拨杆零件的加工工艺设计钻Φ12的钻床夹具.docx
《拨杆零件的加工工艺设计钻Φ12的钻床夹具.docx》由会员分享,可在线阅读,更多相关《拨杆零件的加工工艺设计钻Φ12的钻床夹具.docx(24页珍藏版)》请在冰点文库上搜索。
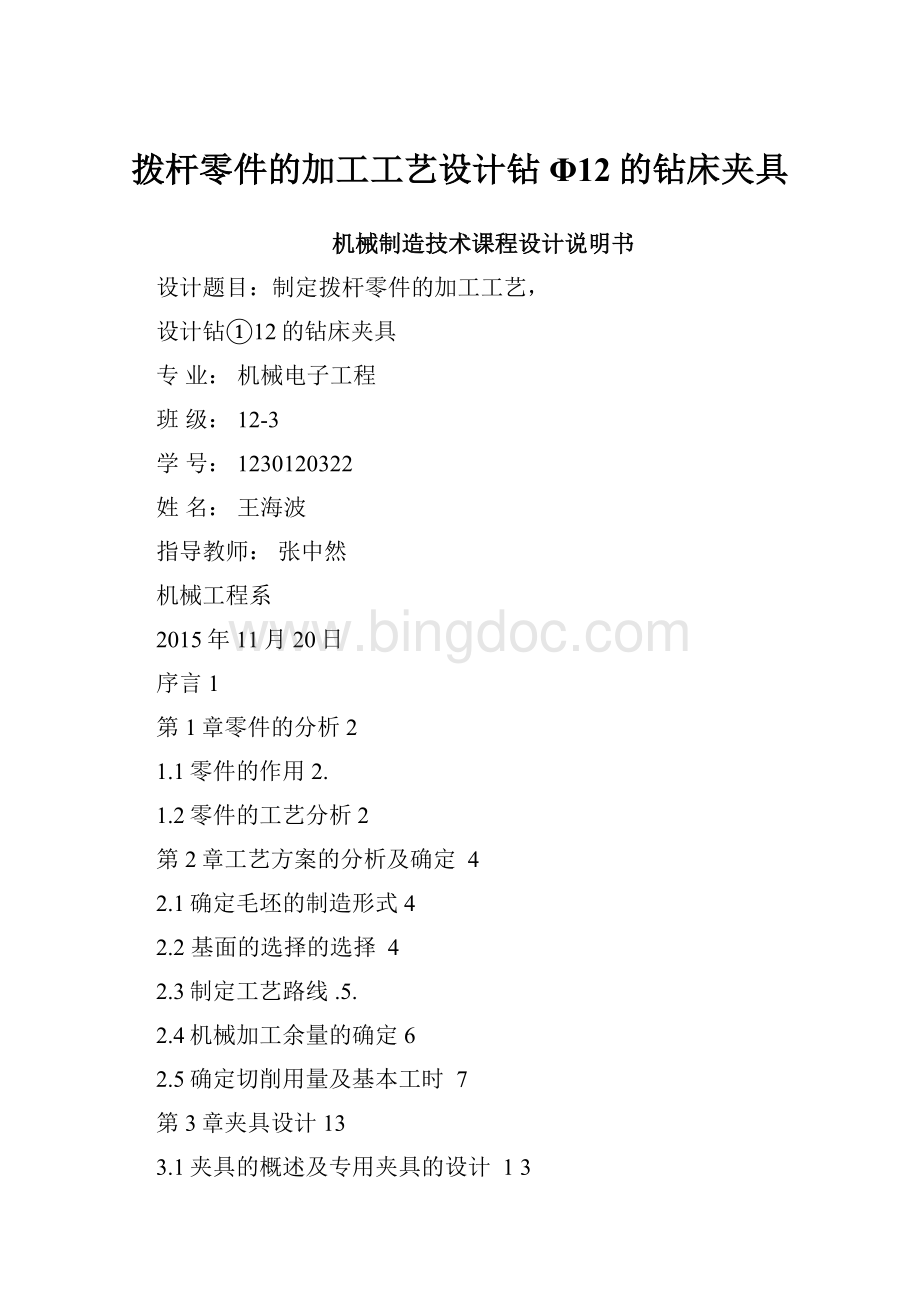
拨杆零件的加工工艺设计钻Φ12的钻床夹具
机械制造技术课程设计说明书
设计题目:
制定拨杆零件的加工工艺,
设计钻①12的钻床夹具
专业:
机械电子工程
班级:
12-3
学号:
1230120322
姓名:
王海波
指导教师:
张中然
机械工程系
2015年11月20日
序言1
第1章零件的分析2
1.1零件的作用2.
