晋开实习报告Word文档下载推荐.docx
《晋开实习报告Word文档下载推荐.docx》由会员分享,可在线阅读,更多相关《晋开实习报告Word文档下载推荐.docx(28页珍藏版)》请在冰点文库上搜索。
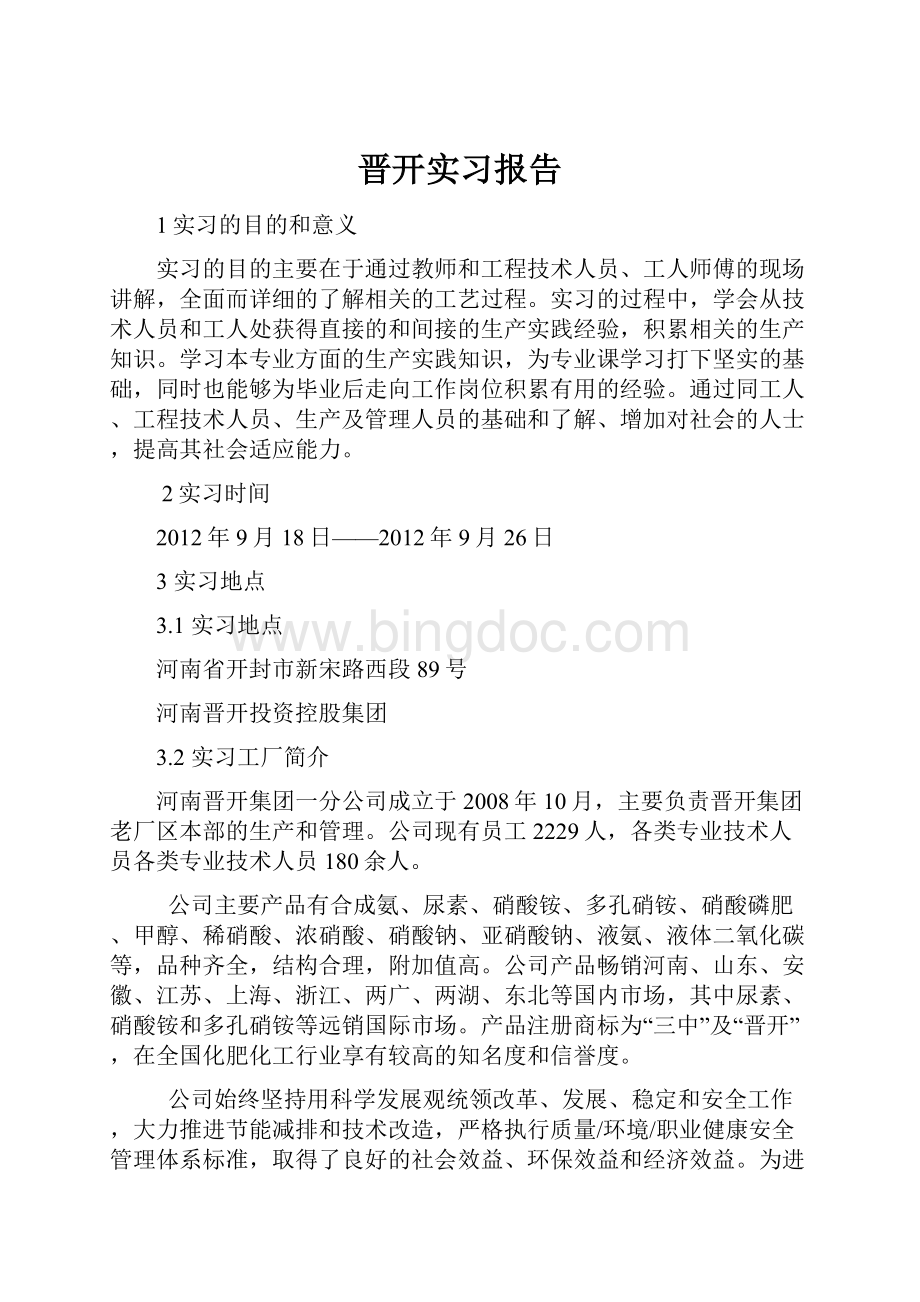
2.保持信息畅通。
在实习过程中不得任意离开实习队伍,如果需要离开则必须请假;
到任何地方都要至少两人结伴;
3.不得任意操作设备以及进入大型设备、塔类设备、空罐、低洼地带等有可能发生危险的地方;
4.在实习过程中要注意周围的环境。
在工厂内走动时(特别是在转弯处时),要注意机动车辆,防止伤害;
5.在实习过程中注意各种安全标识,以避免伤害;
6.实习过程中,当离开某处时最后离开的同学应该注意是否有同学落下。
4.1.2厂方安全教育
2012年9月18日上午我们来到了晋开集团第一分公司。
在进入主厂区之前,厂方安全环保部的工作人员对我们进行了简单的安全教育。
进场须知如下:
1、严禁在厂区吸烟;
2、在厂区内靠右行驶;
3、在厂区内操作设备要有安全证件,如动火证(此次实习不需要办理)
4、高空作业时必须携带安全设施,如安全帽,
5、使用灭火器,厂区内大部分为干粉灭火器,适用于各种火源;
泡沫灭火器在由于电引起的火灾时禁用;
6、简单逃生方法,以氨泄漏为例。
如果发生氨泄漏,应用湿毛巾捂住嘴,在往上风向跑。
7、不要随意触碰电气设备。
8、厂内火警电话:
3383319
4.2造气
4.2.1实习经过
2012年9月21日上午,热心师傅对我们进行了细致的讲解,使我们受益匪浅,下面就是我对造气这一部分的了解。
晋开造气分为两个系统,一系统和二系统。
一系统共9个炉子,二系统共20个炉子此系统中的16个炉子与一系统中9个炉子相同,均为间歇式装置只是二系统的利用率比一系统的要高,此外的4个炉子为富氧炉即炉子反应为连续式装置。
1.工艺流程
造气方法:
以碳为原料制半水煤气。
炉内工艺流程:
整个造气过程由吹风、上吹制气、下吹制气、二次上吹、空气吹净五个阶段组成,整个过程总共耗时2.5min,时间分配:
吹风19-25%、上吹制气20-24%、下吹制气39-49%、二次上吹7-8%、吹净4-5%。
制气阶段反应:
主要反应
H2O过量时
副反应
加煤方式:
采取自动加煤,每次循环下吹制气加煤,每次加煤约75kg,以便稳定炉温,增加有效制气时间。
富氧式工艺流程
煤气发生炉→旋风除尘器→1废锅炉→2废锅炉→洗气塔
间歇式工艺流程
煤气发生炉→旋风分离器→干式水封→热管换热器→洗气塔→气柜
下吹集尘器(下吹制气)
(1)吹风(吹风阶段由于产内操作规程与实际生产不符,暂且写理论步骤):
