FDM技术描述.docx
《FDM技术描述.docx》由会员分享,可在线阅读,更多相关《FDM技术描述.docx(16页珍藏版)》请在冰点文库上搜索。
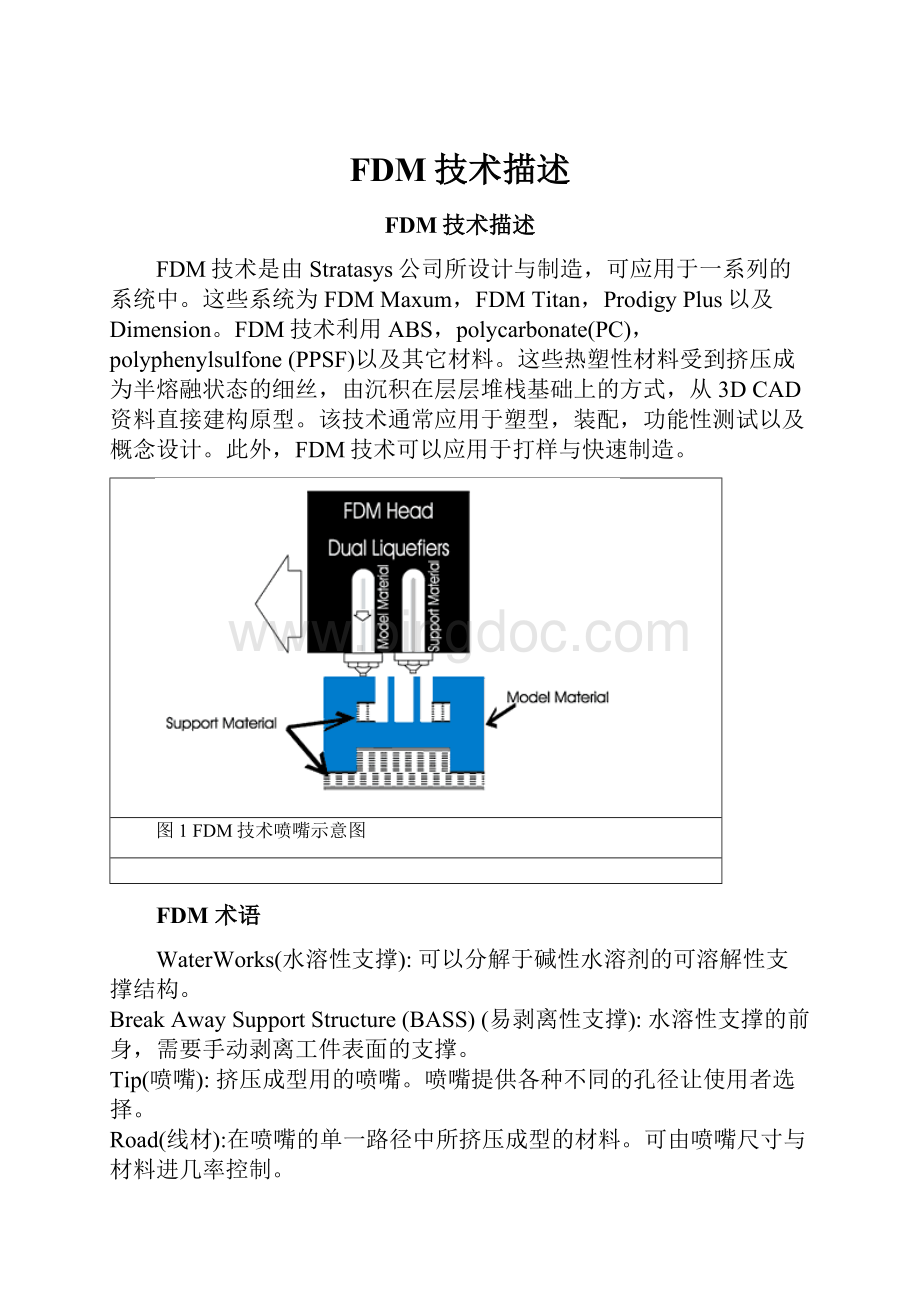
FDM技术描述
FDM技术描述
FDM技术是由Stratasys公司所设计与制造,可应用于一系列的系统中。
这些系统为FDMMaxum,FDMTitan,ProdigyPlus以及Dimension。
FDM技术利用ABS,polycarbonate(PC),polyphenylsulfone(PPSF)以及其它材料。
这些热塑性材料受到挤压成为半熔融状态的细丝,由沉积在层层堆栈基础上的方式,从3DCAD资料直接建构原型。
该技术通常应用于塑型,装配,功能性测试以及概念设计。
此外,FDM技术可以应用于打样与快速制造。
图1FDM技术喷嘴示意图
FDM术语
WaterWorks(水溶性支撑):
可以分解于碱性水溶剂的可溶解性支撑结构。
BreakAwaySupportStructure(BASS)(易剥离性支撑):
水溶性支撑的前身,需要手动剥离工件表面的支撑。
Tip(喷嘴):
挤压成型用的喷嘴。
喷嘴提供各种不同的孔径让使用者选择。
Road(线材):
在喷嘴的单一路径中所挤压成型的材料。
可由喷嘴尺寸与材料进几率控制。
物理属性
符合原型应用的物理需求,大概是选择快速原型技术的最重要因素。
快速原型的物理属性将定义他的品质并决定赋予的应用成败。
工程材料属性
当询问到重要性的排序,快速原型的使用者通常会声明材料属性是最重要的考虑。
致力于工业需求,符合这些预期用来生产的材料的材料属性是很重要的。
而这是FDM技术最重要的强项之一。
当Stratasys公司制造用于FDM技术的所有材料,每一项都是从商业上可用的热塑性树脂来生产。
ABS:
所有的FDM系列产品都提供ABS作为材料选项,而接近90%的FDM原型都是由这种材料制造。
使用者报告说ABS的原型可以达到注塑ABS成型强度的80%。
而其它属性,例如耐热性与抗化学性,也是近似或是相当于注塑成型的工件,其耐热度为摄氏93.3度。
这让ABS成为功能性测试应用的广泛使用材料。
Polycarbonate:
可以在Titan机型上使用的一种新式RP材料--polycarbonate–正在快速成长。
增加强度的polycarbonate比ABS材料生产的原型更经得起力量与负载。
许多使用者相信该材料生产的原型可以达到注塑ABS成型的强度特性,其耐热度为摄氏125度。
其它材料:
FDM技术还有其它的专用材料。
这些包含polyphenylsulfone、橡胶材质以及蜡材。
橡胶材质是用来作类似橡胶特性的功能性原型。
蜡材是特别设计来建立脱蜡铸造的样品。
蜡材的属性让FDM的样品可以用来生产类似铸造厂中的传统蜡模。
Polyphenylsulfone,一种应用于Titan机型的新工程材料,提供高耐热性与抗化学性以及强度与硬度,其耐热度为摄氏207.2度。
图2PPSF耐高温工程材料应用于咖啡壶设计
Stratasys宣布已经针对FDM快速原型系统Titan发表PPSF材料。
