机械创新设计实例分析.ppt
《机械创新设计实例分析.ppt》由会员分享,可在线阅读,更多相关《机械创新设计实例分析.ppt(31页珍藏版)》请在冰点文库上搜索。
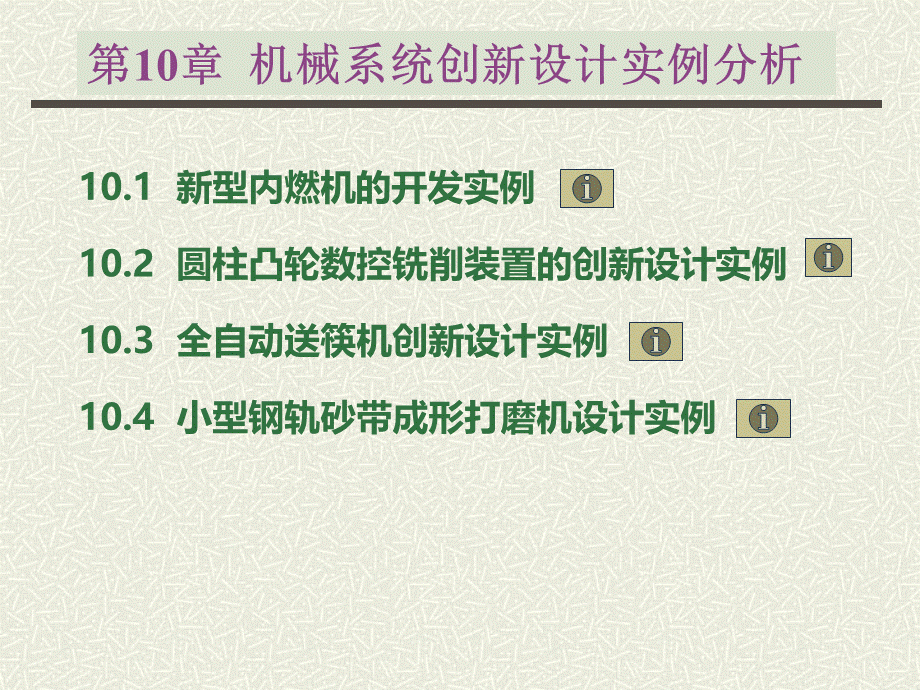
第10章机械系统创新设计实例分析,10.1新型内燃机的开发实例,10.2圆柱凸轮数控铣削装置的创新设计实例,10.3全自动送筷机创新设计实例,10.4小型钢轨砂带成形打磨机设计实例,10.1新型内燃机的开发实例,本实例就新型内燃机开发中的一些创新技法(运用类比、组合、替代等创新技法)进行简单分析。
1.往复式内燃机的技术矛盾,目前,应用最广泛的往复式内燃机由气缸、活塞、连杆、曲轴等主要机件和其他辅助设备组成。
活塞式发动机工作时具有吸气、压缩、做功(燃爆)、排气4个冲程,做功冲程输出转矩,对外做功,活塞1连杆2气缸3曲轴4进气阀5排气阀6,这种往复式活塞发动机存在以下明显的缺点。
(1)工作机构及气阀控制机构组成复杂,零件多;曲轴等零件结构复杂,工艺性差。
(2)活塞往复运动造成曲柄连杆机构较大的往复惯性力,此惯性力随转速的平方增长,使轴承上的惯性载荷增大,系统由于惯性力不平衡而产生强烈振动。
往复运动限制了输出轴转速的提高。
(3)曲轴回转两圈才有一次动力输出,效率低。
上述问题引起了人们改变现状的愿望,社会的需求促进产品的改造和创新,多年来,在原有发动机的基础上不断开发了一些新型发动机。
2.无曲轴式活塞发动机,无曲轴式活塞发动机采用机构替代的方法,以凸轮机构代替发动机中原有的曲柄滑块机构,取消原有的关键件曲轴,使零件数量减少,结构简单,成本降低。
单缸无曲轴式活塞发动机,10.1新型内燃机的开发实例,一般圆柱凸轮机构是将凸轮的回转运动变为从动杆的往复运动,而此处利用反动作,即当活塞往复运动时,通过连杆端部的滑块在凸轮槽中滑动而推动凸轮转动,经输出轴输出转矩。
活塞往复两次,凸轮旋转360。
系统中没有飞轮,控制回转运动平稳。
这种无曲轴式活塞发动机若将圆柱凸轮安装在发动机的中心部位,可在其周围设置多个气缸,制成多缸发动机。
通过改变圆柱凸轮的凸轮轮廓形状可以改变输出轴的转速,达到减速增矩的目的。
这种凸轮式无曲轴发动机已用于船舶、重型机械、建筑机械等行业。
10.1新型内燃机的开发实例,3.旋转式内燃发动机,在改进往复式发动机的过程中,人们发现如果能直接将燃料的动力转化为回转运动必将是更合理的途径。
类比往复式蒸汽机到蒸汽轮机的发展,许多人都在探索旋转式内燃发动机的建造。
1)旋转式发动机的工作原理汪克尔所设计的旋转式发动机简图如图所示,它由椭圆形的缸体1、三角形转子2(转子的孔上有内齿轮)、外齿轮3、吸气口4、排气口5和火花塞6等组成。
旋转式发动机简图,10.1新型内燃机的开发实例,旋转式发动机在运转时同样也有吸气、压缩、燃爆(做功)和排气4个动作。
吸气:
AB弧所对的内腔容积由小变大,产生负压效应,由吸气口将燃料与空气的混合气体吸入腔内。
压缩:
内腔由大变小,混合气体被压缩。
燃爆:
高压状态下,火花塞点火使混合气体燃爆并迅速膨胀,产生强大的压力驱动转子,并带动曲轴输出运动和转矩,对外做功。
排气:
内腔容积由大变小,挤压废气由排气口排出。
10.1新型内燃机的开发实例,2)旋转式发动机的设计特点
(1)功能设计。
内燃机的功能是将燃气的能量转化为回转的输出动力,通过内部容积变化,完成燃气的吸气、压缩、燃爆和排气4个动作以达到目的。
旋转式发动机抓住容积变化这个主要特征,以三角形转子在椭圆形气缸中偏心回转的方法达到功能要求。
而且三角形转子的每一个表面与缸体的作用相当于往复式发动机的一个活塞和气缸,依次平稳地连续工作。
转子各表面还兼有开闭进排气阀门的功能,设计可谓巧妙。
(2)运动设计。
偏心的三角形转子如何将运动和动力输出?
在旋转式发动机中采用了内啮合行星齿轮机构,如图所示。
行星齿轮机构,10.1新型内燃机的开发实例,三角形转子相当于行星内齿轮2,它一面绕自身轴线自转,一面绕中心外齿轮1在缸体3内公转,系杆H转子内齿轮与中心外齿轮的齿数比是1.51,这样转子转一周,使曲轴转3周,输出转速较高。
根据三角形转子的结构可知,曲轴每转一周即产生一个动力冲程,相对四冲程往复式发动机,曲轴每转两周才产生一个动力冲程,可知旋转式发动机的功率容量比是四冲程往复式发动机的两倍。
(3)结构设计。
旋转式发动机结构简单,只有三角形转子和输出轴两个运动构件。
它需要一个化油器和若干火花塞,但无须连杆、活塞以及复杂的阀门控制装置。
零件数量比往复式发动机少40%,体积减少50%,重量下降1/22/3。
10.1新型内燃机的开发实例,3)旋转式发动机的实用比旋转式发动机与传统的往复式发动机相比,在输出功率相同时,具有体积小、重量轻、噪声低、旋转速度范围大以及结构简单等优点,但在实用化生产的过程中还有许多问题需要解决。
随着生产科学技术的发展,必然会出现更多新型的内燃机和动力机械。
人们总是在发现矛盾和解决矛盾的过程中不断取得进步。
而在开发设计过程中敢于突破,善于运用类比、组合、替代等创新技法,认真进行科学分析,将会使人们得到更多创新的、进步的、高级的产品。
10.1新型内燃机的开发实例,10.2圆柱凸轮数控铣削装置的创新设计实例,本实例就圆柱凸轮加工原理开发中运用综合创新技法、反求创新法,通过创造性的综合和巧妙的构思,使综合体发生质的飞跃,做了简单的说明,从而体现出综合创新是一种更具实用性的创新思路。
1.设计目的,圆柱凸轮作为一种机械传动控制部件,具有结构紧凑、工作可靠等突出优点,但其加工制作比较困难。
东北大学东软集团生产的医用全身CT扫描机,有一对复杂的圆柱凸轮,过去一直采用手工加工,不仅制造精度低,而且劳动强度大,生产效率低,成本高。
为此,负责机械加工的东北大学机械厂提出要研制一种精度较高、操作方便、成本较低的圆柱凸轮加工装置,故于2002年年末,其成立了跨年级的研究小组,开始对这一问题进行研究。