1.2零件的工艺分析2
第2章工艺方案的分析及确定4
2.1确定毛坯的制造形式4
2.2基面的选择的选择4
2.3制定工艺路线.5.
2.4机械加工余量的确定6
2.5确定切削用量及基本工时7
第3章夹具设计13
3.1夹具的概述及专用夹具的设计13
3.2确定夹具的方案14
3.3工件的夹紧16
3.4夹紧力三要素的确定16
3.5夹紧装置17
3.6导向装置的确定1.8
3.7定位误差的分析1.8
3.8确定钻套的尺寸与公差带19
3.9内六角螺钉的抗拉强度校核20
3.10夹具操作的简要说明21
总结22
致谢23
参考文献24
序言
机械制造业是制造具有一定形状位置和尺寸的零件和产品,并把它们装备成机械装备的行业。
机械制造业的产品既可以直接供人们使用,也可以为其它行业的生产提供装备,社会上有着各种各样的机械或机械制造业的产品。
我们的生活离不开制造业,因此制造业是国民经济发展的重要行业,是一个国家或地区发展的重要基础及有力支柱。
从某中意义上讲,机械制造水平的高低是衡量一个国家国民经济综合实力和科学技术水平的重要指标。
拨杆的加工工艺规程及其铣尺寸14的夹具设计是在学完了机械制图、机械制造技术基础、机械设计、机械工程材料等进行课程设计之后的下一个教学环节。
正确地解决一个零件在加工中的定位,夹紧以及工艺路线安排,工艺尺寸确定等问题,并设计出专用夹具,保证零件的加工质量。
本次设计也要培养自己的自学与创新能力。
因此本次设计综合性和实践性强、涉及知识面广。
所以在设计中既要注意基本概念、基本理论,又要注意生产实践的需要,只有将各种理论与生产实践相结合,才能很好的完成本次设计。
本次设计水平有限,其中难免有缺点错误,敬请老师们批评指正。
第1章零件的分析
速机构中。
主要用来换挡,使主轴的回转运动按照工作者的要求工作,
从而获得所需要的速度和扭矩的作用。
零件上的φ12孔与操作机构相
连接,通过φ22孔则是用于所控制齿轮所在的轴配合。
通过φ12孔所
受的力拨动φ22孔这端的齿轮变速。
达到所需的作用。
1.2零件的工艺分析
(1)零件图完全表达清楚了此零件的结构特点。
图上尺寸和技术要求都标注齐全、明确、几何元素之间的关系也完全的明确都符合国家标准。
(2)零件技术要求分析主要是对尺寸精度、形状精度、位置精
度、表面粗糙度、及热处理的要求分析。
这些要求都影响零件的质量和使用性能。
这在保证前面的条件的前提下,应满足经济合理性。
此零件的技术要求有φ22孔与φ40的外圆的低端面垂直,φ12孔与φ40外圆的轴线平行,M8×1.5螺纹孔的轴线与φ40外圆的轴线垂直,φ22孔和φ12孔的表面粗糙度分别达到Ra1.6和Ra3.2,φ12孔的端面的表面粗糙度达到Ra6.30其他表面无需加工。
从上面来分析出,φ22H8、φ
12H7孔和两端面采用通用夹具均可加工。
M8×1.5采用设计的专用夹
具进行加工。
第2章工艺方案的分析及确定
2.1确定毛坯的制造形式
毛坯的确定包括确定毛坯的种类和制造方法两个方面。
毛坯的种类选择铸件。
考虑到零件在机床运行过程中所受的冲击不大,零件的材料选择HT200。
铸件选择砂型铸造毛坯。
2.2基面的选择的选择
基面的选择是工艺规程设计中的重要工作之一。
基面选择的合理,合理。
可以保证加工质量。
否则就会使加工工艺过程问题百出,严重的还会造成零件大批报废,使生产无法进行。
1、粗基准选择应当满足以下要求:
(1)粗基准的选择应以加工表面为粗基准。
