圆筒冲裁拉深件设计说明书.docx
《圆筒冲裁拉深件设计说明书.docx》由会员分享,可在线阅读,更多相关《圆筒冲裁拉深件设计说明书.docx(30页珍藏版)》请在冰点文库上搜索。
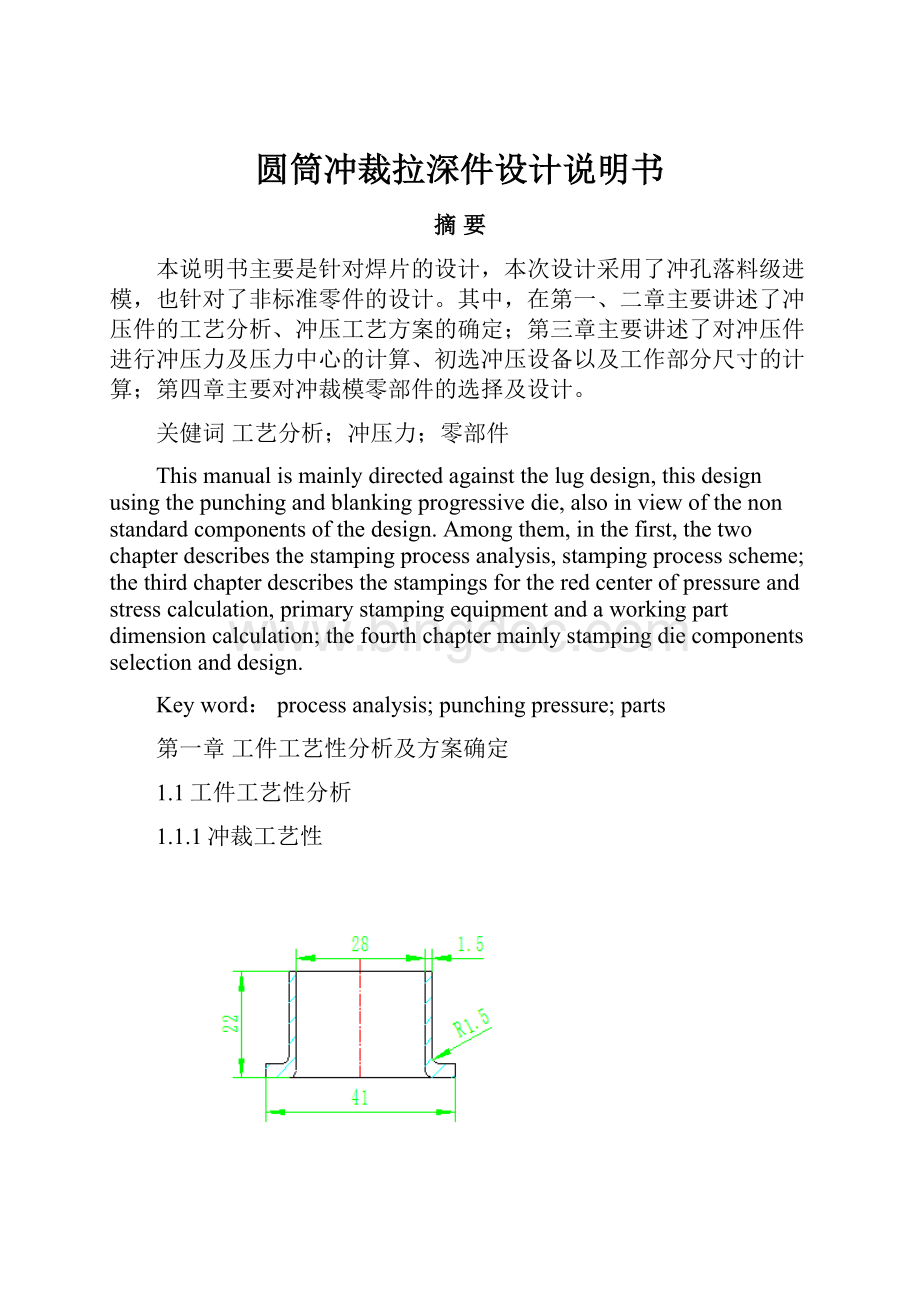
圆筒冲裁拉深件设计说明书
摘要
本说明书主要是针对焊片的设计,本次设计采用了冲孔落料级进模,也针对了非标准零件的设计。
其中,在第一、二章主要讲述了冲压件的工艺分析、冲压工艺方案的确定;第三章主要讲述了对冲压件进行冲压力及压力中心的计算、初选冲压设备以及工作部分尺寸的计算;第四章主要对冲裁模零部件的选择及设计。
关健词工艺分析;冲压力;零部件
Thismanualismainlydirectedagainstthelugdesign,thisdesignusingthepunchingandblankingprogressivedie,alsoinviewofthenonstandardcomponentsofthedesign.Amongthem,inthefirst,thetwochapterdescribesthestampingprocessanalysis,stampingprocessscheme;thethirdchapterdescribesthestampingsfortheredcenterofpressureandstresscalculation,primarystampingequipmentandaworkingpartdimensioncalculation;thefourthchaptermainlystampingdiecomponentsselectionanddesign.
Keyword:
processanalysis;punchingpressure;parts
第一章工件工艺性分析及方案确定
1.1工件工艺性分析
1.1.1冲裁工艺性
图1-1零件图
由零件简图2-1可见,该工件的加工涉及到落料、冲孔、翻边或拉深等工序成形。
该零件的外径为Φ41mm,属于小制件,形状简单且对称,适于冲裁加工。
查《冷冲压模具设计与制造》表2.3冲压件内、外形所能达到的经济精度,因制件形状简单、对称,冲裁件内外形所能达到的经济精度为IT12-IT13。
查表2.5孔中心与边缘距离尺寸公差为±0.5mm。
查表2.7一般剪切断面表面粗糙度为3.2µm.
查《冷冲模设计》表2—3,得材料8号钢的力学性能如下表:
表1-18号钢的性能
抗剪强度τ
255~333MPa
抗拉强度σb
294~432MPa
屈服点σs
206MPa
伸长率δ
29%
材料10钢,其冲压性能较好,孔与外缘的壁厚较大,复合模中的凸凹模壁厚部分具有足够的强度。
1.1.2翻边工艺性
1.翻边工件边缘与平面的圆角半径r=(2~3)t
2.翻边的高度h=22≥1.5r=1.5
3.翻边的相对厚度d/t=14.73>(1.7~2),所以翻边后有良好的圆筒壁