经过一年多的时间,完成了圆柱凸轮数控铣削装置的综合创新设计,由东北大学机械厂完成制造,并成功地投入使用,满足了圆柱凸轮加工的精度和生产率的要求。
圆柱凸轮数控铣削装置包括工作台直线运动坐标轴和工件回转运动坐标轴,在加工圆柱凸轮时,本装置根据数控加工程序控制工件作旋转进给运动和直线进给运动,通过普通立式铣床工作台的垂直运动进行切深调整,这样就可以实现一条凸轮曲线槽的连续自动化加工。
本装置的传动原理如图所示。
圆柱凸轮数控铣削装置传动原理图,本装置由简易CNC装置控制驱动器,驱动两个高精度步进电动机,两个电动机分别控制分度头的转动和滚珠丝杠的直线运动,由分度头带动工件做回转进给运动,滚珠丝杠则带动工作台做直线方向的进给运动,由普通立式铣床进行切深调整,从此实现了一条凸轮槽的连续加工。
2.工作原理,10.2圆柱凸轮数控铣削装置的创新设计实例,3.设计方案在方案设计阶段,通过对圆柱凸轮的各种加工方案进行深入的分析研究得出:
对于复杂的、多导程圆柱凸轮,理想的加工方法是采用带回转台的四轴立式加工中心或带自驱动式铣刀的车削中心加工,但这两种机床价格昂贵,东北大学机械厂近期难以购买这两种机床。
创新思路拟在普通立式铣床上,加装高精度数控装置,将传统的机械技术与现代高新数控技术和电子技术等有机地综合在一起,从而实现高精度的可靠加工要求。
因此根据数控技术越来越普及以及简易数控系统价格比较便宜的现状和特点,东北大学机械厂决定设计一个简易的圆柱凸轮数控铣削装置。
将该装置放置在普通立式铣床上,由普通立式铣床的主轴做切削运动,由其工作台的垂直方向运动进行切深调整,该装置则根据数控加工程序控制工件做旋转进给运动和直线进给运动,实现一条凸轮曲线槽的连续自动化加工。
这种加工方法成本很低,加工自动化程度较高,操作方便,加工精度高,且能满足圆柱凸轮不断改型的要求。
10.2圆柱凸轮数控铣削装置的创新设计实例,4.功能及特点,
(1)圆柱凸轮数控铣削装置包括工作台直线运动坐标轴(Z轴)和工件回转运动坐标轴(X轴),采用德国BERGERLAHR高精度步进电动机驱动,德国ENGELHARDT两轴CNC系统控制。
X向脉冲当量为0.0009;Z向脉冲当量为0.001mm,可以完成圆柱凸轮复杂凸轮槽的连续、自动化加工。
(2)工件回转运动(即X轴)的机械传动由普通分度头完成,其蜗杆涡轮的降速比大(i=40)、传动精度高、价格便宜。
(3)工作台的直线运动(即Z轴)采用双螺母垫片式滚珠丝杠螺母传动,并采用滚珠导轨支承,其摩擦力小、运动灵敏、精度高、刚度大。
(4)数控编程采用CAD/CAM一体化编程方法。
在CAXA/ME的支持下,首先绘制圆柱凸轮的展开曲线,然后生成G代码程序,最后利用R232接口将加工程序传输给数控系统。
编程过程精确、直观、方便、灵活。
该装置可完成各种圆柱凸轮的精确自动化加工,另外还可以加工各种平面凸轮。
10.2圆柱凸轮数控铣削装置的创新设计实例,5.主要创新点,
(1)工件回转运动采用标准分度头传动,简化了设计制造,降低了研制成本。