在各种快速原型材料之中,PPSF(或是称为polyphenylsulfone)有着最高的强韧性、耐热性、以及抗化学性。
航天工业、汽车工业以及医疗产品业的生产制造商是第一批期待使用这种PPSF材料的用户。
航天业将会喜欢该材料的难燃属性;汽车制造业也非常想应用其抗化学性以及在400度以上还能持续运作的能力;而医疗产品制造商将对PPSF材质的原型可以进行消毒的能力感到兴趣。
测试单位,ParkerHannifin安装了一个PPSF作的模型到汽车引擎中。
该零件是一个名为crankcasevaporcoalescer的过滤器,装在一组V8引擎并作40小时的测试以决定过滤器媒介的效能。
该零件收集的燃气包含有160度的润滑油,燃料,油烟,以及其它燃烧的化学反应生成物。
ParkerHannifin的RussJensen说,“该装配件并没有产生外漏,并且其展现出与第一次装配时相同的强度与属性。
我们相当满意它的表现。
”
测试单位,MSOE(MilwaukeeSchoolofEngineering)的操作经理ShekuKamara,同样地很满意该新材料。
“当在玻璃熔融的450度时,在各种快速原型材料之中,PPSF材料还拥有着除了金属之外最高的操作温度以及坚硬度,”他说。
“在粘着剂测试期间,PPSF原型零件遭受于温度从14度到392度的考验且依然保持完整。
”
颜色
包含最常用到的白色,ABS提供六种材料颜色。
色彩的选项包含蓝色,黄色,红色,绿色与黑色。
医学等级的ABSi提供针对于半透明的应用,例如汽车车灯的透明红色或是黄色。
图3、4彩色模型装配件
属性稳定度
不像SLA以及PolyJet的树脂,FDM材料的材料属性不会随着时间与环境曝晒而改变。
就像是注塑成型的副本,这些材料几乎在任何环境下都会保持他们的强度,硬度以及色彩。
精准性
快速原型的尺寸精度取决于许多因素,而其结果可能会因为每个工件或是不同日期而有些微小变化。
需要考虑的事情必须包含已知的条件,例如量测的时间范围,工件的修整以及环境的曝晒。
Maxum,Titan以及ProdigyPlus精准度资料详见附表一。
精度测试工件如图5、6所示,在每一台机器中均用层厚0.18mm所建构以形成目前的精准性资料。
图5图标的工件试用来比较精准性
图6所示的测试工件是用来做尺寸精度及运作时间分析。
该工件是由FDMTitan在层厚0.18mm时所制作的。
MAXUM
TITAN
PRODIGY
理论尺寸
实际尺寸
百分比
理论尺寸
百分比
理论尺寸
百分比
A
76.2
76.2
0.00
76.2
0.00
76.1
0.17
B
25.4
25.5
0.30
25.5
0.40
25.6
0.60
C
152.4
152.4
0.00
152.3
0.08
152.4
0.00
D
2.54
2.51
1.00
2.54
0.00
2.54
0.00
E
76.2
76.15
0.07
76.07
0.17
76.12
0.10
F
101.6
101.57
0.02
101.42
0.18
101.50
0.10
G
25.4
25.48
0.30
25.50
0.40
25.55
0.60
H1
12.7