目的是为了保证加工面与不加工面的相互位置关系精度。
如果工件上表面上有好几个不需加工的表面,则应选择其中与加工表面的相互位置精度要求较高的表面作为粗基准。
以求壁厚均匀、外形对称、少装夹等。
(2)选择加工余量要求均匀的重要表面作为粗基准。
例如:
机床床身导轨面是其余量要求均匀的重要表面。
因而在加工时选择导轨面作为粗基准,加工床身的底面,再以底面作为精基准加工导轨面。
这样就能保证均匀地去掉较少的余量,使表层保留而细致的组织,以增加耐磨性。
(3)应选择加工余量最小的表面作为粗基准。
这样可以保证该面有足够的加工余量。
(4)应尽可能选择平整、光洁、面积足够大的表面作为粗基准,以保证定位准确夹紧可靠。
有浇口、冒口、飞边、毛刺的表面不宜选作
粗基准,必要时需经初加工。
(5)粗基准应避免重复使用,因为粗基准的表面大多数是粗糙不规则的。
多次使用难以保证表面间的位置精度。
基准的选择是工艺规程设计中的重要工作之一,他对零件的生产是非常重要的。
先选取①22孔及其端面作为定位基准。
2、精基准的选择
精基准的选择应满足以下原则:
(1)“基准重合”原则应尽量选择加工表面的设计基准为定位基准,避免基准不重合引起的误差。
(2)“基准统一”原则尽可能在多数工序中采用同一组精基准定位,以保证各表面的位置精度,避免因基准变换产生的误差,简化夹具设计与制造。
(3)“自为基准”原则某些精加工和光整加工工序要求加工余量小而均匀,应选择该加工表面本身为精基准,该表面与其他表面之间的位置精度由先行工序保证。
(4)“互为基准”原则当两个表面相互位置精度及自身尺寸、形状精度都要求较高时,可采用“互为基准”方法,反复加工。
(5)所选的精基准应能保证定位准确、夹紧可靠、夹具简单、操作方便。
以基准面A及另外两侧面作为定位精基准,加工其它表面及孔。
主要考虑精基准重合的问题,当设计基准与工序基准不重合的时
候,应该进行尺寸换算,这在以后还要进行专门的计算,在此不再重复。
2.3制定工艺路线
制订工艺路线的出发点,应当是使零件的几何形状、尺寸精度及位置精度等技术要求能得到合理的保证。
在生产纲领已确定为成批生产的条件下,可以考虑采用万能型机床配以专用夹具,并尽量使工序集中在提高生产率。
除此以外,还应当考虑经济效果,以便使生产成本尽量降下来。
工序01:
铸造
工序02:
时效处理
工序03:
检验零件是否符合加工余量要余
工序04:
粗铣φ40的两端面,余量为2mm
工序05:
精铣φ40孔上下端面,表面粗糙度为3.2
工序06:
粗铣φ20的两端面,余量为2mm
工序07:
精铣φ20孔上下端面
工序08:
钻φ20的孔
工序09:
钻φ12的孔
工序10:
钻φ8的孔,留余量0.5mm
工序11:
检验至图纸要求
工序12:
入库
2.4机械加工余量的确定
加工余量是指加工过程中所切去的金属层厚度
平面的加工余量确定:
加工面
基本尺寸
粗加工余量
精加工余量
说明
φ40的两端面
45
3.9
0.2
双面加工
①20孔的两端面
14
1.8
0.11
双面加工
孔的加工余量确定
加工孔
基本尺寸
钻孔加工余量
扩孔加工余量
φ22
φ22
20
2
φ12
φ12
10
2
M8
M8
6
8.44
2.5确定切削用量及基本工时
1、粗铣φ40、φ22孔的下端面,以φ40上端面为基准
加工条件:
工件材料:
HT200δ0=170—240MPa
加工要求:
粗铣φ40、φ22孔的下端面。
加工余量1.8mm、3.9mm
