金属技术监控工作规程Word文档格式.docx
《金属技术监控工作规程Word文档格式.docx》由会员分享,可在线阅读,更多相关《金属技术监控工作规程Word文档格式.docx(39页珍藏版)》请在冰点文库上搜索。
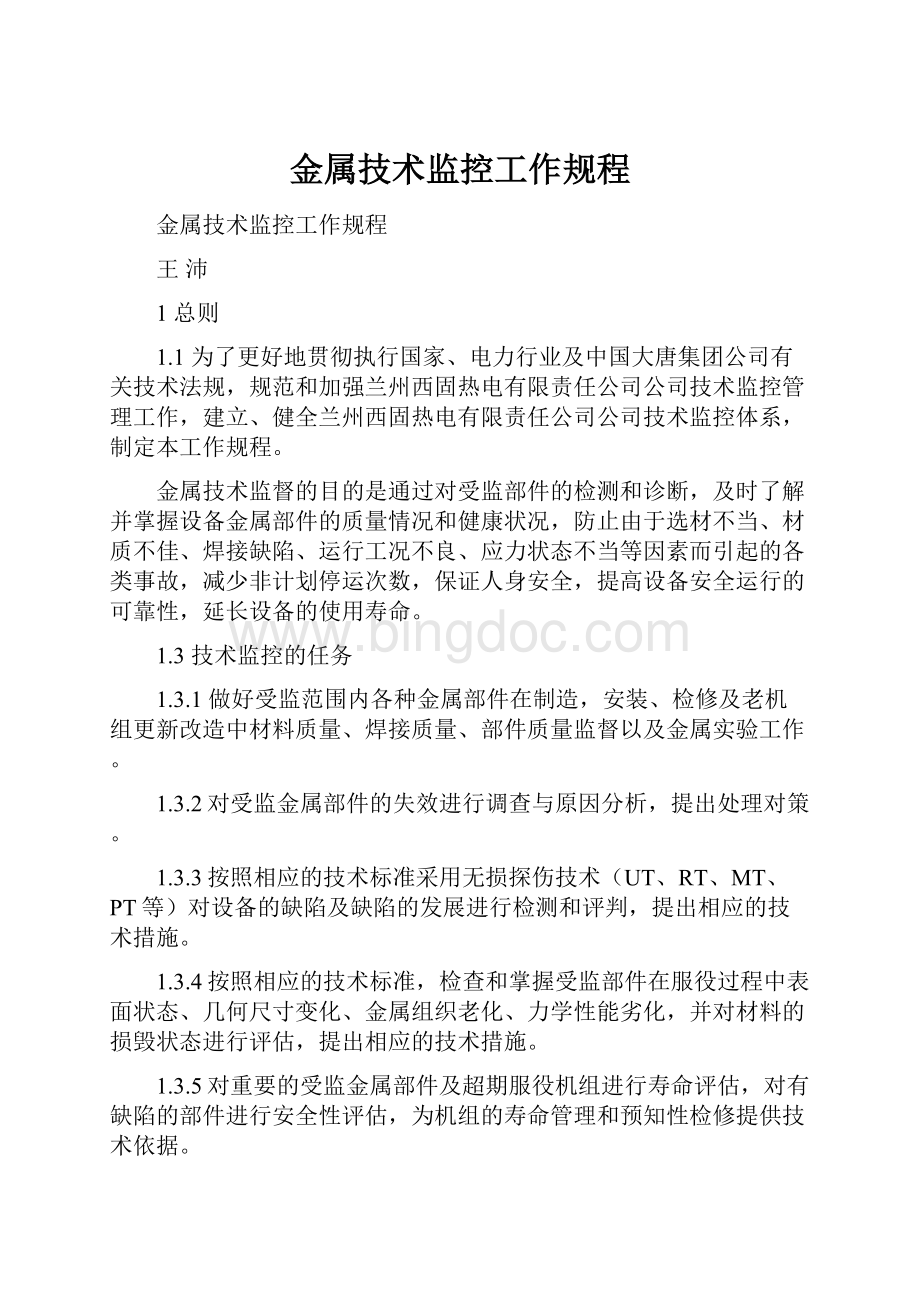
10.DL/T786-2001《碳钢石墨化检验及评级标准》
11.DL/T752-2010《火力发电厂异种钢焊接技术规程》
12.DL/T939-2005《火力发电厂锅炉受热面管监督检验技术导则》
13.DL/T820-2002《管道焊接接头超声波检验技术规程》
14.DL/T821-2002《钢制承压管道对接焊接接头射线检验技术规程》
15.DL/T616-2006《火力发电厂汽水管道与支吊架维修调整导则》
16.JB/T4730-2005《承压设备无损检测》
17.DL/T884-2004《火电厂金相检验与评定技术导则》
18.DL/T647-2004《电站锅炉压力容器检验规程》
19.DL/T439-2006《火力发电厂高温紧固件技术导则》
20.DL/T787-2001《火力发电厂用15CrMo钢珠光体球化评级标准》
21.DL/T999-2006《电站用2.25Cr-1Mo钢球化评级标准》
22.DL/T773-2001《火力发电厂用12Cr1MoV钢球化评级标准》
23.DL/T884-2004《火电厂金相检验与评定技术导则》
24.GB/T3323-2005《金属熔化焊焊接接头射线照相》
25.TSGZ6002-2010《特种设备焊接操作人员考核细则》
26.《中国大唐集团公司火电金属技术监督制度》
3监督范围
3.1工作温度大于等于450℃的高温承压金属部件(含主蒸汽管道、高温再热蒸汽管道、过热器管、再热器管、联箱、阀壳和三通),以及与主蒸汽管道相联的小管道。
3.2工作温度大于等于435℃的导汽管。
3.3工作压力大于等于3.82MPa的锅筒。
3.4工作压力大于等于5.88MPa的承压汽水管道和部件(含水冷壁管、省煤器管、联箱和主给水管道)。
3.5300MW及以上机组的低温再热蒸汽管道。
3.6汽轮机大轴、叶轮、叶片和发电机大轴、护环、风扇叶。
3.7工作温度大于等于400℃的螺栓。
3.8工作温度大于等于435℃的汽缸、汽室、主汽门。
3.9设计温度大于450℃或工作压力大于等于5.88MPa,起连通、测量、排放和取样等作用的抽(排)汽管、疏放水管、加药管、再循环管、蒸汽取样管、仪表管、联络管、蒸汽吹灰管和锅炉底部加热管道。
