XXXX新版GMP颗粒自动包装机.docx
《XXXX新版GMP颗粒自动包装机.docx》由会员分享,可在线阅读,更多相关《XXXX新版GMP颗粒自动包装机.docx(55页珍藏版)》请在冰点文库上搜索。
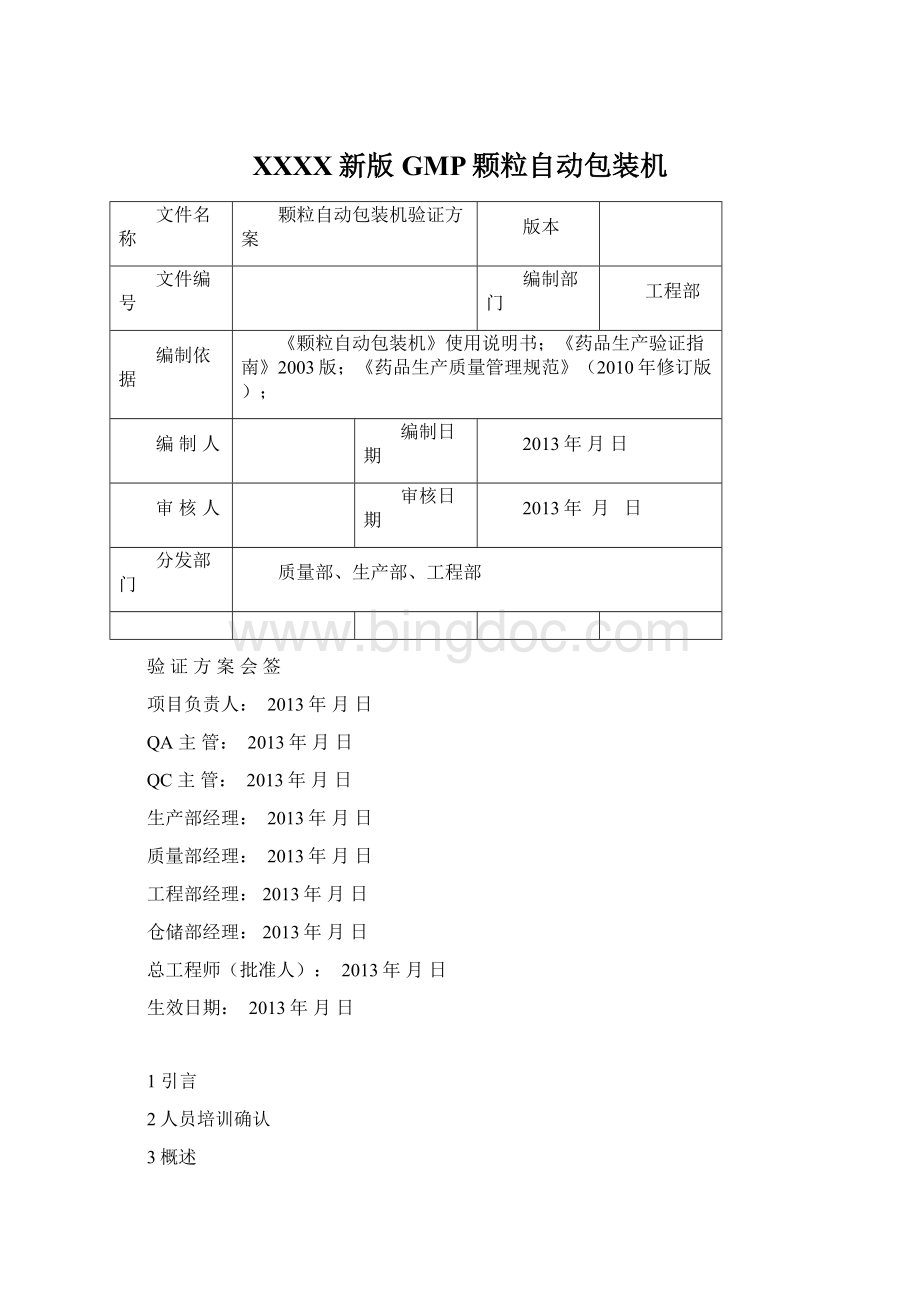
XXXX新版GMP颗粒自动包装机
文件名称
颗粒自动包装机验证方案
版本
文件编号
编制部门
工程部
编制依据
《颗粒自动包装机》使用说明书;《药品生产验证指南》2003版;《药品生产质量管理规范》(2010年修订版);
编制人
编制日期
2013年月日
审核人
审核日期
2013年月日
分发部门
质量部、生产部、工程部
验证方案会签
项目负责人:
2013年月日
QA主管:
2013年月日
QC主管:
2013年月日
生产部经理:
2013年月日
质量部经理:
2013年月日
工程部经理:
2013年月日
仓储部经理:
2013年月日
总工程师(批准人):
2013年月日
生效日期:
2013年月日
1引言
2人员培训确认
3概述
4验证的目的
5验证所需文件
6验证范围
7验证项目和时间安排
8风险评估
9设计确认
10供应商审计和评估
11安装确认IQ
12运行确认
13性能确认
14结果与评价
15验证周期
16设备使用阶段
17设备报废阶段
1引言
1.1验证小组:
姓名
所在部门
职务
验证分工
王立新
生产部
固体车间
组长
王元元
生产部
操作工
组员
赵丛丛
质量部
QA监控员
组员
冯月
质量部
QC检验员
组员
屠丽丽
工程部
工程部经理
组员
张华
工程部
维修工
组员
1.2验证小组职责
1.2.1负责验证方案的审批;
1.2.2负责验证的协调工作,以保证验证方案规定项目顺利实施;
1.2.3负责验证数据及结果的审核;
1.2.4负责验证报告的审批;
1.2.5负责发放验证证书;
1.2.6负责验证周期的确认;
1.2.7验证小组组长负责组织方案起草、方案实施全过程的组织和验证报告;
1.2.8验证小组组员分别负责方案实施验证部分具体工作。
1.3工程部
1.3.1负责颗粒自动包装机的调试,并做好相应记录;
1.3.2负责提供颗粒自动包装机的档案、资料交档案室;
1.3.3负责仪器仪表的校正;
1.3.4负责拟定验证周期;
1.3.5负责收集各项验证、试验记录,并对数据进行分析、评估,起草验证报告,报验证小组;
1.3.6确保验证设备的完好运行,为验证过程中提供有关的技术服务;
1.3.7负责颗粒自动包装机的维护保养。
1.3.8负责设备的统筹管理,包括设备的配置、验收、建档、检修和报废等。
1.4质量部
1.4.1负责对生产部提供的参数要求进行确认;
1.4.2各种检验的准备,取样及样品的测试工作;
1.4.3负责根据检验结果,出具检验报告单;
1.4.4负责组织验证方案、验证报告、验证结果的会审会签;
1.4.5负责对验证全过程实施监控。
负责验证的协调工作,以保证本验证方案规定项目的顺利实施;
1.4.6负责建立验证档案,及时将批准实施的验证资料收存归档;
1.4.7负责验证过程的取样、检验、测试及结果报告。
1.5生产部
1.5.1负责提供与颗粒自动包装机有关的主要参数;
1.5.2负责指定颗粒自动包装机的管理人员及操作人员;
1.5.3负责验证中各种试验材料的准备工作,并派人参加验证工作对机器的操作和清洁维护保养工作;
1.5.4组织实施验证方案,参加会签验证方案、验证报告,收集记录验证资料、数据。
