课程设计说明书1111Word格式文档下载.docx
《课程设计说明书1111Word格式文档下载.docx》由会员分享,可在线阅读,更多相关《课程设计说明书1111Word格式文档下载.docx(18页珍藏版)》请在冰点文库上搜索。
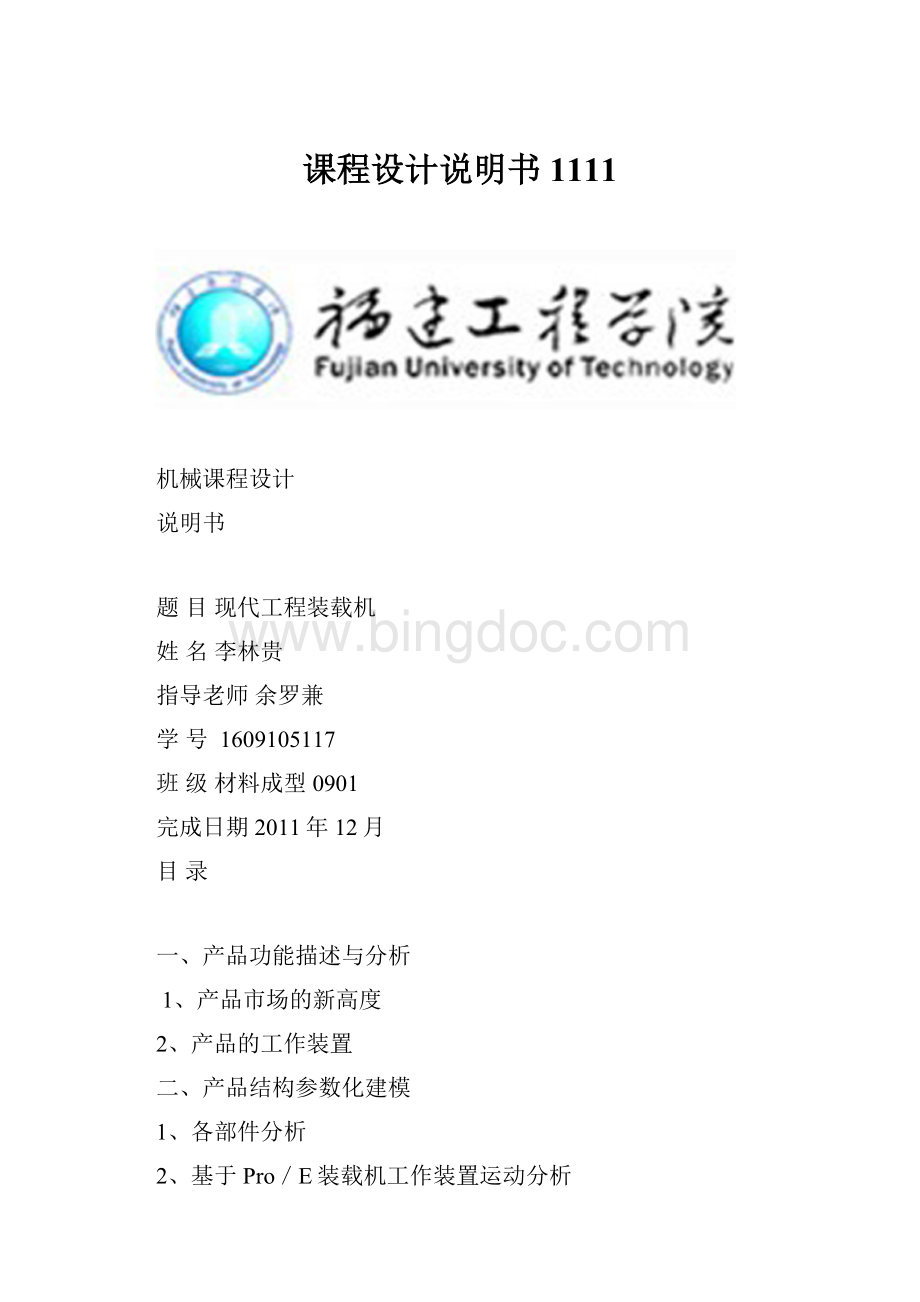
对于了解现有装载机的新结构、新技术、新应用和新发展,具有很好的借鉴作用和促进作用。
2、产品的工作装置
1装载机的工作过程
当装载机用于将货物从料堆装入运输车辆或将货物由一地转移至另一地时,其工作过程大体包括:
空架运行、叉取货物、叉架提升、稳载运行、卸货等5个循环作业过程。
1.1空架运行
装载机叉装货物时,需空架驶向料堆,在卸货后,后退、落架并驶向堆。
运行中,叉架处于运输位置,使叉架底面与前轮的公切线和地面成15°
角运行,以保证必要的离地间隙。
1.2叉取货物
当装载机驶近堆料前1~1.5m处时,换入低挡,并下降动臂使叉架底面贴地,以全力切进料堆。
在叉取货物时,一般采用两种方法,即一次切入叉装法和复合叉装法。
前者是叉架一次切进货物堆,随后叉架上转,再提升动臂完成叉取作业;
而后者是利用多次边切进边上转叉架的复合动作,来完成叉装货物。
由于复合叉装法能缩短作业循环时间约10%,故采用较为广泛。
1.3叉架提升
完成叉装作业后,为保证装载机移动和不使货物散落,叉架应提升某一高度,该动作是通过液压系统完成,由动臂操纵杆予以控制。
1.4稳载运行
装载机完成上述动作后,后退一定距离,并转向驶向运输车辆或卸货点,并再度举升叉架。
1.5卸货
动臂举升至卸物位置(以叉架前翻时不致碰到车厢边缘为限),对正车厢后,使叉架前翻将货物卸入运输车辆,随后返回货物堆,进行循环作业。
2装载机作业方式
装载机的作业方式一般有两种:
(1)汽车停稳后不动,装载机在叉架叉取货物后,后退并转向驶进汽车卸货物,然后返回重新叉取物料;
(2)装载机和汽车联合工作,装载机垂直于货物堆前进和后退进行装卸,而汽车则平行于货物堆往返行驶。
根据装卸货场地的条件,为方便装卸作业,还可以采用其他作业方式。
如将汽车垂直于货物堆停放,装载机往返、转向进行装卸。
也可以将汽车停放在距货物堆较远处,装载机在货物堆与汽车之间来回进行装卸。
限于货场条件,可选用不同的作业方式,完成装卸作业。
3装载机的工作装置
装载机工作装置的种类很多,工作装置由叉架、动臂、摇臂、连杆、转斗油缸、动臂油缸以及液压统等组成。
A、B、C、D4个铰接点和E、F、G、H4个铰接点各构成1个四连杆机构,2个四连杆机构便构成了整个工作装置的连杆构。
在动臂油缸和转。
架油缸的作用下,可保证叉架在地面位置能自动放;
叉取货物后,使叉架口向上,货物不易散落;
动臂升起时,叉架能作近似于平行的移动;
在最大起升高度时,叉架能做达到要求的翻倾角度的各种动作。
3.1叉架
叉架是装载机用来叉取货物的工具,它是具有一定挂去叉体的焊接件。
架壁为垂直状结构,以便叉装稳载货物,叉尖用耐磨材料制造,以延长叉架的使用寿命,叉架上部和各板连接角处均用角钢或钢板加焊,以加强叉架的刚度。
