质量控制检验规范.docx
《质量控制检验规范.docx》由会员分享,可在线阅读,更多相关《质量控制检验规范.docx(16页珍藏版)》请在冰点文库上搜索。
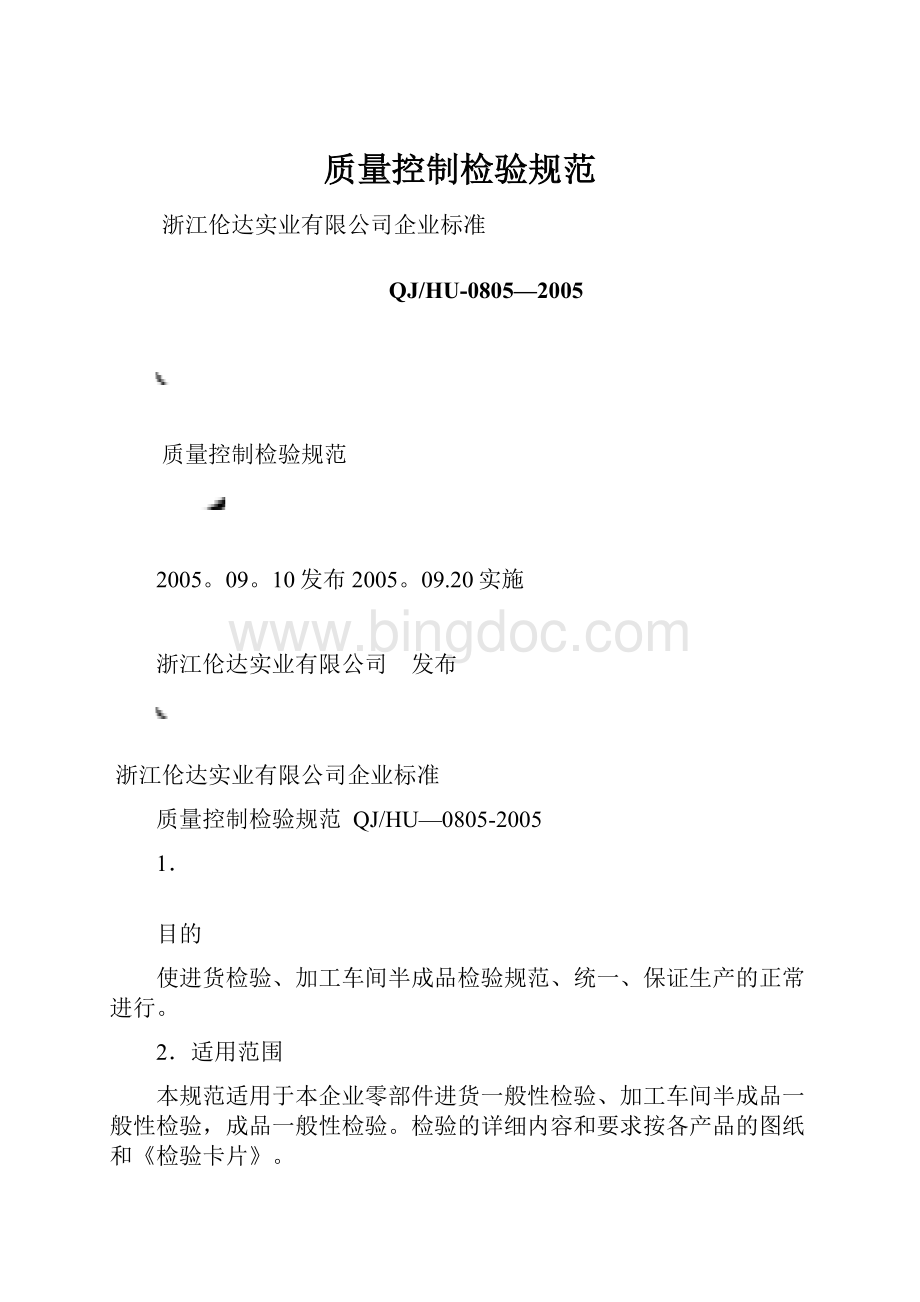
质量控制检验规范
浙江伦达实业有限公司企业标准
QJ/HU-0805—2005
质量控制检验规范
2005。
09。
10发布2005。
09.20实施
浙江伦达实业有限公司 发布
浙江伦达实业有限公司企业标准
质量控制检验规范QJ/HU—0805-2005
1.