1.6仓储部:
负责提供物料支持。
1.7人事部
1.7.1负责组织验证人员的相关培训。
1.7.2负责培训的考试及档案归档。
2人员培训确认
认可标准:
检查并确认本验证涉及人员是否经过培训,考试合格,且持有上岗证。
姓名
检查项目
培训课时
检查结果
颗粒自动包装机验证方案及各环节确认、与GMP相关理论知识培训,岗前操作技能的培训与验证相关知识的培训,相关考试合格。
一天
□合格□不合格
□合格□不合格
□合格□不合格
□合格□不合格
□合格□不合格
□合格□不合格
结论:
检查人:
复核人:
日期:
3概述
DXDK80C-H型颗粒自动包装机是我公司固体车间的关键设备,主要用于颗粒剂的袋分装,具有装量稳定、热封效果好、产品包装外观平整、无毛边等优点。
该机器采用CPU集中控制机器的各功能状态,设有人机对话界面;智能型温控仪双路控制横、纵封体温度;在额定范围内无级调整包装速度。
定位张口停机;智能光电定位,亮动、暗动任意转换,抗干扰强,连续三袋光标异常即停机报警;采用容积法计量,制袋精度高,操作维护方便。
设备名称:
颗粒自动包装机设备型号:
DXDK80C-H型
设备编号:
出厂日期:
2009年11月
生产厂家:
北京大松惠基包装机械有限公司使用部门:
固体制剂车间
主要技术参数
项目
参数
包装速度
55-80袋/分
计量范围
10-50ml
制袋尺寸
长50-120mm宽60-85mm
电源电压
三相四线制380V/50Hz
功率
0.86kw
外型尺寸
730mm×630mm×1580mm(长×宽×高)
重量
180kg
4验证的目的
对颗粒自动包装机进行设计、安装、运行、性能的验证,以证实符合用户需求标准(URS)的要求,符合药品生产对设备的要求。
确认在规定的SOP操作,设备能稳定运行且各项指标均能达到设计要求,以证明该设备不仅能满足生产需要,而且符合工艺标准要求
5验证所需文件
资料名称
文件编号
文件生效日期
存放处
颗粒自动包装机说明书
---------
---------
档案室
产品合格证
---------
---------
档案室
颗粒自动包装机标准操作规程
档案室
颗粒自动包装机维护保养操作规程
档案室
颗粒自动包装机清洁标准操作规程
档案室
结论:
文件真实、完整,为现行标准,已经过批准
检查人:
复核人:
日期:
6验证范围
本验证方案适用于DXDK80C-H型颗粒自动包装机的验证。
7验证项目和时间安排
计划于2013年-月进行颗粒自动包装机设备验证,内容严格按照本验证方案,检查颗粒自动包装机其设计确认、安装确认、运行确认、性能确认达到规定的标准要求。
验证时间:
设计确认:
从2013年月日至2013年月日
安装确认:
从2013年月日至2013年月日
运行确认:
从2013年月日至2013年月日
性能确认:
从2013年月日至2013年月日
起草报告:
从2013年月日至2013年月日
8风险评估
8.1目的:
降低和控制槽形混合机验证过程中潜在质量风险,保证最终产品质量。
8.2风险因素标准的评定
8.2.1风险评估方法:
遵循FMEA技术(失效模式效果分析)。
8.2.2失败模式效果分析(FMEA)由三个因素组成:
风险的严重性(S)、风险发生的可能性(P)、风险的可测性(D)。
8.3.2.2.1严重性(S):
主要针对可能危害产品质量数据完整性的影响。
严重程度分为四个等级:
严重性(S)
风险系数