鼓风机→空气总管→吹风阀→煤气炉→旋风除尘器→吹风气回收阀→吹风气回收系统→烟囱放空
(2)上吹制气:
蒸汽和加氮空气→煤气炉→旋风除尘器→上行煤气阀→干式水封→热管换热器→洗气塔→气柜(净化)
(3)下吹制气:
蒸汽→煤气炉→集尘器→下行煤气阀→干式水封→热管换热器→洗气塔→气柜(净化)
(4)二次上吹:
(5)空气吹净:
空气→吹风阀→煤气炉→旋风除尘器→上行煤气阀→干式水封→热管换热器→洗气塔→气柜(净化)
2.各个设备作用:
煤气发生炉:
使燃料与气化剂在此设备内作用制得合乎规格的半水煤气或水煤气。
旋风除尘器:
除去煤气中的细灰,减少锅炉热管磨损。
因为从煤气炉出来的煤气到旋风除尘器后,因体积扩大使气流速度降低,气体碰到室壁可以出去煤气中的部分灰量不致带入热管换热器,煤气成切线方向进入旋风除尘器,提高除尘效率。
集尘器:
除去气体中的大颗粒灰尘,当气体由炉内以很大的速度进入集尘器时,由于气体碰壁和方向的改变,使气体流速大为减弱,因而气体中一些灰尘便依靠自己的重量而落下,起到初步除尘的作用。
干式水封:
防止煤气炉在停炉检修时,总管里的煤气倒回单炉系统而发生爆炸。
热管换热器:
回收上下吹煤气的热量,产生低压蒸汽,为煤气炉制气或其他化工生产提供一部分蒸汽。
洗气塔:
洗涤煤气灰尘和一部分可溶性气体(如硫化氢,二氧化碳)以减少设备的堵塞腐蚀,并冷却煤气使煤气中的大部分水蒸气冷凝,随冷却水经塔外溢流水封一起排出,所以洗气塔亦可以说骑着气体部分净化干燥的作用。
蒸汽缓冲罐:
煤炉运转时,制气用的蒸汽式间歇送入的,在吹风时不用蒸汽,蒸汽总管中的压力就升高,多用蒸汽时,蒸汽压力就降低,这种现象影响压力波动很大,压力波动大,就使进入煤气炉中的蒸汽也波动。
蒸汽缓冲罐的作用就是减少这种压力波动情况。
空气鼓风机:
供给煤气炉吹风用空气及加氮空气。
现场观看的主要设备记录:
中心管,煤气再此管内反应;
灰斗(2个),盛放炉渣。
空气阀一个,混合器控制总阀一个,氮气阀一个(一般不开,调节氮气比例用),上吹阀一个,下吹阀一个;
旋风分离器;
集尘器;
热管换热器,两进两出,过热段,进饱和水蒸汽,出过热蒸汽,加热段,进冷却水,出饱和水和饱和水蒸汽;
汽包(与煤气发生炉连接)与联合汽包(与热管换热器连接),换热过程中起气水分离作用,冷却水循环继续与对应的炉子换热,(汽包与联合汽包)出来的饱和水蒸汽进入到热管换热器的过热段;
蒸汽缓冲罐,处理过热段过来的过热蒸汽。
3.气化过程的工艺条件
(1)温度:
燃料层温度是沿着炉的轴向而变化,以氧化层温度最高。
操作温度一般指氧化层温度,简称炉温。
如前所述,高炉温对制气阶段有利,从化学平衡角度分析,高温时煤气中一氧化碳与氢气含量高,水蒸气含量低;
从反应速度来说,高温下反应速度加快。