目的
使进货检验、加工车间半成品检验规范、统一、保证生产的正常进行。
2.适用范围
本规范适用于本企业零部件进货一般性检验、加工车间半成品一般性检验,成品一般性检验。
检验的详细内容和要求按各产品的图纸和《检验卡片》。
3.零部件进货一般性检验的内容、要求及抽样标准
检验部门:
外协检验(如不合格退货,再次送检应加严)
3。
1压铸件毛坯(如头壳、前盖、一般传动箱)
3。
1。
1压铸件填充饱满,外表光洁,无飞边毛刺及缺口,无气孔,无裂纹,无夹渣。
按IL=I,AQL=2。
5检验。
3.1。
2机加工部位留加工余量适度,一般为0。
5~0。
7mm.每批抽查2~3套。
3.1.3外形尺寸符合图纸要求。
每批抽查1~2套。
3。
1.4与封样件对照一致。
3.2塑料注塑件、压注件(如塑料机壳、后罩、侧手柄、风叶)
3.2。
1色泽均匀一致,外壳同色件之间无明显色差,无明显飞边毛刺,无流纹和银丝,填充饱满,无气孔,无裂纹,无收缩引起凹凸不平。
按IL=I,AQL=2.5检验.
3。
2.2材质符合要求(听掉落发出声音),强度符合要求,尼龙料零件要煮过.
3.2.3外形尺寸、配合部位尺寸符合要求。
每批抽查2~3套.
3。
2.4检验机过的形位误差(重点查看定、转子有无擦铁现象),其余零件相互间的配合情况。
每批抽查2~3套。
3.2。
5有特殊要求检验的按照特殊要求规定进行检验(如对色卡,相互间色差等)。
3。
2.6由注塑件、压注件厂家提供一份注塑件、压注件性能检测报告,样品封样。
3.2.7与封样件对照一致。
3。
3机加工零件(如输出轴、电机轴、压板等)
3。
3.1检验配合尺寸,配合面表面质量:
重要外圆、内孔尺寸(如轴颈尺寸、表面粗糙度)等尺寸。
必要时可以把相关配合件装配后目测.按IL=I,AQL=2.5检验。
3。
3.2检验重要的长度尺寸(如两颈之间的距离).按IL=I,AQL=2。
5检验。
3.3.3检验必要的形位公差,如跳动、对称度等。
按IL=I,AQL=2。
5检验.
QJ/HU-0805-2005
浙江伦达实业有限公司2005-09-10批准 2005-09-20实施
质量控制检验规范QJ/HU-0805—2005
3。
3.4检验表面处理情况及打硬度(如发黑、发兰)。
按IL=I,AQL=2。
5检验。
3。
4冲压件(如轴承压板、定子冲片、转子冲片、金属风叶)
3。
4。
1冲压外形完整,无明显翘曲,冲压毛刺符合要求,表面无明显锈蚀。
按IL=I,AQL=2.5检验。
3.4.2外形尺寸符合要求,形位公差符合要求,材料正确,每批抽查3~6件。
3.4.3如定子铁芯、电枢铁芯由冲压件冲片组成的,材料正确,不得有残片、缺角等。
定子铁芯垂直度,铆接牢固度。
按IL=I,AQL=2。
5检验。
3。
4。
4冲片的含硅量应通过外部机构进行不定期的检测。
3.4.5与封样件对照一致。
3.5齿轮
3.5.1齿轮表面不允许有裂纹、剥落及伤痕等缺陷.按IL=I,AQL=4.0检验.
3.5。
2齿形不允许在明显的大、小齿,齿形一致,齿部不得有崩齿、影响齿声的毛刺。
按IL=I,AQL=4.0检验.
