部分螺纹可以把整个航空接头注塑出来以后再单独加工,在此试着设计一套模具直接把这部分三节螺纹注塑出来,直接注出来是有难度的,所以在此我们将三节螺纹分为三部分,用三个侧型芯,利用斜导柱、滑块和侧向抽芯结构,另外,航空接头中有44个直径为3㎜,长度为40㎜的通孔,这一部分通孔由于长度长,如果用长型芯的话,注出来的塑件孔容易出现弯曲,所以在此把这部分长孔分为两部分型芯注塑出来,另外一部分细螺纹用螺纹型芯,将整个航空接头注出来以后,利用人工的方式将整个接头直接旋出来。
2.4航空接头原材料分析
聚丙烯的英文名称为:
Polypropylen,缩写为PP,目前聚丙烯已经成为发展速度最快,产量最大的,牌号最多的,用途最广的,用量高速增长的合成树脂之,聚丙烯为无色圆柱形颗粒,无毒、无味、五嗅,密度为0.90-0.91g/cm3。
性质较硬,具有良好的延伸型、电绝缘性、化学稳定性、加工性能良好。
聚丙烯的分子结构规整,结晶度94-99%,熔点160-175℃,目前国内最多用25公斤编织袋包装,其具有较高的刚性和较低的密度(0.90—0.91),高拉伸强度(特别是在拉身后),优良的透明性、耐应力开裂性、耐化学性,较高的耐热性,熔点达到164度,可以在100-120度以下长期使用,电绝缘性良好,耐折叠性好。
聚丙烯经过填充和增强后,其机械性能在许多应用领域足以与成本更高的工程塑料竞争。
具有良好的注塑加工性。
可以被拉伸和定向,从而可生产纤维和拉伸薄膜。
薄膜制品:
聚丙烯薄膜制品透明性好,而且有光泽,水蒸气和空气的透过率很小,根据加工工艺不同可分为吹塑薄膜、流涎薄膜(cpp)、双向拉伸薄膜(BOPP)。
注塑制品:
可用于汽车、电器、机械、仪表、无线电、纺织、国防等工程配件,日用品,周转项,医疗卫生器材,建筑材料。
挤塑制品:
可做管材、型材、拉丝、渔用绳索、打包带、捆扎绳、编织袋、纤维、复合涂层、片材、板材等。
吹塑中空成型制品各种小型容器等。
其他:
热成型、发泡、高发泡可做结构泡沫体,合成木材、层压板、合成纸[3]。
3注塑设备的选择
3.1估算塑件的体积
估算塑件的体积与质量
通过pro/e造型分析,可以得出塑件体积为
通过查文献知聚丙烯密度为
,计算出塑件的质量为
(1)
3.2选择注塑机
通过上述数据,经过查阅相关资料和经验数据,我们初选注塑机型号为SZ—320/1250的注塑机[4]。
注塑机的参数如下:
结构形式:
卧式注塑机
理论注塑容量/cm3:
335
注塑压力/Mpa:
145
螺杆直径/mm:
48
注射速率/(g/s):
140
塑化能力/(g/s):
19
螺杆转速/(r/min):
10~200
锁模力/KN:
1250
拉杆内间距/mm:
415×
415
移模行程/mm:
360
最大模具厚度/mm:
550
最小模具厚度/mm:
150
锁模形式:
双曲肘
模具定位孔直径:
ф160
喷嘴球半径:
SR15
3.3模架的选择
由于航空接头的结构形状比较复杂,为了避免标准模架由于尺寸上的限制给模具设计带来不便,所以在此次设计上我们采用自行设计的模架尺寸。
3.4最大注射压力的校核
航空接头的原料为PP,所需注射为70—120MPa,而所选注射机压力为145MPa,所以注射压力符合要求。
3.5最大注塑量的校核
注塑机的最大注塑量应大于制品的质量或体积(包括流道及浇口凝料和飞边),通常注塑机的实际注塑量最好是注塑机的最大注塑量的80%。
所以选用的注塑机最大注塑量应满足[5]:
0.8V机≥V塑+V浇
(2)
式中V机————注塑机的最大注塑量,270cm3
V塑————塑件的体积,该产品V塑=46cm3
