防爆无轨胶轮车地盘传动系统设计Word格式.doc
《防爆无轨胶轮车地盘传动系统设计Word格式.doc》由会员分享,可在线阅读,更多相关《防爆无轨胶轮车地盘传动系统设计Word格式.doc(73页珍藏版)》请在冰点文库上搜索。
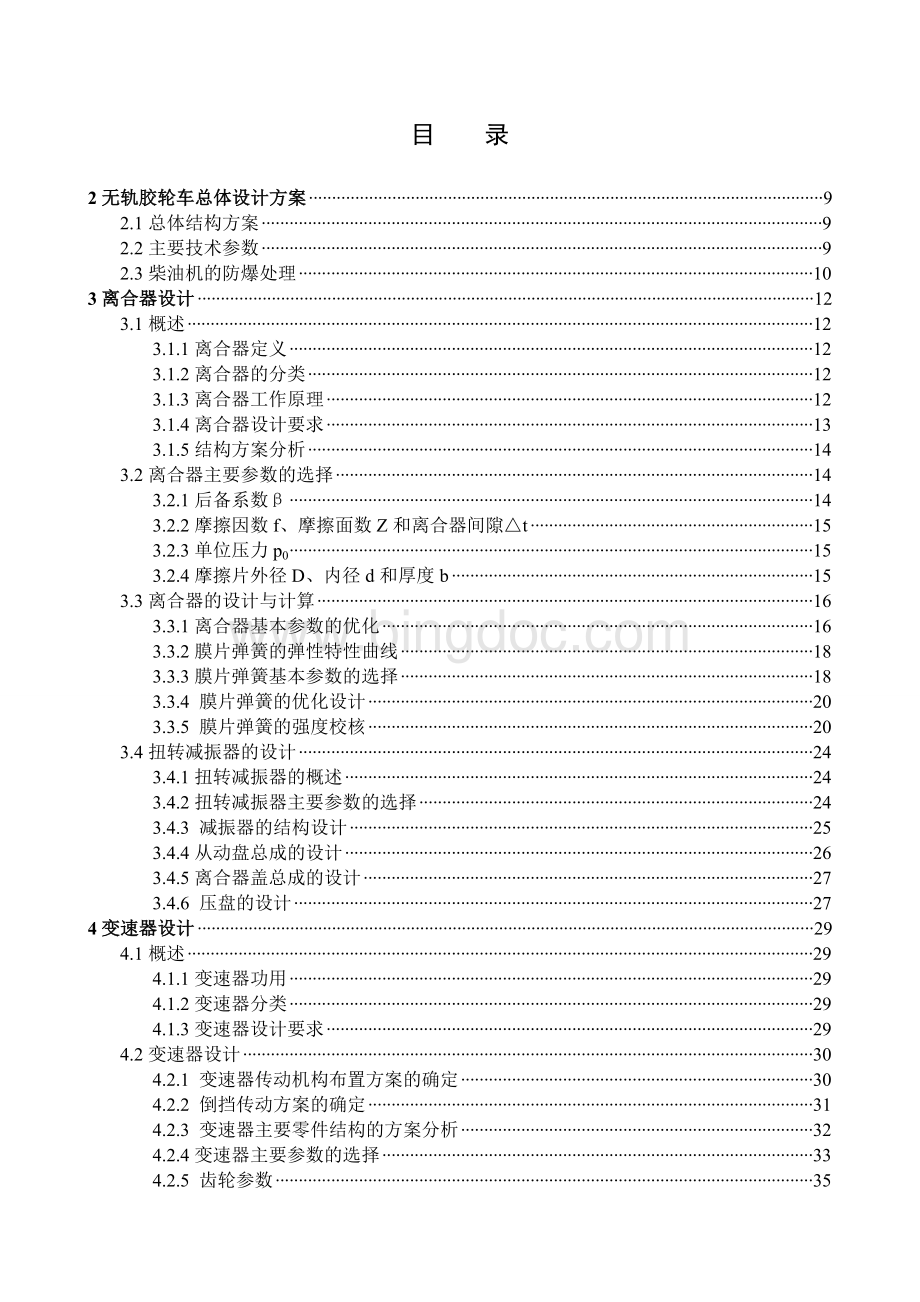
4.2.9变速器同步器的设计 47
4.2.10轴承的选择 49
5驱动桥设计 51
5.1概述 51
5.2主减速器设计计算 52
5.2.1主减速器的结构形式的选择 52
5.2.2主减速器的基本参数选择与设计计算 53
5.2.3双曲面齿轮尺寸计算 55
5.2.4主减速器双曲面齿轮的强度计算 63
5.2.5主减速器锥齿轮轴承的载荷计算 65
5.2.6主减速器齿轮的材料及热处理 69
5.2.7主减速器的润滑 69
5.3差速器设计计算 70
5.3.1差速器类型的选择 70
5.3.2差速器齿轮的基本参数选择 71
5.3.3差速器齿轮的几何参数的计算 72
5.3.4差速器齿轮与强度计算 74
5.3.5半轴的设计 74
6制动器设计 77
6.1概述 77
6.1.1定义 77
6.1.2无轨胶轮车对制动器的要求 77
6.1.3煤矿井下无轨轻型胶轮车制动器的选型 77
6.1.4全封闭湿式安全型多盘制动器 78
6.2盘式制动器的主要元件 78
6.3盘式制动器设计 79
2无轨胶轮车总体设计方案
2.1总体结构方案
本次设计参照太原煤科院设计的WqC2J型煤矿胶轮车,在平头单排载货汽车的基础上,通过安装防爆柴油机、防爆离合器、防爆湿式制动器、防爆电气等系统,并对车架、驾驶室、车厢进行了改造和加强,改装成防爆车辆,适用于有瓦斯和煤尘爆炸危险的煤矿井下使用。
整车结构为整体车身、防爆柴油机、防爆电机、防爆蓄电池、防爆机械传动、4×
2后双轮驱动、钢板弹簧悬挂、带差速器驱动桥、边梁式车架、前后轮湿式制动、可拆卸式驾驶室、平头后开式车厢。
整车在发动机、离合器、制动器、电气系统等方面采取符合规程中有关防爆规定的防爆措施。
防爆柴油机主机选用国外主机并配套研制新型防爆、净化、冷却、启动等装置;
选用后备功率大的防爆柴油机,能满足长距大坡度运行工况的要求,提高车辆的爬坡性能;
工作制动采用湿式制动方式,满足防爆要求和制动性能要求;
为提高使用可靠性,其发动机和气动系统中的关键部件选用进口件。
图2-1防爆无轨脚轮车
2.2主要技术参数
表2-1整车技术参数
驱动方式
4×
2后双轮驱动
型式
平头后开门货厢式
驾驶操纵
正向操纵
额定载质量(kg)
3000
整车装备质量(kg)
3800
外形尺寸(㎜)
(长×
宽×
高)
4850×
2000×
2180
最小离地间隙(㎜)
200
轮胎型号
8.25-16
表2-2防爆柴油机主要技术参数
类型
四缸直列水冷式
额定功率/转速
60kw/2200r/min
最大扭矩/转速
300N·
m/1500-1600/min
2.3柴油机的防爆处理
该车选用四缸直列式水冷柴油机,采用闭式水冷却循环系统和气压启动方式,安装空气压缩机、风冷型散热器、气控熄火装置及附属装置。
进排气系统是柴油机防爆装置的主要部分。
