仓储作业流程优化设计.docx
《仓储作业流程优化设计.docx》由会员分享,可在线阅读,更多相关《仓储作业流程优化设计.docx(20页珍藏版)》请在冰点文库上搜索。
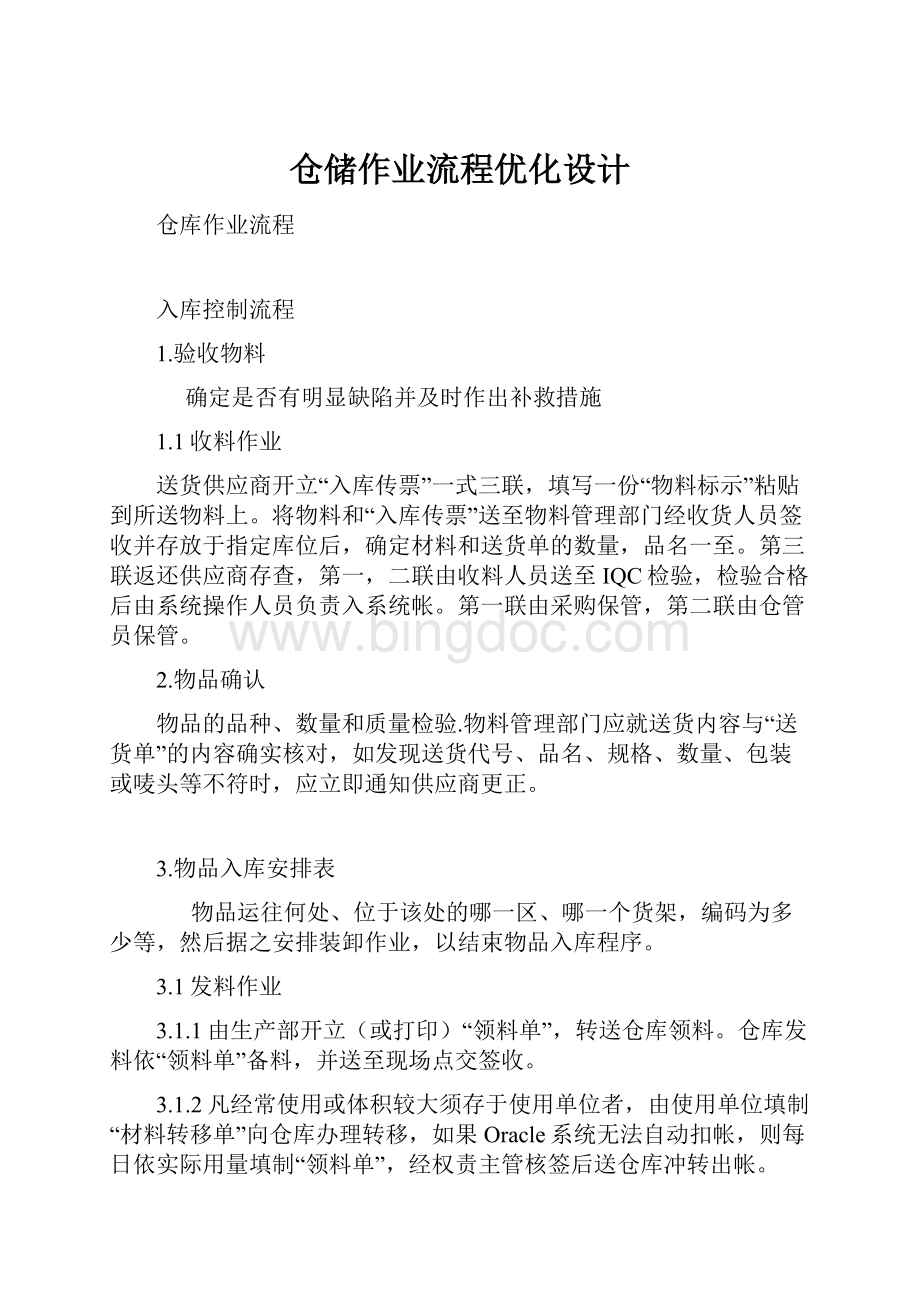
仓储作业流程优化设计
仓库作业流程
入库控制流程
1.验收物料
确定是否有明显缺陷并及时作出补救措施
1.1收料作业
送货供应商开立“入库传票”一式三联,填写一份“物料标示”粘贴到所送物料上。
将物料和“入库传票”送至物料管理部门经收货人员签收并存放于指定库位后,确定材料和送货单的数量,品名一至。
第三联返还供应商存查,第一,二联由收料人员送至IQC检验,检验合格后由系统操作人员负责入系统帐。
第一联由采购保管,第二联由仓管员保管。
2.物品确认
物品的品种、数量和质量检验.物料管理部门应就送货内容与“送货单”的内容确实核对,如发现送货代号、品名、规格、数量、包装或唛头等不符时,应立即通知供应商更正。
3.物品入库安排表
物品运往何处、位于该处的哪一区、哪一个货架,编码为多少等,然后据之安排装卸作业,以结束物品入库程序。
3.1发料作业
3.1.1由生产部开立(或打印)“领料单”,转送仓库领料。
仓库发料依“领料单”备料,并送至现场点交签收。
3.1.2凡经常使用或体积较大须存于使用单位者,由使用单位填制“材料转移单”向仓库办理转移,如果Oracle系统无法自动扣帐,则每日依实际用量填制“领料单”,经权责主管核签后送仓库冲转出帐。
3.2退料作业
3.2.1使用单位对于领用的材料,在使用时遇有材料质量异常,用料变更或用余时,使用单位应注记于“退料单”内,再连同料品缴回仓库;
3.2.2材料质量异常欲退料时,应先将退料品及“退料单”送质量管理部门检验,并将检验结果注记于“退料单”内,再连同料品缴回仓库;
3.3帐物 卡作业
3.3.1“有料必有帐,有帐必有料,且料帐要一致”,物料有了平面及立体布置规划,且又能整齐摆放,物料标示朝外,所有要用的物料,都能很迅速地取出。
3.3.2物料管理除了有料、帐外,每一种物料都应设立“物料管制卡”
3.4呆料作业
物料管理部门应于每月初,依料库类别的原材料中最近六个月无异动(异动的依据以配料单及领料单为准),或异动数量未超过库存量30%的材料,列出“六个月无异动呆料明细表”,送交相关部门。