风险可能导致的结果
关键
4
直接影响产品质量要素或工艺与质量数据的可靠性、完整性或可跟踪性。
此风险可导致产品不能使用;直接影响GMP原则,危害产品生产活动。
高
3
直接影响产品质量要素或工艺与质量数据的可靠性、完整性或可跟踪性。
此风险可导致产品召回或退回;不符合GMP原则,可能引起检查或审计中产生偏差
中
2
尽管不存在对产品或数据的相关影响,但仍间接影响产品质量要素或工艺与质量数据的可靠性、完整性或可跟踪性;此风险可能造成资源的浪费。
低
1
尽管此类风险不对产品或数据产生最终影响,但对产品质量要素或工艺与质量数据的可靠性、完整性或可跟踪性仍产生较小影响
8.2.2.2可能性(P):
测定风险产生的可能性,为建立统一基线,建立以下等级:
可能性(P)
风险系数
风险可能导致的结果
极高
4
极易发生
高
3
偶尔发生
中
2
很少发生
低
1
发生可能性极低
8.2.3可测性(D):
在潜在风险造成危害前,检测发现的可能性,定义如下:
可测性(D)
风险系数
风险可能导致的结果
极低
4
不存在能够检测到错误的机制
低
3
通过周期性控制可检测到错误
中
2
通过应用于每批的常规手动控制或分析可检测到错误
高
1
自动控制装置到位,检测错误(例:
警报)或错误明显(例:
错误导致不能继续进入下一阶段工艺)
8.3风险级别评判标准
8.3.1风险优先系数(RPN)计算公式
RPN=SPD=严重性(S)×可能性(P)×可测性(D)
8.3.2风险评价标准
风险优先系数
RPN
风险水平
描述
RPN>16或
严重程度=4
高风险水平
此为不可接受风险。
必须尽快采用控制措施,通过提高可检测性及降低风险产生的可能性来降低最终风险水平。
验证应先集中于确认已采用控制措施且持续执行。
由严重程度为4导致的高风险水平,必须将其降低至RPN最大等于8。
8≤RPN≤16
中等风险水平
此风险要求采用控制措施,通过提高可检测性及(或)降低风险产生的可能性来降低最终风险水平。
所采用的措施可以是规程或技术措施,但均应经过验证。
RPN≤7
低风险水平
此风险水平为可接受,无需采用额外的控制措施。
风险评估与控制表
序号
项目
风险发生的失败模式
风险可能导致的后果
严重程度S
发生概率p
可预知性D
RPN
值
预采取的控制措施
1
设计确认
设备不符合设计和生产使用要求,不符合GMP要求。
设备不能正常使用
4
2
1
8
按照设备用户需求(URS)进行管理
2
安装确认
设备送货到场后,设备型号不符合,设备损坏,设备及其配件、文件资料不齐。
设备不能正常安装使用,设备资料不齐影响设备的日常使用及培训管理。
4
2
1
8
应进行设备开箱验收的确认,确认设备到货部件的名称、型号、数量,是否有损坏及腐蚀,设备配件及文件资料是否齐全。
与药品直接接触的设备材质不符合GMP要求。
影响产品质量。
4
2
1
8
进行设备开箱验收的确认,取得供应商的材质证明。
设备安装环境不符合要求。
缩短设备使用寿命。
污染产品。
4
2
1
8
进行安装确认,确认设备安装环境的洁净室等级、温湿度、光线等。
安装定位不合适。
影响日常使用和设备的维修。
2
2
1
4
由实际操作员模拟操作,留有足够的安全操作距离及维修空间。
电力供应无接地。
漏电,造成人员伤害。
1
2
1
2
有电工在场,进行电力供应有效接地的确认。
电力、压缩空气、水系统等配套设施的连接安装不良;供应的电力、压缩空气压力、水系统等与设备铭牌不符。