进气由防爆栅栏和气控阻风门装置组成。
排气系统由排气防爆栅栏、水冷却排气管及废气处理箱组成,排气管采用水冷却方式,对排气管、废气处理箱及其防爆栅栏进行了特殊设计制造,使尾气净化,排气温度下降到70℃以下,以满足防爆要求。
图2-2柴油机防爆系统
3离合器设计
3.1概述
3.1.1离合器定义
离合器是汽车传动系中直接与发动机相连接的总成,其主要功用是切断和实现对传动系的动力传递,以保证汽车起步时将发动机与传动系平顺地接合,确保汽车平稳起步;
在换挡时将发动机与传动系分离,减少变速器中换挡齿轮之间的冲击;
在工作中受到大的动载荷时,能限制传动系所承受的最大转矩,防止传动系各零件因过载而损坏;
有效地降低传动系中的振动和噪声。
3.1.2离合器的分类
汽车离合器有摩擦式、液力式和电磁式等三种类型
摩擦离合器主要由主动部分(发动机飞轮、离合器盖和压盘等)、从动部分(从动盘)、压紧机构(压紧弹簧)和操纵机构(分离叉、分离轴承、离合器踏板及传动部件等)四部分组成。
主、从动部分和压紧机构是保证离合器处于接合状态并能传递动力的基本结构,操纵机构是使离合器主、从动部分分离的装置。
3.1.3离合器工作原理
在机械式传动系统中,离合器是作为一个独立的部件而存在。
它实际上是一种依靠其主、从动部分间的摩擦来传递动力且能分离的机构(见图3-1)其基本功用有三:
第一,在汽车起步时,通过离合器主动部分(和发动机曲轴相联)和从动部分(与变速器第一轴相接)之间的滑磨、转速的逐渐接近,使旋转着的发动机和原为静止的传动系平稳地联接起来,以保证汽车平稳起步;
第二,当变速器换档时,通过离合器主、从动部分的迅速分离来切断动力传递,以减轻换档时轮齿间的冲击,便于换档;
图3-1离合器工作原理
a)离合器处于接合状态;
b)离合器处子分离状态
1一飞轮;
2一离合器从动盘;
3一离合器踏板;
4一压紧弹鳖;
5一离合器轴;
6一从动盘毅;
7一曲轴
第三,当传给离合器的扭矩超过其所能传递的最大力矩(即离合器的最大摩擦力矩)时,其主、从动部分将产生相对滑磨。
这样,离合器就起着保护传动系防上其过载的作用。
例如:
当汽车作紧急制动而又没有分离离合器时,由于离合器的滑磨可避免发动机因突然减速而引起巨天的惯性力矩。
由上述工作原理可以看出,摩原离合器基本上由主动部分、从动部分、压紧机构和操纵机构四部分组成。
主、从动部分和压紧机构是保证离合器处于接合状态并能传递动力的基本结构,而离合器的操纵机构主要是使离合器分离的装置。
离合器的具体结构,首先应在保证传递发动机最大转矩的前提下,满足两个基本性能要求:
①分离彻底;
②接合柔和。
其次,离合器从动部分的转动惯量要尽可能小。
前己提及,离合器的功用之一是当变速器换挡时中断动力传递,以减小齿轮间冲击。
如果与变速器主动轴相连的离合器从动部分的转动惯量大,当换挡时,虽然由于分离了离合器,使发动机与变速器之间的联系脱开,但离合器从动部分较大的惯性力矩仍然输入给变速器,其效果相当于分离不彻底,就不能很好地起到减轻轮齿间冲击的作用。
此外,还要求离合器散热良好,因为在汽车行驶过程中,驾驶员操纵离合器的次数是很多的,这就使离合器中由于摩擦面间频繁地相对滑磨而产生大量的热。
