PPRouting工艺路线的分解数与工作中心单项能力.docx
《PPRouting工艺路线的分解数与工作中心单项能力.docx》由会员分享,可在线阅读,更多相关《PPRouting工艺路线的分解数与工作中心单项能力.docx(9页珍藏版)》请在冰点文库上搜索。
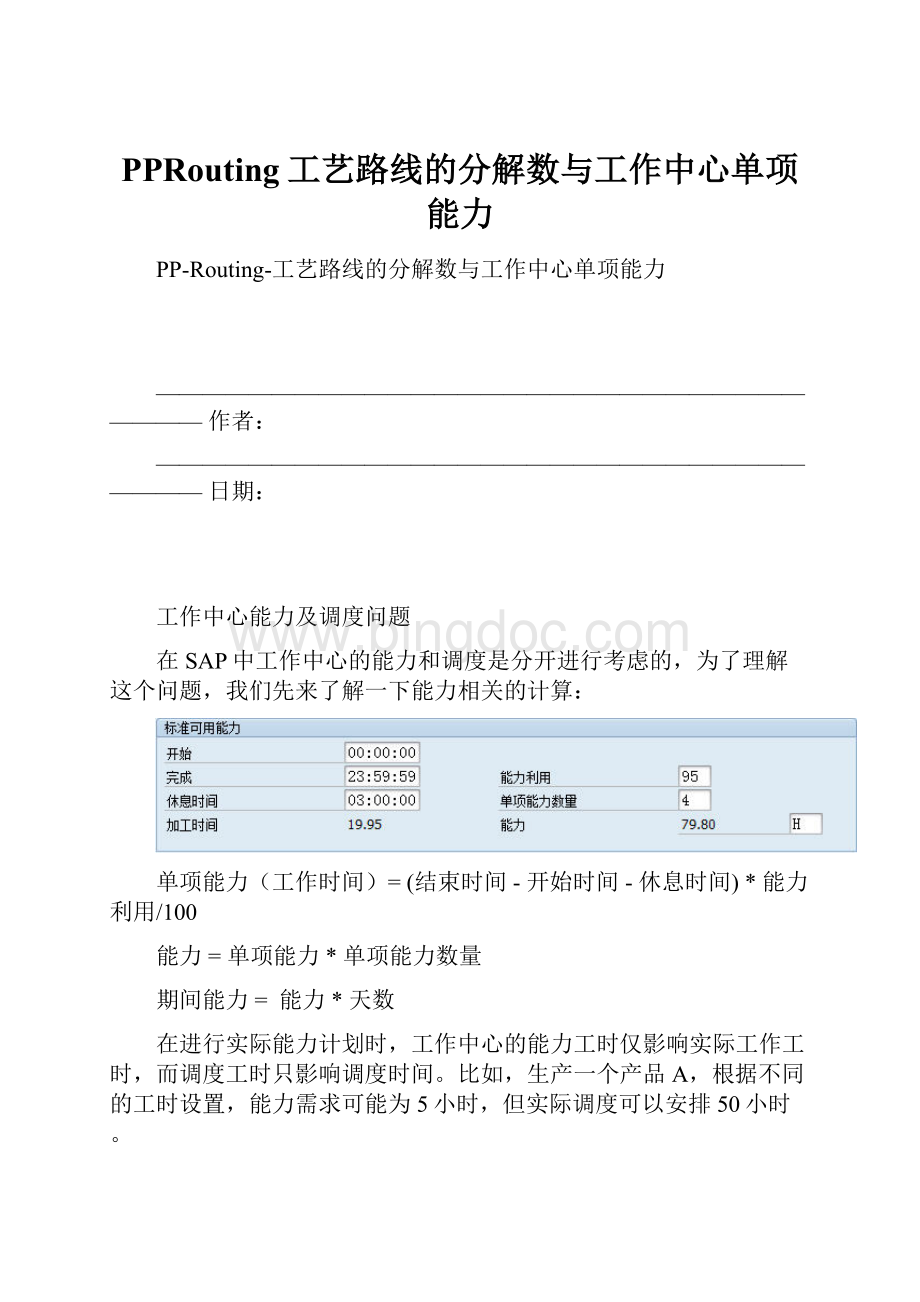
PPRouting工艺路线的分解数与工作中心单项能力
PP-Routing-工艺路线的分解数与工作中心单项能力
————————————————————————————————作者:
————————————————————————————————日期:
工作中心能力及调度问题
在SAP中工作中心的能力和调度是分开进行考虑的,为了理解这个问题,我们先来了解一下能力相关的计算:
单项能力(工作时间)=(结束时间-开始时间-休息时间)*能力利用/100
能力=单项能力*单项能力数量
期间能力= 能力*天数
在进行实际能力计划时,工作中心的能力工时仅影响实际工作工时,而调度工时只影响调度时间。
比如,生产一个产品A,根据不同的工时设置,能力需求可能为5小时,但实际调度可以安排50小时。
下面我们来具体看看能力和调度的相关计算,以下以加工工时为例:
假设工作中心的单项能力为20,单项能力数量为5,则工作中心能力为100。
有一个产品A,工艺路线中定义基本数量为100PC,工序工时为1,工序分解数为5。
现需要生产10000PC的产品A,能力需求和调度时间(计划加工跨度时间)如下:
场景1:
能力分解、调度分解
能力加工工时公式=工时*工序数量/基本数量/工序分解
调度加工工时公式=工时*工序数量/基本数量/工序分解
能力需求=20H
调度时间=20H
负荷率=20%
场景2:
能力不分解、调度分解
能力加工工时公式=工时*工序数量/基本数量
调度加工工时公式=工时*工序数量/基本数量/工序分解
能力需求=100H
调度时间=20H
负荷率=100%
场景3:
能力分解、调度不分解
能力加工工时公式=工时*工序数量/基本数量/工序分解
调度加工工时公式=工时*工序数量/基本数量
能力需求=20H
调度时间=100H
负荷率=20%
工作中心和工艺路线
工作中心和工艺路线是PP的重要环节。
创建工作中心,不是根据具体的地点、设备、人员,而是根据类型。
将同类型的生产模块化,以便于统计能力、进行排产和收集成本。
创建工作中心过程中,工作中心的类型其标识作用,一般分机器和人工。
其中“能力”标签下,是设定最大产能用的,其公式统计的是总机时/工时,填写开始时间、完成时间、休息时间,再根据机器或人员的数目设置单项能力数。
“调度”标签则用于排产,即设定该工作中心的能力需求是取决于机器还是工时,公式统计的是分解后的生产需时。
“成本核算”标签则为收集成本服务,若只添加其中一项(PRM/LRM),则只统计该项能力。
创建工艺路线比较麻烦的是机时、工时的统计,一般用单位时间(1天、1小时)除于产量得出。
须注意,调度能力的时间决定了另一能力的时间。
当然,这里的机时、工时,跟排产和成本的计算都有关系。
该处,“拆分”是指分解成多少条线去生产,只影响排产(时间),不影响成本(价值)。
拆分与单项能力数没有必然的关系。
生产订单上的时间及计划相关配置
2013/05/22 REVERFELEAVEACOMMENT