4.冲孔毛刺面与翻边方向相反,翻边后工件质量没大影响。
5.查《中国模具设计大典》第3卷,第35页,K.W.I扩孔实验,预加工孔Φ15.16可扩孔到Φ45左右,而制件为Φ28,即满足翻边性能。
总体看来:
该制件均满足冲裁工艺性和翻边工艺性,适于冲裁加工。
1.1.3判断能否一次性翻边成形
由预冲孔公式可以得到翻边高度H的表达式:
H=
+0.43r+0.72t(1-1)
或H=
(1-
)+0.43r+0.72t
=
+0.43r+0.72t
若将Kmin带入上式,则可得到许可的最大翻边高度Hmax
Hmax=
(1-Kmin)+0.43r+0.72t
其中D—翻边后的中经(mm)
Kmin—极限翻边系数
r—翻边圆角半径(mm)
t—材料厚度(mm)
查《冷冲模设计》,表7-1低碳钢圆孔极限翻边系数
这里凸模采用圆柱形平底型式孔的加工方式为冲孔
因相对厚度d/t=14.73得Kmin=0.55
于是Hmax=
(1-0.55)+0.43×2+0.72×1
=8.0(mm)
因工件高度H=Hmax,所以在平板上能一次性翻边成形
1.2工艺方案确定
根据工件形状,初步确定采用落料、冲孔和翻边等工序,现确定以下方案:
方案一:
一套落料、冲孔、翻边复合模
方案二:
一套落料、冲孔、翻边单工序模
方案三:
一套落料、冲孔、翻边连续模
单工序模、连续模和复合模的相互比较见表1-2
表1-2单工序模、连续模和复合模的性能比较
项目
工序模
连续模
复合模
工作情况
尺寸精度
精度较高
可达IT13~10级
可达IT9~8级
工件形状
易加工简单件
可加工复杂零件,如宽度极小的异形件、特殊形件
形状与尺寸要受模具结构与强度的限制
孔与外形的位置精度
较高
较差
较高
工件平整性
推板上落料,平整
较差,易弯曲
推板上落料,平整
工件尺寸
一般不受限制
宜较小零件
可加工较大零件
工件料厚
一般不受限制
0.6~6mm
0.05~3mm
工艺性能
操作性能
方便
方便
不方便,要手动进行卸料
安全性
比较安全
比较安全
不太安全
生产率
低,压力机一次行程只能完成一道工序,但在多工位压力机使用多副模具时,生产率高
高,压力机一次行程内可完成多道工序
较高,压力机一次行程内能完成两道以上工序
条料宽度
要求不严格
要求严格
要求不严格
模具制造
结构简单,制造周期短
结构复杂,制造和调整难度大
结构复杂,制造难度大
总的看来:
方案一:
生产效率高,因为滑块下行一次既完成落料、冲孔和翻边等工序,不存在定位误差,同轴度高,因此冲压出来的制件精度也较高;但模具结构较复杂,因此模具制造难度大。
方案二:
生产效率不高,由于要多机床或多道工序完成,致使生产效率和经济效益都降低;但模具制造周期短。
方案三:
生产效率较高,完成落料、冲孔的连续模生产效率较高,和方案二一样,由于第二道翻边单工序的存在,降低了生产效率不说,精度也难保证。
因此综合考虑采用方案一,再来确定采用正装复合模还是采用倒装复合模。
正装复合模和倒装复合模的比较见下表2-3
表2-3正装复合模和倒装复合模的比较
