10000立罐施工方案Word文档格式.docx
《10000立罐施工方案Word文档格式.docx》由会员分享,可在线阅读,更多相关《10000立罐施工方案Word文档格式.docx(29页珍藏版)》请在冰点文库上搜索。
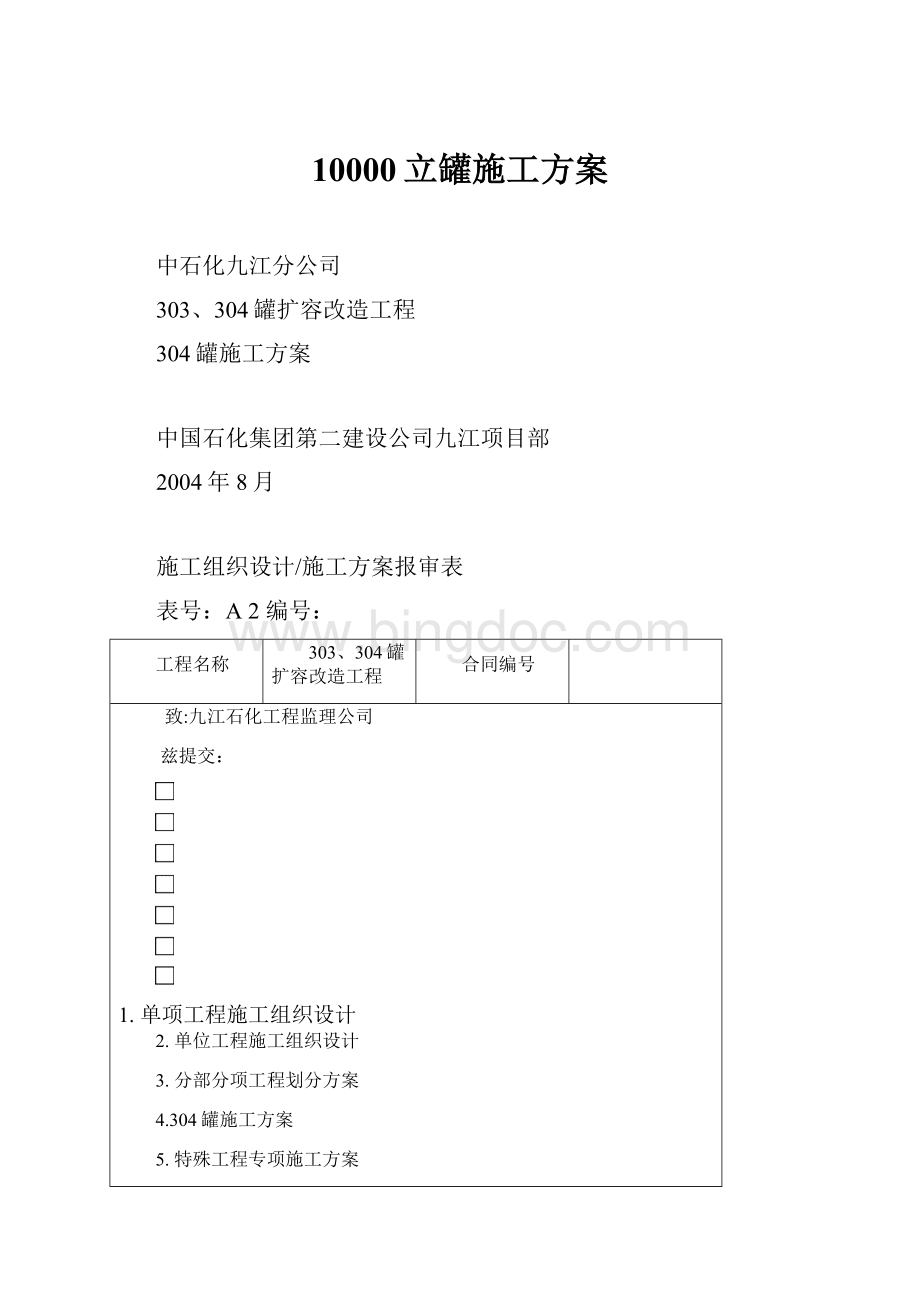
“十五”建设办公室
审批栏
部门
审批意见
技术质量办公室
物资供应办公室
经营财务办公室
施工管理办公室
综合管理办公室
项目总工程师
编制:
审核:
目录
一、工程概述………………………………………………………………………………………………………………..1
二、编制依据………………………………………………………………………………………………………………..1
三、主要工程实物量………………………………………………….…………………………………………..1
四、主要施工程序………………………………………………….………………………………………..…..3
五、质量保证措施……………………………………………….………………………….……………..…..13
六、施工安全、环境与健康(HSE)保证措施………………….…………………...…..14
七、施工平面布置图及施工网络计划……….………………………….………..……..…..19
八、主要施工机具及手段用料……….………………………….………..…………..…..…..19
附录一:
304罐扩容改造施工平面布置.………………………….………..……..…....21
附录二:
304罐扩容改造施工网络计划…………………….………..……..………......22
一、工程概述
中国石化股份有限公司九江分公司304罐扩容改造将原5000m3汽油罐拆除,在原位置新建一台10000m3汽油罐。
储罐计算容积11213.6m3,金属重量237.18t,储罐内径为30m,罐壁高度15.864m,总高度19.145m。
罐底中幅板采用搭接,边缘板采用带垫板的对接焊缝;
罐壁由九圈板组成,壁厚分别为δ=14mm、12mm(两圈)、10mm(一圈)、8mm(四圈)。
拆除施工工期为7天,安装施工工期50天、焊接施工工程量大,要求焊工技术精湛、焊接一次合格率高。
施工现场紧邻现有罐区,对动火和用电的安全措施必须到位。
二、编制依据
1、九江分公司提供的《招标文件》及施工合同。
2、304罐扩容改造施工图。
3、中国石化集团第二建设公司QG/SE18.01-1996质量手册和QG/SE18.02-1996《质量体系程序文件》及QG/SE11.01-2001《安全、环境与健康管理手册》