离合器接合越柔和,产生的热量越大。
这些热量如不及时地散出,对离合器的工作将产生严重影响。
3.1.4离合器设计要求
为了保证离合器具有良好的工作性能,对汽车离合器设计提出如下基本要求:
1)在任何行驶条件下均能可靠地传递发动机的最大转矩,并有适当的转矩储备;
2)接合时要平顺柔和,以保证汽车起步时没有抖动和冲击;
3)分离时要迅速、彻底;
4)离合器从动部分转动惯量要小,以减轻换挡时变速器齿轮间的冲击,便于换挡和减小同步器的磨损。
5)应有足够的吸热能力和良好的通风散热效果,以保证一工作温度不致过高,延长其使用寿命。
6)应使传动系避免扭转共振,并具有吸收振动、缓和冲击和减小嗓声的能力。
7)操纵轻便、准确,以减轻驾驶员的疲劳。
8)作用在从动盘上的压力和摩擦材料的摩擦因数在使用过程中变化要尽可能小,以保证有稳定的工作性能。
9)应有足够的强度和良好的动平衡,以保证其工作可靠、寿命长。
10)结构应简单、紧凑、质量小、制造工艺性好,拆装、维修、调整方便等。
3.1.5结构方案分析
(1)从动盘数的选择:
单片离合器
单片离合器:
对乘用车和最大质量小于6t的商用车而言,发动机的最大转矩一般不大,在布置尺寸容许条件下,离合器通常只设有一片从动盘。
单片离合器的结构简单,轴向尺寸紧凑,散热良好,维修调整方便,从动部分转动惯量小,在使用时能保证分离彻底,采用轴向有弹性的从动盘可保证结合平顺。
(2)压紧弹簧和布置形式的选择:
拉式膜片弹簧离合器
膜片弹簧是一种由弹簧钢制成的具有特殊结构的碟形弹簧,主要由碟簧部分和分离指部分组成。
a.膜片弹簧离合器与其他形式的离合器相比,有如下优点:
1)具有较理想的非线性弹性特性。
2)兼起压紧弹簧和分离杠杆的作用。
3)高速旋转时,弹簧压紧力降低很少,性能较稳定。
4)以整个圆周与压盘接触,使压力分布均匀,摩擦片接触良好,磨损均匀。
5)通风散热良好,使用寿命长。
6)膜片弹簧中心与离合器中心线重合,平衡性好。
b.与推式相比,拉式膜片弹簧离合器具有许多优点:
取消了中间支承各零件,并不用支承环或只用一个支承环,使其结构更简单、紧凑,零件数目更少,质量更小等。
(3)膜片弹簧的支撑形式
图3-2为拉式膜片弹簧的支承形式—单支承环形式,将膜片弹簧大端支承在离合器盖中的支承环上。
图3-2拉式膜片弹簧离合器支撑形式
3.2离合器主要参数的选择
3.2.1后备系数β
后备系数β是离合器设计中的一个重要参数,它反映了离合器传递发动机最大转矩的可靠程度。
在选择β时,应考虑摩擦片在使用中的磨损后离合器仍能可靠地传递发动机最大转矩、防止离合器滑磨时间过长、防止传动系过载以及操纵轻便等因素。
轿车和微型、轻型货车β=1.20—1.75,
中型和重型货车β=1.50—2.25,
越野车、带拖挂的重型车或牵引车β=1.80一4.0,
本次设计取β=1.5。
3.2.2摩擦因数f、摩擦面数Z和离合器间隙△t
摩擦片的摩擦因数f取决于摩擦片所用的材料及其工作温度、单位压力和滑磨速度等因素。
摩擦因数f的取值范围见下表。
表3-1摩擦材料的摩擦因数f的取值范围
摩擦材料
摩擦因数
石棉基材料
模压
0.20~0.25