机床:
X51立式铣床
刀具:
YG6硬质合金端面铣刀铣削宽度ae≤50深度apv4
Z=6刀具直径d0=80mm选择刀具前角Y0=0°后角α0=8°副后角α0'=10°刃倾角λs=-10°主偏角Kr=60°副偏角Kr'=5°
切削用量确定切削用量ap
因为余量较小,故选用ap=3.9一次走刀可以完成
确定每齿进给量fz本工序为粗加工尺寸精度和表面粗糙度可以不
考虑。
使用YG6硬质合金端面铣刀加工,机床功率4.5KW。
查表得:
fz=0.09—0.18故选择fz=0.18mm∕z
确定刀具的磨钝标准查表得:
铣刀刀齿后刀面最大磨损量1.5mm
铣刀直径d0=80mm故选用刀具使用寿命T=120min
计算切削速度VCVf当d0=80mmZ=12ap≤7.5
fz≤0.18mm/z
通过查表得:
vt=98m∕min,nt=250r∕min,Vft=471mm∕min
各修正系数为:
kMV=1.0,ksV=0.8则切削速度的计算公式
CVd0qvI
VC=PkV
PV
TmaPXVfZyVaeUVZ
245800.2
fz=0.18Z=12
VCraPXVfZyVaeUVZPVkV
=1200.323.90.150.180.35400.212°8
=191m∕min
1000VC1000191
760r∕mιn
确定机床转速ns=dw3.1480
计算工时tm=L∕Vc=40∕191=0.2min
2、精加工此工序、粗精加工另一面的切削用量相同。
3、钻扩φ22孔
钻头米用
根据查表,选择高速钢麻花钻钻头,粗钻时do=18mm,
宽l=4mm,棱带长度∣1"5mm,2,1OO,=30°
3°〔a-1∙67*3,由表2.7,系数为0.5,则:
f=(0.43~0∙53)0.5=(0.215~0.265)mm∕r
按钻头强度选择:
查表钻头允许进给量为:
f=2.0mm/r;
时,进给量为f".93mm/rO
f=0.22mm∕r
0.215~0.265mm∕r°根据查表得:
最终选择进给量
由于是通孔加工,为避免即将钻穿时钻头折断,故应在即将钻穿时停止自动进给而改为手动进给。
根据表查出,钻孔时轴向力Ff=2500N,轴向力修正系数为1.0,故Ff=2500N°根据Z525立式钻床使用说明书,机床进给机构允许的最大轴向力为8830N>Ff,故所选进给量可用。
确定钻头磨钝标准及寿命
后刀面最大磨损限度(查表得)为0.6mm,寿命T=45min
切削速度
查表切削速度计算公式为:
χv=0,YV=0∙55,f=0.22,查得修正系数:
kTv=1.0,k∣v=0.85
ktv=1∙0,故实际的切削速度:
查机床说明切削用量选择为:
f=0.22mm∕rn=nc=272r∕minV^15.4m/min
IL45ccc∙
tm0.82min
计算工时nf2720.22
扩孔至φ22
查表扩孔进给量为:
f=°.7~°∙8mm∕r,并由机床使用说明书最终
选定进给量为:
f=0∙81mm∕r
nw=97r/min
先钻φ8大的底孔
使用说明书,现取f=°∙22mm∕r。
查表,v=17m/min,计算机床主
轴转速:
1000v100017I、
ns676.7r∕min
応dwπ×8
按机床选取nwYBOr/min,所以实际切削速度为:
V=鱼=^≡=17.08m∕min
10001000
计算切削基本工时:
根据资料,切削速度V二0.4^,其中V钻为用钻头钻同样尺寸实心
nw=272r∕min
l12.