总的表现为蒸汽分解率高,煤气产量高,质量好。
但炉温是由吹风阶段确定的,高炉温将导致吹风温度高,而且一氧化碳含量高,造成热损失大。
未解决这一矛盾,在流程设计中,应对吹风的显热及燃烧热作充分的回收,并根据碳-氧之间的反应特点,加大风速,以降低吹风过程中一氧化碳的含量,在这一前提下,以略低于燃料的灰熔点,维持炉内不致结疤为条件,尽量在将高温度下操作。
生产中测定燃料灰熔点时,多将灰渣作为角锥状,置于还原性气氛中加热,可观测到与灰熔点有关的三个温度:
1、变形温度T1——此时角锥尖峰变圆;
2、软换温度T2——角锥上部变形,劲儿倒在试台上;
3、熔融温度T3——灰渣呈熔融状,可沿试台流动。
对于固定层气化过程,灰分在T2温度时开始粘连结疤,气化条件恶化。
因此,要求燃料的T2应高于1250℃,炉温在实际操作中较T2低50℃左右。
(2)吹风速度:
提高炉温的主要手段是增加吹风速度和延长吹风时间。
后者使制气的时间缩短,不利提高产量,而前者对制气时间无影响。
在氧化层中,碳的燃烧反应加速较快,属扩散控制;
而在还原层中,二氧化碳的还原反应速度较慢,属动力学控制。
所以,提高吹风速度,可使氧化层反应加速,且使二氧化碳在还原层中停留时间减少,最终变现为吹气中一氧化碳含量的降低,从而减少了热损失。
但风量过大,将导致飞灰增加,燃料损失加大,甚至燃料层出现风洞以致被吹翻,造成气化条件严重恶化。
(3)蒸汽用量
蒸汽用量是改善煤气产量的重要手段之一,此量随蒸汽流动和加入的延续时间而改变。
蒸汽一次上吹制气时,炉温较高,煤气产量与质量较好,但随着制气的进行,气化区温度速度下降并上移,造成出口煤气温度升高,热损失加大,所以上吹时间不宜过长。
蒸汽下吹时,使气化区恢复到正常位置,特别是对下垂蒸汽进行预热的流程,由于蒸汽温度较高,制气情况良好,所以下垂时间比上吹长,但蒸汽用量过大将导致蒸汽分解率降低。
一般而言,风量每增加1500m3/h,可增加蒸汽流量0.25t/h。
蒸汽用量改变0.25t/h时相当于改变1%制气百分比,在调节两者之间的分配时,以改变百分比的效果更好。
通常调节上下吹百分比和蒸汽用量的主要依据是根据单炉上下吹气体成分中二氧化碳含量多少和蒸汽分解率高低来确定的。
入炉蒸汽压力对气化的影响:
当入炉蒸汽压力提高后,因蒸汽的密度增加,故而蒸汽的比容减少。
即在相同的重量条件下,通过燃料层的流速也随之减慢,因而延长了蒸汽在炉内的停留时间,故而有利于蒸汽分解率的提高。
而且根据气化反应动力学的原理,入炉蒸汽压力越高,则进入燃料层的阻力越小,反之,入炉蒸汽压力越低,则进入燃料层的阻力越大。
生产中,还可在制气阶段加入部分空气。