4金属材料的监督
4.1受监范围的金属材料及其部件应严格的按照相应的国内外国家标准,行业标准的规定对其质量进行验收。
4.1.1高压锅炉用无缝钢管定货按GB5310-2008执行。
受监的钢材、钢管、备品及配件应按质量保证书100%进行质量验收。
4.1.2受监的钢材、焊接材料以及备品备件入库前应通知金属技术监督部门按照相应的标准、规程,进行入厂检验,质量符合标准要求的方可入厂入库。
合金钢部件、焊接材料、备品备件使用前都应交金属技术监督部门进行光谱试验以核对材质,避免错用.
4.1.3我公司重要受监部件的材质与规格见附表A(330MW)、附表B(165MW)。
4.2锅炉用材料入厂验收按JB/T3375-2002执行。
当缺少原始资料时,物资管理部门应主动委托有资格的检验单位进行试验。
4.3对进口钢材、钢管和配件等,进口单位应在索赔期内,按合同规定进行质量验收。
除应符合相关国家的标准和合同规定的技术条件外,还应有商检合格证明书。
4.4金属材料的代用原则
4.4.1采用代用材料,应持慎重的态度,要有充分的技术依据,原则上应选用性能略优者;
应保证在使用条件下各项性能指标均不低于设计要求。
4.4.2检修中使用代用材料时,应征得金属技术监督专责工程师的同意,并经总工程师批准。
4.4.3采用代用材料后应做好记录,同时应在相应的图纸上注明。
4.5物资供应部、班组仓库储存受监范围的钢材,钢管、焊接材料和备品配件等,应建立严格的质量验收和领用制度,严防错用错发。
4.6原材料的存放应根据当地的气候条件,存放时间的长短,建立严格的保管制度,防止变形,腐蚀和损伤,奥氏体不锈钢不能与碳素钢不能混放,要单独存放。
5金属备品配件安装使用前的监督与检验
5.7主蒸汽、再热蒸汽、导汽管,根据DL/T438-2009在进入生产现场使用前要进行如下检验:
a)钢管表面上的标记(钢印或漆记)应与该制造商产品标记相符。
b)100%进行外观检查,钢管的内外表面不容许有裂纹、折叠、结疤、离层等缺陷,钢管的表面的裂纹、机械划痕、擦伤和凹陷等缺陷应完全清除,清除出应圆滑过渡,清理处的最小壁厚不得小于钢管偏差所允许的最小值且不应小于钢管计算最小壁厚值。
钢管的直径与壁厚必须要达到我们的使用要求并且符合相关国家标准或行业标准的规定与要求。
c)钢管的内外表面不允许有大于以下尺寸的直道缺陷:
热轧(挤)管,大于壁厚的5%,且最大深度大于0.4mm.