在研制过程中,通过分析对比选择了合理的驱动位置,保证了传动精度,这种方法在国内尚属首次。
(2)工作台的直线运动采用先进的滚珠丝杠传动,并采用滚动导轨支承,其传动灵活、精度高、刚度大。
(3)该装置采用简易CNC系统控制,采用CAD/CAM一体化编程,选择廉价的CAXA/ME作为支撑软件,利用反求设计创新思维进行了创新改造,并进行了二次开发,对编程方法进行了合理的改进,使数控编程精确、直观、方便、灵活。
因而其操作方便,使用灵活,能满足各种圆柱凸轮的加工。
(4)该装置可在普通铣床上完成各种复杂圆柱凸轮曲线的精确、高效、自动化加工,其操作方便、价格低廉。
此外,该装置也可用于各种平面凸轮的加工,因此颇具推广应用价值。
该装置已在东北大学机械厂投入使用,,10.2圆柱凸轮数控铣削装置的创新设计实例,10.3全自动送筷机创新设计实例,本实例就开发新型全自动送筷机采用的创新思维(新型、实用、快捷)和创新技法(系统分析法、组合创新法、形态分析法、机构构型创新设计法等)作了一些简单的介绍,以期对创新设计有所启发。
1.设计目的学生每天到食堂就餐都得从筷筒里胡乱地抓取筷子,这样既不方便又不卫生,久而久之便萌发了设计一种自动送筷机的灵感。
如图所示为全自动送筷机外观图。
2.设计过程,初定的送筷方式(利用系统分析法和形态分析法进行论证分析)有3种:
朝上竖直送;水平横向送;水平竖向送。
通过反复多次模拟实验发现,朝上竖直送取筷子最为方便,但筷子的水平移动距离长,所需水平推力也大,会导致机器的结构复杂,成本增加。
水平横向送筷子,由于筷子尺寸、形状、大小及摆放的不规则,能顺利取出筷子的概率不足30%。
而水平竖向送筷子不仅出筷顺畅,而且在抽出筷子后,在重力作用下筷子会自由下落,省去了机械传动成本,这种方式取筷也比较方便。
因此,最终选择了第三种方案。
1)送筷方式的确定,10.3全自动送筷机创新设计实例,2)出筷机构的选择可供选择的出筷机构(利用机构组合创新法和机构构型创新设计进行分析)有盘形凸轮机构、摆动导杆机构、曲柄摇杆机构、曲柄滑块机构等。
通过模拟实验,分析对比,发现盘形凸轮机构虽然结构简单,但由于从动件行程较大(70mm),使机构的总体结构尺寸过大;曲柄摇杆和导杆机构不仅平稳性较差,而且占据的空间也大;而曲柄滑块机构占据的空间最小,结构比较简单。
因此,最后确定用曲柄滑块机构与移动凸轮组合机构作为出筷的执行结构,如图所示。
10.3全自动送筷机创新设计实例,3)电动机的选择通过模拟实验测定推筷子的阻力和最佳的出筷子速度,从而确定电动机的功率为25W,减速电动机的输出转速为60r/min。
3.工作原理,当曲柄滑块机构运动时,滑块带动移动凸轮(阶梯斜面)反复移动,将筷子水平送出。
推出的一截筷子如果未被取走,则移动凸轮空推,已推出的筷子静候抽取。
如果推出的筷子被取走,则上方的筷子在重力作用下会自由下落到箱体底部,而被再次推出,如图所示。
阶梯推杆推筷示意图,10.3全自动送筷机创新设计实例,设计阶梯推杆的目的:
一是提高送筷子的效率;二是防止筷子由于摆放不规则,出现卡死、架空等现象。
初定的推杆只能推一双筷子,不仅效率低,而且经常出现卡死、架空等现象。
阶梯推杆推出的3双筷子成并排阶梯状。
伸出箱体最长的筷子被抽取走后,如果上方筷子不能自由下落,则再抽取伸出较短的一双,如果抽走后上方的筷子还不能自由下落,则再抽走最短的第三双筷子,由于3双筷子较宽,故3双都抽走后,上方筷子必然失去支撑而下落到箱体底部。
阶梯推杆斜面的作用:
一是起振动作用;二是防止筷子未对准出口时被顶断,如图所示。
当筷子未对准出口、顶在箱体壁上时,筷子在阶梯推杆的斜面上滑过。
经过多次作用,只有筷子对准出口时才能被顶出。
斜面推杆作用示意图,10.3全自动送筷机创新设计实例,4.主要创新点,1)产品创新该产品属国内外首创,经过市场调查及网上查询,国内外还没有自动出筷机等自动出筷装置。
由于市场容量很大,产品又获得专利权,投放市场后将取得良好的社会及经济效益。
2)机构创新点将曲柄滑块机构与移动凸轮机构(阶梯斜面推杆)有机组合,能实现多项功能:
一是机构组合本身结构非常简单、紧凑,可大幅度降低成本及机器的结构尺寸;二是阶梯推杆可有效地防止筷子被卡住而不能自由下落的现象;三是斜面推杆能有效防止筷子未对准出口而被机器顶断的现象;四是斜面推杆可适用所有不同横截面的筷子。
10.3全自动送筷机创新设计实例,10.4小型钢轨砂带成形打磨机设计实例,本实例就小型钢轨成形打磨机更新再设计所采用的创新设计思维(反求设计、移植创新设计等)以及运用的创新技法(组合变异创新技法、功能设计创新法等)作介绍说明。
1.设计背景,火车钢轨是轨道结构最重要的部件,它直接承受车辆载荷。
由于长时间运行,致使轨道表面疲劳点蚀和磨损破坏,圆弧部分压溃为不规则形状及侧面形成毛刺等。
钢轨打磨技术可以用来消除钢轨的波形磨耗、车轮擦伤、钢轨端部裂纹、接头的马鞍形磨耗和轨道表面裂纹萌生,控制钢轨表面接触疲劳的发展。
因此,钢轨打磨是铁道建设和养护的重要措施,随着高速、重载列车的运行,钢轨打磨变得尤为重要。
目前铁路线路维修用于钢轨打磨的机具主要分为两类:
一是进口的大型钢轨打磨列车;二是各铁路单位自行研制的小型钢轨打磨机。
二者均是以砂轮为磨具,在现场使用中,这两类打磨工具分别存在着一些不足:
前者价格昂贵、能耗大、砂轮耗材大等;后者的功能和应用多限于小范围、离散病害点的单一性病害的修理性打磨,而且因结构局限性,不能打磨道岔,对钢轨顶面、侧面和圆弧联结部分须分次打磨,打磨效率低,无法打磨出较理想的标准钢轨端部的复杂廓面。
因此,设计出一种实用可靠、效率高的小型打磨机很有必要。
2.创新构思及设计过程,1)打磨机的设计要求产品的性能要求来自市场以及用户的需求。
根据调研发现,铁路现场对小型打磨机的性能要求主要有以下内容。
10.4小型钢轨砂带成形打磨机设计实例,
(1)安全实用,轻便,两人能搬动。
(2)能打磨道岔。
(3)能较准确打磨标准钢轨轮廓面。
(4)打磨效率高、质量好,调节方便。