设备不能正常使用。
3
2
1
6
检查电力安装符合电路图。
检查压缩空气、水系统连接正确。
检测电力、压缩空气、水系统的供应符合设备铭牌的要求。
序号
项目
风险发生的失败模式
风险可能导致的后果
严重程度S
发生概率p
可预知性D
RPN
值
预采取的控制措施
2
安装确认
转动设备的主动和被动链轮之间的链条过松或过紧。
设备运行不畅,易打滑、松脱。
2
2
2
8
制定管理规程,要求对设备进行定期检查、维护。
各电器元件、接线松动脱落,各零部件安装紧固不良。
设备不能正常安装使用,设备易出现故障。
2
1
2
4
制定管理规程,要求对设备定期进行进行电器元件、接线及零部件紧固度的安装确认。
设备与地面间的缝隙不密封或不利于清洁操作。
易积尘,滋生微生物。
2
2
1
4
设备安装固定后,检查设备与地面的密封性或规定清洁所需高度。
无紧急停机按钮,或位置不便于应急操作
无法应急操作,影响产品质量,对产品造成损失
2
1
1
2
需确认设备有紧急停机按钮,并方便应急操作
电控开关控制功能不符合要求。
设备无法正常操作,易发生安全事故。
2
1
2
4
设备安装确认。
检查主电源开关、运行开关情况。
使用的润滑剂不符合要求、设备不润滑。
影响产品质量、影响设备使用寿命。
3
1
2
6
检查润滑剂的规格是否符合要求;开机前检查设备的润滑情况和润滑记录。
设备未进行初始清洁、消毒。
设备的初始清洁、消毒不彻底。
污染环境。
2
2
2
8
进行设备的初始清洁、消毒确认。
检查清洁效果及清洁、消毒记录。
序号
项目
风险发生的失败模式
风险可能导致的后果
严重程度S
发生概率p
可预知性D
RPN
值
预采取的控制措施
3
运行确认
设备未定期维护保养。
设备维护保养不全面。
缩短设备使用寿命;影响正常生产。
3
2
2
12
制定设备维护保养SOP,对相关人员进行培训并检查培训记录。
触控面板功能失效。
各种参数不能调整,设备不能正常运转,产品质量无法保证。
3
1
3
9
试运转时检查触控面板能否正常运行,能否有效控制设备。
进瓶缓冲转盘与翻转轨道及拨轮间不能顺利通过样瓶,其过渡不通畅。
设备不能正常投入使用。
3
1
2
6
确认重新进行设备安装调试并无障碍。
出瓶轨道至烘箱通道不通畅。
设备不能正常投入使用。
4
1
1
4
确认重新进行设备安装调试并无障碍。
出瓶处至烘箱通道百级层流不符合要求。
污染产品。
4
1
1
4
确认有相应的认证报告并处于合格状态。
未能将水排尽
积水引起微生物滋生。
4
1
2
8
确认重新进行设备安装调试并无障碍。
脏水回流至洗瓶机
造成污染
4
1
1
4
确认重新进行设备安装调试并无障碍。
序号
项目
风险发生的失败模式
风险可能导致的后果
严重程度S
发生概率p
可预知性D
RPN
值
预采取的控制措施
3
运行确认
玻璃瓶位置错误。
玻璃瓶不洁净
4
2
2
16
使用控制系统调整设备
设备运转不平稳;有漏油现象;有异常噪音。
设备不能正常投入使用。
3
1
2
6
进行设备空机运转稳定性的确认。
设备进行大修
验证状态发生偏移,影响产品质量
3
2
3
18
重新进行设备验证
4
仪表、衡器
仪器仪表、衡器规格不符合生产使用要求,未校验或不在校验期内。
影响设备运行参数的检查,不能正常判断是否操作正常。
3
2
2
12
检查所有的仪器仪表、衡器的规格是否符合生产使用要求,是否有校验标志且在校验期内。
5
文件与人员培训
无操作指导文件;操作人员未经有效培训。