编织
0.25~0.35
粉末冶金材料
铜基
铁基
0.35~0.50
金属陶瓷材料
0.70~1.50
本次设计取f=0.30。
摩擦面数Z为离合器从动盘数的两倍,决定于离合器所需传递转矩的大小及其结构尺寸。
本次设计取单片离合器Z=2。
离合器间隙△t是指离合器处于正常结合状态、分离套筒被回位弹簧拉到后极限位置时,为保证摩擦片正常磨损过程中离合器仍能完全结合,在分离轴承和分离杠杆内端之间留有的间隙。
该间隙△t一般为3~4mm。
本次设计取△t=3.5mm。
3.2.3单位压力p0
单位压力p决定了摩擦表面的耐磨性,对离合器工作性能和使用寿命有很大影响,选取时应考虑离合器的工作条件、发动机后备功率的大小、摩擦片尺寸、材料及其质量和后备系数等因素。
p取值范围见表3-2。
表3-2摩擦片单位压力p的取值范围
摩擦片材料
单位压力p/Mpa
0.15~0.25
p选择:
0.10MPa≤p0≤1.50MPa,本次设计取p=0.28MPa。
3.2.4摩擦片外径D、内径d和厚度b
摩擦片外径是离合器的重要参数,它对离合器的轮廓尺寸、质量和使用寿命有决定性的影响。
D=(3-1)
其中为直径系数,轿车=14.5;
微型、轻型货车:
单片=16.0~18.5,双片=13.5~15;
重型货车=22.5~24.0。
本设计取17.5。
D=17.5=303mm
取D=325mm
当摩擦片外径D确定后,摩擦片内径d可根据d/D在0.53~0.70之间来确定。
表3-3离合器摩擦片尺寸系列和参数
外径D(mm)
内径d(mm)
厚度h(mm)
单面面积F()
160
110
3.2
0.687
0.676
106
180
125
3.5
0.691
0.667
132
140
0.700
0.657
225
150
0.703
221
250
155
0.620
0.762
302
280
165
0.589
0.796
402
300
175
0.583
0.802
466
325
190
0.585
0.800
546
350
195
4
0.557
0.827
678
380
205
0.540
0.843
729
405
220
0.543
0.840
908
430
230
0.535
0.847
1037
取d=190mm
摩擦片厚度b主要有3.2mm、3.5mm、4.0mm三种。
取b=3.5mm。
C===0.585
3.3离合器的设计与计算
3.3.1离合器基本参数的优化
设计离合器要确定离合器的性能参数和尺寸参数,这些参数的变化直接影响离合器的工作性能和结构尺寸。
这些参数的确定在前面是采用先初选、后校核的方法。
下面采用优化的方法来确定这些参数。
1)摩擦片外径D(mm)的选取应使最大圆周速度v不超过65~70m/s,即
v=nD10=220032510=37.4m/s≤65~70m/s(3-2)
符合要求。
式中,v为摩擦片最大圆周速度(m/s);
n为发动机最高转速(r/min)。
2)摩擦片的内、外径比c应在0.53~0.70范围内,本次设计取c=0.69。