V浇————浇注系统体积,该产品V浇=2cm3
故V机≥(46×
4+2)cm3
3.6锁模力校核
F锁﹥pA(3)
式中p————熔融型料在型腔内的压力,该塑件的压力为150Mpa
A————塑件和浇注系统在分型面上的投影面之和,经计算A=1664mm3
F锁————注塑机的额定锁模力。
故F锁>pA=150Mpa×
1664mm3
选定的注塑机的压力为1250KN,满足要求。
3.7模具与注塑机安装部分相关尺寸校核
A模具闭合高度长宽尺寸要与注塑机模板尺寸和拉杆间距相合适[6]
模具长×
模具宽<
拉杆面积
B模具闭合高度校核
Hmin————注塑机允许最小模厚=550mm
Hmax————注塑机允许最大模厚=150mm
H——————模具闭合高度=210mm
故满足Hmax>H>Hmin。
(4)
所以选择的注塑机符合上述要求,可以选用。
4.航空接头注塑模具的设计
注射模结构设计主要包括:
分型面的选择、模具型腔数目的确定及型腔的排列、浇注系统设计、型芯、型腔结构的确定、推件方式、侧抽芯机构的设计、模具结构零件设计等内容[7]。
4.1分型面的选择
该塑件为航空接头塑件,由于此接头结构形状复杂,两端有两条螺纹,中间又有一块厚度为4㎜,长度为50.5㎜的正方形压板,并且正方形压板四个角分布着四个直径为4㎜的通孔,所以为了分模的时候方便,我们选择下面的一种分模方案,如下图6所示:
图6航空接头的分型面图
4.1.1排气槽的设计
塑料熔体在填充模具的型腔过程中同时要排出型强及流道原有的空气,除此以外,塑料熔体会产生微量的分解气体。
这些气体必须及时排出。
否则,被压缩的空气产生高温,会引起塑件局部碳化烧焦,或塑件产生气泡,或使塑件熔接不良引起强度下降,甚至充模不满[8]。
由于航空接头结构非常复杂,但是其模具为小型模具,且分型面适宜,可利用分型面排气,所以无需设计排气槽。
4.2型腔数目的确定
尽管航空接头形状结构复杂,但是为了提高生产效率,本次设计中采用一模四腔的结构,同时为了能够保证制品质量的均一和稳定,另外为了防止模具承受偏载而产生溢料现象,我们采用H形排列。
这样有利于构成平衡浇注系统。
4.3浇注系统的设计
4.3.1主流道的设计
主流道是指浇注系统中从注射机喷嘴与模具接触处开始到分流道为止的塑料熔体的流动通道,是熔体最先流经模具的部分,它的形状与尺寸对塑料熔体的流动速度和充模时间有较大的影响[9]。
因此,必须使熔体的温度降和压力损失最小。
根据手册查得SZ—320/1250型注射机喷嘴的有关尺寸:
喷嘴球半径:
SR=15mm;
喷嘴孔直径:
d=Ф10mm。
主流道尺寸
主流道通常设计在浇口套中,为了让主流道凝料能顺利从浇口套中拔出,主流道设计成圆锥形,其锥角
为
,流道表面粗糙度
,小端直径
比注射机喷嘴直径大0.5~1mm。
现取锥角a=
,小端直径比喷嘴直径大0.5mm。
浇口套一般采用碳素工具钢材料制造,热处理淬火硬度50~55HRC。
由于小端的前面是球面,其深度为3-5mm(现取为5mm),注射机喷嘴的球面在该位置与模具接触并且贴合,因此要求主流道球面半径比喷嘴球面半径大
。
浇口套与模板间配合采用
的过渡配合,主流道长度取为60mm。
主流道是一端与注射机喷嘴相接触,另一端与分流道相连的一段带有锥度的流动通道。
主流道小端尺寸为4.5mm。
4.3.2主流道衬套的形式
主流道小端入口处与注射机喷嘴反复接触,属易损件,对材料要求较严,因而模具主流道部分常设计成可拆卸更换的主流道衬套形式,以便有效的选用优质钢材单独进行加工和热处理。