d)对合金钢管要逐根进行光谱分析,光谱检验按DL/T991-2006执行。
e)校核钢管的壁厚和管径要符合相关标准的规定和订货要求。
f)合金钢管按同规格根数的50%进行硬度检验,每炉批至少抽查1根在每根钢管的3个截面(两端和中间)检验硬度,若发现硬度异常,要进行金相组织的检验。
常用金属材料的硬度值见附表C。
g)合金钢管按同规格根数的10%进行金相检验,每炉批至少抽查1根。
5.8受监督的弯头、弯管,根据DL/T438-2009在进入生产现场使用前要进行如下检验:
a)弯头、弯管表面上的标记(钢印或漆记)应与该制造商产品标记相符。
b)100%进行外观检查,钢管的内外表面不容许有裂纹、折叠、结疤、离层等缺陷,钢管的表面的裂纹、机械划痕、擦伤和凹陷等缺陷应完全清除,清除出应圆滑过渡,清理处的最小壁厚不得小于钢管偏差所允许的最小值且不应小于钢管计算最小壁厚值。
c)按质量证明书校核弯头、弯管规格并检查弯头、弯管的中性面、内外弧侧壁厚、椭圆度和波浪率。
d)弯头、弯管对要逐根进行光谱分析,光谱检验按DL/T991-2006执行。
e)对合金弯头、弯管100%进行硬度检验,至少在外弧侧顶点和侧弧中间位置侧3点。
f)对合金弯头、弯管按10%进行金相检验,同一规格不得少于1件。
g)弯头、弯管的外弧侧的最小壁厚小于计算最小壁厚时按不合格处理。
h)弯头、弯管的几何形状和尺寸不符合要求时按不合格处理。
5.9受监督的锻制、热压和焊制三通以及异径管,根据DL/T438-2009在进入生产现场使用前要进行如下检验:
a)三通以及异径管上的标记(钢印或漆记)应与该制造商产品标记相符。
b)100%进行外观检查,钢管的内外表面不容许有裂纹、折叠、重皮、尖锐划痕和凹陷等缺陷,如果有应完全清除,清除出应圆滑过渡,清理处的最小壁厚不得小于钢管偏差所允许的最小值且不应小于钢管计算最小壁厚值。
三通肩部的厚度要大于主管公称壁厚的1.4倍。
e)合金钢管三通以及异径管逐根进行光谱分析,光谱检验按DL/T991-2006执行。
f)合金钢管三通以及异径管100%进行硬度检验,三通至少在肩部和腹部位置各测3点,异径管至少在大小头位置侧3点。
g)合金钢管三通及异径管按10%进行金相检验,不得少于1件。
h)三通以及异径管几何形状和尺寸不符合要求时按不合格处理。
i)三通以及异径管最小壁厚小于计算最小壁厚时按不合格处理。
5.10受监督的阀门,根据DL/T438-2009在进入生产现场使用前要进行如下检验:
a)阀门上的标记(钢印或漆记)应与该制造商产品标记相符。
b)按质量证明书校核阀壳材料有关技术指标应符合现行国家或行业标准。
c)校核阀门的规格,并进行100%外观检验铸造阀壳内外表面应光洁,不得存在裂纹、气孔、毛刺、夹砂及尖锐划痕等缺陷;
锻造阀壳表面不得存在裂纹、折叠、重皮、凹陷及尖锐划痕等缺陷;
焊缝表面不得有裂纹、气孔、咬边、漏焊和焊瘤等缺陷;
从在上述缺陷的因完全清除,清除厚度不得超过公称壁厚的负偏差值,清理处的实际壁厚不得小于计算最小值。
d)对合金钢阀壳逐件进行光谱分析,光谱检验按DL/T991-2006执行。
e)按20%对阀壳进行表面探伤,至少抽查一件。
5.11高温联箱,根据DL/T438-2009在进入生产现场使用前要进行如下检验:
5.11.1工作温度高于400℃的联箱在安装使用前应做如下检验:
a)检查合格证,进口的还要查看商检合格证明单。
b)联箱上的标记(钢印或漆记)应与该制造商产品标记相符。
c)进行外观质量检验,检查技术参数是否符合设计要求。
表面质量按DL/T438-2009中8.1.2条进行验收。