3。
5.3检验齿轮尺寸:
a)圆柱齿轮:
齿顶圆直径、内孔尺寸、齿轮宽度、公法线长度、齿圈(顶)跳动、键槽宽度、键槽深度、齿轮卡位长度。
按照IL=I,AQL=4。
0.(必要时抽装机5付检测齿音)。
b)弧齿锥齿轮:
齿顶圆直径、内孔尺寸、齿轮宽度、键槽宽度、键槽深度、齿轮卡位长度。
按照IL=I,AQL=4.0.(必要时装配2~3套查看其啮合接触斑点).
3。
5。
4齿轮表面质量:
粗糙度、齿面硬度。
每批抽检3~4只.
3。
5。
5带有冲击齿的齿轮,应检验冲击齿的外径、深度、冲击齿表面的硬度。
每批抽
检3~4只。
3.6粉末冶金件(如冲击块、含油轴承、压板、连接套)
3.6.1粉末冶金件不得有裂纹、伤痕等缺陷.按IL=I,AQL=4.0检验.
3.6。
2检验重要尺寸:
装配中心距、轴承室内孔、外形配合尺寸.每批抽检5~6只。
3。
6。
3检验配件硬度,每批抽检5~6只。
3。
6.4粉末冶金件存在冲击齿部分的,检验冲击齿外径、深度、硬度等。
每批抽检3~4只。
3。
6。
5与封样件对照一致。
3.7表面处理(如镀锌、镀铬、静电喷漆)
QJ/HU-0805-2005
质量控制检验规范QJ/HU-0805—2005
3。
7。
1镀层均匀,颜色正确,无明显漏镀,镀层面用2H铅笔不能划出痕迹。
IL=I,
AQL=4.0检验。
3。
7.2喷漆色泽均匀,外表平整光滑,漆层厚薄均匀、坚固,不容易剥落。
不应喷的位置不得有涂层,喷漆面用2H铅笔不能划出痕迹,全检。
3。
8弹簧
3。
8.1弹簧圈数、内径、外径、弹簧钢丝直径、自由高度。
每批抽检5~6只。
3。
8。
2按图纸检验弹簧压力。
每批抽检3~4只。
3.9开关
3。
9.1验外观质量:
与机壳配合良好。
每批抽检3~4只。
3。
9。
2应标有制造厂名(英文)或商标,型号标志,额定电压范围,额定频率或频率范围,额定负载电流等标志;标志应清晰耐久并符合有关国家标准。
(用一块浸透蒸馏水的脱脂棉在约15s擦拭15个来回,随后用一块浸透汽油的脱脂棉在15s内擦拭15个来回,所用压力约为2N之后仍清晰。
)每批抽检1~2只。
3.9.3检验通断情况。
按IL=I,AQL=2。
5检验。
3。
9。
4开关动作灵活无卡滞。
按IL=I,AQL=2.5检验。
3.9。
5软起动元件:
a)应标有制造厂名(英文)或商标,型号标志,额定电压或电压范围,额定频率或频率范围,额定负载电流,引出线英文名,连线图等标志.
b)按照图纸检验外形尺寸,测量装配中心距。
装机壳实际检测灵活性,每批检测3~5只。
c)检验软起动性能,应能缓慢而稳定起动。
按IL=I,AQL=2.5检验。
3。
9.6与封样件对照一致。
3.9.7同开关供方提供该型号开关的使用寿命检测报告一份,样品封样.