序号
正装
倒装
1
对于薄冲件能达到平整要求
不能达到平整要求
2
操作不方便,不安全,孔的废料由打棒打出
操作方便,能装自动拔料装置,能提高生产效率又能保证安全生产,孔的废料通过凸凹模的孔往下漏掉
3
废料不会在凸凹模孔内积聚,每次由打棒打出,可减少孔内废料的胀力,有利于凸凹模减少最小壁厚
废料在凸凹模孔内积聚,凸凹模要求有较大的壁厚以增加强度
4
装凹模的面积较大,有利于复杂制件拼快结构
如凸凹模较大,可直接将凸凹模固定在底座上省去固定板
从表2-3中可以看出:
正装对于薄冲件能达到平整要求,且废料不会在凸凹模孔内积聚,有利于凸凹模减少最小壁厚。
而倒装不能达到平整要求,而且废料在凸凹模孔内积聚,凸凹模要求有较大的壁厚以增加强度。
从保证冲裁件质量、经济性和安全性前提下,综合考虑采用正装复合模,即模具结构为落料、冲孔、翻边正装复合模。
第二章排样及计算材料利用率
2.1计算预冲孔大小
图2-1零件图
该制件是在冲孔后的平板毛坯上翻边成形,在翻边时,同心圆之间的距离变化不显著,预制孔直径可以用弯曲展开的方法近似计算:
查《冷冲模设计》第215页
预冲孔直径公式d=D1-2[
(2-1)
因D1=D+t+2rh=H-r-t代入上式,并简化得:
d=D-2(H-0.43r-0.72t)
式中D—翻边后的中经(mm)H—翻边高度(mm)
r—翻边圆角半径(mm)
t—材料厚度(mm)
这里D=28mmH=22mmr=1.5mmt=1.5mm
所以d=28-2(8-0.43×1.5-0.72×1)
=14.73(mm)
同可得:
相对厚度d/t=14.73/1=14.73
翻边系数d/D=14.73/28=0.53
2.2确定排样方式
采用有废料和少废料排样,排样图分别如图3-2和图3-3
图2-2有废料排样
图2-3无废料排样
少废料排样虽然材料利用率有所提高,但由于条料本身的宽度公差,以及条料导向与定位所产生的误差会直接影响冲裁件尺寸而使冲裁件的精度降低,也降低了模具寿命,结合各自的优缺点,综合考虑采用有废料排样法。
2.3计算材料利用率
1.计算制件的面积A
制件面积A的计算公式:
A=
(D2-d2)(2-2)
=
(412-14.732)
=1149.2613(mm2)
式中D—毛坯外径(mm)
d—冲孔直径(mm)
2.确定搭边a与a1的值
查《冷冲模设计》表3-10搭边a与a1数值
取a=0.8mma1=1.0mm
于是条料宽度:
b=41+2a1=43mm
进距:
l=41+a=41.8mm
3.材料利用率计算
查《中国模具设计大典》第3卷冲压模具设计。
表18.3-24轧制薄钢板的尺寸(GB/T708-1988)
板料规格选用1.0mm×750mm×1500mm(tmm×Bmm×Lmm)
1)若采用纵裁:
裁板条数n1=B/b=750/43=17条余19mm
每条个数n2=
=(1500-0.8)/41.8=35个余36.2mm
每板总个数n总=n1×n2
=17×35
=595(个)
材料利用率η总=