d)对合金钢制的联箱进行光谱检验,光谱检验按DL/T991-2006执行。
e)联箱环焊缝按10%进行超声波探伤,角焊缝按50%进行表面探伤复查。
f)对合金钢制的联箱,要进行硬度检验,发现硬度异常时,需进行金相组织检验。
g)检查联箱内部的清洁度。
5.11.2联箱筒体、焊缝有下列情况是,应予以返修或判不合格:
a)母材存在裂纹、夹层或无损检验有超标缺陷。
b)焊缝存在裂纹、无损检验有超标缺陷。
e)筒体和管座的壁厚小于最小需要壁厚。
f)筒体和管座型式、规格、材料牌号不匹配。
5.12给水管道及低温联箱,根据DL/T438-2009在进入生产现场使用前要进行如下检验:
a)给水管道材料、使用前检验按5.3中的相关条款执行。
b)低温联箱材料、使用前检验按5.7中的相关条款执行。
4.13汽包在进入生产现场使用前的检验按DL/T438-2009中10.1中的相关条款执行。
5.14汽轮机部件在进入生产现场使用前的检验按DL/T438-2009中12.1中的相关条款执行。
5.15所有监督范围内的高温紧固螺栓,在安装前应进行无损探伤、光谱分析及硬度检查和必要的金相组织抽查,不符合标准要求的螺栓不得进行安装。
5.16发电机部件在进入生产现场使用前的检验按DL/T438-2009中13.1中的相关条款执行。
5.17校核钢管的壁厚和管径要符合相关标准的规定和订货要求。
6焊接质量的监督
6.1凡承担金属监督范围内的锅炉、汽轮机承压管道及部件的焊接,必须是由经过专门培训并按照《焊工技术考核规程》(DL/T679-1999)和《特种设备焊接操作人员考核细则》(TSGZ6002-2010)考核合格,具有相应资格的焊工担任。
对有特殊要求的部件的焊接,焊前要做有针对性的模拟练习,熟悉部件的焊接特性。
6.2凡焊接金属监督范围内的锅炉、汽轮机承压管道及部件,焊前应按DL/T868-2004的规定进行焊接工艺的评定;
焊接材料的选择、焊接工艺、焊后热处理、焊接质量检验及质量评定标准等,按DL/T869-2004和DL/T819-2002执行。
6.3凡焊接金属监督范围内的锅炉、汽轮机承压管道及部件,所有焊接接头要进行100%无损检验。
对接焊接接头采用UT或RT方法检测,角接焊接接头采用MT或PT方法检测,质量验收按照DL/T820-2002、DL/T821-2002和GB/T3323-2005以及JB/T4730-2005标准的规定执行。
各类焊接接头的质量级别见表1。
6.4焊接材料(焊条、焊丝、焊剂、钨棒、氩气、氧气和乙炔)的质量要符合国家有关标准规定的要求,焊条、焊丝等均应有制造厂家的质量合格证;
焊材过期在没有重新送检之前不能使用。
6.5焊接材料应设专库储存,库房的湿度和温度要符合有关要求,
表1各类焊接接头的质量级别
焊接接头类别
检验方法
Ⅰ
Ⅱ
Ⅲ
锅炉范围内
锅炉范围外
射线检验
Ⅱ
Ⅲ
超声波检验
Ⅰ
磁粉检验
渗透检验
:
检查结果不得有裂纹、成排气孔、分层和长度大于1.5mm的线性缺陷显示(长与宽之比大于3的缺陷显示按线性缺陷处理)
防止变质腐蚀。
焊接材料的保管还应符合相关安全技术规定。
6.6外委工程中凡属受监范围内的部件和设备的焊接,应遵循如下原则:
6.6.1承包方要有按照DL/T868-2004规定进行的焊接工艺评定,且评定项目要覆盖所承担的工作范围。
6.6.2承包方要有相应的检验试验能力,或与有能力的检验单位签订技术合同,负责其承担范围内的检验工作。
6.6.3承包方要有符合6.1要求的持有合格证的焊工。
6.6.4所有焊接接头要进行100%无损检验。
具体按6.3规定执行。
6.6.5委托方要及时跟踪检查焊接质量和检验情况,并对焊接与检验技术报告进行监督检查。