3)为了保证离合器可靠地传递发动机的转矩,并防止传动系过载,不同的车型的β值应在一定范围内,最大范围为1.2~4.0,本次设计取β=1.50。
4)为了保证扭转减振器的安装,摩擦片内径d必须大于减振器弹簧位置直径2R约50mm,即d>
2R+50mm
5)为反映离合器传递转矩并保护过载的能力,单位摩擦面积传递的转矩应小于其许用值,即
=(3-3)
式中,为单位摩擦面积传递的扭矩(N·
m/);
为其允许值(N·
m/),按表3-4取值。
表3-4单位摩擦面积传递扭矩的许用值()
离合器规格D/mm
≤210
>210~250
>250~325
>325
0.28
0.30
0.35
0.40
=0.35N·
m/
T=βT=1.5300=450N.m
==4.12N·
m/<
6)为降低离合器滑磨时的热负荷,防止摩擦片损伤,对于不同车型,单位压力p根据所用的摩擦材料在一定范围内选取,p的最大范围为0.10~1.50Mpa。
本次设计取p=0.3Mpa。
7)为了减少汽车起步过程中离合器的滑磨,防止摩擦片表面温度过高而发生烧伤,离合器每一次结合的单位摩擦面积滑磨功w应小于其许用值[w]。
汽车起步时离合器结合一次所产生的总滑磨功(J)为:
W=()==16771.9J
式中,m为汽车总质量(kg);
rr为轮胎滚动半径(m);
i为汽车起步时所用变速器档位的传动比;
i为主减速器传动比;
n为发动机转速(r/min)。
w=<
[w]=0.4J/mm
满足要求
3.3.2膜片弹簧的弹性特性曲线
图3-3不同H/h值时的无因次特性曲线
前面说过膜片弹簧起弹性作用的部分是其碟簧部分。
碟簧部分的弹性变形特性和螺旋弹簧不一样。
它是一种非线性的弹氓其特性和碟簧部分的原始内曲维高H及弹簧片厚A之比值H/h有关。
不同的H/A值可以得到不同的弹性变形特性。
一船可分成下列四种情况,
(1)=1.5
如图3-3中=0.5的曲线。
其曲线形状表现为:
载荷p的增加,变形λ总是不断增加。
这种弹簧的刚度很大,可以承受很大的载荷,适合予作为缓冲装置中曲行程限制器。
(2)=
如图3-3中=之曲线,弹簧的特性曲线在中间有一段很平直,变形的增加载荷P几乎维持不变。
此种弹簧叫做零刚度弹簧。
(3)
如图3-3中=2.75者,弹簧的特性曲线中有一段负刚皮区域,即当变形增加时,载荷反而减小。
具有这种特性的膜片弹簧很适用于作为离合器的压紧弹簧。
因为可利用其负刚度区,达到分离离合器时载荷下降、操纵省力之目的。
当然,负刚度过大也不适宜,以免弹簧工作位置略微变动造成弹簧压紧力变化过大。
(4)
如图3-3中=3时,这种弹簧的特性曲线中具有更大的负刚度不稳定工况区而且具有载荷为负值的区域。
这种弹簧适用于汽车液力传动中的锁止机构。
3.3.3膜片弹簧基本参数的选择
1)比值H/h和h的选择
设计膜片弹簧时,要利用其非线性的弹性变形规律,因此要正确选择其特性曲线的形状,以获得最佳的使用性能。
一般汽车上膜片弹簧的H/h值都在1.5~2.0,板厚h为2~4mm。
取h=4mm,H/h=1.7,即H=1.7h=6.8mm。
2)R/r比值和R、r的选择
比值R/r的选定,关系到碟簧材料的利用。
研究表明,R/r愈大,则弹簧重量利用效率愈低。