×100%(2-3)
=(595×1149.2613)/(1500×750)×100%
=60.78%
2)若采用横裁:
裁板条数n1=L/b=1500/43=34条余44mm
每条个数n2=
=(750-0.8)/41.8=17个余38.6mm
每板总个数n总=n1×n2
=34×17
=578(个)
材料利用率η总=
×100%(2-4)
=(578×1149.2613)/(1500×750)
×100%
=59.05%
显然纵裁的材料利用率要高些,因此选用纵裁。
4.计算零件的净重G
G=F.t.ρ(2-5)
式中G—工件重量(g)
F—工件面积(cm2)
t—材料厚度(cm)
ρ—材料密度(g/cm3)
8号钢属于低炭钢,在这里密度取ρ=7.85g/cm3
则G=F.t.ρ
=1149.2613×10-2×1.0×10-1×7.85
=9.02g
第三章冲裁力及压力中心计算
3.1.落料力F落
查《冷冲模设计》第54页,落料力F落公式为
F落=KLtτ(3-1)式中F落—落料力(N)
L—冲裁件周长(mm)
t—材料厚度(mm)
τ—材料的抗剪强度(MPa)
K—系数,常取K=1.3
这里L=π×54mmt=1mm取τ=300MPa
则F落=1.3×π×41×1×300
=50208.6(N)
3.2卸料力F卸
查《冷冲模设计》表3-8卸料力、推件力和顶件力系数
取K卸=0.035
F卸=K卸.F落(3-2)
=0.035×50208.6
=1757.301(N)
3.3冲孔力F冲
查《冷冲模设计》第54页,落料力F冲公式为
F冲=KLtτ(3-3)
式中F冲—落料力(N)
L—冲裁件周长(mm)
t—材料厚度(mm)
τ—材料的抗剪强度(MPa)
K—系数,常取K=1.3
这里L=π×35mmt=1mm取τ=300MPa
于是F冲=1.3×π×35×1×300
=42861(N)
3.4顶件力F顶
查《冷冲模设计》表3-8卸料力、推件力和顶件力系数
取K顶=0.06
F顶=K顶.F冲(3-4)
=0.06×42861
=2571.66(N)
3.5翻边力F翻
查《冷冲模设计》,第216页,翻边力公式为
F翻=1.1π(D-d)tσs(3-5)
其中F翻—翻边力(N)
D—翻边后中经(mm)
d—翻边预冲孔直径(mm)
t—材料厚度(mm)
σs—材料的屈服点(MPa)
这里D=28mm,d=14.73mm,t=1.5mm,σs=206MPa
于是F翻=1.1×3.14(28-14.73)×1.5×206
=9441.9235(N)
3.6总冲压力F总
F总=F落+F冲+F卸+F顶+F翻(3-6)
=50208.6+42861+1757.301+257.66+9441.9235
=104526.48(N)
3.7计算压力中心
计算压力中心的目的是使模柄轴线和压力机滑块的中心线重合,避免滑块受偏心载荷的影响而导致滑块轨道和模具的不正常磨损,降低模具寿命甚至损坏模具。
从制件的形状可以看出,该制件是回转体结构,形状对称,故模具压力中心就在圆心部位,即无须再来计算了。
