外观检验作业标准规范.docx
《外观检验作业标准规范.docx》由会员分享,可在线阅读,更多相关《外观检验作业标准规范.docx(24页珍藏版)》请在冰点文库上搜索。
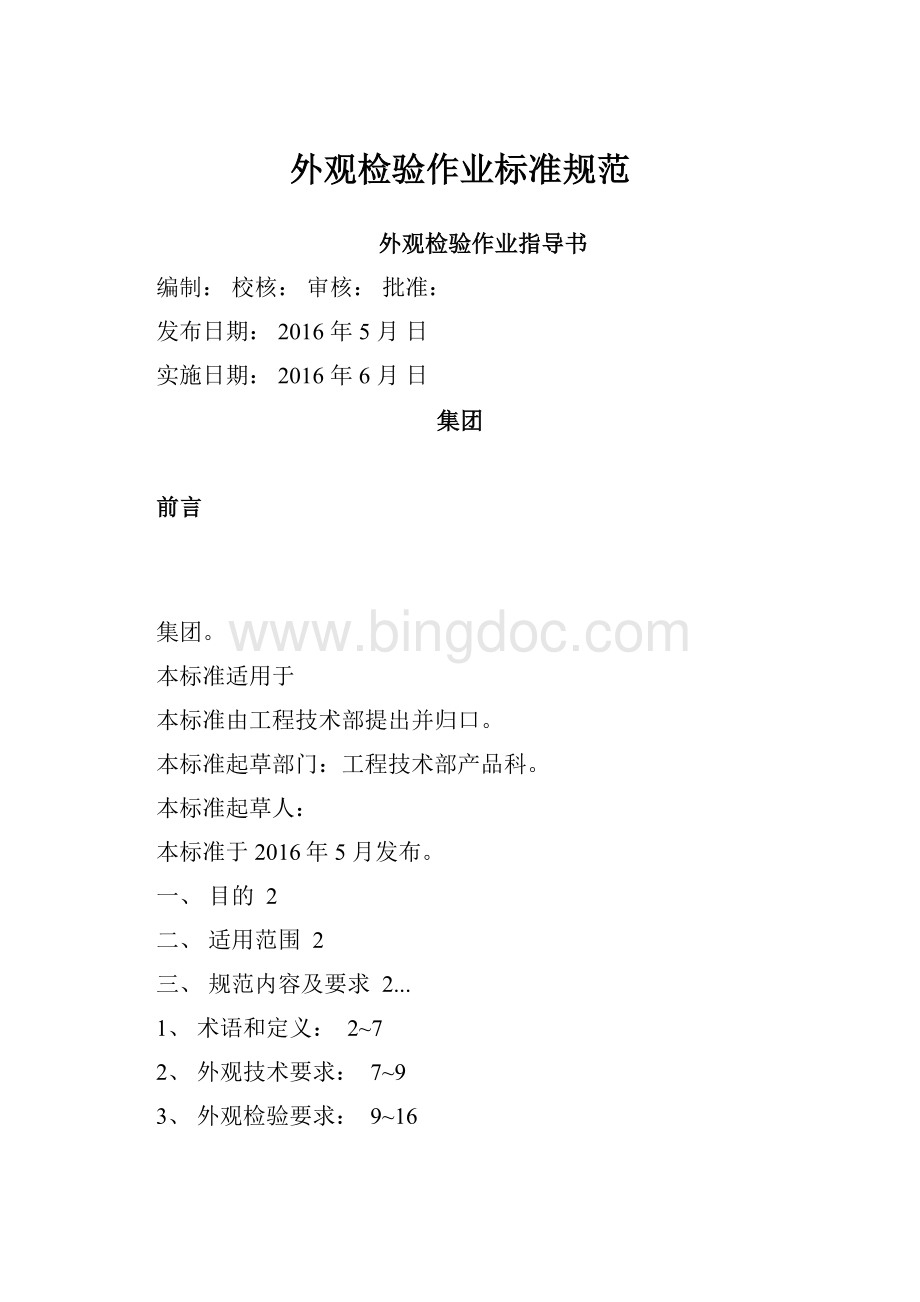
外观检验作业标准规范
外观检验作业指导书
编制:
校核:
审核:
批准:
发布日期:
2016年5月日
实施日期:
2016年6月日
集团
前言
集团。
本标准适用于
本标准由工程技术部提出并归口。
本标准起草部门:
工程技术部产品科。
本标准起草人:
本标准于2016年5月发布。
一、目的2
二、适用范围2
三、规范内容及要求2...