这样,在进行蒸汽分解反应的同时亦有碳的燃烧反应,如此即可缩短吹风时间,反而有利于燃料层温度的稳定,在制气阶段加入的空气由于增加了水煤气的氮含量,故称“加氮空气”。
(4)燃料层高度
对制气阶段,较高的燃料层将事水蒸气停留时间加长,而且燃料层温度较为稳定,有利于提高蒸汽分解率。
但对吹风阶段,由于吹风空气与燃料接触时间加长,吹风气中一氧化碳含量增加。
根据实践经验,对粒度较大、热稳定性较好的燃料,采用较高的染料层是可取的。
但对颗粒小或热稳定性差的燃料,则燃料层不宜过高。
(5)循环时间及其分配
每一工作循环所需的时间称为循环时间。
一般地说,循环时间长,气化层温度和煤气的产量、质量波动大。
循环时间短,气化层的温度波动小,煤气的产量与质量也较稳定,但阀门开关过于频繁,易于损坏,根据自控水平及维护炉内较为稳定的原则,一般循环时间为120s左右。
循环时间一般不做随意调整,在操作中可由改变工作循环个阶段时间的分配来改善气化炉的工况。
循环中个阶段的时间分配,随燃料的性质和工艺操作的具体要求而异。
吹风阶段的时间,以能提供制气所必需的热量为限。
其长短主要取决于燃料灰熔点及空气流速等。
空气流速较大可缩短吹风时间。
上下吹制气阶段的时间,以维持气化区稳定,煤气质量高及热能的合理利用为原则。
二次上吹和空气吹净阶段的时间短,以能够达到排净气化炉下部空间和上部空间残留煤气为原则,后者还可兼调节煤气中氮含量,但一般较少改变。
(6)气体成分
主要调节半水煤气中一氧化碳和氢气与氮气的比值。
方法是改变加氮空气量,或改变空气吹净时间。
在生产中还应经常注意保持半水煤气中低的氧含量(不大于0.5%),否则将引起后继工序的困难,氧含量过高还有爆炸的危险。
(7)燃料品种的变化与工艺条件的调整
气化操作中,优质的固体燃料(焦炭或无烟煤),一般具有灰熔点较高,机械强度及热稳定性良好,粒度均匀等特点,对固定层煤气发生炉气化时允许染料层较高,吹风速度大,炉温高,因而蒸汽分解率高,煤气产量大;
而对劣质的固体燃料,则应根据具体情况调整工艺操作指标。
入灰熔点低,则吹风时间不宜过长,适当提高上吹蒸汽加入量,以防结疤。
对含固定碳低的燃料,应勤加料,勤排渣,以提高气化强度。
对机械强度及热稳定性差的固体燃料,则宜采用低燃料层气化,以减少床层阻力。
综上所述,间歇式气化过程的操作中,首先根据燃料的粒度与灰熔点确定吹风阶段的时间百分比,吹风风量及蒸汽用量。
视炉温情况调整制气各阶段的时间分配,根据气体成分调节加氮空气量或空气吹净时间。
应尽量维持气化区位置的相对稳定。
防止因局部温度过高造成严重结疤,或因出现风洞以及阀门泄漏而使煤气中氧含量增高。
应做到综合考虑,及时处理,以提高制气效率。
4.提出问题和解答
问:
整个生产过程中半水煤气的含氧量控制在多少?