上述性能要求中的大部分是现有小型打磨机所不具备的,也就是新型打磨机应达到的主要功能要求。
2)设计过程
(1)总体创新构思。
在小型打磨机的总体构思中,突破原产品的约束,提出以下创新点。
采用移植创造原理,把切削加工中的砂带磨削技术引入打磨机的设计中,变刚性打磨为柔性打磨,从而改善磨削质量。
在柴油机气缸盖等复杂曲面砂带磨削装置的诱导启发下,构思出快速、准确打磨钢轨轮廓面的成形打磨头。
10.4小型钢轨砂带成形打磨机设计实例,现有小型砂轮打磨机都是单轨行驶,由于道岔宽度等于单轨宽度,所以不能打磨道岔,为此运用变性创造原理和技法,设计出双轮行走部分,解决了打磨道岔的问题。
在上述创新构思基础上,通过功能设计法设计出小型砂带打磨机,其总体方案如图所示。
该打磨机由打磨系统和行走系统两部分组成。
打磨系统安装在滑板6上,滑板可在导轨上移动,导轨固定在带4个行走轮的减振底盘上。
滑板移动至预定位置,可通过锁紧机构10加以固定。
两个打磨头4经两个带滚动轴承的多片摩擦离合器3分别由两台汽油机2驱动,打磨头与钢轨相对接触位置的调节和锁定由竖直方向和轨距方向的螺旋调节机构进行。
底盘轮轴上装配可调间隙的圆柱滚子轴承,使打磨机通过时其曲线具有随轨自适性。
打磨机传动示意图,10.4小型钢轨砂带成形打磨机设计实例,该打磨机的执行动作为:
将打磨机推至工作区间,放下接触轮,然后预调打磨头与钢轨的接触位置。
根据钢轨病害诊断结果(由专门设备完成),确定分次打磨的实际切深,再细调并锁定,最后开机至一定转速,合上离合器,开始打磨。
打磨机由人力推动进给,打磨效果用专门的检验设备检验。
(2)打磨磨具的移植创新。
与砂轮磨削相比,砂带磨削有如下特性。
高效:
磨削效率为砂轮磨削的4倍以上。
低耗:
一般情况下,砂轮旋转运动所消耗的能量占总功率的15%20%,而维持砂带运动的功率占4%10%,工作时,磨削热低。
适用范围广:
可打磨各种钢轨及进行各种复杂形面的修整。
磨削质量好:
表面粗糙度值可小于Ra(0.10.5),在工件表面的残余应力状态及微观裂纹等方面,优于砂轮磨削。
寿命较高:
由于涂附磨料,模具达到新发展和静电植砂砂带的使用,以及抗“粘盖”添加剂的使用,砂带使用寿命可达1012h。
10.4小型钢轨砂带成形打磨机设计实例,因此,在打磨机功能实现上,完全可以引入砂带磨削技术,但它也有下列问题需通过进一步的试验才能解决,即砂带选型、最佳砂带打磨速度、最佳打磨进给量、最佳行走速度等。
(3)成形打磨头部件的相似诱导移植设计。
为了提高打磨效率和打磨质量,在创新构思的基础上,对成形打磨构件进行了相似诱导移植技术设计。
相似诱导移植指的是借助类似或相近的结构和技术,移植相似元中的部分要素或全部要素,结合当前的具体问题,使求解该问题的有用信息幅度大大增加,以至于形成突发性灵感思维,从而获得当前问题的解决。
如图所示为打磨头传动示意图,图中:
驱动轮1、张紧轮2和接触轮3为实体式,以钢、铝材料为轮芯,外包弹性橡胶等耐磨材料制成,其外缘硫化一层耐磨的耐油胶料。