1、术语和定义:
2~7
2、外观技术要求:
7~9
3、外观检验要求:
9~16
外观检验作业指导书
、目的
根据产品要求及生产技术水平而制定,作为产品外观是否合格判断的依据,同时兼顾已
形成惯例的一些共识,并参考已在执行的部分检验标准,对一些可以接受的表面外观缺陷进行限制,在本文中未出现的外观缺陷种类属于不允许范围。
二、适用范围
三、规范内容及要求
1、术语和定义:
产品指公司确定的、处于向客户发货状态下的物品,如整机、模块、散件
A级表面
在产品正常工作状态下,在不移动产品的情况下,客户能经常直接正视到的表面。
B级表面
在产品正常状态下,在不移动产品的情况下,客户偶尔能够看到或者打开门板之后能看
到的表面
C级表面
客户在正常的产品操作中不可见或在拆装打开产品后,才可以看到的表面正视指检查者站立于被检查表面的正面,视线、光线分别与被检表面呈45-90°而进行的
光源
观察(如图1)
被检查表面
光源
被检查表面
图:
“正视”位置示意图
金属表面包括电镀、氧化、钝化、以及金属压铸面等表现为金属质感的表面,非喷涂面
拉丝
是一种砂带磨削加工,通过砂带对金属表面进行磨削加工,去除金属表面缺陷,并形成具有一定粗糙度、纹路均匀的装饰表面,例如发纹不锈钢
基材花斑
电镀或氧化前因基材腐蚀、或者材料中的杂质、或者材料微孔等原因所造成的与周围材质表面不同光泽或粗糙度的斑块状花纹外观
镀前划痕
指电镀或氧化之前因操作不当、或对明显缺陷进行粗打磨等人为造成的基体材料上的划伤或局部磨擦痕迹,一般呈细线型
浅划痕
膜层表面划伤,但未伤至底层(既底层未暴露);对其它无膜层表面则为:
目测不明显、手指甲触摸无凸凹感、未伤及材料本体的伤痕
深划痕
表面膜层划伤,且已伤至底层(既底层已暴露出来);对无膜层表面则为:
目测明显、手指甲触摸有凸凹感、伤及材料本体的伤痕
凹坑
由于基体材料缺陷、或者加工过程中操作不当等原因而在材料表面留下的小坑状痕迹凸凹痕
因基材受撞击或校形不良等而呈现出的明显变形、凸凹不平整的现象,手摸时有不平感觉
抛光区
对基材上的腐蚀、划伤、冲裁毛刺、焊接区等部位进行机械打磨抛光后表现出的局部高光泽、光亮区域
烧伤
拉丝处理或打磨时因操作不当,造成零件表面过热而留下的烧蚀痕迹
水印
电镀或氧化后因清洗水未及时干燥或干燥不彻底所形成的斑纹、痕迹
水纹
塑胶或压铸件成形时,熔体流动产生的可见条纹
缩水
因材料、工艺等原因使塑胶或压铸件表面出现的收缩现象
气泡
指塑胶件因工艺原因内部出现的可见气泡
砂眼
塑胶或压铸件表面的疏松针孔。
披锋
压铸或塑胶件上浇口残留物去掉后的毛刺,金属板材冲裁和金属切削后的毛刺
露白
镀锌彩色钝化膜因磨擦而被去除露出锌层,或因缝隙截留溶液导致的无钝化膜现象,呈现为区别于周围彩色的白色
雾状
镀铬、镀镍表面或透明塑胶表面上的模糊、不清晰、不光亮的现象
局部无铬层
指镀铬表面因电镀工艺的局限而在凹槽内、深孔内、折弯内角等低电位区出现铬层未电镀上的现象
修补
因膜层损伤而用涂料所作的局部遮盖
异物
由材料、模具、环境或机器设备中的灰尘、夹杂物、污物等影响而形成的与表面不同色的斑点
颗粒
因材料杂质或外来物(如焊渣等)的影响而在表面形成的、颜色与正常表面一致的凸起现象
挂具印
指电镀、氧化、或喷涂等表面处理生产过程中,因装挂用辅助工具的遮挡而使其与零件相接触的部位局部无膜层的现象