为避免叉架举高时,货物散落造成事故,叉架中部用挡板做栏,并与侧架连接,主架板和侧架板直接与物料接触,磨损较严重,一般采用硼钢制造。
在主架板上还可以安装楔形斗齿,用叉取硬质物料,并可以在磨损后随时更换。
叉架背面焊有与动臂和连杆连接的支撑板,上、下支撑板之间用连接板连接,以增加其连接强度和加强叉架的刚度。
叉架还焊有上、下限位挡板,用以限制叉架翻转的极限位置,避免连杆机构出现死点位置和发生机构干涉现象。
3.2动臂
动臂是工作装置中受力最大的构件,其他零件均安装在它上面,因此动臂应有足够的强度和刚度。
其外形通常有直线形和曲线形两种,断面形状多为变断面,以适应动臂的受力特点。
装载机动臂是以两块厚钢板组焊而成的弯曲形动臂,在左、右动臂之间以横梁加固,构成整体式的坚固构架。
近年来,单板式动臂应用比较广泛,即整个动臂由一块钢板切成,结构简单、加工方便。
在两侧动臂之间加焊坚固的横梁,该横梁同时用作摇臂支架,使动臂质量大为减小。
3.3连杆机构
装载机的连杆机构,既是工作装置中的连接件,又是传力件,它应保证叉架的叉取、卸料以及上升、下降的运动要求,同时传力可靠。
连杆机构的种类很多,有反转连杆机构、正转连杆机构和正转双摇臂连杆机构等多种。
为保证叉架平移和翻转等方面的要求,通常将各连秆机构均设计成非平行的四连杆机构。
连杆机构各铰点的布置方案,一般由总布置采决定。
1.1装载机前车架结构设计及强度校核
装载机在作业过程中,由于受工作环境恶劣、工作时间长等因素影响,前车架结构频繁发生断裂、弯曲等现象,尤其是工作装置承载位置的结构问题尤为突出,严重影响了产品的可靠性。
因此,在我们团队在设计阶段,采用科学、高效的设计方法,以装载机前车架为分析基础,论述了其结构设计过程以及进行应力、应变的校核及验证方法。
1.1.1结构参数对比分析
装载机前车架结构起到铰接后车架、连接前轮驱动桥以及承载工作装置的作用,结构如图1所示。
从后车架铰接位置、工作装置承载位置、前轮驱动桥连接位置三个方面进行结构参数对比。
图2给出了工作装置承载位置的结构对比情况,图3给出了后车架铰接位置、前轮驱动桥连接部位的具体结构。
对比分析图2和图3,可以得到以下结论:
(1)工作装置承载位置按结构的不同可分为两大类型:
1)顶板式,如图2(a)所示;
2)侧板式,如图2(b)所示。
鉴于前者结构存在装配复杂、工艺流程繁琐、维修不便等缺点,因此,考虑采用后者的结构形式。
(2)后车架铰接位置、前轮驱动桥连接位置结构基本相同,主要区别在于加强板、加强筋的焊接位置略有区别。
根据以上两点,结合相关结构设计经验,绘制三维模型。
设计方案是:
工作装置承载位置采用侧板竖置、圆钢管横置支撑相结合的结构形式,如图4(a)所示。
后车架铰接位置、前轮驱动桥连接位置结构用U形筋板、弧形板进行加强处理,如图4(b)所示。
1.1.2力学计算分析
根据工作装置的工况不同可以分为叉取、提起、抬升、卸物4个过程。
由于在抬升工况中,工作装置处于持续运动状态下,车架相应连接位置结构受力情况较为复杂;