3.10电磁线
3。
10.1检验规格、漆膜厚度、漆膜强度,漆膜表面应光滑,无漆瘤、无气孔、无针孔等现象。
每批抽检2~3米。
3.10.2绝缘强度检验,按照特定要求检验。
3。
11电缆线及插头
3.11.1检验外观:
电缆线及插头形状完整,无气泡、无磨损;电缆橡皮护套绝缘厚度均匀,外表光洁,无气泡、无裂纹,电缆线的绝缘层应紧密挤包在导体上,且应容易剥离而不损伤绝缘体、导体和镀锡层。
按IL=I,AQL=2。
5检验。
QJ/HU-0805-2005
质量控制检验规范QJ/HU-0805-2005
3.11.2检验标志及长度:
应标有英文制造厂名或商标,型号标志,额定电压或电压范围;要求印字清晰完整,不错印、漏印,有关内容及长度符合任务单要求。
每批抽检5~6根。
3.11。
3检验结构尺寸:
每批抽检2~3根
芯数X标称截面导电线芯根数/单线标绝缘标称厚度护套标称厚度
称直径(mm)(橡皮绝缘/聚氯乙烯)(橡皮绝缘/聚氯乙烯)
2X0.7542/0。
15(24/0.20)0.6/0。
60.8/0。
8
2X156/0.15(32/0.20)0.6/0.60.9/0.8
2X1.584/0。
15(30/0.25)0。
8/0。
71。
0/1.0
3X0。
7542/0。
15(24/0。
20)0。
6/0。
60.9/0。
8
3X156/0.15(32/0.20)0.6/0。
60。
9/0。
8
3X1。
584/0。
15(30/0。
25)0.8/0。
61.0/0。
9
3。
11.4耐高压电缆线及插头体应能承受50HZ正弦波电压3750V历时1min不击穿,两铜脚间应承受正弦波1500V历时1min不击穿或闪络。
按IL=I,AQL=0检验。
3.11。
5插脚之间尺寸按图纸检验。
每批抽检2~3根。
3.11.6由供方提供每种型号电缆线的电缆线抽检测报告,样品封样.
3。
12换向器
3。
12。
1检验内、外圆尺寸,长度尺寸、片数、下线槽宽度。
每批抽检3~4个。
3。
12.2解剖一个,检验铜片形状,绝缘层厚度.
3.12.3检验换向片间耐压,对轴芯耐压。
按IL=I,AQL=0检验.
3.13包轴
3。
13.1检验外圆尺寸,长度尺寸。
每批抽检5~6支.
3。
13。
2检验铁芯档、换向器档对二中心孔的跳动量.按IL=I,AQL=2。
5检验。
3。
13.3检验耐压:
全检。
3。
13.4由包轴供方提供包轴材料的性能检测报告一份,样品封样。
3。
14一次成型铁芯
3。
14。
1检验外圆尺寸,长度尺寸。
每批抽检5~6支。
3.14。
2铁芯档、换向器档、齿轮档对二中心孔的跳动量。
按IL=I,AQL=2。
5检验.
3。
14.3铁芯对轴的耐压.按IL=I,AQL=0检验。
3。
15电缆护套、轴承衬套等橡胶件
3.15。
1外圆尺寸,内孔尺寸,长度尺寸。
每批抽检10个。
必要时可以按试装要求进行.
QJ/HU-0805-2005
质量控制检验规范QJ/HU-0805-2005
3。
15。
2轴承衬套的同轴度。
每批抽检10个。
3.15。
3检验材料及其机械强度。
每批抽检3~4个。
3.16电刷
3.16.1检验碳刷的牌号、尺寸、弹力及电阻。
按IL=I,AQL=4。
0检验。
3。
16。
2碳刷装在刷握里灵活无卡滞。
按IL=I,AQL=2。
5检验。
3.16.3装机检测火花、温升及磨损度,按批次抽检3~4付。
3。
16。
4由供方提供碳刷材料性能检测报告一份,样品封样。
3。
17内接线
3。
17.1应标明制造厂家名称,电线型号及截面,额定电压,制造日期,标准号(JB1138-76)。
按IL=I,AQL=4.0检验。
3。
17.2线外表要求均匀平滑、无气泡、针孔、折皱及疵点.每批抽检2~3米.
3.17.3规格尺寸:
每批抽检1~2卷。
芯线结构(根数/线径)横截面外径电线最大外径绝缘厚度20℃下的直流电阻Ω/km
28/0。
150。
52(mm)2。
20.536.4
42/0.150.7522。
90.724。
3
32/0.21。
023.10.717。
8
48/0.21.523.40.711。
9
3。
17.4耐高压:
1500V不击穿(浸入室温水6h后进行试验,试验周期为1min)。
按特殊要求进行检验.
3。
18电容
3.18.1检验电容量:
按照铭牌±5%测量.按IL=I,AQL=4.0进行检验。
3。
18.2耐电压:
按铭牌上耐电压数值检测。
按IL=I,AQL=4。
0进行检验。
3.18。
3检验外形尺寸.每批抽检3~4只。
3.19电感
3.19。
1按规定检验电感量。
按IL=I,AQL=4.0检验。
3。
19.2检验丁晴线规格,绕制匝数。
按IL=I,AQL=4。
0检验.