tm0.2min
计算工时:
nf2720.22
5、钻扩M12×1.5螺纹底孔
机床:
Z525立式钻床
底孔已经确定为φ8.44钻孔直径为φ8,再扩孔至φ8.44
钻φ8的孔
确定进给量f:
根据查表得,f=0.22~0.26mm/r,查Z525机床使用说明书,现取f=0∙22mm∕r。
查表,v=17m/min,计算机床主轴转速:
按机床选取nw=680r∕min,所以实际切削速度为:
dwnw二8680
=17.08m∕min
V二
10001000
计算切削基本工时:
扩孑Lφ8.44
确定扩孔进给量f:
根据查表得,f=0.22~0∙26mm∕r,查Z525
机床使用说明书,现取f=0.22mm∕rO
根据资料,切削速度V二0.4^,其中V钻为用钻头钻同样尺寸实心
孔时的切削速度,故:
v=0∙417=6∙8m∕mi,
nw=272r∕min
l10.
tm0.166min
计算工时:
nf2720.22
5、攻螺纹M12
机床:
Z525立式钻床
刀具:
丝锥M12,P=1.5mm
切削用量选为:
V=0.1m/s=6m/min,机床主轴转速为:
nw=97r∕min,丨/omm,计算切削基本工时:
J0.1min
fn197
第3章夹具设计
3.1夹具的概述及专用夹具的设计
一、机床夹具是在机床上加工时用来装夹工件的工艺设备。
其作用
是使工件相对机床和刀具有一个正确的位置,并在加工中保持这个位置
不变。
1、机床夹具的用途
2、保证被加工表面的位置精度。
由于使用夹具解禁工件可以准确的确定工件与机床、刀具间的相对位置,因而能稳定地获得较高的位置精度
3、减少辅助时间,提高劳动生产率。
二、机床夹具的组成
1、定位元件
它与工件的定位基准相接触是确定工件在夹具中正确位置的一类主要元件。
2、夹紧装置它的作用是将定位后的工件压紧夹牢保证工件已确定的位置在受到切削力、惯性力等作用时不产生位移和变形。
3、夹具体
它是将定位元件、夹紧装置等联接成一体的夹具主体。
三、确定夹具与刀具之间相对位置的元件,用于确定刀具位置并引导刀具的加工的元件。
1、确定夹具与机床之间的相对位置的元件
以上的组成部分不是都必须具备的,但是定位元件、夹紧装置、和夹具体则是夹具最基本的组成部分
四、专用夹具的设计
为了提高劳动生产率、保证加工质量、降低劳动强度需要设计专用
夹具。
设计的工序是加工M8×1.5螺纹孔的夹具。
本夹具将用于Z525立式钻床。
3.2确定夹具的方案
设计夹具时必须根据工件的加工要求和确定的定位基准来选择方
法。
设计定位元件并分析定位精度。
一、定位分析及选择
定位主要根据工件在加工时所需要限制工件在空间直角坐标系中的
各个自由度来选择定位方法。
根据该零件加工的工序和基准来分析,采用一面两孔来定位。
二、定位元件的选择
1、上面分析出定位方法,采取一面两孔定位来选取元件。
(1)平面定位选择φ40的下端面定位。
同时采取φ10H7孔的下端面辅助支撑。
(2)孔定位φ22H8孔选取圆柱销进行定位,φ12H7孔选取20菱形销定位。
0.015
孑L1=φ12H7=φ120
0.033
孑L2=φ22H8=φ220
孔的中心距=75-0.01则夹具的两定位销的中心距尺寸=75-0∙01。
2、确定圆柱定位销的尺寸和偏差
圆柱销的长度确定为20mm。
为了减小工件移动时基准位移误差
(△j,y)并考虑到定位销制造时可能达到的经济精度,取配合为f7。
_Q.02