库存报警
1.安全库存报警
根据存货的安全库存量,当现有的库存低于安全库存时,即发出库存补充单。
2.滞销品报警
让企业随时了解哪些产品属于滞销品,从而对滞销品进行处理并调整经营策略。
3.保质期报警
依企业对物品保质期的设定,使企业在维护信誉的同时减少不必要的浪费。
安得物流Y公司仓储作业系统优化设计
工商管理学院求知分队
1.导言
安得在顺应时代的发展中孕育而生,然而随着企业的发展,物流费用的上升却没有带来物流服务竞争力的提高,进出作业量不均、装卸搬运方式的不合理、人员流失率高等都制约了企业的发展。
我们小组以Y公司3、4号仓库作为分析改进的目标,用系统分析的方法对Y公司的3、
4号仓库的作业系统进行优化设计。
重新整合了装卸流程、合理分布了仓库产品、重新组织了作业方式、充分利用了仓库面积,在仓库成本上升较小的情况下大大提高了作业效率和反应速度,增加了仓库的实际使用面积,对于Y公司的发展有一定的实际意义。
2.现状分析及问题界定
Y公司是安得物流公司地处南方的一家中等规模的分公司,在这几年中其业务一直处于快速增长阶段。
它的主要客户T客户近年的业务增幅均超过30%,据Y公司A经理反映,仓库作业效率低下的问题随着客户的业务增长显得非常突出,特别在销售旺季时,客户、承运司机会不断地向Y公司的A经理抱怨,如等待时间太长、仓储作业效率太低、内部人员出工不出力的情况时有发生。
根据对Y公司3、4号仓库的资料分析,我们对目前Y公司的仓储作业的主要问题归纳如下:
2.1作业流程不合理
作业流程:
装1标准车:
转板→平移→卸货→装车
卸1标准车:
卸货→上板→平移→堆码
从目前的作业流程来看,每次装车需要经过转板、平移、卸货、装车作业过程,而每次卸车需要经过卸货、上板、平移、堆码作业过程。
这种作业流程往往使得工人在作业时出现等待的现象,即环节太多,连续性不强。
导致这种作业的非连续性的原因是:
一是各个作业环节不能密切衔接,各个作业环节存在着等待间歇时间;二是因为作业对象的复杂性(产品型号多达253种),有的品种易于装卸,有的品种难以装卸,从而导致作业量的不均衡性。
问题一,如何设计作业流程来提高作业效率?