4、中国石化集团第二建设公司《企业管理标准(制度)》。
5、GBJ128-90立式圆筒形钢制焊接油罐施工及验收规范
6、GB50235-97工业金属管道工程施工及验收规范
7、GB50236-1999现场设备、工业管道焊接工程施工及验收规范
8、GB50168-92电气装置安装工程电缆线路施工及验收规范
9、GB50169-92电气装置安装工程接地装置施工及验收规范
10、GB50150-91电气装置安装工程电气设备交接试验标准
11、GBJ93-86工业自动化仪表工程施工及验收规范
12、SH3521-1999石油化工仪表工程施工技术规程
13、SH3022-1999石油化工企业设备与管道涂料防腐蚀技术规范
14、GB50259-94工业金属管道工程质量检验评定标准
三、主要工程实物量
1、罐本体主要实物量
序号
名称
单位
数量
重量(Kg)
1
罐底
Kg
49995
2
罐壁
125915
3
包边角钢
1865
4
罐顶
57115
5
盘梯
1080
6
罐顶平台及栏杆
1085
7
人孔
个
378
8
接管
241.4
9
补强圈
196
10
透光孔
96
11
内浮盘
件
4400
12
罐壁通气孔
270
13
带放水管排污孔
231
2、工艺管线主要实物量
名称
备注
钢管
米
1897
弯头
55
法兰、法兰盖
64
阀门
16
过滤器
套
采样器
自动脱水器
油罐油品调合旋转喷头
量油孔
通气管
空气泡沫产生器
集水器
3、电气、仪表主要实物量:
雷达液位计
台
液位开关
双金属温度计
支
单法兰液位变送器
安全栅
块
电源分配器
法兰闸阀
镀锌水煤气管
442
电线电缆
3780
防腐连接器
只
镀锌扁钢
490
镀锌角钢
根
17
四、主要施工程序
(一)旧罐拆除
旧罐拆除前应在旧罐东西两侧各修一条简易施工道路。
并在旧罐周围垫上片石,片石上再用细石铺平压实,厚度为0.3m。
同时在旧罐的东、北、西三面搭好防火墙,搭设高度与旧罐高度一致,防止气割火星飘到临近的油罐上引起火灾。
拆除时先在罐外沿罐搭一圈脚手架,搭到比罐顶低1.5m的高度。
电气仪表拆完后首先拆除盘梯、罐内浮梯及立柱、顶平台,然后分片拆除罐壁板,分片拆除的罐壁板宽度以方便装车为宜,最宽不超过2m。
罐壁板拆完后分片拆除罐底板。
拆除作业用25吨汽车吊配合。
(二)罐本体施工
材料验收合格后运至预制场进行预制,预制结束后用15吨汽车运至施工现场,由25吨汽车吊配合装卸。