3.19。
3检验磁环尺寸,电感外形尺寸。
每批抽检3~4只。
3.20青壳纸
3。
20.1产品表面应均匀平滑,无气泡,针孔,折皱及疵点,不分层。
在实际做的过程中进行检验。
QJ/HU—0805—2005
质量控制检验规范QJ/HU—0805-2005
3.20.2检验厚度。
每卷检验1处。
3.20.3击穿电压:
1500V/3S。
按IL=I,AQL=4.0检验。
3。
21自锁销
3.21。
1检验重要的长度尺寸、外圆尺寸。
按IL=I,AQL=2.5检验。
3。
21.2检验外形尺寸,外形与头壳自锁销孔相配合时间隙均匀,安装时不能有卡滞现象,间隙不能超过0。
3mm.每批抽检6~8只.
3。
21.3抽检自锁销塑料钮的强度,自锁销塑料钮应不易被夹碎、撞击中不被打碎。
每批抽检6~8只。
3。
22刷握
3。
22。
1检验重要长度尺寸、外圆尺寸、配合尺寸。
按IL=I,AQL=2.5检验.
3.22。
2检验重要的形位误差(对称度、同轴度).
3.22.3检验外形配合尺寸,与机壳配合松紧恰当,必要时装到机壳里检查。
每批抽检3~4副。
3.23连杆活塞
3。
23。
1要求有外协厂材料及强度检测报告,按批次抽检。
3.23。
2按图纸及检验卡片检验尺寸及形位公差.
4.加工车间半成品一般性检验,检验内容、要求及抽样标准
检验部门:
车间检验(一次不合格,二次加严,再不合格全检)
4.1压铸件加工(头壳、前盖、一般传动箱)
4。
1。
1压铸件金加工按照图纸进行加工。
4。
1。
2首检:
a)检验相交线公差,轴承室尺寸,配合面尺寸、装配距尺寸(中心距等),对比相关表面粗糙度。
b)检验装配外形(如头壳与前盖,头壳与机壳),错位量不大于0。
5.
c)检验自锁销孔尺寸,自锁销孔外形尺寸与自锁钮外形配合间隙为0.2mm。
4。
1.3巡检:
a)检验相交线公差,装配距尺寸(中心距等),每4小时巡检1次:
轴承室尺寸,配合面尺寸,相关粗糙度,每3小时巡检1次。
b)检验装配外形及错位置。
巡检频率一次。
c)检验自锁销孔配合。
巡检频率一次。
4.1。
4完工检验:
批量加工完之后,应进行完工抽检,检验轴承室尺寸,配合尺寸.按照IL=2,AQL=2。
5进行检验。
(如批量分几天完成,可以每天抽检累加)。
QJ/HU—0805-2005
质量控制检验规范QJ/HU-0805—2005
4。
2电枢加工
4。
2.1首检,巡检:
a)检验电枢外圆尺寸,装配距长度,轴承档外径,换向器装配尺寸,换向器开槽质量等.
b)检验铁芯档、轴承档、换向器档对两中心孔的跳动公差.
c)压风叶尺寸,且风叶不能有明显的不垂直现象,电枢表面不得残留铁芯加工后的毛刺.
d)动平衡不得有对打,不得有打穿铁芯表面,不得打在绝缘片上.按照动平衡工艺操作规程进行。
e)首检合格之后才能进行后续加工。
加工时应进行巡回检验,巡验频率不少于每班三次。
4.2.2完工检验:
批量加工完之后,应进行完工抽检,检验各个重要尺寸、跳动公差。
按照IL=2,AQL=2.5进行检验。
(如批量分几天完成,可以每天抽检累加)。
4。
3定子
4。
3.1检验定子线圈参数(漆包线直径、绕线匝数),铁芯规格、尺寸、垂直度,绝缘端片厚度,青壳纸长度。
在每批量做之前抽检3~4套。
4.3.2检验定子整形尺寸,引出线线头是否正确,线包到铁芯的爬电距离≥2。
2。
按照IL=I,AQL=0检验。
4。
3。
3浸漆前检验耐压:
1500V,3s不击穿。
全检。
4.3。
4在加工之间应进行自检,巡检,巡检频率不少于每班四次.