2.2货物出入库量不均衡
一年中淡旺季出库量比较明显,8月~2月是出货旺季,五一、国庆、元旦和春节几个
重大节日前10天是出货高峰,作业量是平时的2-3倍;同一月中,出库量不均匀,月底最高,下旬的出库量占到50%;每天出库量在时间分布上也不是均匀的,上午很少,平均为5%,下午占30%,晚上占65%;每天的入库量基本是固定的,上午、下午、晚上的比例分别为20%、45%、35%;由于出货量的不均匀,造成了作业流程上的不稳定性。
问题二,应采取怎样的方法来解决出入库量不均衡?
2.3库容不足
T客户的业务量以30%的速度递增,目前Y公司的3号和4号仓库加在一起才能满足T客户的需要,以T客户的发展眼光来看,库容将会成为新的瓶颈。
问题三,如何通过节省仓库面积来满足未来T客户对于库容的需求?
2.4装卸方式落后
现有柴油叉车5台,液压手推车14台,主要以人力作业方式为主,没有什么较为现代
化的设备,工人的劳动强度偏大,负荷不均匀。
问题四,采用何种作业方式搬运货物?
2.5装卸效率偏低
装1标准车大概需要70分钟,卸1标准车大概需要60分钟,装卸工采用按组计件工资,
一班到底效率太低,在晚上由于作业时间长,出现干劲不足磨洋工的现象;有时装卸工也会计较同一组内劳动强度大小以及是否快干多干的不同意见,另外不同装卸组也会争抢品种较少比较好装车的计划,而一些品种多的计划都不太愿意装。
工人按月考核,与作业量不挂钩,出现出工不出力的情况。
问题五,怎样来减少装卸时间,提高装卸效率?
2.6堆放方式不规范
采用散货堆场的形式进行堆码,可堆码5层,但摆放杂乱,不能有效对商品进行标示,给查找货物增加难度,容易造成作业的混乱。
问题六,应该采取怎样的方式来规范货物在库堆放,保证质量?
2.7车辆等待时间过长
由于受订单的约束,有40%不是满车出库,其次,由于货物品种的原因,出库的车辆
有时需要在3号和4号仓库装车,有时需要在仓库间排两次队,排队原则主要依据车到仓库的先后
顺序,而仓库的作业效率低下,造成车辆在仓库的等待时间过长,这个也是承运司机抱怨最多的地
方之一。
问题七,如何处理车辆等待问题?
3.系统目标设计及其优化原则
3.1仓储作业系统结构
根据上述7个问题,按照系统目标设计及其优化的要求,总体上可归纳为“安得物流作业系统优化设计”问题,具体表现在出入库装卸、作业流程、仓库内部设施规划及布局、车辆排队4个方面。
因此,安得物流作业系统结构如下:
由此,我们确定仓储内部作业优化可分为如下几个子系统:
3.2系统优化的目标及其原则
1、仓储作业总体目标:
快进、快出、高效、保质、低成本
1)快进:
当货物到达仓库后,以最快的速度完成接货、验收和入库作业。
2)快出:
包含货物在库停留时间尽可能缩短,也包含出库作业环节的快速性。
3)高效:
在合理规划的基础上最大限度利用有效的储存面积和空间,提高单位面积的储存量和面积使用率。
在一定的货物流通下,使用尽可能少的劳动力。
4)保质:
按照货物的性质和储存性质和储存条件,合理安排储存场所,采取科学的
保管方法,使其在保管期间内质量完好、数量准确。
5)低成本:
成本尽可能的控制。
2、子系统的优化目标
1)出入库装卸系统的设计需要达到装车45分钟,卸车25分钟的目标。
2)作业流程的设计应该以提高经济性为目的。
3)仓库的内部规划做到最大限度利用仓库的面积,并且有利于日常保管工作的展开;布局上应该保证货物的快进、快出。
4)订单子系统建设上应该使装车之间的等待时间明显地缩短,并且从整体上压缩车辆在库时间。
3、仓储作业应遵循的原则:
连续性、均衡性
1)连续性:
即要求储存货物在各个环节或工序间的流动,在时间上尽可能衔接,不发生或少发生不必要的停顿或等待。