12.62
0.60
12.65
0.40
12.55
1.20
H2
12.7
12.62
0.60
12.67
0.20
12.55
1.20
I
12.7
12.67
0.20
12.7
0.00
12.62
0.60
J
6.35
6.43
1.20
6.55
3.05
6.48
2.00
K
12.7
12.67
0.20
12.78
0.60
12.78
0.60
表1为Maxum、Titan以及ProdigyPlus的尺寸精度资料。
所有的测试零件均用层厚0.18mm所建构。
(单位:
mm)
工件建构
一般而言,FDM技术所提供的准确性通常相等或是优于SLA技术以及PolyJet技术,且确定优于SLS技术。
然而,由于精准性是取决于许多的因素,所以矛盾的结果便会发生在个别的原型上。
FDM技术的精准性受到较少的变量影响。
用SLA,SLS以及PolyJet技术,尺寸精准性会受影响的因素有机器的校正,操作的技巧,工件的成型方向与位置,材料的年限以及收缩率。
Z轴
这并非一定都会这样,Z轴可能是被证明准确性最小的。
除了先前所讨论的变化之外,原型的高度可能由于层厚整数误差而改变。
对所有的RP系统而言都是这样的。
任何特征的表面顶端或是底端无法对齐成为一层时,在软件中的切层算法会将尺寸整数化到最接近的层厚数。
在最坏的情形下,一端的表面往下整数化而另一端向上,高度可能偏离一个层厚。
对于典型的FDM参数,这可能会产生的误差至少为0.127mm。
稳定性
尺寸的稳定性是FDM原型的关键优势,如同SLS技术,时间与环境的曝晒都不会改变工件的尺寸或其他的特征。
一但原型从FDM系统分离,当它达到室内温度后,尺寸是固定不变的。
如果温度度数变化,用SLA或是PolyJet技术则不是这样的情形。
图7大型工件的尺寸稳定
成本预估
机型:
StratasysFDMMaxum
材料费:
(按每年用量100KG计算)
100kg*36%=36kg(应用省料加工办法)
36kg*2400元/千克=86400元
喷嘴更换费:
每年需更换1次,两个喷嘴,单价150美元,折合人民币约1239元
150*8.26*2=2478元
基板费用:
每年需20张,总计232美元,折合人民币共1916元
综合预估每年使用成本为90794元(人工费及电费未计)
EOS/3DSYSTEM
材料费:
(按每年用量100KG计算)
100kg*1000元/千克=100000元
由于SLS是粉末烧结的成型原理,故无法应用省料加工技术。
而SLA需要一缸料(200KG以上)作为“底料”,使用过程中再添加新料。
100KG*2400元/KG=240000元,国产材料500-800元/KG,但材料性能与进口材料相比较差很多。
激光器更换费用:
每个激光器保用时间为5000小时,按每月25天,每天工作16小时计算
每年需更换一次,每次更换费用为20000美圆,折合人民币计165400元
平均每年费用165400圆
氮气消耗费用
氮气消耗量2天/瓶,每瓶单价200圆
每天100圆成本,每年需30000圆(每月25天*12个月)
恒温恒湿房间费用
建房费用:
200000圆
维护费用:
100圆/天