另外在抬升过程中,当A,C两点连线与货物重心方向垂直时(图5),车架相应连接位置结构承载力矩最大[2]。
鉴于以上两点分析,选取工作装置抬升工况中,其动臂处于水平条件下的状况(即A,C两点连线处于水平位置)进行车架工作装置连接位置结构瞬态受力分析。
图中:
D,F两点和E,H两点是液压缸弹性连接点;
J,G两点是连杆刚性连接点;
C点与动臂藉销轴连接。
已知装载物料质量M=1500kg,由力、力矩平衡原理,经计算:
C点受力FC=94845N;
D点受力FD=6158N,方向是DF连线;
E点受力FE=47830N,方向是EH连线。
1.1.3结构优化方案及强度校核
优化方案是:
在侧板上C点左右两个铰接孔位置增加加强圆板、支撑板;
在此基础上,E点左右两个铰接孔位置会显得比较薄弱,因此,也相应增加强耳板,见图7(a);
另外前车架内侧放置加强横梁板,见图7(b)。
1.1.3.1应力校核过程
由应力基本方程式:
σ=F/A可知[8]:
在压力F一定的条件下,应力σ与受力面积A成反比关系。
具体方案为:
在保持铰接孔径Φ不变的前提下,利用如图7(a)所示的在侧板上4个铰接孔位置添置加强圆板、加强耳板来增加等效线性宽度B,如图8所示(即图5中C,E两点位置分别在Y向的投影宽度尺寸B1与B2之和),从而达到增大受力面积、降低应力的目的。
σ=F/A,推导如下方程式:
F=σfmax×
Af=σrmax×
Ar
(1)
Af=0.5×
π×
Φ×
Bf
(2)
Ar=0.5×
Br(3)
零部件满足强度要求方程式[7]:
σrmax≤[σb]/K(4)
σfmax=σcmax(5)
由公式
(1)、
(2)、(3)、(4)、(5),得到强度校核方程式:
σrmax=(Br/Bf)×
σcmax≤[σb]/K(6)
式中:
Bf,Br———分别为结构优化前、后C点的等效线性宽度,mm;
σfmax,σrmax———分别为结构优化前、后C点的最大应力值,MPa;
K—钢材基本安全系数(一般情况下,取2.0~2.5)。
已知:
Bf=24mm,Br=96mm,[σb]=530MPa,σcmax=600MPa,K=2.5。
由方程式(6)得到:
σrmax=150MPa,[σb]/K=212MPa。
最大应力值在安全范围内,应力情况得到了极大改善。
1.2装载机摇臂的分析
1.2.1工况与载荷分析
装载机工作装置结构如上图所示。
摇臂上铰孔与转斗液压缸铰接相连,中轴套与动臂铰接相连,下铰孔通过拉杆与叉架相连。
叉架的上下翻转通过转斗液压缸的伸缩来实现,从而实现装载机装卸货物的功能。
摇臂是由2块侧板、1块上封板和1块下封板焊接而成的箱型结构(见左图),中轴套穿过左右侧板,上下铰接孔处焊圆搭。
结合装载机的典型作业过程,根据经验,选取两种作业工况来计算摇臂强度。
(1)工况一:
在地面位置拉起物料此工况下的载荷情况如下图所示,转叉液压缸活塞杆伸出,推动摇臂顺时针转动,从而带动叉架克服货物阻力M逆时针转动,实现货物拉起。
按最大叉架拉起力计算,摇臂上铰点的作用载荷等于转叉液压缸的最大推力F推=πpD2/4,式中:
p为系统工作压力,Pa;
D为转叉液压缸内径,m。