根据现场施工能力尽量加深度,减少现场的安装工作量,提高工作效率。
1、罐底的预制
(1).罐底应按照到货板材的实际情况依据规范的技术要求,并结合施工图纸进行排版,经审核后方可下料。
排版时为补偿焊接收缩及考虑基础坡度,罐底直径放大40mm。
(2).中幅板沿罐底半径方向的最小尺寸不得小于700mm,如果图纸有要求按施工图纸要求施工,中幅板宽度不得小于1000mm,长度不得小于2000mm。
(3).罐底板任意相邻两个接头之间的距离不小于200mm,边缘板接头距底圈壁板纵缝的距离不应小于300mm。
(4).罐底板采用氧-乙半自动切割机切割,边缘板的垫板采用剪板机剪切。
罐底板预制检查合格后应标明编号、规格以便于安装使用。
(5).罐底板运至施工现场前涂刷沥青防腐漆。
(6).罐底板的运输和保管过程中应采取防变形措施。
2、罐壁板的预制
(1).壁板应按照到货板材的实际情况依据规范的技术要求并结合施工图纸及罐底排版图综合考虑进行排版,下料按中径计算。
(2).罐壁板的宽度应大于1000mm,长度应大于2000mm。
(3).上下两圈壁板纵缝距离不小于500mm。
(4).罐壁板开孔接管或接管补强圈边缘与罐壁纵缝距离不小于250mm,与罐壁板环缝之间的距离不小于100mm。
(5).按排版图控制每圈的集合尺寸,每圈预留一张封口板,根据现场实际情况确定其尺寸,其余每张壁板下料长度按下列公式计算:
π*(内径+壁厚)/整圈板的张数-对口间隙+焊接收缩量
(6).壁板的切割(包括坡口加工)用氧-乙炔半自动切割机切割,壁板的几何尺寸、坡口角度等必须符合施工图纸及规范的要求。
(7).磨好的坡口及钝边,运至石化总厂机修厂用滚板机滚弧,滚制好的壁板应立置在平台上用直线样板检查平直度,其间隙不得大于1mm,用弧形样板检查弧度,其间隙不大于1mm,为了防止变形,壁板成型后应放置在专门制作的胎具上及时运至施工现场。
(8).罐壁板加工后的偏差应符合下表:
测量部位
环缝对接
板长AB(CD)≥10m
板长AB(CD)<10m
宽度AC、BD、EF
±
1.5
长度AB、CD
对角线之差
AD、BC
≤3
≤2
直线度
AC、BD
≤1
AB、CD
3、罐顶板的预制
(1).罐顶板按照到货板材的实际情况依据规范的技术要求并结合施工图纸及壁板排版图综合考虑进行排版。
(2).依据施工图给定的尺寸及曲率制作胎具。
(3).依据排版图尺寸分瓣进行下料。
(4).将切割、拼好的罐顶板放置在胎具上,与事先煨好弧度的筋板组焊成一体。
(5).罐顶板预制后同样应放置在制作的胎具上运输及保管。
4、包边角钢及其他构件的预制.