SLS综合预估每年使用成本为331900圆(人工费及电费未计)
SLA综合预估每年使用成本为431900圆(人工费及电费未计)
综合评比:
~FDM通过软件控制,可以采用省料加工技术,可降低64%材料消耗,并可提高2.5倍加工速度
~根据我厂提供的数据加工的样件,精度为0.127mm,是各个厂家中最高的.
~综合使用成本预估,FDM为82982元/年,使用成本较低
后处理输出
许多RP件都需要手工完成工件的光滑性。
例如,SLA需要从工件表面手动移除支撑结构,且工件表面需要一些手工打磨。
这表示工件的精准性不再只是受到系统精度的作用。
它现在是受到后处理技师的技术等级所控制。
对于塑型,装配以及功能性原型,多数的使用者发现FDM工件的表面精度是可以接受的。
那么,当结合了水溶性支撑以及易剥离支撑,表示FDM原型的精准性不会受到手工的改变。
当然,如果需要翻硅胶模用或是喷漆用的表面精度,FDM工件将需要后处理,如同其它的技术一样。
既然这样,工件后处理技师的技艺在可以做到的原型精度上扮演了一个关键的角色。
图8模型可烤漆
图9模型可以真空电镀
表面完工精度
受到使用者与Stratasys公司双方的公认,FDM技术最明显的限制就是表面完工精度。
由于是半熔融状态塑料挤制成型,表面完工精度比SLA与PolyJet还要粗糙,而与SLS不相上下。
当由较小的线材宽度与较薄的层厚来改进表面完工精度时,仍然可以在顶端,底面,以及侧墙看出经过挤压喷嘴的等高线轮廓与建构层厚。
表2所列的为Maxum与Titan的表面完工精度。
为了改善表面完工精度,Maxum与Titan现在都提供0.127mm层厚。
使用者发现工件的成型方向,可以满足考虑表面完工精度需求。
这些要求较高完工精度的表面通常以垂直方向成型。
较不重要的表面通常以水平方向成型,就像是底端或是顶端的表面。
如同其它技术,二次加工(后处理输出)可以用来使之相同。
然而,ABS与polycarbonate材料的硬度让打磨耗费人力。
使用者通常使用溶剂或用是粘结剂完成或是预备用打磨。
商业上可用的这些介质包含有熔接,ABS快干胶,Acetone以及two-partepoxies。
要符合足够的精度,FDM技术与竞争对手的产品都可以提供翻硅胶模用或是喷漆用的表面。
这关键的差异是要花费多少时间才能达到要求的结果。
MaxumRa(μin)
TitanRa(μin)
顶面
未处理表面
已处理表面
550
275
475
150
侧面
未处理表面
已处理表面
450
200
425
175
底面
未处理表面
已处理表面
550
125
575
100
表2:
Maxum和Titan的表面精度资料。
所有的测试零件均用层厚0.18mm所建构。
特征定义
尽管高阶的FDM系统可以生产较小的特征,大多数FDM原型的最小特征尺寸受限于两倍线材宽度。
没有使用者的介入,FDM技术使用的”closedpath”选项会限制最小特征尺寸为两倍挤压成型喷组的宽度。
对于一般喷嘴与建造参数而言,最小特征尺寸范围从0.4到0.6mm。
尽管大于SLA与PolyJet的最小特征尺寸,但是该范围是与这些技术的可用最小特征尺寸相同。