裂纹
材料(如尼龙、塑胶、压铸件、热处理后零件)中出现的介质不连续现象
图文损伤
印刷图文因局部脱落或擦伤、附着不良、污染等造成的图形、字迹不完整不清晰现象外购件
指不是由本公司自行设计制造的一些成品采购件或元器件等
1.32色差
同一套产品不同零件表面颜色不一致,零件表面颜色与标准色板(或封样)不一致,或同一表面变色、脱色、掉色
1.33喷涂毛刺
喷涂区域边缘由于保护胶纸等撕掉后留下的毛刺
1.34皱皮
由于涂膜的流平性不良,涂层处产生的皱褶
1.35桔皮喷涂表面因基材表面质量,喷涂粉末沉降等导致涂层或者粉末上粉不良出现类似桔子皮的皱纹
1.36针孔在底漆或面漆喷涂后,涂层表面呈现出密密麻麻的小孔症状
1.37垂流(流挂/滴流)涂层后由于局部喷漆量过大,产生下垂形成条状物
1.38露底、掉漆露出喷涂层下面基体材料颜色的缺陷
1.39起泡
喷涂表面有凸起(气泡造成),用力压破后出现表面凹陷或露底2、外观技术要求:
2.1总则
2.1.1原则:
产品外观应美观,单独一零/部件的整体视觉效果不能受到破坏,不会给人以劣质产品的印象。
生产者应认真操作,严格控制产品质量,避免在生产过程中出现对各种表面的损伤。
如果发现某一缺陷具有批量性或大面积,既便此缺陷属于“可接受“范围,也可以对该产品不予验收。
2.1.2公司产品的各部位表面按其在产品中所处位臵和质量要求划分为三个等级,既:
A级、B级和C级表面。
2.1.3有签样或图纸上有特殊要求的零部件,其对应的缺陷优先按其样板或技术要求的标准进行判断。
其它结构件表面不能超出表2的要求,否则为不合格。
表2中未包括的缺陷均属于不允许范围(但符合零件状态标准的除外)。
(注:
表2中所列的缺陷个数当在每一表面上超过2个时,每2个缺陷之间的距离必须大于10mm,否则视为不同一缺陷,面积以其总和计。
)
2.1.4零件的生产应首先按照各种零件技术的要求和各工序检验规范进行质量控制(如下);组装后的结构件按本规范检验表面外观
2.1.5对于颜色、光泽和纹理,按零件生产要求进行控制。
2.1.6特殊装饰表面应在相应的零件图纸中(或以签样的形式)规定是否允许表面缺陷、包括是否允许折弯模具压痕等。
2.2印刷图文
对于印刷图文的要求按照每个合同的具体要求执行。
在外部表面的印刷图文周围20mm范围内不允许有任何表面缺陷。
其它按表2执行。
2.3加工工艺原因导致的问题
2.3.1拉丝或喷砂后再进行折弯,容易在折弯变形部位出现裂纹。
应控制裂纹深度,必要时以签样标准加以限制。
2.3.2拉丝或喷砂表面经压铆后在压铆区域纹理、光泽不完全一致的现象(装饰纹被压平或有压过痕迹),可以接受。
2.3.3对于在压铆、焊接的背面所呈现的轻微凸凹痕迹,属于正常的加工痕迹;但在要求较高的装饰性表面(如喷有机涂层的外部表面)应加以适当的掩饰处理。
2.3.4镀彩锌零件先电镀后压铆时,压铆区的电镀层外观在颜色或光泽上有变化、但镀层及钝化膜无损伤,不作为缺陷。
若钝化膜有损伤,可对钝化膜部位进行涂漆(金色)修补,该修补不受表2的面积限制。
2.3.5对于机械加工过程中形成的正常模具压印,不属于缺陷;但必须保证其与零件边缘轮廓平行或者具有一定的规律性。
2.3.6冲压过程中产生的接刀痕,只要符合安全尺寸规定,即可接受。
2.3.7带有盲孔、或者较深通孔的零件进行电镀或喷涂时,孔内较难镀(喷)上。