据分析,碟形弹簧储存弹性能的能力在比值R/r=1.8—2.0时为最大。
因此在设计供缓和冲击、吸收振动等需要储存大量弹性能的碟形弹簧时,最好取R/r=1.5—2.1。
对于汽车的膜片弹簧来说,设计上并都要求储存大量的弹性能,而是根据结构布置与压紧力的需要,通常取R/r<1.5,一般都在1.25左右。
膜片弹簧大端外半径4,应当满足结构上的要求而和摩擦片的尺寸相适应,大于摩擦片的内半径d/2,近于摩擦片的外半径D/2。
此外,当H、h及R/r等不变时,增加R特有利于膜片弹簧应力的下降。
为使摩擦片上的压力分布较均匀,拉式膜片弹簧的r值宜为大于或等级。
即
R=摩擦片外径162.5mm
取R/r=1.3,r=R/1.3=125mm。
3)α的选择
膜片弹簧自由状态下圆锥角α与内截锥高度H关系密切,α一般在9°
~15°
范围内。
α===10.3°
,符合要求。
4)膜片弹簧小端内半径,小端半径及分离轴承作用半径rp的确定
由离合器的结构决定,其最小值应大于变速器第一轴花键的外径。
rp应大于。
I轴外径DA=105=33.13mm
取>
I轴花键外径=24mm
由文献[4]得知花键尺寸
所以=33mm,=36mm,rp=40mm
5)分离指数目n,切槽宽度δ1、δ2及半径re的确定
分离指数目n常取18,大尺寸膜片弹簧可取24,小尺寸膜片弹簧可取12。
取分离之数目n=18。
δ=3.2~3.5mm,δ=9~10mm,re的取值应满足rre≥δ。
本次设计取δ=3.5mm,δ=10mm,re≤rδ=115mm。
6)支承环平均半径e和膜片弹簧与压盘接触半径L
e和L的大小将影响膜片弹簧的刚度。
一般说,e值应尽量接近r而略大于r,L应接近R而略小于R。
e=129mm,L=157mm
3.3.4膜片弹簧的优化设计
膜片弹簧的优化设计就是要确定一组弹簧的基本参数,使其弹性特性满足离合器的使用性能要求,而且弹簧强度也满足设计要求,以达到最佳的综合效果。
1)应保证所设计的弹簧工作压紧力与要求压紧力相等,即
2)为了保证各工作点A,B,C有较合适的位置A点在凸点M左边,B点在拐点H附近,C点在凹点N附近,应正确选择相对于拐点的位置,一般/=0.8~1.0,即
0.8
3)为厂保证摩擦片磨损后离合器仍能可靠地传递转矩,并考虑到摩擦因数的下降,摩擦片磨损后弹簧工作压紧力、应大于或等于新摩擦片时的压紧力,即
4)为了满足离合器使用性能的要求,弹簧的H/h与初始底锥角α≈H/(R-r)应在一定范围内,即
1.5≤H/h=1.7≤2.5
9°
≤α≈H/(R-r)=10.3°
≤15°
5)弹簧各部分有关尺寸的比值应符合一定的范围,即
1.20≤R/r=1.3≤1.35
70≤2R/h=81.25≤100
3.5≤R/r0=4.9≤5.0
6)为了使摩擦片上的压紧力分布比较均匀,拉式膜片弹簧的压盘加载点半径e应位于摩擦片的平均半径与外半径之间,即
(D+d)/4≤e=129≤D/2
7)根据弹簧结构布置要求,R1与R,rf与r0之差应在一定范围内,即
1≤R-L=5.5≤7
0≤=4≤4
0≤=3≤4
8)膜片弹簧的分离指起分离杠杆的作用,因此其杠杆比应在一定范围内选取,即
3.5≤