氨法脱硫装置经验Word下载.doc
《氨法脱硫装置经验Word下载.doc》由会员分享,可在线阅读,更多相关《氨法脱硫装置经验Word下载.doc(7页珍藏版)》请在冰点文库上搜索。
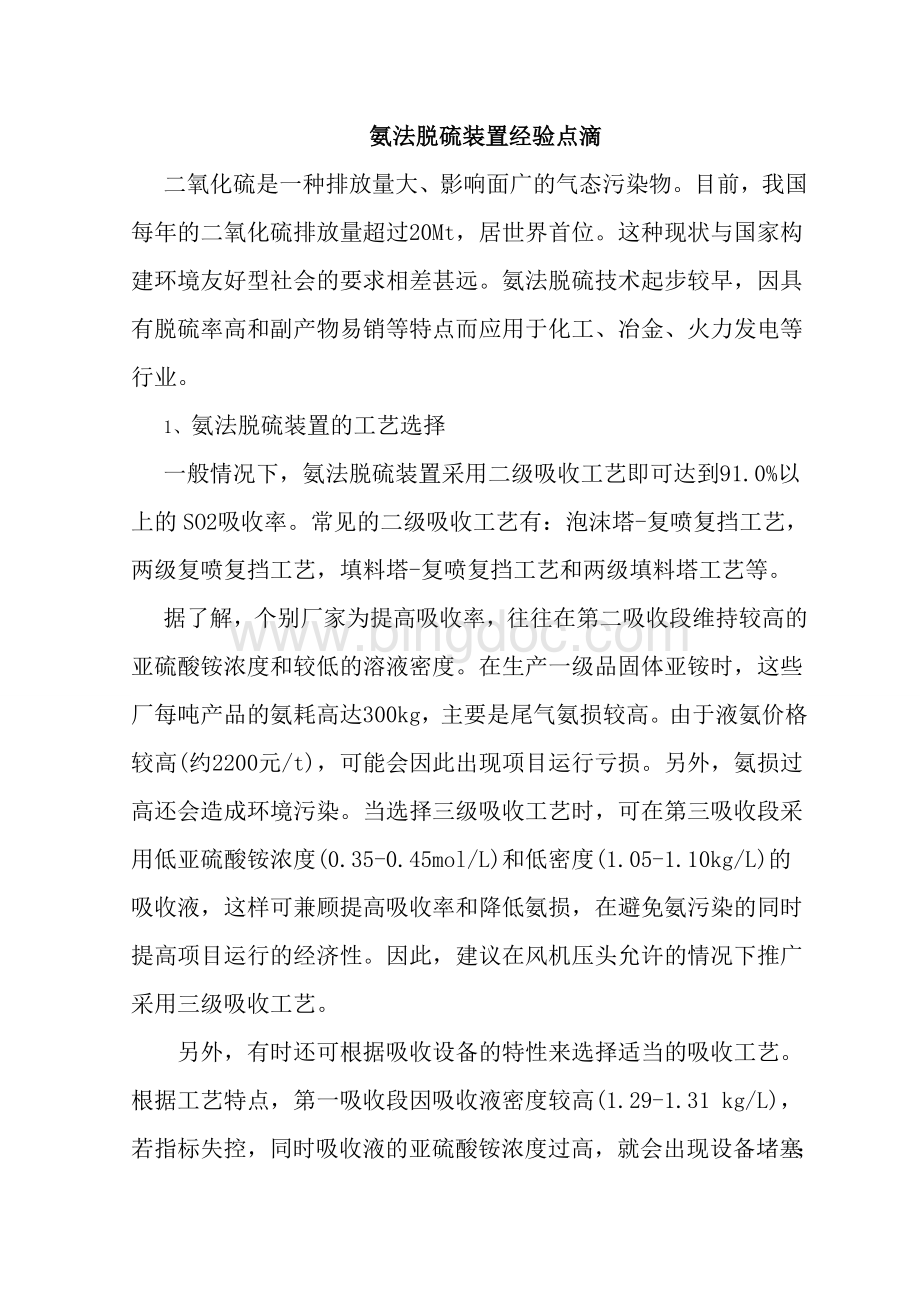
据了解,个别厂家为提高吸收率,往往在第二吸收段维持较高的亚硫酸铵浓度和较低的溶液密度。
在生产一级品固体亚铵时,这些厂每吨产品的氨耗高达300kg,主要是尾气氨损较高。
由于液氨价格较高(约2200元/t),可能会因此出现项目运行亏损。
另外,氨损过高还会造成环境污染。
当选择三级吸收工艺时,可在第三吸收段采用低亚硫酸铵浓度(0.35-0.45mol/L)和低密度(1.05-1.10kg/L)的吸收液,这样可兼顾提高吸收率和降低氨损,在避免氨污染的同时提高项目运行的经济性。
因此,建议在风机压头允许的情况下推广采用三级吸收工艺。
另外,有时还可根据吸收设备的特性来选择适当的吸收工艺。
根据工艺特点,第一吸收段因吸收液密度较高(1.29-1.31kg/L),若指标失控,同时吸收液的亚硫酸铵浓度过高,就会出现设备堵塞;
而第二、三吸收段的吸收液密度较低,吸收设备不易堵塞。
因此,设计时可将不易发生堵塞的管道式复喷用作第一级吸收设备,而将易发生堵塞的泡沫塔用作第二或第三级吸收设备,例如可将泡沫塔一两级复喷复挡工艺变成复喷复挡-泡沫塔-复喷复挡工艺等。
2、氨法脱硫装置的设备选型
氨法脱硫装置常见的吸收设备有泡沫塔、填料塔、管道式复喷等,个别脱硫工艺也有使用文丘里做吸收设备的。
泡沫塔具有吸收液氧化率低、吸收效率高、投资相对较省的优点,加之泡沫塔一、二回收段呈立体布置、共用塔体而占地面积小,尤其适合一些场地受限的厂家使用;
其缺点是当吸收液工艺指标失控时易发生堵塞。
一般认为,填料塔是易堵塞、投资高、吸收液易氧化、维修工作量较大的吸收设备。
但据了解,一些厂的填料塔采用1.8m/g的高操作气速和三级回收工艺,吸收率高达99.0%,并未出现明显的吸收液氧化和设备堵塞现象。
管道式复喷吸收器具有结构简单、设备不易堵塞、气体压降低、投资省、对气量波动适应性强和可根据需要设置喷嘴排数的优点,其缺点仅是需配用复挡,占地面积较大,在场地面积允许时,可优先使用。
总之,吸收设备的选型应结合实际,因地制宜。
为避免腐蚀,吸收工序的吸收液循环槽多选用硬PVC材料或FRP材料制作。
若采用液氨做氨源,在向吸收液中通氨的过程中,循环槽易受到冲击、产生振动而损坏。
因此建议,当选用硬PVC材料或FRP材料制作吸收液循环槽时,加氨管离循环槽侧壁的距离应不小于500mm;
另外加氨管的出口不应垂直对着槽底,而应弯向循环槽中心,加氨管出口距槽底的距离应不小于350mm。