查公差表得:
φ20f7=φ20卫033
1、确定菱形销的尺寸和偏差
菱形销的长度确定为15mm。
查表选择菱形销的宽度
b1=4mm
B=d-2=10-2=8mm
2ab12(0.010.02)4
由X1min=DI=10=0.024mm
所以菱形销的最大直径
d=D1-X1min=10-0.024=9.976mm
按定位销一般制造经济精度,取直径公差带为h6,则菱形销的定
位圆柱部分定位直径尺寸为:
-0.024
d=9.976h6=φ10ω.033mm
2、计算定位误差
移动时基准位移误差
Δj,y=Δd2+ΔD2+X1min
=0.013+0.033+0.02
=0.066mm
△d1+ΔD1+X1min+Δd2+ΔD2+X2min
tanθ=2L
0.0090.0150.0240.0130.0330.02
=275
=0.00076
△θ=0.043
3.3工件的夹紧
为了保证工件在夹具中定位后不会因为在加工中的切削力、惯性力及离心力等作用下而发生变动,必须采用夹紧装置将其夹紧。
1、设计夹紧装置时应满足以下就基本要求
(1)保证加工精度,不破坏工件的定位或产生不允许的变形
(2)保证生产率,力求夹紧迅速
(3)结构简单、紧凑、制造维修方便,尽量使用标准件。
(4)操作方便、省力、安全。
2、计算切削力
刀具:
高速钢麻花钻dθ=8
Z^ryFI
Ff=CFdofkF
其中.Cf=883∙85Zf=10-7do=4f=0.22
HB200
kF=(190)0-6=(190)0-6=1.03
107
F=883.580.22-1.03=1190N
3.4夹紧力三要素的确定
1、夹紧力的方向应不破坏工件定位的准确性和稳定性,即夹紧力应朝主要定位基准,把工件压向定位元件的定位面上。
此零件的切削力的方向如图4所示:
2、夹紧力的作用点
(1)夹紧点应正对支撑元件或位于支撑元件所形成的支撑面内。
(2)夹紧点应位于工件刚性较好的部位并有一定的作用面积。
(3)夹紧点应尽量靠近加工表面,以减少切削力对夹紧点的力矩防止工件的转动和振动。
此零件的夹紧点的作用图如图3所示。
3、夹紧力的大小
在用计算法求夹紧力时,通常将夹具和工件看作为刚体系统,并视工件在切削力、夹紧力、重力和惯性力作用下,处于静力平衡,然后列平衡方程式求出理论夹紧力,再乘以安全系数K,作为实际夹紧力。
3.5夹紧装置
此零件采取螺旋夹紧装置夹紧工件
螺旋夹紧装置应用最为广泛,它的优点是结构简单、制造方便、夹紧力大、自锁性好、工作可靠而且行程不受限制,缺点是夹紧动作缓慢。
1、夹紧力的计算
此零件在加工时,采用定位销定位,承受了很大的切削力。
所以工件不需要很大的夹紧力,只需要将工件夹紧即可。
所以不需要计算夹紧力。
2、螺旋夹紧机构
为了提高生产效率,在选取垫圈时选用开孔垫圈。
只要松开夹紧螺母,即可实现工件的快换。
3.6导向装置的确定
导向装置主要是在加工孔时借助于钻套确定刀具位置和引导刀具进给方向。
被加工孔的尺寸精度主要由刀具的本身精度来保证。
孔的坐标位置精度,则由钻套在夹具上的位置精度来确定。
并能防止刀具在切入后引偏。
这就是导向装置的作用。
此零件的导向装置是可换钻模和快换钻套。
可换钻套装在衬套中,而衬套则是压配在钻模板中,可换钻套由螺
F7
钉固定住,防止转动。
可换钻套与衬套采用n6配合,衬套与模板采用
HZ
n6配合。
增加衬套的目的是避免模板的磨损克服固定钻模后不易更换的缺点。