4。
3。
5完工检验:
批量加工完之后,应进行完工抽检,检验各个重要尺寸。
按照IL=2,AQL=2。
5进行检验。
(如批量分几天完成,可以每天抽检累加)。
4。
3.6浸漆检验按浸漆工艺守则进行,并检查定子线包尺寸。
按照IL=2,AQL=2。
5检验。
4。
4电枢
4。
4。
1检验绕组参数(漆包线直径、绕线匝数)铁芯规格、尺寸、铁芯跳动量,槽楔长度、厚度。
在每批量做之前抽检3~4套。
4。
4.2检验接线偏槽是否正确,绕线是否正确,线包上不能有单独的松的漆包线,检验青壳纸度按照IL=I,AQL=2.5检验。
4.4.3检验点焊的形状、大小、深度及漆包线的烧焦情况,按照点焊工艺规程进行.
4。
4。
4电枢检验:
利用电枢检验仪进行检验,不得有虚焊、短路、断路。
全检.
4.4。
5耐压检验:
基本绝缘1500V/3S不击穿,全检。
QJ/HU-0805—2005
质量控制检验规范QJ/HU—0805-2005
4。
4。
6滴漆检验按照滴漆工艺守则进行(节拍时间、温度、漆的配比)。
滴漆后应进行电枢完工检。
查看有无气泡,滴漆饱满度,表面质量。
5.包装物一般性检验、检验内容、要求及抽样标准(如不合格,加严)
5。
1说明书
5。
1.1首次制作或内容修改,先由销售部确认内容是否正确,再由品质部检验;重复制
作则直接由品质部检验;说明书字迹应印刷清晰,说明书内页不得有缺角,残页。
按照IL=I,AQL=4.0检验.
5.1.2说明书内容、语言类型、材料应符合包装资料通知单要求.按照IL=I,AQL=4。
0检验。
5.2商标
5.2。
1商标上字迹印刷清晰,不得有重影、缺角,内容应完整;使用材料应正确,首次制作或有修改应先由销售部确认内容。
按照IL=I,AQL=4.0检验。
5.2。
2检验商标尺寸,商标尺寸应与机壳商标位置尺寸相吻合,商标不干胶应粘接牢靠、不卷曲、不翘曲。
每批抽检3~4副。
5.2。
3商标内容、标志、颜色、材质应与包装资料通知单要求相符合。
5。
3彩盒
5.3.1彩盒外表面字迹、图案印刷清晰明朗,不得有重影,破损,内容完整正确.按照IL=I,AQL=4。
0检验。
5。
3.2彩盒的撕揉硬度应符合规定要求,彩盒外表尺寸应符合规定要求。
每批抽检2~3只。
5。
3。
3彩盒印刷内容、标志、颜色、材料、层数、表面处理方法应与包装资料通知单要求相符合。
按照IL=I,AQL=4。
0检验。
5.4外箱
5。
4.1外箱字迹印刷清楚,内容完整正确,文字大小、纸箱强度符合要求,外表不得有破损。
按照IL=I,AQL=4.0检验。
5.4。
2检验外箱尺寸是否符合包装规定要求,同彩盒的配合是否合理。
每批抽检2~3只。
5。
4。
3外箱表面印刷内容、颜色、标志、层数与产品包装资料通知单要求相符合。
按照IL=I,AQL=4。
0检验.
5。
5袋子
QJ/HU-0805-2005
质量控制检验规范QJ/HU-0805-2005
5.5。
1检验包装用袋子(说明书袋、碳刷袋、扳手袋、整机袋等)内容、撕揉强度是否符合包装使用要求.按照IL=I,AQL=4.0检验。
5。
5.2检验袋子规格、厚薄是否适合包装要求,检验袋子上印刷标志、内容是否同包装资料通知单相符合,检验开口尺寸超过18mm的袋子是否打孔.每批抽检5~8只.