设备操作失当,出现操作事故。
2
2
2
8
由熟悉设备的人员制订设备操作文件;并进行有效培训。
序号
项目
风险发生的失败模式
风险可能导致的后果
严重程度S
发生概率p
可预知性D
RPN
值
措施确认
采取控制措施后风险等级评估
是否引入新的风险
严重程度S
发生概率P
可预知性D
RPN值
1
设计确认
设备不符合设计和生产使用要求,不符合GMP要求。
设备不能正常使用
4
2
1
8
按照设备用户需求(URS)进行管理
3
1
1
3
否
2
安装确认
设备送货到场后,设备型号不符合,设备损坏,设备及其配件、文件资料不齐。
设备不能正常安装使用,设备资料不齐影响设备的日常使用及培训管理。
4
2
1
8
已建立设备开箱验收管理规程。
3
1
1
3
否
与药品直接接触的设备材质不符合GMP要求。
影响产品质量。
4
2
1
4
进行设备开箱验收的确认,取得供应商的材质证明。
3
2
1
6
否
设备安装环境不符合要求。
缩短设备使用寿命。
污染产品。
4
2
1
4
进行安装确认,确认设备安装环境的洁净室等级、温湿度、光线等。
3
1
1
3
否
安装定位不合适。
影响日常使用和设备的维修。
2
2
1
4
由实际操作员模拟操作,留有足够的安全操作距离及维修空间。
2
1
1
2
否
电力供应无接地。
漏电,造成人员伤害。
1
2
1
2
有电工在场,进行电力供应有效接地的确认。
2
1
1
2
否
电力、压缩空气、水系统等配套设施的连接安装不良;供应的电力、压缩空气压力、水系统等与设备铭牌不符。
设备不能正常使用。
3
2
1
6
检查电力安装符合电路图。
检查压缩空气、水系统连接正确。
检测电力、压缩空气、水系统的供应符合设备铭牌的要求。
3
1
1
3
否
采取控制措施后风险再评估表
序号
项目
风险发生的失败模式
风险可能导致的后果
严重程度S
发生概率p
可预知性D
RPN
值
措施确认
采取控制措施后风险等级评估
是否引入新的风险
严重程度S
发生概率P
可预知性D
RPN值
2
安装确认
转动设备的主动和被动链轮之间的链条过松或过紧。
设备运行不畅,易打滑、松脱。
2
2
2
8
已制定管理规程,要求对设备进行定期检查、维护。
2
2
1
4
否
各电器元件、接线松动脱落,各零部件安装紧固不良。
设备不能正常安装使用,设备易出现故障。
2
1
2
4
已制定管理规程,要求对设备定期进行进行电器元件、接线及零部件紧固度的安装确认。
2
2
1
4
否
设备与地面间的缝隙不密封或不利于清洁操作。
易积尘,滋生微生物。
2
2
1
4
设备安装固定后,检查设备与地面的密封性或规定清洁所需高度。
2
1
1
2
否
无紧急停机按钮,或位置不便于应急操作
无法应急操作,影响产品质量,对产品造成损失
2
1
1
2
需确认设备有紧急停机按钮,并方便应急操作
2
1
1
2
否
电控开关控制功能不符合要求。
设备无法正常操作,易发生安全事故。
2
1
2
4
设备安装确认。
检查主电源开关、运行开关情况。
2
1
1
2
否
使用的润滑剂不符合要求、设备不润滑。
影响产品质量、影响设备使用寿命。
3
1
2
6
检查润滑剂的规格是否符合要求;开机前检查设备的润滑情况和润滑记录。
3
1
2
6
否
设备未进行初始清洁、消毒。
设备的初始清洁、消毒不彻底。
污染环境。
2
2
2
8
进行设备的初始清洁、消毒确认。
检查清洁效果及清洁、消毒记录。
2
1
2
4
否