当然,若采用碳钢、铝等金属材料制作循环槽则效果更佳。
为减少吸收循环液中氨、二氧化硫等有害气体的外逸,循环槽多设有顶盖。
但加装顶盖后槽内液面高度不易观察和控制。
笔者在工程实践中,通过自制浮标来解决这一问题。
取一根Φ160mm、长250mm的硬PVC管段,两端用硬PVC板焊死做浮子,在浮子上端的端盖中心垂直焊一根Φ50mm的硬PVC管做标尺;
然后在槽内垂直安装一根Φ220mm硬PVC管贯穿全槽,并在该管底部的管壁上开孔,作为浮标的限位筒;
最后将浮标安装在限位筒内。
这种浮标制作简单,效果良好。
选用液下泵做吸收液循环泵,可有效避免卧式泵的漏液缺陷。
吸收液循环泵的出口管道建议选用碳钢材质。
国内某亚硫酸铵生产装置,在新装置开车过程中,因设计缺陷吸收液循环泵出口聚丙烯管道数次被“打爆”。
采取以下措施解决了问题:
a.原设计中聚丙烯管段的对接处仅用焊条满焊,强度不够。
新方案中除聚丙烯管段的对接处仍满焊外,在焊口外用直径大一个等级的管段打包箍,包箍两端焊死,用以补强。
b.在循环泵出口的聚丙烯管道上每隔2m管长安装一个管夹,用以固定管道,以解决泵运行中可能出现的管道振动。
c.启动泵前全关出口阀,待电机运行正常后缓慢打开泵的出口阀至额定开度,以避免出现“水锤”现象。
当然,若吸收液循环泵出口管道选用碳钢或铸铁等金属材料,上述问题可不予考虑。
不同来源的烟气具有不同的组成,腐蚀情况也会有差别。
为稳妥起见,在选用金属材料制作吸收设备前,应取类似的吸收液作为介质,模拟生产工况进行挂片试验。
吸收液工艺指标的选取
第一吸收段因产品由此产出而称之为“产品段”;
第二吸收段的主要作用是为了提高SO2吸收率,因此被称为“除害段”;
第三吸收段的作用除进一步提高SO:
吸收率外,还可解决尾气的氨损问题,因此可称之为“除氨段”。
而根据最终产品的不同,第一吸收段的工艺指标有一定的差异。
若最终产品为固体亚硫酸铵,则第一吸收段吸收液工艺指标的选取,在兼顾吸收率的同时,应着重考虑如何获得粗大的一水亚硫酸铵结晶。
若最终产品为高浓度亚硫酸氢铵溶液,则应使第一吸收段的吸收液维持较低的亚硫酸铵浓度和较高的溶液密度。
如国内某亚硫酸铵生产装置,第一吸收段吸收液的亚硫酸铵浓度为0.3-0.5mol/L,溶液密度为1.32-1.34kg/L,S/C值为0.93。
因吸收液的亚硫酸铵浓度太低,溶液密度太高,不利于溶液在中和结晶槽析出粗大的一水亚硫酸铵结晶,故该厂很长时间未生产出固体亚硫酸铵产品。
采纳笔者意见后,该厂将第一吸收段吸收液的亚硫酸铵浓度调整为0.8-1.1mol/L,溶液密度调整为1.29-1.31kg/L,S/C值调整为0.85-0.89,结果生产出结晶粗大的一水亚硫酸铵产品。
所推荐的固体亚硫酸铵生产装置的吸收液指标如下:
第一吸收段:
吸收液的亚硫酸铵浓度0.8-1.1mol/L,溶液密度1.29-1.31kg/L,S/C值为0.85-0.89;
第二吸收段:
吸收液的亚硫酸铵浓度1.1-1.3mol/L,溶液密度1.18-1.22kg/L,S/C值为0.74-0.80;
第三吸收段:
吸收液的亚硫酸铵浓度0.35-0.45mol/L,溶液密度1.05-1.10kg/L,S/C值为0.69-0.86。
所推荐的高浓度液体亚硫酸氢铵生产装置的吸收液指标如下:
第一吸收段:
吸收液的亚硫酸铵浓度0.5-0.7moL/L,溶液密度1.32-1.35kg/L,S/C值为0.92-0.95;
第二、三吸收段吸收液的组成可大致与生产固体亚硫酸铵时相同。
4、固体亚硫酸铵生产装置的设备布置
固体亚硫酸铵生产装置的中和、离心分离、产品包装部分可立体布置,即将亚硫酸氢铵溶液的中和结晶槽布置在三楼,中和结晶槽旁高位设置成品溶液储槽,中和后的亚硫酸铵溶液经二楼的离心机分离,分离出的固体亚硫酸铵在一楼进行产品包装。
离心机滤液进入滤液中间储槽后,因温度降低会有结晶析出。
个别厂由于吸收工序距中和结晶岗位距离太远,从滤液储槽向吸收工序输送滤液的管道常因结晶附着、沉积而堵塞。
为此笔者建议,固体亚硫酸铵生产装置的吸收、中和、离心分离、产品包装等部分尽量集中布置。
离心机的滤液中间储槽若能设置低速搅拌器效果会更佳。
5、氨法脱硫的氨源和产品选择
氨法脱硫装置的氨源有液氨、碳酸氢铵和氨水等。
氨源选择应认真考虑经济因素。
如我国北方地区液氨资源充沛,液氨价格相对较低,氨法脱硫选择液氨作氨源或许可以;
而在南方因液氨价格太高,以农用碳酸氢铵作氨源则较经济。
据了解,我国南方一些氨法脱硫装置以固体碳酸氢铵作氨源,以经济价值更高的硫酸铵作产品,获得了较好的经济效益。
但用碳酸氢铵作氨源生产固体亚硫酸铵时,存在着产品晶粒较差和难以达到一级品的缺点,故建议新设计的固体亚硫酸铵装置用碳酸氢铵作氨源时应慎重考虑这一因素!
在产品选择上,若原料为矿制酸尾气,生产亚硫酸铵是恰当的。
笔者发现,冶炼烟气制酸,特别是采用氧气或富氧熔炼工艺的烟气制酸,因尾气中氧含量偏高及铜、铅、锌等金属氧化物粉尘的作用,生产固体亚硫酸铵时,常常会出现产品中硫酸铵成分超标现象,并可能影响SO2的吸收率。
因此冶炼烟气制酸采用氨法处理尾气的,最好不要选择固体亚硫酸铵作产品!
部分火电厂曾向有固体亚硫酸铵产品的硫酸厂免费提供亚铵溶液,但因硫酸铵含量高而被拒绝使用。
若提供给硫酸铵厂使用或自己生产硫酸铵,可能就是双赢之举。
如果烟气中SO2浓度偏低,应避免选择高浓度亚硫酸氢铵溶液作产品。
据报道,当烟气中Φ(SO2)<
0.6%时,就难以产出合格的高浓度亚硫酸氢铵溶液。