第四章主要工作部分尺寸计算
4.1落料刃口尺寸
查《冷冲模设计》表3-3冲裁模初始双面间隙Z
取Zmin=0.1mmZmax=0.14mm
对零件图中未注公差的尺寸,冲压件一般保证精度IT14,因制件形状简单且对称,在这里保证精度IT13。
查《互换性与测量技术基础》表3-6简单形状冲裁时凸凹模的制造偏差
δ凹=+0.03mmδ凸=-0.02mm
因此:
|δ凹|+|δ凸|=0.03+0.02mm
=0.05mm
Zmax-Zmin=0.14-0.1mm
=0.04mm
|δ凹|+|δ凸|>Zmax–Zmin
因此在这里采用单配方法加工。
对于落料,先做凹模,并以它作为基准配做凸模
查《互换性与测量技术基础》表2-4查出其极限偏差为:
mm
查《冷冲模设计》表3-5磨损系数取X=0.5
则D凹=
(4-1)
=
mm
=
mm
落料凸模的尺寸按凹模尺寸配制,其双面间隙为0.10~0.14mm
4.2冲孔刃口尺寸
冲孔部分:
δ凹=+0.02mmδ凸=-0.02mm
|δ凹|+|δ凸|=0.02+0.02mm
=0.04mm
|δ凹|+|δ凸|=Zmax–Zmin
对于采用分别加工时,应保证下述关系:
|δ凹|+|δ凸|≤Zmax–Zmin(4-2)
但对于形状复杂或料薄的工件,为了保证凸、凹模间一定的隙值,必须采用配合加工。
因此在这里采用还是采用单配方法加工
对于冲孔,先做凸模,并以它作为基准配做凹模
查《互换性与测量技术基础》表2-4查出其极限偏差为:
mm
查《冷冲模设计》表3-5磨损系数取X=0.5
则d凸=
(4-3)
=
=
mm
冲孔凹模的尺寸按凸模尺寸配制,其双面间隙为0.10~0.14mm
4.3翻边工作刃口尺寸
4.3.1翻边间隙
如图5-1,由于在翻边过程中,材料沿切向伸长,因此其端面的材料变薄非常严重,根据材料的统一变形情况,翻边凹模与翻边凸模之间的间隙应小于原来的材料厚度。
图5-1翻边间隙
查《冷冲压模具设计与制造》,表5-5平板毛坯翻边时凸凹模之间的间隙
得Z/2=0.85mm
4.3.2翻边刃口尺寸
1.翻边凸模的刃口尺寸计算
查《互换性与测量技术基础》表2-4查出其极限偏差为:
mm
查《冷冲模设计》表3-5磨损系数取X=0.5
则d凸=
(4-4)
2.翻边凹模的刃口尺寸计算
根据翻边间隙和翻边凸模的刃口尺寸来确定翻边凹模的刃口尺寸
D凹=
(4-5)
=
=
mm
第五章凸模、凹模及凸凹模的结构设计及校核
5.1落料凹模结构设计
5.1.1最小壁厚
冲孔落料复合模的凸凹模.其刃口平面与工件尺寸相同,这就产生了复合模的“最小壁厚”问题。
冲孔落料复合模许用最小壁厚可按表6-1选取,形式如图6-1表示,表值为经验数据。
表6-1 凸凹模最小壁厚a数值(单位:
mm)部分如下
材料厚度
0.8
0.9
1.0
1.5
最小壁厚
2.3
2.5
2.7
3.2
最小直径
15
18
图5—1最小壁厚
为了增加凸凹模的强度和减少孔内废料的涨力,可以采用对凸凹模有效刃口以下增加壁厚或将废料反向顶出的办法.如图6—1所示。