代入相关参数,可计算得出F推=508938N。
(2)工况二:
最高位置处卸载货物此工况下的载荷情况如左图所示。
转叉液压缸活塞杆向里收缩,拉动摇臂逆时针转动,从而带动叉架克服斗装物料重量G顺时针转动,实现货物卸载。
按最大卸载能力计算,摇臂上铰点的作用载荷等于转叉液压缸的最大拉力F拉=πP(D2-d2)/4,式中:
d为叉架转叉液压缸活塞杆直径,m。
代入相关参数,得出F拉=408407N。
1.2.2摇臂结构的分析
两种工况下最大应力均出现在上铰点侧板处,是明显的应力集中区域,与开裂部位相吻合。
工况一下的最大应力值达307MPa,由于摇臂采用的材料为Q345,其屈服强度为345MPa,故其安全系数S=345/307=1.12;
工况二下的最大应力为267MPa,其安全系数S=345/267=1.29。
1.3装载机叉架叉拉过程受力分析
1.3.1叉拉过程分析
装载机的主要功能是叉拉货物并运送到指定地点。
在叉拉过程中,叉架缓缓升起。
装载机在叉拉时,叉架的叉拉阻力由5个作用力组成,如右图所示。
1.3.1.1沿叉架刃方向的插入阻力F1
F1=k0ρgSHcosα
(2)
k0—被叉拉货物的插入阻力影响系数;
ρ—物料密度,kg/m3;
g—重力加速度,9.8m/s2;
S—叉架叉拉截面积,m2;
H—填土高度,m;
α—水平方向与叉架运动方向之间的夹角,(°
)。
1.3.1.2铲斗底部阻力F2
F2=μF1sin(α-β)(3)
μ—摩擦系数;
β—叉拉刃与水平方向的夹角,(°
由图4(b)及公式(3)可知,当α>
β时,叉架能够沿运行方向向前叉拉,否则叉拉阻力大于叉拉作用力,使叉架无法正常叉拉货物。
1.3.1.3铲掘物料的重力F3
F3=Mg(4)
M—叉架中的货物质量,kg。
1.3.1.4叉架与叉架上货物之间的摩擦力F4
F4是叉架上货物与叉架之间的相对滑动或移动
引起的摩擦力。
F4=μF3cosβ+μF5cos(φ-β)(5)
φ—摩擦内角,(°
);
F5—叉架前端的滑动力,N。
1.3.1.5叉架前端的滑动力F5
随着不同阶段的叉拉,滑动力F5会发生变化。
在叉拉第二阶段,叉架内部物料会形成一个虚拟面来推动叉架外部货物。
根据墙体与滑移面之间的土楔整体处于平衡状态时的静力条件,可应用库伦土压力理论,将虚拟面看作为库伦土压力墙(简称库伦墙)。
应用库伦土压力理论可以估算叉拉时库伦土压力墙所受到的压力,如上图所示。
图中,D为已经叉入架上的货物,E为正在叉拉的货物,F为尚未叉入架上的货物。
正在叉拉的物料E不断压缩已经叉入架内的货物D,并形成库伦土压力墙,此过程产生库伦土压力。
依据文献,求得库伦土压力计算方程:
FP—库伦土压力,N;
ε—库伦墙与垂直方向的夹角,(°
δ—库伦土压力FP与库伦墙背面法线方向的夹角,(°
γ—货物堆上表面与水平方向的夹角,(°
利用库伦土压力可以计算滑动力F5,如果F5大于F4,叉架上的货物将发生移动,叉架之外的货物被叉入叉架。
叉架叉拉作用力要保证大于力F5,否则装载机将无法正常叉拉货物。
因此,对滑动力F5是装载机正常运作的关键。