(1).包边角钢及根据实际情况煨制成型后的弧度和翘曲度应合规范要求。
(2).热煨制成的构件其减薄量不应超过1mm,并且不得有过烧变质现象。
(3).盘梯预制成段运至安装现场,其他附件均预制成型后运至现场安装。
所需检查样板一览表:
检查样板名称
罐顶板样板
罐壁直线样板
罐壁弧样板
焊缝角变形样板
规格
2m
1m
5、液压顶升装置的准备
(1).选用SQD-160-100F型松卡式液压千斤顶。
(2).逐台检查液压千斤顶、阀门、接头,且以1.5倍工作压力试压,保持10分钟不漏为合格。
(3).检查油路主、进回油管及各支路油管,阀门及配件确保内部清洁无杂物。
主油路采用无缝钢管、支路采用高压软管。
(4).全面检查液压控制箱、实验操作平台各电器按钮,检查各元件,确保操作正常,保持油箱、油液清洁。
(5).检查提升架的滑板、滑动是否正常,在导轨上抹润滑油。
(6).制作胀圈,准备足够的卡具、销子,胀圈采用双背槽钢[20制作。
(7).制作液压提升架的垫板,垫板规格为700×
500×
18。
(8).确定液压千斤顶使用的数量。
计算公式:
N≥Pmax/ξ*G
式中:
N—为千斤顶数量
Pmax—为提升最大总负荷。
ξ—为液压千斤顶折减系数,取ξ=0.6~0.8
G—为液压千斤顶的额定起重量G=160KN
PMaX=K(P1+P2+¨
¨
+P顶+P附)
式中:
K=1.1
(P1+P2+¨
+P顶+P附)—罐壁板、罐顶及附件的重量(单位:
N)
10000m3罐PmaX=212952kg=2088349N
N≥PMaX/ξ*G=2088349/0.7*160000=18.646
取N=20
6、基础验收
(1).储罐安装前,必须按土建基础设计和GBJ128-90《立式圆筒形钢制焊接油罐施工及验收规范》的规定对基础表面尺寸进行检查。
(2).储罐基础的表面尺寸、符合下列规定:
基础中心标高允许边查为±
20m;
对支撑罐壁的基础表面高差:
有环梁时,每10米弧长内任意两点的高差不得大于6mm,整个圆周长度内任意两点的高差不得大于12mm,无环梁时,每3米弧长任意两点的高差不得大于6mm,整个圆周长内任意两点的高差不得大于12mm。
(3).沥青沙层表面应平整密实,无突出的隆起,凹陷及贯穿裂纹。
沥青砂表面凹凸度检查时,以基础中心为圆心,以不同直径作同心圆,将各圆周分成若干等分,在等分点测量沥青砂层的标高.同一圆周上的测点,其测量标高与计算标高之差不得大于12mm。
同心圆的直径和各圆周上最少测点数应符合下表:
同心圆直径(mm)
测量点数
D/4=7500
8(均布)
D/2=15000
16(均布)
3D/4=22500
24(均布)
(4).验收合格并办理中交手续后方可进行罐底的铺设。
7、罐底施工
(1).罐底铺设前,钢板需进行除锈并露出金属光泽后,在底面刷WF120环氧煤沥青防腐漆两道,每块底板边缘50mm内不刷.
(2).以基准中心分别划出0°
~180°
90°
~270°
十字基准线,根据排版图分别再划出中幅板及边缘板安装位置线,边缘板安装位置圆周线要计入边缘板对接缝的收缩量,以及铺设边缘板。
(3).中幅板铺设按排版图从中心向四周铺设,本罐底中幅板采用搭接。
(4).边缘板组对采用带垫板的对接缝焊接,对接缝应完全焊透,垫板应与对接的两块底板贴紧,其间隙不得大于1mm.
(5).罐底采用手工电弧焊.罐底的组对依据罐底的焊接顺序进行.