5.1.2模具材料的选择
从众多模具材料中选出9Mn2V钢,该模具钢是一种综合力学性能比碳素工具钢好的低合金工具钢,它具有较高的硬度和耐磨性,淬火时变形较小,淬透性很好。
由于钢中含有一定量的钒,细化了晶粒,减小了钢的过热敏感性,同时碳化物较细小和分布较均匀。
9Mn2V钢的化学成分和物理性能分别如表5-2和表5-3所示
表5-29Mn2V钢化学成分(GB/T1299—2000)W%
C
Si
Mn
V
P
S
0.85~0.95
≤0.40
1.70~2.00
0.10~0.25
≤0.030
≤0.030
表5-3临界温度
临界点
Ac1
Acm
Ar1
Ar3
温度(近似值)
730
760
655
690
表5-4综合性能
耐磨性
耐冲击性
淬火不变形性
淬硬深度
中等
中等
好
浅
红硬性
脱碳敏感性
切削加工性
差
较大
较好
所以这里不管是凸模、凹模还是凸凹模,材料都选用9Mn2V钢
这里的落料凹模的热处理硬度为60~62HRC
5.1.3确定凹模外形尺寸
确定凹模外形尺寸的方法有多种,通常都是根据零件的材料厚度和排样图所确定的凹模型孔壁间最大距离为依据,来求凹模的外形尺寸。
凹模的刃口形式,考虑到本例生产批量较大,所以采用刃口强度较高的凹模,故采用阶梯形直壁式。
凹模的外形一般有矩形与圆形两种,凹模的外形尺寸应保证凹模有足够的强度与刚度,凹模的厚度还应考虑修模量。
凹模的外形尺寸一般根据冲材料的厚度和冲裁件的最大外形尺寸来确定。
查《冷冲模设计》,第101页,凹模厚度和壁厚公式为
凹模厚度H=Kb(≥15mm)(5-1)
式中K—系数,考虑板料厚度的影响
b—冲裁件的最大外形尺寸
凹模壁厚C=(1.5~2)H(≥30~40mm)(5-2)
查《冷冲模设计》,表4-3系数K值
因b=41mm取K=0.22
故H=0.22×41
=9.02mm
C=1.5×35
=52.5mm
考虑到翻边高度22mm和保证H≥15mm,最后取H=35mm
5.1.4凹模的强度校核
查《中国模具设计大典》,第三卷,表20.1-18凹模强度计算公式
Hmin=
(5-3)
式中Hmin—凹模的最小厚度(mm)
F—冲压力(N)
σwp—许用弯曲应力(MPa)
d、do—凹模刃口与支承口直径(mm)
这里F=F落=50208.6(N)σwp=500MPad=40.77mmdo=51mm
Hmin=
=8.3879mm
而真实的凹模厚度为35mm,所以凹模的强度满足要求。
5.2落料、翻边凸凹模外形尺寸
1.落料、翻边凸凹模的高度
落料、翻边凸凹模的高度满足翻边高度和凸、凹模之间安全距离外,还考虑翻边间隙,保证强度要求,即凸凹模壁厚大于最小壁厚。
这里落料、翻边凸凹模的高度为47mm。
2.落料、翻边凸凹模的强度校核
Lmax≤
(5-4)式中Lmax—冲孔凸模许用的最大自由长度(mm)
E—冲孔凸模材料的弹性模量(MPa)
d—凸模或冲孔直径(mm)
τ—冲件材料的抗剪强度(MPa)