尽管SLA技术可以建造小到0.08(Vipersi2机种)或0.25mm(所有机种),以及PolyJet技术可以建造小到0.04mm,几乎很少原型会用到这些极小值的优势来作最小的细节。
考虑到材料属性,通常发现SLA技术与PolyJet技术的原型常用最小特征尺寸为0.5mm。
FDM技术的最小特征尺寸相等于或是优于SLS技术的0.6到0.8mm。
由于材料属性相似于注塑成型的ABS或是polycarbonate,FDM技术可以给予功能性特征尺寸在0.4到0.6mm范围中。
环境抵抗力
FDM原型提供的材料性质相似于热塑性材料。
这包含了环境的与化学的曝晒。
对ABS材料而言,使用者可以实验他们的原型在93度的温度下以及包含石油,汽油以及甚至某些酸类等的化学媒介。
一关键的考虑为水气的曝晒,包括浸没与湿气。
SLA技术与PolyJet技术使用的光敏树脂对于潮湿水气敏感且会受到伤害。
暴晒在水中或是湿气中不只会影响原型的机械属性,也会影响尺寸精度。
当光敏树脂的原型吸收了水气之后,他们将会开始软化并且变的有点易于弯曲。
而且,工件会有翘曲或是膨胀的倾向,这会严重影响尺寸的精度。
FDM技术的原型,以及SLS技术的原型,都不受湿气影响,所以他们可以保持原有的机械属性以及尺寸精度。
机械加工
FDM原型可以进行铣床加工,钻孔,研磨,车床加工等。
为了补偿表面精度不足并加强特征细节,当有特殊的品质需求时,使用者通常会进行二次加工来提升原型的细节。
图10原型上可进行加工处理,如锁螺丝
操作上的考虑
在考虑原型的物理属性之后,注意力应该转移至操作的参数上。
下列领域可以影响到原型在预期应用上的使用。
工件尺寸
不像某些快速原型技术,广告中FDM技术的建造范围就是最大的工件尺寸。
在家族系列产品中,FDM技术提供了广泛的建造范围。
Maxum,最超大型,所提供的工件尺寸可达600x500x600mm。
这样的建造范围与最大型的SLA系统相同。
Titan,则提供最大的工件尺寸为406x355x406mm。
这样的建造范围稍微大于SLSSinterstations系统。
ProdigyPlus,办公室桌上型,拥有的建造范围为203x203x305mm,该尺寸稍微大于PolyJet系统以及最小型的SLA系统。
当使用具竞争性的技术时,快速原型超过建造范围的部分通常分段建构然后作粘结。
使用商业上可用ABS快干胶,FDM工件的粘和强度可以满足功能性测试的应用。
此外,FDM工件可以使用超音波熔接,这种选项无法使用在SLA以及PolyJet,因为他们不是使用热塑性材料。
支撑结构
在FDM技术中,需要支撑结构来形成基底以制作工件并支撑任何超过悬挂的特征。
在工件的接口,支撑材料的坚固堆层已经放下。
在这坚固堆层下,线材为0.5mm且在间隔为3.8mm下沉积。
FDM技术提供两种类型的支撑--易于剥离支撑结构(BASS)以及水溶性支撑结构(WaterWorks)。
BASS支撑是由手工将支撑从工件表面剥离以移除。
当他们不想损坏工件表面,考虑的是必须要容易进入与接近细小特征。
水溶性支撑(WaterWorks)是使用水溶性材料,可分解于碱性水溶剂的解决方案。