常用浇口套分为浇口套、定位圈整体式和浇口套与定位圈单独分开两种,在此设计中我们采用前者,由于注射机的喷嘴球半径为15mm,所以浇口套的为R20mm。
4.3.3分流道的设计
分流道是主流道与浇口之间的通道,一般开在分型面上,起分流和转向的作用。
分流道截面的形状可以是圆形、半圆形、矩形、梯形和U形等,圆形和正方形截面流道的比面积最小(流道表面积于体积之比值称为比表面积),塑料熔体的温度下降小,阻力小,流道的效率最高。
但加工困难,而且正方形截面不易脱模,所以在实际生产中较常用的截面形状为梯形、半圆形及U形[10]。
分流道设计要点:
(1).在保证足够的注塑压力使塑料熔体能顺利的充满型腔的前提下,分流道截面积与长度尽量取小值,分流道转折处应以圆弧过度。
(2).分流道较长时,在分流道的末端应开设冷料井。
对于此模来说在分流道上不须开设冷料井。
(3).分流道的位置可单独开设在定模板上或动模板上,也可以同时开设在动,定模板上,合模后形成分流道截面形状。
(4).分流道与浇口连接处应加工成斜面,并用圆弧过度。
分流道的长度
分流道的长度取决于模具型腔的总体布置方案和浇口位置,从在输送熔料时减少压力损失,热量损失和减少浇道凝料的要求出发,应力求缩短。
分流道的断面
分流道的断面尺寸应根据塑件的成形的体积,塑件的壁厚,塑件的形状和所用塑料的工艺性能,注射速率和分流道长度等因素来确定。
分流道要减小压力损失,希望流道的截面积大,表面积小,以减小传热损失,同时因考虑加工的方便性。
分流道应考虑出料的流畅性和制造方便,熔融料的热量损失小,流动阻力小,比表面和小等问题,由于采用的是潜伏式二级分流道对热损失及流动提出了较高的要求,采用圆形的分流道,为了保证外形无浇口痕,浇口前后两端形成较大的压力差,增加流速,得到外形清晰的制件,提高熔体冷凝速度,保证熔融的塑料不回流,同时可隔断注射压力对型腔内塑料的后续作用,冷却后快速切除。
同时它的效果与S浇注系统有同样的效果,有利于补塑。
4.3.4浇口形式的选择
浇口又称进料口,是连接分流道与型腔之间的一段细短流道(除直接浇口外),它是浇注系统的关键部分[11]。
其主要作用是:
(1)型腔充满后,熔体在浇口处首先凝结,防止其倒流。
(2)易于在浇口切除浇注系统的凝料。
浇口截面积约为分流道截面积的0.03~0.09,浇口的长度约为0.5mm~2mm,浇口具体尺寸一般根据经验确定,取其下限值,然后在试模是逐步纠正。
当塑料熔体通过浇口时,剪切速率增高,同时熔体的内磨檫加剧,使料流的温度升高,粘度降低,提高了流动性能,有利于充型。
但浇口尺寸过小会使压力损失增大,凝料加快,补缩困难,甚至形成喷射现象,影响塑件质量。
浇口位置的选择:
浇口位置应使填充型腔的流程最短。
这样的结构使压力损失最小,易保证料流充满整个型腔,同时流动比的允许值随塑料熔体的性质,温度,注塑压力等的不同而变化,所以我们在考虑塑件的质量都要注意到这些适当值。
浇口设置应有利于排气和补塑。
浇口位置的选择要避免塑件变形。
采侧浇口在进料时顶部形成闭气腔,在塑件顶部常留下明显的熔接痕,而采用点浇口,有利于排气,整件质量较好,但是塑件壁厚相差较大,浇口开在薄壁处不合理;
而设在厚壁处,有利于补缩,可避免缩孔、凹痕产生。
浇口位置的设置应减少或避免生成熔接痕。
熔接痕是充型时前端较冷的料流在型腔中的对接部位,它的存在会降低塑件的强度,所以设置浇口时应考虑料流的方向,浇口数量多,产生熔接痕的机会很多。
流程不长时应尽量采用一个浇口,以减少熔接痕的数量。
对于大多数框形塑件,浇口位置使料流的流程过长,熔接处料温过低,熔接痕处强度低,会形成明显的接缝,如果浇口位置使料流的流程短,熔接处强度高。