因此允许在孔内部、深度大于孔半径的区域没有膜层,但可以涂上油漆(或其它类似的有保护作用的干膜涂料)加以保护,不允许有可见的腐蚀物。
(同时需注意满足尺寸要求)。
2.3.8表面处理的挂具印应安排在C级表面。
对于只有A级表面的零件,其挂具印应位于边角位臵,并要求其大小控制在S≤2.0且P≤4(S及P的含义见表2)。
材料缺陷导致的问题
2.4.1由于原材料制造原因,铝制零件有时会在化学处理后、在其表面呈现出粗晶组织现象(如斑纹状态)。
这种缺陷不允许出现在面板类零件等外部表面,但可用于其它表面(前提是该材料的其它性能符合相关技术要求,如化学成份、机械性能等,而且花纹比较均匀)。
但若是批量性,则按2.1.1规定执行。
2.4.2由电镀锌板或电镀锡板(马口铁)制作的零件,在其切口断面会出现锈迹。
只要这种锈蚀现象只发生在断面上,而没有延伸到平板区域,切呈零星点状、不成片,则认为可接受。
2.4.3镀锌钢板、耐指纹板、覆铝锌板在折弯时出现的模具压痕处膜层损伤,只允许出现在内部表面。
缺陷的改善
2.5.1对于基材花斑、或镀前划痕、或者焊接后的表面不平整等,均可以采取打磨抛光的方式加以去除,但抛光区不能留下有深度感的打磨条纹(既应采用较细的磨料,表面粗糙度Ra低于1.0μm),且打磨后的基材必须符合零件尺寸要求。
因抛光区的光泽与周围区域不同,对同一表面上抛光区的面积和数量限制如表2;当超出限制时,应对整个表面进行抛光处理以使该表面光泽基本均匀一致,同时也应满足本文2.1.1的原则:
不能在整个表面布满了小面积的抛光区。
2.5.2表面缺陷的消除可采取拉丝、喷砂或焊补之后打磨抛光的方法加以补救。
但要求拉丝、喷砂或抛光后整个表面纹路均匀,所形成的表面粗糙度Ra不大于1.0μm。
(建议:
拉丝
用的砂带型号最终为400目以细),其它要求不变。
(注意:
本文中其它地方所提到的“喷砂”和“拉丝”,不包括本节所述的情况。
)
2.6特殊情况
2.6.1当型材棱边有磕碰凹痕时,在A级表面上,正视其磕碰凹痕深度不能超过0.7mm(如图2),宽度不限;数量每条边不多于2处。
0.7mm
图2:
棱边上的磕碰凹痕
2.6.2无色氧化处理的铝表面上的划痕,均当作“镀前划痕”对待。
2.6.3当用数控冲床进行加工时,由于机床台面对板材的磨擦作用会出现一些轻微的磨擦痕,既外观上此种擦痕较宽,无凹入感.此类极轻微的擦痕可以出现在内部表面上,不受表2限制。
2.6.4螺钉头上若出现槽口明显变形、或表面膜层破损,均不允许。
若槽边缘出现的轻微毛刺,在外部表面上不允许,在其它表面,以目视没有明显的变形、或凸起、或膜层脱落等缺陷。
2.6.5对无凹入感的镀前划痕,当其与轮廓边平行者,允许L≤300且P≤2。
(L及P的含义见表2)3.外观检验要求
3.1目视检测条件为:
在自然光或光照度在300-600LX的近似自然光下(如40W日光灯,距离500mm处),且检查者位于被检查表面的正面,视线、光线分别与被检查面呈45-90°进行正常检查(参见图1)。
要求检查者的校正视力不低于1.0。
3.2检查时,每一表面按其面积或该表面最大外形尺寸划分为不同大小类别,当有两个条件满足时,以大的一类为准。
表面大小划分标准如表1。
当缺陷所在的检测面尺寸超过表2中对应的最大一类时,则将该表面划分为几个这样的最大面对待,且划分方法因保持同一方式(既始终按面积分,或始终按外形尺寸分)。