(6).罐底焊完后所有焊缝进行100%真空试漏检查,以不泄露为合格.
8、罐体安装
(1).划线
在边缘板上划出罐壁板的安装基准圆线,基淮圆计公式为:
R=r+N×
a/2π
R:
壁板基准圆内半径单位:
mm
r:
罐壁设计半径单位:
a:
立缝的焊接收缩量(1~1.8mm)
N:
壁板数量
π:
圆周率
在基准圆内侧50mm位置划线一个检查圆,检查直径为D=2R-100mm。
在基准圆线上安装[14垫块,每个垫块长约150mm,每两个垫块之间的距离为500mm左右,在每个垫块上也划出基准线,在每个垫块基准圆线侧点焊一个δ=670×
50的垫块。
在每两个垫块之间罐底边缘板的基准圆内侧点焊δ=8100×
80挡板。
(2).顶圈壁板的安装
按图纸和罐壁排版图从一固定点开始依次围顶圈壁板,相邻两块壁板间用组卡具固定,每道纵缝用2个组对卡具,对卡具的“豆腐块”宜在围板之前点焊好。
点焊壁板的纵缝间隙以2mm为准,检查壁板的间隙错边量,角变形,垂直度,椭圆度等符合要求后,在纵缝的内侧安装3块圆弧板,以防止焊接角变形,外侧点焊防波浪变形竖背杠,然后交付电焊焊接。
点焊壁板的预留缝之前,应用盘尺测量罐壁上、下口的周长,保持严格相等,误差不得大于2mm。
壁板纵缝焊完以后应对壁板进行找圆及找正。
保证罐壁凹凸度、垂直度、上下口水平度等符合要求,凹凸度≤13mm,垂直度≤3mm,相邻两壁板的上下口水平度≤2mm,任意两点上下口水平度≤6mm。
(3).罐顶包边角钢安装
将预制好的罐顶包边角钢分段安装在第一圈罐壁上,安装时注意包边角钢与罐壁的接合弧度,弧度要求同罐壁。
(4).胀圈及液压提升架安装
a.将液压提升架吊入罐内,以罐内壁周长均分设置,液压提升架尽量靠近罐壁以减少提升时的弯矩。
b.液压提升架应设置在罐底板平实的地方,不得设置在凹凸处,尤其不得设置在罐底基础的开孔处。
液压提升架亦应错开焊道,以不影响射线探伤为基准。
c.将液压提升架底部加垫板,用铁水平尺或线坠测量提升架两个方向的垂直度,并与罐底板固定点焊,注意垫板与罐底板、垫板与提升架座均应贴实。
d.将液压提升架顶部与罐底用φ45×
3.5钢管焊死,并调整提升架的滚轮与罐壁贴实,将滚轮架的紧固螺钉锁死。
e.在罐壁板距底边缘50mm左右处,安装胀圈。
胀圈与罐壁用龙门卡具及销子,防滑挡板等连接。
胀圈的安装应用水平管找平,以防止提升时罐体的偏斜。
f.龙门卡具应在距提升架中心750mm的两侧各设置一个,其它每隔2000mm设置一个。
g.胀圈用20t或10t螺旋千斤顶胀实,胀圈千斤顶接头的两侧各用一个龙门卡具与罐壁连接,并用销子与罐壁打实。
h.将液压千斤顶的控制箱设置在罐外排空管处。
I.将SQD-160-100S型千斤顶安装在提升管架上。
j.安装液压千斤顶的进、回主油管及各支路油管,环形主油管用φ25×
4无缝钢管,支路油管用高压软管。
油管内部在安装之前彻底清洗,不许有杂物。
油路的布置应均匀,压力一致,保证罐体提升尽量同步。
k.由专业人员对液压提升装置全面检查,确保安全无误方可提升。
l为了使提升的托架与胀圈底部良好接触,首先进行预提升—液压提升的低压调整,步骤如下:
第一步:
松开液压千斤顶的上、下头的松卡螺母,使上、下卡头均处于锁紧状态(卡头的滑块下降至底表示卡头锁紧)。
第二步:
首先充油排气。
以提升载荷的1/10运行千斤顶,控制箱进油并保持3~5分钟,确保每个提升托架受力一致。
(在不足以提升罐体的前提下,可以增加一点进油压力,以保证托架与胀圈的底部的贴实)