6.6.6工程竣工时,承包方要向委托方提供完整的技术报告,并由委托方金属监督专责工程师签字留存。
6.7焊接过程中采用代用材料后,要做好记录,并在相应的图纸上表明,尤其要做好抢修更换管排时材料变更后的用材及焊缝位置。
6.8焊口组对
6.8.1焊口的位置要避开应力集中区,且便于施焊与热处理。
6.8.2除设计规定的冷拉口外,其余焊口禁止强力对口,不允许利用热膨胀法对口。
6.8.3焊件下料和坡口制备采用机械加工的方法,坡口内外20mm内母材无裂纹、重皮毛刺及坡口破损等缺陷。
6.8.4焊件组对要做到内壁齐平,如有错口,其错口值要符合下列要求:
a)对接单面焊的局部错口值不得超过壁厚的10%,且不大于1mm。
b)对接双面焊的局部错口值不得超过壁厚的10%,且不大于3mm。
6.8.5不同厚度焊件对口时,其厚度差按照DL\T869-2004标准4.3.4规定处理。
6.8.6锅炉受热面管子的焊口,其中心线距离管子弯曲起点或联箱外壁或支架边缘至少70mm,同根管子两个对接焊口间的距离不得小于150mm。
6.8.7管子对接焊口,其中心线距离管道弯曲起点不小于管道外径,且不小于100mm(定制弯头除外)。
距支、吊架边缘不小于50mm。
同管道两个对接焊口间的距离不得小于150mm,当管道公称直径大于500mm时,同管道两个对接焊口间的距离不得小于500mm。
6.8.8焊口的局部间隙过大时,应设法修正到规定尺寸,严禁在间隙内加添塞物。
6.9焊接方法和工艺
6.9.1承压管道焊接时,所用的焊接方法采用表2的规定。
6.9.2合金含量较高的耐热钢(Cr含量≥3%或合金总含量>5%,如T/P91钢、不锈钢)管子和管道对接焊接时内壁必须充氩保护。
6.9.3外径大于194mm的管子和锅炉密集管排的对接接头采取二人对称焊。
6.9.4公称直径不小于1000mm的管道或容器的对接接头,采用双面焊,并应采取清根措施。
6.9.5焊接接头有超标缺陷时,采用重新焊接或挖补的方式返修。
但同一位置上的挖补次数不得超过三次,耐热钢不得超过两次,并遵守下列规定:
a)彻底清除缺陷;
b)补焊时要制定具体的补焊措施并按照工艺要求实施;
c)需要进行热处理的焊接接头,返修后重新做热处理。
6.9.6承压管道焊接时,采用的焊接方法如表2的规定。
表2承压管道的焊接方法
部件名称
根部焊接
其它焊道
P≥10MPa,δ≤6mm的锅炉受热面管子
Ws
P≥10MPa,δ>6mm的管子及管道
Ws/Ds
P≥4MPa,t≥450℃的管道
再热蒸汽冷、热段管道及其旁路
Ds
汽轮机、发电机的冷却、润滑系统管道及燃油管道
P<10MPa,δ≤6mm的中低压锅炉受热面管子
其他管道(推荐)
注:
P-工作压力;
δ-壁厚;
t-工作温度
6.9.7严禁对焊接接头进行加热校正。
6.9.8对口所使用的加载工具,需待整个焊接和热处理完毕后方可卸载。
6.10焊前预热
6.10.1焊前预热加热方法、加热宽度、保温要求、测温要求等按照DL/T819-2002有关规定执行。
6.10.2几种常用钢材施焊的预热温度见表3。
表3常用钢材预热温度
钢种
壁厚(mm)
预热温度(℃)
C≤0.35的碳素钢及部件
≥26
100~200
16Mn、16MnR
≥15
150~200
15CrMo、ZG20CrMo
≥10
150~250
12Cr1MoV
≥6
200~300
12Cr2MoWVTiB、10CrMo910、
250~350
T23
-
P22
P/T91
350~400
ZG20CrMoV
250~300
6.10.3异种钢焊接时,预热温度按焊机性能较差或合金含量较高的一侧选择。