确定钻模板孔、衬套外径、钻套的尺寸。
根据所钻的孔径来分析,确定以上三个尺寸及公。
钻套外径φ
0,0180,0180.021
15n6=φ15a007,衬套外径φ22n6=φ220.007,钻模孔φ22H7=φ220。
3.7定位误差的分析
一、计算钻套中心线与工作台的垂直度误差
0,0180,018
钻套外径φ15n6=φ150.007与衬套内经φ22n6=φ220.007的最大间
隙为。
ΔImaX=ES-ei
查公差表得:
EI=16IT=18则ES=El+IT=16+18=34=0.034mm
ei=12=0.012mm
Δ1max=ES-ei=0.034-0.012=0.022mm
衬套外径22n6与钻模板孔中φ22H7的最大间隙为。
Δ2max=ES-ei
查公差表得:
EI=0IT=21贝UES=EI+IT=0+2仁21=0.021mm
ei=15=0.015mm
Δ2max=ES-ei=0.021-0.015=0.006mm
则钻套的中心工作台平面的垂直度误差为。
Δ1max+Δ2max=0.022+0.006=0.028
二、计算定位销轴与工作台平行度误差
圆柱销轴与夹具体孔的最大间隙
-Q.020
定位销尺寸φ16q033
0.033
夹具体孔尺寸φ160
Δmax=ES-ei=0.033-(-0.033)=0.066
夹具体孔的长度为18mm,则圆柱定位销轴与工作台的最大平行度
误差为0.066/18即0.0036
3.8确定钻套的尺寸与公差带
加工螺纹孔M10×1.5要分为几步进行加工。
分为钻孔、扩孔、螺
纹加工。
所以一下确定各个加工孔所用的钻套的尺寸与公差带。
螺纹底孔的确定:
d0=d-(1.04—1.06)P
=10-(1.04—1.06)×1.5
=8.44
螺纹底孔直径为8.44,所以先用φ8的麻花钻钻孔,再选用φ8.44的扩孔钻扩孔,再用M12的丝锥攻螺纹。
所以一下确定各个加工孔所
用的钻套的尺寸与公差带。
一、钻孔钻套的尺寸与公差带的确定
φ8的钻头上偏差为0,故选用钻套孔径为φ8F7
0.034
即φ80∙016
二、扩孔钻套的尺寸与公差带的确定
φ8.44的扩孔钻的上偏差为0,故选用钻套孔径为φ8.44F7
0.034
即φ8.440016
三、丝锥的钻套的尺寸与公差带的确定
φ12的丝锥的上偏差为0,故选用丝锥钻套的孔径为φ12G7
0.025
即φ120∙006
3.9内六角螺钉的抗拉强度校核
在钻孔时,定模板受力不大。
所以螺钉只受到模板的重力。
其他可以忽略不计。
F
抗拉强度的计算:
δmax=A=[δ]
F=GG=mg
已知:
m=6.48kg[δ]=598MPa
G=mg=6.48×9.8=63.5KN
贝UF=G=63.5KN
Fδmax=A≤[δ]
3
63.510N
二(0.014-0.01)2
=4=505.5MPa≤[δ]
所以螺钉的抗拉强度满足要求
3.10夹具操作的简要说明
此零件采用了一面两孔定位。
将工件装夹在夹具中后,用螺旋夹紧装置。
为了提高劳动生产率。
为此,设计了快换装置。
所以在设计垫圈时选用了U形开口垫圈。
所以在装夹和拆卸工件时只需要将螺母松开1
—3扣,取下U形开口垫圈,这样实现了工件的快换。
*sXτ
总结
设计是大学学习中最重要的一门科目,它要求我们把大学里学到的所有知识系统的组织起来,进行理论联系实际的总体考虑,需把金属切削原理及刀具、机床概论、公差与配合、机械加工质量、机