不像是易于剥离支撑(BASS),该支撑可以任意坐落于工件深处地嵌壁式的区域,或是接触于细小特征,因为机械式的移除方式是可以不加考虑的。
此外,水溶性支撑可以保护细小特征。
在其它的快速原型技术中,他们要如何移除支撑而不造成特征损坏,是一项极大挑战。
一体成型的装配件
随着水溶性支撑的出现,FDM技术提供了一项独特的解决方案--建构可运转的一体成型装配件。
因为水溶性支撑可以进行分解,一个多件的装配件可以在一次机械运转中建构完成。
当多件的装配件可以在SLS或是PolyJet中实行时,要小心地考虑到残留在原件之间的材料。
举例来说,如图3所示的FDM技术的脑型齿轮组,可以不用手工劳动就能完成并用一些时间就能将水溶性支撑进行分解。
用SLS技术制作这样相同的工件,可能需要一个小时以上的手工劳动来清除齿轮与轴柄之件的粉末。
有了水溶性支撑,整个装配件的CAD资料可以当作一个工件处理。
同样地,也不需要手工劳动或是时间进行工件的装配。
图11脑型齿轮利用水溶性支撑以一体成型的方式建构而不用考虑手动移除支撑
运行时间
运行时间在FDM技术制程中明显地取决于不同的因素。
这样提供所有工件在所有的制作时间比较表是不可能的。
然而,一般来说,FDM技术的运行时间比起SLA技术与SLS技术是需要略久一些的时间,而跟PolyJet技术比较起来则相似。
表3表示运行时间的是针对于图1所作的精准性测试工件进行纪录。
所有工件采用0.25mm层厚所建构。
FDM系统
时数
Maxum
2.2
Titan
2.7
ProdigyPlus
4.2
表3表示运行时间
FDM技术的运行时间是由工件的材料容积以及支撑结构来定义。
不像SLA,SLS或是PolyJet,Z轴高度都不影响时间。
工件的材料总额与材料沉积率都是决定FDM技术运行时间的重要因素。
材料沉积率是喷嘴尺寸,线材宽度以及层厚的作用。
较小的层厚与喷嘴将会增进特征细节与表面完工精度,而建造时间会增加。
额外的考虑是FDM技术的运行时间不因材料不同而有变化。
而对于SLA技术与SLS技术,运行时间是取决于材料种类并且会有20%以上的变化。
为了减少运行时间,FDM系统提供了”稀疏填充”(轻量化技术)的选项。
这种选项类型会建立实体状的周围与骨架状的内部。
线材的间隔为3.8mm且在每一层会交替线材的方向,所以材料的总额与建构时间都会减少。
既然FDM技术的运行时间都不受Z轴高度影响,除了任何额外支撑材料之外,工件的成型方向可以为了最佳的品质而不造成时间损失。
在其它每一项技术之中,通常时间与品质两者不可兼得,当以Z轴为最低的成型方向时可以减少建构时间,但是特征的品质较差。
还有需要考虑的是FDM技术不需要显著的时间去暖机到运行温度或是去让完成的工件冷却。
在SLS或SLA技术制程中,系统每运行一次的预先暖机与输出冷却都需要增加2到4个小时。
并且在SLA技术制程中,制作出来的原形件需要用酒精或丙酮清洗掉表面的液体树脂,然后放到紫外光固化箱中进行二次固化。
在SLS技术制程中,制作出来的原形件需要“清粉”、浸蜡处理。
以上这些费时、费力的后处理过程FDM都不需要。
设备使用环境
快速成型设备最好能放置于电脑设计室内以便于工作,要求设备无烟尘、无震动和噪音并且材料安全无毒。