3.3不同等级面的检验要求
检验条件
A级表面
B级表面
C级表面
检查时间(s)
10
5
3
检查距离(mm)
500~550
是否旋转
局部角度进行旋转
不旋转
不旋转
注:
重点合同可根据实际要求加大检查力度。
3.4喷涂件检验要求
3.4.1有封样或图纸上有特殊要求的零件,其对应的缺陷优先按其限度样板或技术要求
的标准进行判断。
3.4.2可接收的等级面缺陷不能影响产品的装配和功能,否则仍判不合格。
3.4.3对某一缺陷判定有歧异,或者出现本规范中未定义的缺陷时,由QE工程师进行仲裁判定并签订《品质问题对策书》。
3.4.4同一表面缺陷不能聚集过多,实际缺陷数量不能超过缺陷允收表规定的缺陷数N。
3.4.5同一表面同一区域缺陷不能聚集过大,即以规定缺陷间距为半径的圆周内,实际测量结果不能大于缺陷允收表的要求。
对于可累积计算的缺陷如长度L和面积S等,记录累积值(L=L1+L2+⋯Ln,S=S1+S2+⋯Sn)与缺陷允收表比较。
对无法累积计算的缺陷如高度H,宽度W,直径D等,记录最大的测量值与缺陷允收表比较。
3.5.磁性测厚仪法
利用电磁场磁阻原理,以流入钢铁基板的磁通量大小来测定涂层厚度。
适用于以冷轧板、镀锌板为基板的彩涂板涂层厚度的测定。
若涂层厚度低于3μm时则本方法不适用。
当彩涂板基板为冷轧板时,选取距试样边缘距离大于25mm的3个不同位臵,用磁性测厚仪直接进行涂层厚度测量,并记录厚度值。
当彩涂板基板为镀锌板时,选取距试样边缘距离大于25mm的3个不同位臵,用磁性测厚仪测量镀锌层和涂层的总厚度。
用对镀锌层无腐蚀作用的脱漆剂将涂层去除,在同样的地方测量镀锌层厚度(或用已知锌层单位面积重量换算成锌层厚度),总厚度与镀锌层厚度之差即为涂层厚度。
3个不同测量部位涂层厚度的算术平均值,即为该试样的涂层厚度,以微米(μm)表示。
3.6划格检验将试样放在平整的平面上,用划格器或刀具在试样的涂层上用均匀的压力和相同的间距(1-2mm)以平稳的手法划出平行的切割线(6或11条),所有的切口需穿透到基板的表面,切入基板不能太深。
再与原先的切割线成90°角垂直交叉划出平行的6条或11条切割线,形成格子图形。
用胶带粘住和压紧划格区域,以确保胶带与整个划格区域全部粘住,然后用与试样表面成垂直方向的力迅速一次拉下胶带。
所划格区域涂层底部不能存在刮腻子现象
3.7划格试验等级
按下表的6级分类,评定试样划格试验等级。
等级
涂层脱落程度
脱落面积%
0
切口的边完全平滑,格子上没有方格脱落
0
1
在交叉点,有小的片状涂层脱落
≤5%
2
沿着切口的边和交叉点,有小的片状涂层脱落
5-15%
3
沿着切口的边和方格部分有涂层脱落
15-35%
4
沿着切口的边,涂层长条式地脱落
35-65%
5
涂层长条式地严重脱落
>65%
3.8喷涂件产品外观缺陷的可接受范围
缺陷类型
A级表面
B级表面
C级表面
色差
参考限度样品
参考限度样品
参考限度样品
浅划痕
L≤3,W≤0.2,N≤1
L≤10,W≤0.5,N≤2
不限制
深划痕
不允许
不允许
允许,但不伤及基材且
L<10mm,W<0.2,N<2
凹陷
门板类:
≤0.07mm
框架类:
≤0.20mm
门板类:
≤0.1mm
框架类:
不能影响安装