t—冲件材料的厚度(mm)
这里E=2.2×
MPad=40.77mmt=1mmτ=300MPa
于是Lmax≤
=
×
=2095.4mm
而实际的冲孔、翻边凸凹模厚度为47mm,所以强度完全满足要求。
材料同样选用9Mn2V钢,其热处理硬度为58~60HRC
落料、翻边凸凹模
5.3冲孔、翻边凸凹模外形尺寸
冲孔、翻边凸凹模的功能是完成冲孔、翻边,重要性大,其热处理硬度也相对比落料凸模大,其材料选用9Mn2V钢,热处理硬度为60~62HRC
1.冲孔、翻边凸凹模的高度
冲孔、翻边凸凹模的高度=冲孔、翻边凸凹模固定板的厚度+落料凹模的厚度
=12mm+35mm
=47mm
2.冲孔、翻边凸凹模的强度校核
1)冲孔凹模的强度校核
查《中国模具设计大典》,第三卷,表20.1-18凹模强度计算公式
Hmin=
(5-5)
式中Hmin—冲孔、翻边凸凹模的最小厚度(mm)
F—冲压力(N)
σwp—许用弯曲应力(MPa)
d、do—冲孔、翻边凸凹模刃口与支承口直径(mm)
这里F=F冲=42861Nσwp=500MPad=15.3mmdo=16.3mm
Hmin=
=8.97mm
2)翻边凸模稳定能力的校核
Lmax≤
(5-6)
式中Lmax—冲孔凸模许用的最大自由长度(mm)
E—冲孔凸模材料的弹性模量(MPa)
d—凸模或冲孔直径(mm)
τ—冲件材料的抗剪强度(MPa)
t—冲件材料的厚度(mm)
这里E=2.2×
MPad=27mmt=1.5mmτ=300MPa
于是Lmax≤
=
×
=745.6mm
而实际的冲孔、翻边凸凹模厚度为47mm,所以强度完全满足要求。
6.4冲孔凸模外形尺寸
1.冲孔凸模的形式采用类似直通式的形式,少了阶梯形式的复杂,主要受上顶杆孔和凸模孔的影响,避免出现最小壁厚。
2.冲孔凸模的长度
冲孔凸模的长度=冲孔凸模固定板的厚度+落料、翻边凸凹模的高度+超出落料、翻边凸凹模的2mm
则冲孔凸模的长度=12mm+47mm+2mm
=61mm
3.强度校核
1)凸模稳定能力的校核
查《中国模具设计大典》,第三卷,表20.1-10凸模稳定能力校核计算公式
Lmax≤
(5-7)式中Lmax—冲孔凸模许用的最大自由长度(mm)
E—冲孔凸模材料的弹性模量(MPa)
d—凸模或冲孔直径(mm)
τ—冲件材料的抗剪强度(MPa)
t—冲件材料的厚度(mm)
这里E=2.2×
MPad=15.3mmt=1.5mmτ=300MPa
于是Lmax≤
=
×
=307mm
2)承压能力的校核
σk=
≤σp(5-8)式中τ—冲件材料的抗剪强度(MPa)
t—冲件材料的厚度(mm)
d—凸模或冲孔直径(mm)
σk—凸模刃口的接触应力(MPa)
σp—凸模材料的许用压应力(MPa)
这里τ=300MPat=1.5mmd=15.3mmσp=1500MPa
则σk=
=
=600MPa≤σp=1500MPa
即凸模稳定能力和承压能力均满足要求。
第六章主要零部件设计
6.1模柄的设计
查《中国模具设计大典》第3卷,表22.