答:
理论值:
0.5%,晋开:
0.23%。
一氧化碳和氢气与氮气比例?
3.1-3.2。
什么时候进料?
下吹制气加煤。
4.3净化
4.3.1实习经过
2012年9月24日,由于我们是去净化的第二个分队,师傅给我们讲解一下大致的过程,然后带领我们去车间参观学习。
1.净化车间工艺流程
从651来的半水煤气经655气柜入口水封进入655气柜,从655气柜出口水封进入电除尘,除尘后的半水煤气进入煤气风机进口总管,通过风机加压后大部分送往后工序,少部分通过大循环阀回到进口煤气总管,使煤气系统保持相对平衡。
从煤气风机出来的半水煤气经脱硫前冷却塔降温后进入三个并联脱硫填料塔,与从塔顶喷淋而下的脱硫溶液逆向接触,以脱出半水煤气中的H2S。
脱除H2S的半水煤气沿煤气管进入三个并联的冷却塔底部自下而上冷却降温,降温后的半水煤气沿塔后两根煤气总管进合成压缩机一段,半水煤气压缩机加压后,从压缩机三段出口进焦碳过滤气,除去所夹带的油污后进入加压变换半水煤气预热器壳程,与来自脱碳变煮器的变换气换热后,温度升高,再进入半水煤气换热器Ⅰ的管程与低变炉一段来气换热,然后经蒸汽混合器,调节汽气比后,送入半水煤气换热器Ⅱ的管程,与中变炉三段出来的中变气换热升到反应温度后进入中变炉一段,在催化剂的作用下进行绝热反应,经一段反应温度升高后,进入增湿器Ⅰ,利用喷水汽化法直接加入水蒸汽或冷煤气进行冷激降温,降温后的一段变换气重新进入中边路二段进行反应,温度升高后再次离开中变炉,进入增湿器Ⅲ,采用与增湿器Ⅰ同样的方法使二段变换气降温,降温后的二段变换器,重新进入中变炉的三段进行反应,当CO满足系统要求后,离开中变炉,高温气体进入半水煤气换热器Ⅱ的壳程,换热后进入增湿器Ⅱ,经喷水降温后进入低变炉一段,由于反应放热,温度升高,因此一段反应后离开低变炉进入半水煤气换热器Ⅰ的壳程,与半水煤气换热降温后,再进入低变炉二段进行低变反应,使CO满足系统要求后离开低变炉,彻底完成CO的变换反应,进入脱碳系统煮沸器,利用其热量后,再次回到变换系统的半水煤气预热器管程降温后进入低变分离器,经分离冷却液后进入两个并联的变脱塔,自下而上与从塔顶喷淋而下的脱硫溶液逆流接触,脱除残余H2S后由塔顶进入塔后分离器,分离出所夹带溶液后进入两并联的脱碳吸收塔底部,与脱碳溶液在贫液段和半贫液段逆向接触,脱除大部分CO2后分别进入净化气冷却器冷却降温,降温后的净化气经分离器分离出溶液组分后进入精脱硫塔,脱除残余的有机硫和H2S后,沿“84”总管进入压缩机的4段和3D压缩机进行后工序生产。
2.厂区净化车间气体输送流程
1.进入655气柜→2.除尘塔→3.静电除尘塔→4.送入罗茨风机→5.冷却塔→6.脱硫塔(两个,可串可并)→7.清洗塔→8.静电除焦塔(3个,并联)→9.压缩机一段→10.加压变化丝网过滤器→11.净化炉→12.前换热器→13.后换热器→14.变换炉一段→15.增湿器一段→16.变换炉二段→17.增湿器二段→18.变换炉三段→19.前换热器管程→20.软水加热器→21.变换气冷却器→22.气水分离器→23.两个并联的变脱塔→24.PSA变压吸附装置→25.两个精脱塔→26.压缩机四段→27.生产车间
3.主要工艺指标
1.665气柜高度:
3000-8000m³
,大风天气3000-6000m³
2.半脱出口H2S的含量:
80-150mg/m³
3.压缩一段进口温度:
冬季:
≤30℃,夏季≤40℃
4.变换炉入口H2S含量:
(根据生产要求调整)
5.变换炉热点温度:
200-400℃
6.变脱后H2S的含量:
≤10mg/m³
7.精脱出口H2S的含量:
≤0.1ppm
8.净化气中CO2含量:
≤1.3%
4.生产原理
1.静电除尘
半水煤气自上而下通过电除尘沉淀管时,在高压静电作用下,管中新电晕极产生电晕放电,形成不均匀电场,使煤气中的尘粒被电离或带电向两极移动,绝大部分粉尘移向阳极管(沉淀极),被沿管内壁自上而下连续冲水带出,电晕极上尘粒被间断冲水冲走,从而使半水煤气中所含尘粒得以净化进入652风机岗位。
2.脱硫
合成氨所需的原料气,含有一定数量的硫化氢,其次是二硫化碳,硫氧化碳,硫醇,硫醚和噻吩等有机硫。
按脱硫剂的物理形态,脱硫方法可分为两大类。
1、干法脱硫
(1)无机硫:
可用吸附法——分子筛法
接触反应法——氧化铁、氧化锌、氧化锰法
(2)有机硫:
转化法、钴钼加氢法
2、湿法脱硫
①化学吸收法:
氨水催化、ADA法、栲胶法、乙醇胺法等
②物理吸收法:
低温甲醇洗涤法
③物理、化学吸收法
(2)有机硫
冷NaOH吸收法(脱出硫醇)
热NaOH吸收法(脱出硫醚)
目前晋开公司利用栲胶法氧化脱硫,自吸空气喷射再生流程,其反应机理如下:
(1)碱性溶液吸收硫化氢
(2)硫氢化钠与偏钒酸钠反应生成焦钒酸钠,析出单质硫
(3)氧化态栲胶[T(OH)O2]将焦钒酸钠氧化成偏钒酸钠。
即醌态栲胶氧化四价钒,同时被还原成还原态栲胶[T(OH)3]
(4)还原态栲胶的氧化
(5)反应生成的NaHCO3和NaOH作用生成Na2CO3
(6)未能被氧化的V4+、HS-1被H2O2氧化
(7)副反应
①若气体含有CO2、HCN、O2将发生下列副反应
②H2O2与硫化物将发生下列反应
3.加压变换
由固体原料制得的半水煤气含有30%左右的CO,CO并不是合成氨生产所需要的原料气,反而可使氨合成触媒中毒,因此在合成前必须将其除掉。
工业上从用挂在触媒的作用下,用水蒸汽和CO作用,大部分CO转化为易被脱除的CO2,同时获得合成氨所必须的氢气,并放出大量热,其反应式为:
由反应式知:
(1)反应前后体积不变,从化学平后角度来看,提高压力不能使化学反应向正方向移动。
但提高压力,可以是反映速度加快。
(2)反应为放热反应,降低温度反应向右移动,有利于CO的变换。
但触媒只有在一定温度下才具有较高的活性,所以一般操作温度都是根据出酶活性温度的不同而不同,一般中变触媒的操作温度为350-500℃,低变触媒的操作温度在190-300℃。
(3)增加反应物蒸汽的量可以使反应向右移动,有利于提高CO变换率,但CO变换率并不是与蒸汽量成正比增加。
同时蒸汽用量过大,系统阻力增加,冷却负荷大,对低变炉内催化剂不利、腐蚀范围扩大等所以要有适当的汽气比。
加压变换一般控制蒸汽/煤气=0.4
4.脱碳
变压吸附过程包括吸收一段、吸收二段和精脱。
其装置为两组串联的吸附罐和两个串联的精脱塔以及一系列的真空泵和缓冲罐。
在吸附一段里,经过十次均压(十次升压和十次降压),将二氧化碳的含量控制在8.0%-10.0%左右;
在吸附二段里,经过九次均压,将二氧化碳的含量控制在≤1.3%。
吸附罐中的主要吸附物为硅胶,它在最上层,接下来是活性炭层,最下层是Al2O3层。