打磨头传动示意图,10.4小型钢轨砂带成形打磨机设计实例,张紧轮和接触轮采用凹形结构,如图(a)所示,形状与钢轨轮廓相似,以减少砂带在打磨过程中的变形次数,提高寿命;接触轮的轮廓曲线采用仿轮缘踏面曲线,如图(b)所示,X锯齿形外缘,并在轮缘上沿圆周方向开平行的环形沟槽,即消气槽,以防止运行中砂带憋气,同时可增加摩擦力,提高磨削质量和效率。
接触轮的硬度在4070HS(A)之间。
轮的外形轮廓图,在图所示的砂带张紧快换机构中。
砂带通常在张紧状态下工作,因此在砂带由于受热等因素的影响变长后,必须进一步张紧。
10.4小型钢轨砂带成形打磨机设计实例,砂带张紧快换机构,砂带的张紧通过改变张紧轮与驱动轮之间的中心距来实现,现采用弹簧手柄式砂带快换机构来实现砂带磨削中的张紧,其机构运动原理如下:
转动手柄1、带动拉杆3,使支架4在支杠10中左右移动。
若支架带动张紧轮6向右压缩弹簧2,则缩短了张紧轮和驱动轮的中心距,便于装卸砂带,反之,弹簧推动支架张紧砂带。
为保证张紧可靠,在调整后用螺钉5将支架与支杠固定。
图10.20中的7和9是用于张紧轮调偏的螺钉和螺栓,调偏采用扁轴调偏结构。
10.4小型钢轨砂带成形打磨机设计实例,如图所示为磨削量进给调节机构,其为竖直方向的螺旋调节机构,用以控制接触轮与钢轨的正确接触和施力。
设计中采用结构简单、易于自锁、转运平稳的差动螺旋装置。
图中,支架1上的螺纹与手轮螺杆7的螺纹构成一螺旋副,与接触轮6联接在一起的螺母4中的螺纹与螺杆7的螺纹构成另一螺旋副,两螺旋副组成差动螺旋机构。
套筒3通过螺钉2与支架1固联为一体,螺母4可在套筒3内移动。
为了使打磨接触轮工作可靠,在调整结束后,应用紧定螺钉5将螺母4固定在套筒3上。
磨削量进给调节机构,10.4小型钢轨砂带成形打磨机设计实例,小结上述的4个典型创新设计实例中,全自动送筷机是从工作原理进行创新,内燃机是从实现相同工作原理的不同机构入手创新尝试,其他两个设计实例一是利用反求新思维进行了创新改造,二是利用移植原理进行设计,机械发展史中有无数的创新事例,并不可能一一例举,而是以上述典型实例举一反三、启迪思维,点燃学习者创新设计智慧的火花。
期终考查创新报告(论文),利用所学到的创新思想、原理、方法进行一项机械(或其它)创新设计,据创新内容自定题目写一篇创新报告或论文。
具体如下:
1.前言:
创新的背景(现有机械存在的问题、所要解决的问题等)、意义。
2.创新内容和过程2.1创新所依据的思想、原理、方法2.2创新的原理方案2.3创新的结构方案(手工正规绘制或CAD绘制;越详细越好;若是机构创新,须计算自由度)2.4设计说明书3.总结或结论(创新解决了那些问题、归结创新点,创新尚存在的不足和问题,展望解决办法和今后努力的方向)注:
要体现独创性,禁止克隆拷贝;思想要端正、积极,书写仔细工整(可打印);字数大于2000为宜;优秀作品推荐参加省和国家创新大赛,申报专利;12月30日5点以前交于系办公室段老师。