2)均衡性:
仓库作业过程的各个阶段、各个工序间在人力、物力的配备和时间的安排上必须保持运作均衡。
4.方案分析
4.方案分析
4.1出入库装卸子系统
1.现状分析
案例中的Y公司3、4仓库的作业流程是车辆通过装卸平台直接装卸到库内。
这种作业
流程往往使得工人在作业时出现等待的现象,由于单个仓库面积比较大,单次出入库行走距离平均约为80M,连续性不够强。
从表1中,我们可分析出货物进出库量在时间上是不均衡的,这种不均衡性造成了作业流程上的不稳定性,工人作业也时常出现等待的现象。
2.解决方案
从作业质量的角度考虑作业的连续性,即要求储存货物在各个环节或工序间的流动,在
时间上尽可能衔接,不发生或少发生不必要的停顿或等待。
减少作业时间,提高作业效率。
因此,我们将作业流程设计为从装卸车辆到拣货区再到库内进行保管作业,具有了较高的连续性,也提高了作业效率。
设置拣货区能缓解出入库量的不均衡。
在日出入库量的高峰时间段内,货物暂时先堆放
在拣货区,等出入库量作业处于低峰时再进行货物的搬运储存作业。
从时间效率上讲,有利于货物的快进
快出;从作业质量上讲,它保证了仓库作业的连续性。
从作业负荷均衡上讲,有利于缓解劳动强度,从而使整个仓库作业工作的平稳展开。
未设置拣货区前的效率是装1标准车大概需要70分钟,卸1标准车大概需要60分钟。
从案例资料分析得知,当设置一个拣货区后,装一辆车只需要40分钟,卸一辆车只需要25分钟。
那么现在的装车效率就是先前的56%,卸车效率就是先前的43%。
原来需要55个装卸工,15个仓管员,现在由于效率提升了大约一倍,只需要约32个装卸工,10个仓管员。
按1200元的月工资计算,一年就可以节约人工成本40.32万元,且达到了装车45分钟,卸车25分钟的要求。
4.2作业流程子系统
在优化作业流程时,我们主要是从作业流程的合理性角度出发,重新设计了仓储作业的
方式和顺序。
1.作业方案的提出
在考虑作业方式时,我们是从低成本的角度来考虑问题提出下面3种方案:
A.每个仓库建设输送机。
B.用叉车运送货物。
C.用液压手推车运送货物
2.资料及数据整理
1)根据T客户系列产品包装尺寸(全部尺寸波动平均,取平均值),主要货物的外形尺寸、重量:
电器平均长60cm,宽35cm,高46cm。
每个平均重22kg可堆码5层,因此选择托盘尺寸1.2m×1m,1t。
木托盘价格45元。
按照仓库规划设计组员计算需要托盘65377个,总成本2941,965元。
2).叉车(+托盘):
移动速度约2m/s,出入库距离160m,加上将托盘移到叉车上时因
此叉车每分钟大约作业0.5次,叉车装载16台/次,即8台/分钟。
设(出)入库量为:
Q;设作业时间为:
T分钟;每分钟需要的台数:
q=Q/T;再设叉车每分钟的作业量为:
n;需要叉车的数量为:
N=q/n。
由此,旺季每分钟需要货物台数上下限为11~75台,需要叉车数上下限为2~10台。
淡季每分钟需要货物台数上下限为7.6~47.4台,需要叉车数上下限为1~6台。
单价2.6万元。
3).平板车(+流动式货架):
移动速度约1m/s,加上搬运所需时间,作业速度0.3次/min,
装载量为8台/次。
同样依据上述计算公式
(1),可知,旺季需要手推车上下限为38~250台。
淡季需要手推车上下限为25~158台。
每台手推车的价格为180元。
根据仓库情况进行均衡,需要手推车至少120台。
根据案例材料得知,每个工人的月工资为1200元。
则一年的人工成本为172.8万。
4)双层输送带:
150m,双层共300m,3000元/M。
需要两部,成本为180万元
5)拣货区面积:
从图一中,我们设置了一个面积为S的大拣货区,我们根据旺季最大的日均出入量(17,875+10,302)(台)进行设计,用16台/平方M的标准计算,得出
S=拣货区面积/堆码标准=28,177/16=1,761(平方M)
则大拣货区S占总库区(42000cm2)的比率约为4.19%。
我们将拣货区设置在装卸作业平台与仓库之间,并且对于拣货区进行具体规划,将装货区与卸货区分隔开来,装货区约占总库区面积的2.66%,卸货区约占总库区面积的1.53%。
输送机放置在仓库中间,接到订单后,按订单需要,装卸工提前到达货架,取货用手推平移同时随输送机传送放上货物。
在输送机尾端,即在装卸平台,装卸工从输送机上取货。
共需要10台叉车,开叉车的装卸工10人。
由于手推车使用量大,人工投入大,共需要手推车120台,装卸人员120人。
3.方案评价
1).评价标准(根据装卸搬运合理化的原则)
(1)节约时间;(2连续化);(3)单元化(单元化设备的利用);(4)省力化(节省动力和人力)
(5)人性化(人的承受限度);(6)活性化(适于下一步装卸搬运作业);(7)有效管理
2)评价方法:
使用价值分析采用正交矩阵法对三个方案进行比较。
(1).确定8个评价准则的比重因子
1.节约时间;2.连续化;3.单元化;4.省力化;5.人性化;6.节省空间;7.活性化;8.有效管理
(2).方案评定:
对ABC共3个方案用8个评价准则进行评分.设评分值为R.则加权分
F=WF×R.方案总分N=∑F.(见下面评分表):
经济价值分析
根据前面资料整理与分析得出,采用输送机的成本为180万元;采用叉车运送的成本为
(电瓶叉车成本+托盘成本)=296.79万;采用手推车的成本计算中涉及的人工成本所占比例重,采用这种方式的成本为:
手推车成本+人工成本(一年工资),为174.96万元。
A
B
C
1800000
2967900
1749600
4.选择最优方案
根据上述分析,我们选择总费用/使用价值最小者为最优。
A
B
C
5732
10341
11983
排列顺序如下:
ABC
装卸方法:
A方案:
建设提前拣货区,用输送带运送货物
4.3仓库内部设施规划及布局子系统
1、设施规划
1)货架系统
这里研究的是3、4号仓库,由于货物的库存量非常大,若建设货架就相应地要求在货架间留有通道的距离,采用双面堆货的方式,单边货架的通道宽度相应地要求有0.6M,所以我们将通道宽度设为1.2M,从而保证了工人的操作空间。
我们将货架设计为2层,每层可以堆30台,以5*6台的方式进行堆码,通过计算得出一平方M可以堆30.3台,而原来只能堆25台,那么每平方M就可以节约(30.3-25)/30.3=0.174也就是可以节约17.4%的面积,即为42000*0.14=7308m2。
2)传输装置
采用皮带传输机,输送带宽为1M,长150M,两个仓库各一个,占地面积就为300m2
在库房内建设七个小的拣货区,总面积与大拣货区的面相当,为1761m2,则全部拣货区的面积为3522m2,剩余的库房面积为:
7308-3522-300=3466m2剩余的库房面积占总面积的8.25
2.仓库内部储位规划
储位的规划主要从保质的角度讲,按照货物的性质和储存性质和储存条件,合理安排储
存场所,采取科学的保管方法,使其在保管期间内质量完好、数量准确。
我们根据储存货物的不同性质安排不同储位。
对于出货天数高的货物根据实际情况,尽量安排在下层,而出货天数低的货物尽量安排在临时储位。
对于分类1的商品,因其特性特别需要提高其拣货时的安全系数,保证必要的拣货空间,将其主要分布于货架的下层,以便迅速存取货;
对于分类2的商品,存量水平低,估计所需空间可减少其安全系数,减少多余的拣货空间将起分布于货架的下层,以便节省员工的工作量;