活性炭主要吸附H2S等物质,Al2O3层主要吸附气体中的水蒸气。
但是,在吸附二段里吸附罐中没有Al2O3层,因为水蒸气在吸附一段里已经吸收殆尽。
每个精脱塔分两段,每段填充一种吸附剂,两个精脱塔中共四种吸附剂。
主要用于吸收无机硫、有机硫、氯离子和羟基铁等对于后续工序里催化剂有影响的物质。
从精馏塔里流出的气体进入下一流程。
4.4合成氨
在尿素的合成过程中,最基本的原料是氨气和二氧化碳,而氨气的合成是其中的重中之重,原料氨的生产成本直接影响着整个尿素合成的成本,而晋开化工集团的氨的合成就是依靠山西晋煤集团强大的煤炭供应作为后盾的。
下面介绍的就是氨的合成工艺。
1.合成氨概述
合成氨工业诞生于本世纪初,其规模不断向大型化方向发展,目前大型氨厂的产量占世界合成氨总产量的80%以上。
氨是重要的无机化工产品之一,在国民经济中占有重要地位。
除液氨可直接作为肥料外,农业上使用的氮肥,例如尿素、硝酸铵、磷酸铵、氯化铵以及各种含氮复合肥,都是以氨为原料的。
合成氨是大宗化工产品之一,世界每年合成氨产量已达到1亿吨以上,其中约有80%的氨用来生产化学肥料,20%作为其它化工产品的原料。
德国化学家哈伯1909年提出了工业氨合成方法,即“循环法”,这是目前工业普遍采用的直接合成法。
反应过程中为解决氢气和氮气合成转化率低的问题,将氨产品从合成反应后的气体中分离出来,未反应气和新鲜氢氮气混合重新参与合成反应。
合成氨反应式如下:
N2+3H2≈2NH3
合成氨的主要原料可分为固体原料、液体原料和气体原料。
经过近百年的发展,合成氨技术趋于成熟,形成了一大批各有特色的工艺流程,但都是由三个基本部分组成,即原料气制备过程、净化过程以及氨合成过程。
合成氨的原料主要是天然气,近些年来,随着天然气石油资源的逐渐减少,煤作为一种替代型原料越来越受到重视,越来越多的化工厂开始采用煤作为主要原料来制造含氢和氮的粗原料气。
而这次实习所在的晋开化工集团的母公司山西晋煤集团有着深厚的煤业背景,因此其旗下的化工子公司大多采用煤作为其原料。
由于这次实习主要是在尿素生产车间,因此对于合成氨方面的了解仅限于企业导师的讲解和提供的资料以及我自己从各个途径获得的各项资料。
下面我将从煤这个方面对合成氨的工艺流程就行介绍。
1.制备
(1)原料气制备将煤制成含氢和氮的粗原料气。
对于固体原料煤和焦炭,通常采用气化的方法制取合成气;
渣油可采用非催化部分氧化的方法获得合成气;
对气态烃类和石脑油,工业中利用二段蒸汽转化法制取合成气。
(2)净化对粗原料气进行净化处理,除去氢气和氮气以外的杂质,主要包括变换过程、脱硫脱碳过程以及气体精制过程。
①一氧化碳变换过程
在合成氨生产中,各种方法制取的原料气都含有CO,其体积分数一般为12%~40%。
合成氨需要的两种组分是H2和N2,因此需要除去合成气中的CO。
变换反应如下:
CO+H2OH→2+CO2=-41.2kJ/mol0298HΔ
由于CO变换过程是强放热过程,必须分段进行以利于回收反应热,并控制变换段出口残余CO含量。
第一步是高温变换,使大部分CO转变为CO2和H2;
第二步是低温变换,将CO含量降至0.3%左右。
因此,CO变换反应既是原料气制造的继续,又是净化的过程,为后续脱碳过程创造条件。
②脱硫脱碳过程
各种原料制取