不能影响安装
凸起
不允许
≤0.1mm
不能影响安装
异物
S≤0.5,H≤0.5,N≤1
S≤1.5,H≤0.5,N≤2
不限制
污迹
不允许
不允许
不允许
流挂
不允许
不允许
允许局部轻微缺陷
桔皮
不允许
允许边角处S≤50
不限制
起泡
不允许
不允许
不允许
露底/针孔
/掉漆
不允许
不允许
不允许被看到
挂具印
不允许
不允许
S≤5
毛刺/边
不允许
不刮手
不刮手
修补
允许拐角或边缘处的线状补
漆,且L≤2,W≤0.2,
N≤2,修补不允许引入色差
缺陷。
L≤10,W≤0.5,N≤2或S≤3,N≤2,修补不允许引入色差缺陷。
L≤50,W≤0.5,N≤2或S≤50,N≤1,且修补后不能有明显色差。
杂点
不允许
不允许
S≤2,N≤2
3.9喷涂件检验内容
序号
检验
项目
技术要求
检验方法
抽样
方法
检测
工具
1
外观
喷涂件
A、B级表面涂层应均匀、连续、色泽一致,没有结瘤、缩孔、起泡、针孔、开裂、剥落、粉化、颗粒、流挂、露底、肥边、磷化液、划伤、杂色、夹杂物、毛边、保护不齐等缺陷。
目测外观,可参照《喷涂表面缺陷允收表》
全检
目测
2
厚度
喷粉件
砂纹粉末:
60—130μm
橘纹粉末:
70—150μm返修件不能超出250微米,具体的厚度值应保证涂层外观纹路一致,若技术要求存在防腐等级要求,涂层厚度值应按照该种产品的具体质量要求进行控制。
注:
重点合同要求进行全检。
测厚仪测量
2件/种
测厚
仪
喷漆件
钢铁件:
普通(标准)防腐:
70-120μm;重防腐:
90-150微米;超重防腐:
120-180μm。
铝质件:
一般防腐:
35-55μm,重防腐70-120μm,超重防腐:
90-150μm。
作为装饰性用途的铝制品,喷漆厚度以表面色泽一致、不露底为主,喷漆厚度不做为考量。
注:
若技术要求存在防腐等级要求或者明确厚度时,涂层厚度值应按照该种产品的具体质量要求进行控制。
重点合同要求进行全检;厚度值原则上不能低于下限值。
2件/种
3
颜色
喷涂件
工件之间应保证没有明显颜色差别,若存在问题无法定论时,可借助色差仪与标准色板对照进行判断。
白色、浅灰色系色差值△E0.8;深灰色、蓝色、红色系色差值△E1.2;黑色系色差值△E2.0
目测,存在问
题时借助色
差仪判断
2件/种
色差
仪
4
丝孔及螺钉保护
喷涂件
1、M8以下丝孔喷涂之后必须采取过丝处理,过丝后,要求丝孔内部没有涂层;2、M8(含M8)以上要求进保护,去保护后要求丝孔内没有涂层。
3、螺钉保护后要求螺纹表面没有涂层
目测
2件/种
目测
5
过程
参数
控制
喷涂生产线参数
1、生产链速合乎工艺要求;
2、烘干、固化炉温符合工艺要求;
3、槽式前处理槽液温度符合工艺要求
4、前处理槽液参数化验合乎工艺要求注:
各项工艺参数详见各生产线参数控制表格
目测
1次/天
目测
6
附着
力
喷涂件
1、在喷粉线固化炉温出现低于下限值20℃时,
对于加工后的产品要做附着力检验,附着力等级要求在1级以上。
2、喷漆件(非平高产品)随合同对工件附着力进行抽检;平高客户产品要求每面屏体进行附着力划格试验。
附着力等级要求在1级以上。
划格试验
随机
刀片
及附着力胶带
表1:
表面大小类别划分
表面大小
标准划分
按面积
按最大外形尺寸
小
检测面积≤6400mm2