而光敏树脂(SLA)液态原材料有毒,需特别小心处理,并且需配置抽风系统,以抽除建模过程中产生之毒烟;而粉末材料(SLS)需配备抽风系统、吸尘设备、防尘箱及氮气发生系统;纸张(LOM)也需要配置抽风系统以抽除建模过程中产生之烟雾;只有美国Stratasys公司的FDM快速成型机只需要在一般办公室环境下操作。
应用范围
概念模型
许多FDM技术的使用者把该技术当作设计的周边。
就本身而言,为了在制程早期就能审核与确认设计概念,该技术已经变得另一种与CAD系统连结并驱动的工具。
由于这样的应用,FDM技术都是作为概念模型工具以清楚地传达日益精致与复杂的设计。
当FDM技术无法从概念模型中提供预期的速度,它提供了结合概念模型与视觉应用的优势。
这些强处包含精准性,材料属性,色彩以及免用手动工件后处理。
尽管材料强度与硬度并非概念模型的关键,但是它通常值得关注,因为脆弱的模型通常在最不适当的时机破裂。
FDM技术的模型也应用于销售与行销,包含内部与外部。
对内,FDM技术的原型是用来给销售团队,管理阶层以及其它员工在开始制造之前看一眼产品长相。
对外,原型是用来在产品作商品化之前引起预期客户的兴奋与兴趣。
塑型,装配以及功能性模型
对许多技术而言,快速原型的应用在塑型,装配以及功能性分析方面时需要作某些方面的牺牲。
尽管SLA技术与PolyJet技术提供较好的细节,精准度与表面加工精度,但是他们无法提供必要的强度与硬度。
同样地,SLS技术提供强度而牺牲精准性与细节。
对于FDM技术,使用ABS与polycarbonate材料,提供具有细节,精准性与可加工性的坚固原型,以进行注塑成型塑料工件的功能性分析。
尽管未经后处理的工件也许没有生产成品一般的表面精度,但是仍有许多不受此妨碍的应用。
再者,表面加工精度相对于其它因素例如尺寸稳定性,耐热性与抗化学性而言,通常是比较次要的。
图12FDM原型组装测试
修整样品
快速原型可以用来作为建立模具的样品。
不像其它快速原型技术,FDM技术可以成功地用来制作样品。
然而,必须考虑表面加工精度与工件后处理到可以作为母模所需时间。
脱蜡铸造是样品的额外用途,样品必须能在他们自己所建立陶砂壳模之中燃烧消耗掉。
FDM技术制程所建构的蜡模与ABS模都被证实适合应用在陶砂壳模之中燃烧消耗的标准铸造流程。
快速制造(少量多样)
快速原型激起对于短期制造的兴趣,对于少到只有一个单位的订单都很合算。
这样的应用需要工件在许多领域都符合功能性规格。
在FDM技术的精准性与材料属性都是可用之际,它是少数致力于该应用的技术之一。
当尚未经过最后加工修饰的FDM工件可能受限使用于可视化,装饰的应用,但不受妨碍它去作为内部组件,或是那些不需要艺术吸引力的用途。
对于快速制造的应用,运行时间将会成为一项重要的考虑。
然而,就像几位使用者的证明,为数不多的工件运行时间是明显地少于生产模具与成品所需要的总时间。
总结
获得快速原型技术的强处与弱势信息是做出睿智抉择的第一步。
尽管目前的信息十分完整,也不可能包含各种应用的需求。
所以下一步是评估应用的必要需求以及持续从其它来源处取得信息。
要记得,没有任何技术可以适合各种处境。
必须选择最合适的工具以满足手边的工作。