为了提高熔接痕处强度,可在熔接处增设溢溜槽,是冷料进入溢溜槽。
筒形塑件采用环行浇口无熔接痕,而轮辐式浇口会使熔接痕产生。
浇口位置应避免侧面冲击细长型心或镶件。
综合上述要求,我们本模具当中采用截面形状为圆形d=1.6mm的侧浇口形式。
4.4合模导向机构设计
导向合模机构对于塑料模具是必不可少的部分,因为模具在闭合时要求有一定的方向和位置,所以必须设有导向机构,导柱安装在动模一边或定模一边均可,通常导柱设在主型腔周围[12]。
导向机构的主要作用有:
定位、导向和承受一定侧压力。
定位作用:
为避免装配时方位搞错而损坏模具,并且在模具闭合后使型腔保持正确形状,不至因为位置的偏移而引起塑件壁厚不均。
塑件在注入型腔过程中会产生单向侧压力,或由于注射机的精度限制,使导柱工作中承受一不定的导向作用。
动定模合模时,首先导向机构接触,引导动定模正确闭合,避免凸模或型芯先进入型腔,产生干涉而坏零件。
由于注塑压力的各向性就会对导柱进行径向的剪力,导致导柱容易折断。
对型芯和型腔改进后,其的配合可以进行定位。
4.5脱模推出机构设计
鉴于航空接头两端都有螺纹,并且最困难的是中间有44个直径为3mm的通孔右端的三头螺纹我们在模具中采用了侧向型芯,如果左端的细螺纹也采用自动顶出机构,模具将会变得非常复杂,不利于模具的生产与制造,因此我们在此设计中让整个塑件包括两端的螺纹注塑出以后,右端采用侧向抽芯机构可以脱离模具,而左端螺纹采用顶杆将螺纹型芯和塑件整体推出,待型芯与塑件脱离通孔型芯之后人工将塑件旋转出来。
所以在此我们采用每个塑件上用两个顶杆定出螺纹型芯和塑件,其推出机构可选择推杆推出和推板推出,若采用推板推出只能推外围部分,而中间的型芯抱紧部分没有推件力,且塑件上有圆弧过度,推件板制造困难;
推杆推出简单,推出平稳可靠,虽然推出时会在塑件上留下顶出痕迹,但是在航空接头断面上留下痕迹并不会影响航空接头的使用性能,并没有什么大的问题。
所以从以上分析得出:
该塑件可采用推杆推出机构。
4.6侧向抽芯机构设计
在此模具设计中,由于航空接头两端有两个螺纹,并且其中右端侧面一个螺纹为三头宽螺纹,它垂直于脱模方向,阻碍成型后塑件从模具中脱落,所以为了能让三头螺纹能够一次注成,需设置侧向抽芯机构。
该塑件能考虑的抽芯机构有斜滑块抽芯机构和滑块、斜销抽芯机构。
根据塑件的结构分析,若采用斜滑块抽芯机构需将型腔分为三瓣,并且得将型腔与型芯分开,这使得结构不合理,故选择滑块、斜销抽芯机构。
4.6.1斜导柱设计
斜导柱的结构如图7所示,斜导柱的断面为圆形,其固定形式与合模导柱类似的台肩固定,只是由于倾斜安装而台肩轴被削去一部分.斜导柱导向部分可以做成半球型或锥台形,但应注意锥台的斜角须大于斜导柱的倾斜角,以避免斜导柱工作长度部分已脱离
滑块的孔之后,斜导柱头部仍对滑块有驱动作用。
图7斜导柱示意图
斜导柱倾角a确定
斜导柱的倾角a是决定斜导柱抽芯机构工作实效的一个重要的因素。
a的大小关系到模具所需开模力的大小及斜导柱所受弯曲力的大小,有关系到斜导柱的工作长度、抽芯距及开模距离长短。
a的取值一般在15°
~20°
间,根据塑件的侧抽孔的深度,即抽芯距的大小,由于抽芯距较大,所以可取较小的倾角,取a为20°
斜导柱直径的确定
斜导柱主要承受弯曲力,而对斜导柱的直径的确定一般按经验来取,由于塑件的侧抽型芯孔较小,侧抽力不大,所以取斜导柱的直径为20mm[13]。
4.6.2滑块与导滑槽的设计
侧型芯与滑块的连接形式
根据塑件的形式分析,侧型芯与滑块应做成组合式,然后装配在一起,这样可以节约优质钢材,且加工及维修更换方便.。
为了