2.1创建零件模型
利用Pro/E.依照工作装置零件尺寸,建立工作装置的零件模型。
在建模过程中,要根据零件不同的几何特征选择生成命令。
尤其要注意各个零件上饺销孔的相对位置一定要准确。
在模型创建过程中主要用到拉伸、对称、旋转和打孔等命令。
如果命令选择得合适,模型建立就叮以节省很多时间,相反则要耗费很多时间,并且模型也不一定准确,并为后面的特性分析带来误差。
建模流程如右图。
2.2模型装配
零件模型的建立仅仅是完成了一个个单独的零件横型,而一个产品往往是由很多个零件组装在一起形成的。
装配命令就是将分别建立的零件模型组装在一
起形成一个完整的产品。
零件装配是通过定义零件模型之间的装配约束米实现的也就是在各零件之间建立一定的链接关系,并对其进行约束,从而确定各零件在空间的具体位置关系。
可以这样说,零件之间的装配约束就是实际环境中零件之间的设计关系在虚拟环境中的映射。
装配后的完整模型如上图。
2.3运动要素仿真分析
对模型添加运动副、驱动器使其运动起来,实现机构运动仿真。
此外完成机构运动仿真后,运用机构中的后处理功能可以查看当前机构的运动.并可以对机构进行轨迹、位移、速度和运动干涉情况的分析,以便研究机构模型。
总结上述设计过程,可将设计顺序分为四个阶段:
参数对比、仿真分析、优化验证、整体完善。
我们团队论述的设计方法的创新点在于:
1)在仿真分析阶段:
采用次要位置结构预加强与关键位置进行分析相结合的设计方法;
2)优化验证阶段:
利用应力基本公式推导强度校核方程式,以仿真分析阶段的分析结果为输入参数,利用输出结果进行验证。
综上分析表明:
新型装载车结构的设计过程与强度校核方法既保证了结构的可靠性以及关键位置结构优化的准确性,提高了设计效率,减少了设计工作量,降低了设计难度,同时也在其它类型的结构设计过程中提供了一种新的设计思路。
三、总结
在这一次的机械设计中,我收获良多,学会了很多书本上不曾学到的,以前所不懂的知识,深深地会到了团队合作的重要性。
我们小组之前没考虑好课题,老师给了我们一个课题—鱼丸机后经大家的商讨,出于难度兴趣等方面考虑,我们组最终放弃了这个课题。
考虑到大家的能力问题,最终我们小组决定借鉴学长之前设计的课题—叉车。
通过对这个课题的深入了解,得出一些更为实用便捷有效的方案,最终做出了我们的一些改进。
在决定好课题之后,我们便开始了课题的具体设计。
我们大量翻阅了各种资料,并在网上进一步收集有用的课件、文档。
在六人的小组中,我们小组进行了具体的分工,整个小组多次讨论,大家博思集义,取其精华,弃其糟粕,广泛地综合了各方的意见,最终才有了我们现在这一份较为成熟的方案。
功夫不负有心人,们群策群力,分工合作,从开始便定下了最初的方针路线,最后经过大家的共同努力,我们一步步的朝着我们的目标前进。
虽然我们有过争执,但是我们都是朝着共同目标奋斗,都是为了能够好好地完成这个课题,我们在争执中体会团队合作,学会团队合作,在挫折中成长。
从零开始,到现在的课题设计结束,这是一次奇妙的体会,一次青春的成长,一笔人生中的财富,现在回想起,却也不是为一次记忆犹新的体验。