6.10.4接管座与主管焊接时,以主管规定的预热温度为准。
6.10.5承压管道与非承压管道焊接时,预热温度按承压管道选择。
6.10.6在0℃及以下,壁厚不小于6mm的耐热钢管子、管件,预热温度比规定值提高30~50℃。
6.10.7在-10℃及以下,壁厚小于6mm的耐热钢管子和壁厚小于15mm的碳素钢管焊接时要适当预热。
6.11焊后热处理
6.11.1焊后热处理的加热方法、加热宽度、保温要求、测温要求等按照DL/T819-2002有关规定执行。
6.11.2几种常用钢材焊后热处理温度见表4。
表4几种常用钢材焊后热处理温度
热处理温度(℃)
C≤0.35的碳素钢及部件20g、ZG25、16Mn、16MnR
600~650
15CrMo、ZG20CrMo
670~700
12Cr1MoV、ZG20CrMoV、P22
720~750
750~760
WB36(15NiCuMoNb5)、A672B70CL32
590~600
6.11.3对易产生延迟裂纹的钢材,如P/T91钢,焊后要立即进行热处理。
6.11.4下列部件的焊接接头要进行焊后热处理:
a)壁厚大于30mm的碳素钢管道、管件;
b)壁厚大于32mm的碳素钢容器;
c)壁厚大于28mm的普通低合金钢容器(A类Ⅱ级钢);
d)壁厚大于20mm的普通低合金钢容器(A类Ⅲ级钢);
e)耐热钢管子及管件和壁厚大于20mm的普通低合金钢管(6.11.5规定内容除外)。
6.11.5下列部件采用氩弧焊或低氢型焊条,焊前预热和焊后适当缓冷的焊接接头可不进行热处理:
a)壁厚不大于10mm、且直径不大于108mm,材料为15CrMo、12Cr2Mo(P22)的管子。
b)壁厚不大于8mm、且直径不大于108mm,材料为12Cr1MoV的管子。
c)壁厚不大于6mm、且直径不大于63mm,材料12Cr2MoWVTiB的管子。
d)奥氏体不锈钢的管子,采用奥氏体材料焊接的。
6.11.6焊接材料的选用
a)焊接材料应根据钢材的化学成分、力学性能、使用工况条件和焊接工艺的结果选用。
b)同种钢材焊接时,应选用焊接材料熔敷金属的化学成分、力学性能应与母材相当。
c)异种钢材焊接时,采用低匹配原则。
异种钢焊接材料的选用按DL/T752-2010执行。
6.12焊缝无损检验的时机
6.12.1被检验的部位温度不大于50℃.
6.12.2需要热处理的部件,在热处理完毕后再检验。
6.12.3对延迟裂纹敏感的材料,如T/P91等,在热处理完毕24小时后再做检验。
6.12.4锻件的检测安排在热处理后,孔、台等结构机加工前进行。
6.12.5标准抗拉强度大于540Mpa钢材制造的容器,应在焊接结束36小时后进行检测操作。
7机组服役期间的金属监督检验
7.1在役机组金属技术监督重点项目见附表D。
7.2主蒸汽、再热蒸汽管道及导汽管在服役过程中的金属监督
7.2.1机组第一次A级检修或B级检修,按10%对直管段和焊缝进行外观质量、硬度、金相检验、壁厚检验和无损探伤,至10万小时完成100%检验。
7.2.2直管段和焊缝外观检查不允许存在裂纹、严重划痕、重皮和腐蚀的缺陷。
7.2.3焊缝的无损探伤抽查根据安装检验记录选取,对于缺陷较严重的焊缝,每次A级检修或B级检修都要复查。
7.2.4工作温度大于450℃,运行时间较长或受力复杂的碳钢、钼钢制蒸汽管道,重点检验石墨化和珠光体球化。
碳钢的石墨化和珠光体球化评级按DL/T786-2001和DL/T674-1999执行,钼钢的石墨化和珠光体球化评级可参照DL/T786-2001和DL/T674-1999执行。
7.2.5工作温度大于450℃,运行时间