分类3和分类4的商品,由于其存量小,出货量小,可放于货架的上层;
分类5、6、7的商品,由于其特性可以设置临时储位,避免其长时间占据过多储位;
分类8的商品可以根据空余储位的实际情况,分布与货架的上层或下层。
同时根据上述情况,还需对不同种类的商品和货架对应编号,这样就可以在很大程度上保证规范的操作,减少错误的发生。
3、仓库布局规划
Y公司有3、4号仓库,其中主要为T客户提供服务,目前3、4号仓库中存放的品种共有253种,根据案例中提供的产品种类及相关尺寸及重要,我们可以结合订单的情况将产品进行分类,依据A、B、C分类方法,可以将产品分为周转快和周转慢的几种情况,3号仓库4号仓库在品种上应合理搭配,避免作业量不均衡。
尽量平衡两个仓库在各个时间段的出货量,使它们在每个作业时间段都比较均匀,在避免装卸工与装卸工具需要在不同的仓库里调来调去的前提下合理货物分布,从而减少人员器具组织需要时间。
4.4订单处理子系统
以前主要是根据车辆到达仓库的先后顺序进行作业,由于Y公司应该具有与总公司相连接的数据网络,通过获得总公司与客户的资料,掌握订单情况。
根据出入库量的时间差异性,编制合理而科学的作业进度表,合理安排不同仓库的调度作业,使作业之间更加平滑从而避免排队和排队时间过长,提高工作的效率,保证仓库作业过程的流畅。
(作业流程图见下图)
出库由于受订单的约束经常出现排队交替等待现象。
造成原因主要有:
等待搬运、准备时间、查找库位、排队设计不合理。
为了解决上述问题,我们需要做如下安排:
1)在库物品种类分布合理化。
尽量平衡两个仓库在各个时间段的出货量,使它们在每个作业时间段都比较均匀,并且由于前面采用了比较合理的作业流程,保证了较高的作业效率,也避免装卸工与装卸工具需要在不同的仓库里调来调去的情况发生,有利于人员的有效管理。
2)处理订单时,切实按照订单的时间紧迫程度来合理安排排队顺序。
3)由于上面设了拣货区,仓库可以根据订单情况,提前将货物安排到拣货区,这里也就减少了仓管员找库位的时间,提高作业效率,使其能在订单规定的时间内完成作业任务,
从而缓解了车辆的在库时间过长问题。
根据上面的方法,我们可以将装卸两辆车之间的等待时间由原来的30分钟缩短为现在的约10分钟。
并且有效的解决了装车过程中抱怨最多的排队问题,装卸车效率的提高也减短了车辆的在库时间。
5.结论总结
5.1从快出、快进、高效的角度看,由装1标准车大概需要70分钟,卸1标准车大概需要
60分钟,上升到装一辆车需要40分钟,卸一辆车需要25分钟,大大提高了作业效率
和反应速度。
并且由于效率的提高,节约的人工成本为40万元。
5.2从仓库空间的高效利用和保质的角度讲,建货架不仅节约17.4%的仓库面积,而且便于有效标注,进行系统化管理,以此减少错误的发生。
并且便于规范在库物品的日常保管。
5.3从保证仓库作业的连续性和均衡性讲,建拣货区就可以避免由于出货量的时间不均匀造成的工作量的波动,其中拣货区占用仓库面积8.38%;
5.4从低成本的角度讲,经过几种方案的挑选,最后决定选择用双层输送带进行传送,需要资金180万元。
5.5从时间效率上来说装卸两辆车之间的等待时间由原来的30分钟缩短为现在的约10分钟。
并且有效的解决了装车过程中抱怨最多的排队问题;
6.结束语
现代物流是个快速发展的行业,作为现代物流主要环节的仓储作业也处于不断的发展之中。
由于时间较紧,再加上对一些公司数据掌握不够丰富,比如对仓库物品种类的具体分布情况、作业方式的细化等都可以继续的研究,加之水平有限,文中有许多不足之处,衷心希望专家们批评指正。
指导老师:
初叶萍
设计人员:
王丽华、朴日、邹晶、黄本连、王潇潇