第三步:
全面检查提升架的托架与胀圈接触情况,全部予紧后,进行试运转,待各部分正常后,准备正常提升,提升前先将罐的液压千斤顶油缸复位。
第四步:
如果有个别提升架的托架与胀圈不接触,可以进行单独调整,即关闭其它千斤顶的进、油阀,只给接触不良的千斤顶进油、使之预紧。
m.罐体的正常提升
打开千斤顶控制的开关,打到充油(进油)有位置,将压力表调到可以提升罐体的位置,工作油压力必须稳定在正常值内,不得随意提高,进油和回油的时间必须充分,以确保液压千斤顶的行程。
提升的第一行程应缓慢到位后用10~30分钟时间检查罐壁提升架、托架、胀圈、液压升斤顶、油路无异常后继续提升。
反复操作控制箱的进油与回油,使罐体一个行程一个行程的提高。
各个千斤顶的提升高差应控制在50mm以内,且相邻的千斤顶高度应相近,如需调整,一次调整的液压千斤顶的数目不应超过总数的1/3。
调整时关闭偏高的液压千斤顶的进、回油阀,待高度一致再打开这阀门,继续同步提升。
提升高度距外圈壁板上口100mm时应缓慢提升,检查提升的水平度,继续提升至高出外圈壁板上30~50mm,此时暂不回油,将所有阀门关闭。
松开下卡头使之处于自由状态—即使下卡头的松卡螺母上旋,卡块上长直至不动为止。
提升千斤顶的回落可以分组进行,方法是派人分别站在每组千斤顶的下边,统一打开阀门,使有罐重力的作用下自由回落,回落的快慢可以通过针形阀的流量控制。
如果遇到靠罐的重力的作用不能使千斤顶回落的情况,可以以1~2MPa的油压回油强制回落.
点焊环缝—焊接预留收缩缝—焊接环缝,等焊缝凉透回落胀圈,对罐壁找圆。
(5).第二圈壁板的安装、满堂红脚手架搭设。
(6).罐顶安装
(7).罐顶劳动保护安装
(8).其它各圈罐壁的安装
在已施工完的罐体外侧围下一圈壁板,重复各操作步骤,直至最后一圈壁板。
最后一圈壁板施工完毕应提升150~200mm,拆除槽钢[14垫块,并重新在罐底边缘板的安装圆线上点焊挡板。
每圈壁板提升前应松开收口的两导链。
每圈壁板组装好以后均需检查上、下周长及垂直度并作好记录。
每圈壁板提升前,应完成罐壁的除锈防腐工作,避免过多的高空作业
每一圈罐壁提升前,应将内、外侧的焊疤打磨干净。
9、内浮盘安装
罐体施工完后进行总体试验,合格后进行罐内壁喷砂防腐,最后开始安装内浮盘,内浮盘分块到货,采用固定脚,罐内组装时应严格控制组装尺寸,组装后用弧形样板边缘板的凹凸变形,最大局部间隙不大于5mm。
在内浮盘上,量油孔正下方开一个DN150的孔,供采油用。
10、附件施工
顶圈壁板的接管可在罐顶施工完毕且罐体提升以前开孔施工。
开孔时要求先定位划线,由有关人员检查合格后方可施工。
11、盘梯、平台栏杆施工
盘梯的三角架可以在罐壁的提升过程中安装,盘梯在罐体施工完毕分段吊装。
罐顶平台、栏杆可以在罐顶施工完后进行安装。
(三)焊接
1、罐底的焊接方法
罐底边缘板采用加垫板的对接焊缝,中幅板采用搭接焊缝。
焊接采用手工电弧焊。
罐底焊接前垫板的临时固定点必须铲开,以防止焊接变形。
对于通长焊接可适当采用加长直背杠的方法予以固定,控制焊接成型。
中幅板的焊接原则是先焊短缝,后焊长缝。
焊接顺序由中心向外,长缝的焊接采用分段退焊,分段长度为500~600mm。
罐底焊接完毕后应将垫板伸出底板部分切除。
边缘板首先焊接靠外缘300mm部位的焊缝,等罐底与罐壁连接的角焊缝焊完后且边缘板与中幅板之间的收缩缝焊接前,再焊接剩余边缘板对接焊缝,为了防止变形,在每条对接缝的垫板下加高30mm左右,防止焊接下凹角变形.