最大尺寸≤300mm
中
6400<检测面积≤48600mm2
300<最大尺寸≤600mm
大
48600<检测面积≤97200mm2
600<最大尺寸≤1000mm
超大
97200<检测面积≤360000mm2
1000<最大尺寸≤1500mm
表2:
非喷涂件产品外观缺陷的可接受范围
外观缺陷类型
表面
大小
缺陷所处表面类型
合格范围
A级表面
B级表面
外部表面内部表面
基材花斑
不限
金属表面
不允许
S(缺陷面积的总和)≤被测面积的5%
抛光区
小
金属表面
不允许
S≤100且P≤2
不限制
中
S≤100且P≤2
不限制
大
S(总面积)≤被测面积的5%
水印
小
电镀、氧化
不允许
S≤3.0且P≤2
不限制
中
S≤1.0且P≤2
大
S≤3.0且P≤2
不限
压铸
S≤10.0且P≤2
不限制
水纹
缩水
不限
塑胶、压铸
按对应的样件标准,程度应轻于样件
气泡
不限
透明塑胶
不允许
直径≤0.3,P≤4
小
不透明塑胶
不允许
中
直径≤0.3,P≤4
披锋
不限
塑胶、压铸
目视无披锋,手摸不刮手
手摸不刮手
板材冲裁
目视无披锋,手摸不刮手
毛刺允许高度≤
0.2mm
砂眼
不限
压铸
直径≤0.5,P≤4
S≤1.0且P≤4
塑胶
直径≤0.3,P≤4
S≤0.5且P≤4
裂纹
不限
压铸
不允许
不允许
塑胶、尼龙
不允许
不允许
热处理零件
不允许
不允许
露白
不限
镀锌彩色钝化
不允许
S≤4.0且P≤3
黑点
不允许
S≤1.0且P≤3
雾状
不限
镀铬、镀镍、透明表面
不允许
S≤100且P≤2
铜排镀镍
S≤100,P≤2
不限制
局部无
铬层
不限
镀铬
不允许
允许在深孔内壁、凹陷区、内角部位等低电位区出现。
挂具印
小
电镀、氧化
不允许(当只有A级表面时按3.3.8段)
S≤1.0且P≤4
中
S≤2.0且P≤4
大
S≤3.0且P≤4
修补
不限
电镀、氧化
颜色、光泽与原膜层目视无明显差异,S≤4.0且P≤3
颜色、光泽与原涂层目视允许有轻微差异,S≤20.0且P≤3
镀前划痕(手
小
金属表面(但不包括拉丝及喷
L≤15且P≤2
L≤20且P≤3或
L≤40且P≤1
不限制
感无凹入或极轻微凹入)
中
砂面)
L≤20且P≤3或L≤40
且P≤1
L≤20且P≤5或
L≤40且P≤3以及
L≤80且P≤1
大
L≤20且P≤5或L≤40且P≤3以及
L≤80且P≤1
L≤40且P≤5以及
L≤150且P≤1
超大
L≤40且P≤5以及
L≤150且P≤1
L≤300且P≤3
镀前划痕(手感有明显凹入)
小
不允许
L≤40且P≤3
中
L≤20且P≤3或L≤40且P≤1
L≤20且P≤5或
L≤40且P≤3以及
L≤80且P≤1
镀前划痕(手感无凹入)
不限
拉丝及喷砂面
L≤15且P≤2
L≤20且P≤3
不限制
异物
小
所有
不允许
S≤1.0,P≤6
中
S≤0.2且P≤2
大
S≤0.3且P≤4
颗粒
小
所有
S≤0.3且P≤1
S≤1.0且P≤3以及S≤3.0且P
≤2
中
S≤0.3且P≤3或S≤0.5且P≤2或S≤0.7且P≤1
大
S≤0.5且P≤3或S≤0.7且P≤2或S≤1.0且P≤1
超大
S≤1.0且P≤3或S≤1.5且P≤2或S≤2.0且P≤1
注①:
表中的L表示单个缺陷长度,单位为“mm”;