序号
项目
风险发生的失败模式
风险可能导致的后果
严重程度S
发生概率p
可预知性D
RPN
值
措施确认
采取控制措施后风险等级评估
是否引入新的风险
严重程度S
发生概率P
可预知性D
RPN值
3
运行确认
设备未定期维护保养。
设备维护保养不全面。
缩短设备使用寿命;影响正常生产。
3
2
2
12
制定设备维护保养SOP,对相关人员进行培训并检查培训记录。
3
1
2
6
否
触控面板功能失效。
各种参数不能调整,设备不能正常运转,产品质量无法保证。
3
1
3
9
试运转时检查触控面板能否正常运行,能否有效控制设备。
3
1
2
6
否
进瓶缓冲转盘与翻转轨道及拨轮间不能顺利通过样瓶,其过渡不通畅。
设备不能正常投入使用。
3
1
2
6
确认重新进行设备安装调试并无障碍。
3
1
1
3
否
出瓶轨道至烘箱通道不通畅。
设备不能正常投入使用。
4
1
1
4
确认重新进行设备安装调试并无障碍。
3
1
1
3
否
出瓶处至烘箱通道百级层流不符合要求。
污染产品。
4
1
1
4
确认有相应的认证报告并处于合格状态。
3
1
1
3
否
未能将水排尽
积水引起微生物滋生。
4
1
2
8
确认重新进行设备安装调试并无障碍。
3
1
1
3
否
脏水回流至洗瓶机
造成污染
4
1
1
4
确认重新进行设备安装调试并无障碍。
3
1
1
3
否
序号
项目
风险发生的失败模式
风险可能导致的后果
严重程度S
发生概率p
可预知性D
RPN
值
措施确认
采取控制措施后风险等级评估
是否引入新的风险
严重程度S
发生概率P
可预知性D
RPN值
3
运行确认
玻璃瓶位置错误。
玻璃瓶不洁净
4
2
2
16
使用控制系统调整设备
3
1
1
3
否
设备运转不平稳;有漏油现象;有异常噪音。
设备不能正常投入使用。
3
1
2
6
进行设备空机运转稳定性的确认。
3
1
2
6
否
设备进行大修
验证状态发生偏移,影响产品质量
3
2
3
18
重新进行设备验证
3
2
1
6
否
4
仪表、衡器
仪器仪表、衡器规格不符合生产使用要求,未校验或不在校验期内。
影响设备运行参数的检查,不能正常判断是否操作正常。
3
2
2
12
检查所有的仪器仪表、衡器的规格是否符合生产使用要求,是否有校验标志且在校验期内。
3
1
1
3
否
5
文件与人员培训
无操作指导文件;操作人员未经有效培训。
设备操作失当,出现操作事故。
2
2
2
8
由熟悉设备的人员制订设备操作文件;并进行有效培训。
2
1
2
4
否
9设计确认DQ
9.1目的:
提供书面文件证明拟购置的颗粒自动包装机,适用于其预定用途和GMP要求,并能符合本公司生产质量要求。
本设计确认是为了确认颗粒自动包装机是按照买方需求设计,并符合设备和系统设计标准,同时设计确认也将提供一些有用的信息和必要的建议,以便颗粒自动包装机的制造、安装和调试可以有效规避风险的工作。
9.2URS符合性评估
由工程设备部人员将设备的文件及图纸与公司提出的URS进行比较,确认系统/设备已符合用户需求规范。
URS符合性评估表
No.
要求(URS)
必需/期望
符合
是
否
1.
文件资料应包括产品合格证、装箱单、设备使用说明书、变频器说明书、零件图册、设备操作规程、设备维护检修规程、设备清洗规程、设备确认文件、与机器一致的电器原理图、接线图、方框图。
必需
2.
设备供应商应免费提供现场安装调试
必需
3.
设备材质和结构、泵、阀门、垫圈、死角、焊接、喷