罐底与罐壁连接的角焊缝焊接,应等全部壁板焊接完后,由数名焊工从内外同时沿一方向进行分段焊接。
初层的焊道,采用分段退步焊法。
罐底的角焊缝应焊两遍成型,不允许一遍成型。
2、罐壁板的焊接方法
罐壁板的焊接采用手工电弧焊,总的焊接顺序为:
先焊接相邻两圈壁板的立缝,后组对焊接其间的环缝。
罐壁立缝焊接时应由多名焊工沿圆周均匀分布,同时、同向施焊。
焊接顺序是先焊外口,后焊里口。
封底焊接时应分段退焊,退步长度为800mm。
罐壁环缝由多名焊工沿圆周均匀分布,同时同向施焊,起弧点和收弧点应错开20mm以上。
先焊外口,后焊里口。
焊缝背面清根均采用手工碳弧气刨。
3、焊缝检测
边缘板之间每条对接焊缝外端300mm范围内应进行射线探伤检查,检查结果不低于JB4730-94的Ⅲ级。
罐底焊缝应在外观检查合格后采用真空箱法进行严密性试验,试验负压值不得低于0.053Mpa,无渗漏为合格。
底圈罐壁的每条纵焊缝应取2段300mm进行检查,其中一段应靠近底板。
全部罐壁板纵焊缝每位焊工的每种板厚,在最初3m内取300mm射线检查,以后每30m焊缝及其尾数内任取300mm射线检查;
全部罐壁板环焊缝每位焊工的每种板厚,在最初3m内取300mm射线检查,以后每60m焊缝及其尾数内任取300mm射线检查。
探伤结果不得低于JB4730-94的Ⅲ级。
未进行无损探伤的罐壁板其纵、环焊缝均应进行煤油试漏。
4、焊缝修补
缺陷深度超过规范值时进行补焊。
焊缝表面缺陷超过规范要求时,进行打磨或补焊。
焊缝内部有超标缺陷时,进行返修,并按原规定进行探伤检查,达到合格标准。
焊接的修补,严格按焊接工艺进行。
同一部位的返修次数,不宜超过二次,当超过二次时,需经过技术负责人批准。
(四)、充水实验
充水前所有附件及其它与罐体焊接的构件应全部完工,所有焊缝不得涂刷油漆。
水质要求清洁透明,不应有异味,水的PH值在6~8.3之间,水温应高于5℃。
充水实验按GBJ128-90的要求做好有关检查及观测,基础沉降的观测应由专人检查并负责出检查报告。
内浮盘安装完毕后充水做升降试验,检查其升降是否灵活。
充水过程中如有异常应立即停止充水,如渗漏则放水至低于渗漏处300mm进行修补,并应重新充水直至合格。
正压试验在充水至设计高度后封闭开孔,用U形玻璃管液面计测量正压值,用充水方法升压,升至规定压力2200Pa(合水柱224mm)后保持规定时间并在罐顶所有焊缝涂刷肥皂水试漏。
不渗漏、无异常现象、不降压为合格。
合格后卸压。
负压试验采用放水方法进行,测量方法同上。
降至规定压力1300Pa(合水柱