要了解生产订单上的各种时间及计算,首先我们需要了解一下基础的概念。
提前期Leadtime
是指作业开始到作业结束中间所需要的时间,即生产或采购一个产品,包含材料采购,生产加工等,直至满足需求所需要的所有时间,以是MRP运算中的一个重要数据来源和产出。
对于整个生产周期而言,提前期可分为设计提前期,采购提前期,加工提前期,装配提前期等,总计称为总提前期。
基本时间BasicDates
基本的开始和结束时间里面包含了产前产后缓冲期和生产计划的时间。
计划时间Scheduled
计划中生产(工序)应该开始和结束的时间
工作中心公式WorkCenterFormula
将工序时间进行一定的计算,可以用以能力计划,调度和成本计算。
一般来说常见的公式形式是:
=工时*工序数量/基本数量/工序分解
(工序数量:
订单上的生产数量;
基本数量:
工艺路线上的基本数量;
工序分解:
能够进行并行处理的数量,一般来说参考工作中心里的单项能力数,在工艺路线中需要勾选“需要分解”,如果没有输入最大分解数,则默认取单项能力数)
接下来,我们一层一层的分析生产订单上的时间计算逻辑。
这里“Backwards”计划为例
基本结束时间(10.06.201300:
00)-产后缓冲期(4)=计划结束时间(03.06.201317:
30)
计划结束时间(03.06.201317:
30)-工艺计划的处理时间(计算见下文)=计划开始时间(03.06.201313:
01)
计划开始时间(03.06.201313:
01)-产前缓冲期
(2)=基本开始时间(30.05.201300:
00)
基本开始时间(30.05.201300:
00)-下达期间(6)=计划下达期间(24.05.2013)(下达期间有考虑非工作日)
其他的计划类型,比如向前,当前日期等同先后计划类似。
配置
主要是有两点,1.是否调整基本时间,2.相关需求产生的日期
基本时间是一个粗略的时间,配置是否需要参考计划时间调整基本时间。
以上面为例
设置为不调整基本时间,去除浮动值,再计划得到如下结果
可以看到基本时间没有发生变化,而计划时间都做了相应的调整。
然后设置为调整计划时间,再计划得到如下结果
可以看到此刻基本时间也发生了改变
至于相关需求的配置就比较好理解了,即相关需求的产生日期是在订单开始日期(基本开始时间),还是在工序开始日期(计划开始时间)
下面我们再介绍一下工序时间的计划,即工艺计划的处理时间,这里用到的公式是调度公式即Schedulingformula。
首先我们看一下工作中心的配置
能力类别维护的002person,我们需要根据其能力确定计划
处理公式这里只维护了一个(工时*工序数量/基本数量/工序分解),意味着计划时只会考虑standardLabor1。
另外需要提及的是跳读公司间一般都会考虑工序分解数Operationsplits。
能力的维护信息如下
单项能力数实际上并不直接体现在公式中,而能力的分解使用的时工序分解数,这点需要特别的主意。
在订单中
要实现工序的分解还必须勾选“Requiredsplitting”
计算步骤如下
Processingtime=standardLabor1(8)*operationquantity
(1)/Basequantity
(1)/Operationsplits(2<-未限制,默认为单项能力数)=4
系统结果
和计算结果相符。