6.标准件一般性检验、检验内容、要求及抽样标准
6。
1轴承
6.1。
1检验轴承型号、代号是否符合产品任务单、产品使用要求。
每批检验6~8套。
6。
1。
2检验轴承转动灵活性,应地卡滞。
按照IL=I,AQL=4。
0检验。
6.1.3按IL=I,AQL=4在轴承综合检查仪上检验精度。
6.1.4滚针轴承要求供方提供轴承性能检测报告,样品封存.
6。
2螺钉
6.2。
1检验螺钉长度尺寸、外径尺寸符合使用要求。
每袋抽检5~6枚。
6。
2。
2检验螺钉表面处理情况,应符合镀层要求.每袋抽检6~8枚。
6。
2。
3检验螺钉强度,应符合有关标准规定或使用要求(螺钉头不易打滑)。
在实际装配过程中检验。
6.3铜管、接插件
6.3。
1检验其规格尺寸,符合有关标准规定并满足装配使用要求。
每袋抽检6~8只。
6。
3。
2检验强度,应有一定韧性,符合有关标准规或使用要求(不易夹碎)。
在实际装配过程中检验。
7.成品一般性检验、检验内容、要求及抽样示准
检验部门:
装配检验
7。
1检验控制
7.1.1装配巡检:
a)查看机器内部布线是否正确到位,必要时可设立专职岗位检查.内接线是否有露铜,是否有挤压破现象,接插件是否可靠(必要时可吊0。
6kg重量进行确认)开关灵活情况,每班巡检不少于五次.
b)观察流水线上机器振动、火花、齿音、烧机等情况,并进行分析、确认是否为装配质量差所造成,进行反馈纠正.
7.1。
2整机运行:
a)把整机插入到流水线检验台上,让工具空载运行15min。
在运转过程中,观察流水线上整机运转情况,观察火花情况,若出现异常情况应立即拔掉整机插头。
QJ/HU-0805-2005
质量控制检验规范QJ/HU-0805—2005
b)测定机器空载转速,每批机器检测5~8台,应符合要求。
7.2单机检验
7。
2。
1运转15min后,进行高压测试,耐压50Hz、4000V,泄漏电流0。
5mA,耐电压时间3s不击穿。
7。
2。
2外观质量:
a)漆层表面不能有磕碰脱落;
b)塑料件表面不能有裂纹,银丝等缺陷,塑料件之间不应有明显色差;
c)外壳零件相互接合面之间错位量不大于0.5mm。
7.2。
3检验每台机的振动情况.按传统封样进行判别,当总体水平提高时,允许提高判定水平.
7。
2.4检验噪声,在空载运行时,监听机器的运转声,运转应均匀和谐,没有异常杂音,检验时,可以按规定的标准用类比判别法。
当总体水平提高时,允许提高判定水平。
7.2。
5检验火花,符合火花等级情况〈2级.
7.2.6转动输出轴,检查齿轮齿侧间隙,键连接是否过松。
7.2.7检查空载电流或空载功率,不能超过各型号规定要求.
7.2.8各联接螺钉应拧到位,各部件间不应有松动.
7.2.9紧固件不能有锈蚀并无漏装、错装,螺钉槽不能翻边起毛;
7.2。
10开关动作应灵活,有自锁或安全装置的机构需灵活有效;无级调速开关应能调至零转速,调速均匀;装软启动工具的缓起动时间应大于3秒,正常运转时注意转速不能明显较低,必要时测转速。
7。
2.11各类工具固有的性能应灵活、有效,如角磨的自锁钮、冲击钻的冲击。
7.2。
12客户所要求的特殊检验,按照客户要求检验方法进行.
7。
3包装检验
7。
3。
1工具外表干净无污物,漆层无脱落,商标、铭牌位置无差错,方向正确,粘贴牢靠,无翘边。
开关置于“OFF"位置,各种附件数量和放置正确。
8.其它
以上规定如和具体产品的检验卡片不一致时,应按具体产品的检验卡片要求进行具体产品的检验。
附加说明:
1、本标准由浙江伦达实业有限公司技术部提出
2、本标准主要起草人:
3、本标准批准人: