固定卷扬式启闭机通用技术条件SD31589Word下载.docx
《固定卷扬式启闭机通用技术条件SD31589Word下载.docx》由会员分享,可在线阅读,更多相关《固定卷扬式启闭机通用技术条件SD31589Word下载.docx(25页珍藏版)》请在冰点文库上搜索。
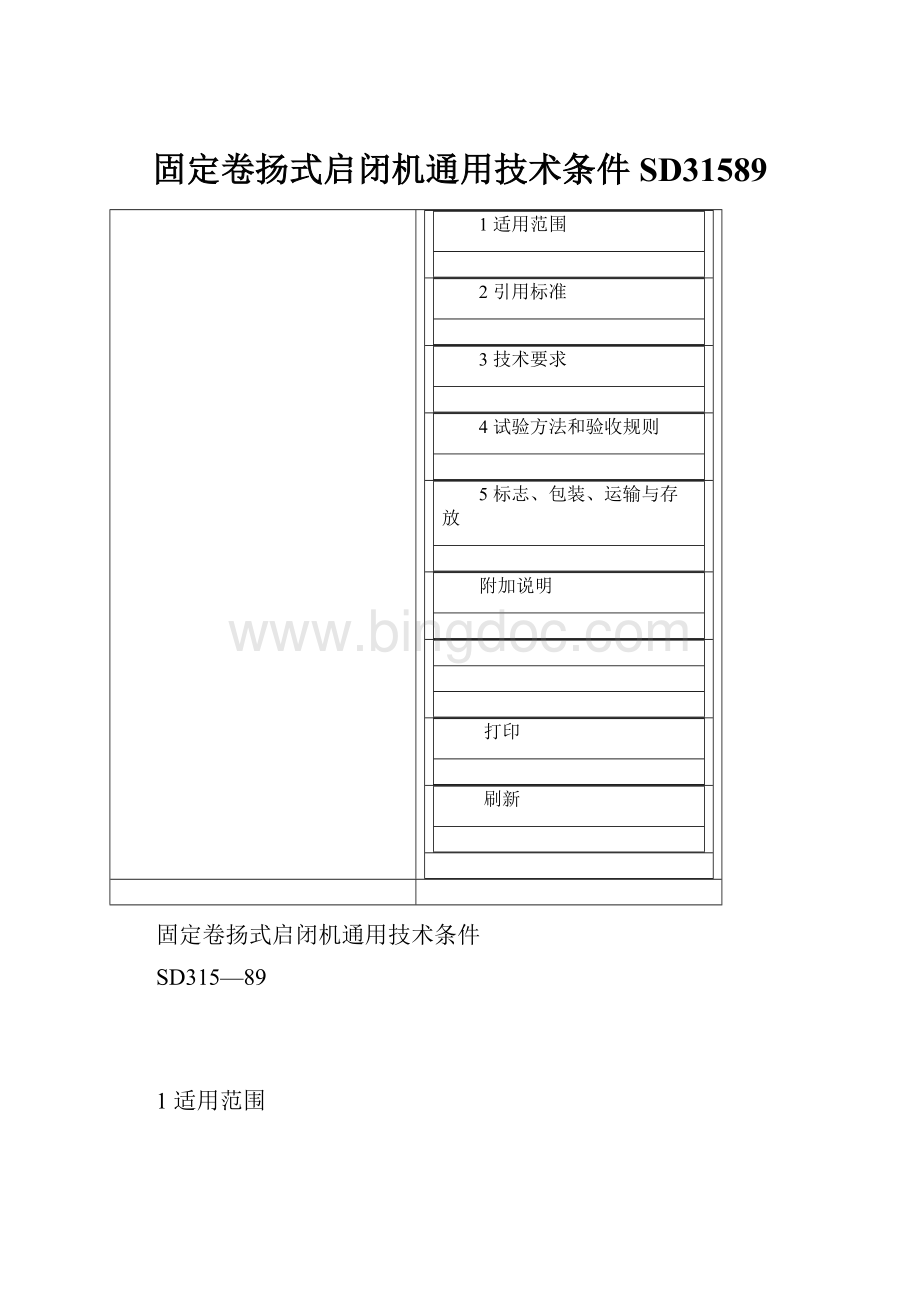
电(D)300
湿热带型开关板
GB1498
低压电器外壳防护等级
GB3181
漆脱颜色标准样本
JB2299
矿山、工程起重运输机械产品涂漆和安全标志
JB8
产品标牌
3.1主要构件和零件
3.1.1金属结构主要构件及主要零件,其材料应符合表1的规定。
表1
工作环境温度
不低于-20℃
低于-20~-25℃
其它条件
板厚大于20mm
—
钢号
A3
C,16Mn
冲击值
(N·
m/cm2)
≥70(常温时)
≥30(-20℃时)
注:
A3除基本保证条件(即常温冲击值,屈服点和冷弯)外,供货单位未提供上述数据时,材料进厂后必须补做试验。
3.1.2焊接卷筒的材料应采用GB700中的A3钢。
铸造卷筒的材料,铸铁应不低于GB5675中的HT200。
铸钢应不低于GB5676中的ZG230~450。
3.1.3铸造滑轮的材料
铸铁应不低于GB5676中的HT200;
3.1.4减速箱和轴承的盖座材料
铸铁应不低于GB5675中的HT200;
焊接应采用A3钢。
3.1.5开式齿轮、联轴器、制动轮及调速器的活动锥套其材料应不低于GB699中的35钢或GB5676中的ZG310~570。
3.1.6卷筒轴和传动轴的材料应不低于GB699中的45钢,对于采用无缝钢管型式的中间传动轴,其材料选用20号无缝钢管。
3.1.7齿轮和齿轮轴的材料,对于锻件应不低于45钢,对于铸钢件应不低于ZG310~570。
3.2钢丝绳
3.2.1钢丝绳应符合GB1102的有关规定。
3.2.2对于水下或经常出入水中工作的钢丝绳,宜选用镀锌钢丝绳;
当选用普通钢丝绳则应加强维护保养。
3.2.3钢丝绳出厂、运输、存放时应卷成盘形,表面涂油,两端扎紧并带有标签,注明订货号及规格,无标注的钢丝绳不得使用。
3.2.4钢丝绳长度不够时,禁止接长。
3.2.5钢丝绳的报废应按GB5972标准执行。
3.2.6钢丝绳端部固定连接的安全要求。
3.2.6.1用绳卡连接时,绳卡不得装反,应满足表2的要求;
同时应保证连接强度不得小于钢丝绳破断拉力的85%。
表2
钢丝绳直径(mm)
7~16
19~27
28~37
38~45
绳卡数量(个)
3
4
5
6
绳下压板应在钢丝绳长头一边;
绳卡间距不应小于钢丝绳直径6倍。
3.2.6.2用编结连接时,编结长度不应小于钢丝绳直径的15倍,并且不得小于300mm。
连接强度不得小于钢丝绳破断拉力的75%。
3.2.6.3用楔块、楔套连接时,连接强度不得小于钢丝绳破断拉力的75%;
楔套应用钢材制造。
3.2.6.4用锥形套浇铸法连接时,连接强度应达到钢丝绳的破断拉力。
3.2.6.5用铝合金压缩法连接时,应以可靠工艺方法使铝合金套与钢丝绳紧密牢固地贴合,连接强度应达到钢丝绳的破断拉力。
3.2.7钢丝绳压板应符合GB5975的有关规定。
3.3滑轮
3.3.1滑轮的槽形应符合图样,用样板检查时,其间隙不大于0.5mm。
3.3.2滑轮槽的径向圆跳动公差不大于GB1184附表4中11级的数值;
沿绳槽的端面圆跳动公差不应大于10级。
3.3.3滑轮槽两侧的壁厚不得小于名义尺寸;
壁厚误差最大允许值为,外径小于或等于700mm时,不大于3mm;
外径大于700mm时,不大于4mm。
3.3.4滑轮加工后的缺陷要求
3.3.4.1轴孔内不允许焊补。
但允许有不超过总面积10%的轻度缩松及下列范围的单个缺陷,面积不超过25mm。
深度不超过4mm缺陷数量不超过:
当孔径小于或等于150mm为2个,大于150mm为3个,且任何相邻两缺陷的间距不小于50mm,但此时应将缺陷边缘磨钝。
3.3.4.2绳槽面上或端面上的单个缺陷面积在清除到露出良好金属后不大于200mm。
深度不超过该处名义壁厚的20%,同一个加工面上不多于2处,焊补后不需进行热处理,但需磨光。
若缺陷超过以上规定,应报废。
3.3.5绳槽表面的粗糙度为GB1301中的
。
3.3.6滑轮上有裂纹时,不允许焊补,应报废。
3.3.7装配好的滑轮应能用手灵活转动,侧向摆动不大于滑轮直径的1/1000。
3.4卷筒
3.4.1铸铁卷筒和焊接卷筒应经过时效处理。
铸钢卷筒应退火处理。
3.4.2卷筒切出绳槽后,各处壁厚不得小于名义厚度;
其壁厚差不应超过下列值:
绳槽底径小于或等于700mm时,不大于3mm;
绳槽底径大于700~1000mm时,不大于5mm;
绳槽底径大于1000mm时,不大于8mm。
为了检查壁厚,可在卷筒端部或中部钻4个
6mm并相互成90°
的孔,在检查后可不必补上。
3.4.3卷筒绳槽底径公差应不大于GB1801~1802中的h10的系值。
绳槽表面粗糙度为GB1031的
,底径圆柱度误差不大于直径公差的一半。
绳槽加工后应用样板检查,样板和绳槽的间隙不大于0.5mm。
3.4.4钢丝绳压板用的螺孔必须光整、螺纹不允许破碎、断裂等缺陷。
钢丝绳固定卷筒的绳槽,其过渡部分的顶峰应铲平磨光。
3.4.5卷筒加工后的缺陷要求
3.4.5.1如加工面上的缺陷为局部砂眼、气孔,其直径不大于8mm,深度不超过该处名义壁厚的20%(但绝对值不大于4mm),在每100mm长度内不多于1处,在卷筒全部加工面上的总数不多于5处,允许不焊补,可作为合格。
3.4.5.2缺陷清除后,允许焊补的范围见表3的规定。
同一断面上和长度100mm的范围内不得多于2处,焊补后可不作热处理,但需磨光。
3.4.6卷筒上有裂纹时,不允许焊补,应报废。
3.4.7卷筒与开放式齿轮或减速箱低速轴的联结,其同轴度不大于GB1184规定11级的数值。
表3
材料
卷筒直径D(mm)
单个缺陷面积(mm2)
缺陷深度
处数
铸钢(铁)
≤700
≤200
≤25%壁厚
≤5
>700
≤250
3.4.8卷筒与大齿轮配合的法兰结合面对轴线垂直度公差不大于GB1184中9级的数值。
3.5联轴器
3.5.1联轴器加工后的陷缺要求
3.5.1.1齿面及齿沟不允许有焊补,如一个齿的加工面上的缺陷为局部砂眼、气孔,其缺陷数目不多于1个,其长、宽、深方向都不超过模数的20%,绝对值不大于2mm或径向细长缺陷的宽不大于1mm,长不大于0.8模数,绝对值不大于5mm,且距离齿的端面不超过齿宽的10%,在一个联轴器上有这种缺陷的齿数不超过3个时,可作为合格,但应将缺陷边缘磨钝。
3.5.1.2轴孔内不允许焊补,但若轴孔内的单个缺陷面积不超过25mm2,深度不超过该处名义壁厚的20%,缺陷数量不应超过:
当孔径小于或等于150mm为2个;
当孔径大于150mm为3个。
任何相邻两缺陷的间距不小于50mm时,可作为合格,但应将缺陷的边缘磨钝。
3.5.1.3其它部位的缺陷在清除到露出良好的金属后,单个面积不大于200mm2,深度不超过该处名义尺寸(壁厚)的20%,且同一加工面上不多于2个,允许焊补。
焊补后可不进行热处理,但需磨光。
3.5.1.4如缺陷超过上述规定或出现裂纹时,联轴器应予报废。
3.5.2CL型、CLZ型联轴器及弹性圈柱销联轴器两轴线的同轴度公差不大于GB1184附表4中9级数值。
3.5.3铸件加工前应进行退火处理。
3.5.4齿型联轴器,其齿的精度应不低于JB179中规定的9级。
齿面硬度应不低于HB230。
3.5.5弹性联轴器应符合GB5014的规定要求。
3.6制动轮
3.6.1制动轮工作表面的粗糙度不大于
3.6.2制动轮制动面的热处理硬度不低于HRC35~45,淬火深度不少于2mm。
3.6.3制动轮外圆与轴孔的同轴度误差不大于GB1184中8级。
3.6.4制动轮有无切削加工时,应进行静平衡试验。
3.6.5制动轮加工后的缺陷要求
3.6.5.1制动面上不允许有砂眼、气孔等缺陷,也不允许焊补。
3.6.5.2轴孔内不允许焊补,但若轴孔内的缺陷在:
单个缺陷的面积不超过25mm2,深度不超过4mm缺陷数量不超过两个,间距大于50mm时,可认为合格,但应将缺陷边缘磨钝。
3.6.5.3其它部位的缺陷在清除到露出良好金属后,单个面积不超过200mm2深度不超过该处名义壁厚的20%,总数量整个加工面上(除去制动面和轴孔外)不多于3个,允许焊补,焊补后可不进行热处理,但需磨光。
3.7制动器
3.7.1安装好的制动轮的径向跳动和端面跳动分别不低于GB1184中的9级和10级。
3.7.2安装制动器时,制动轮中心线对制动闸瓦中心线的位移不得超过下列数值:
当制动轮直径小于或等于200mm时,不大于2mm;
当制动轮直径大于200mm时,不大于3mm;
制动带与制动轮的实际接触面积不得小于总面积的75%。
3.7.3制动带与制动闸瓦应紧密的贴合,制动带的边缘应按闸瓦修齐,并使固定用铆钉的头必须埋入制动带厚度的三分之一以上。
3.7.4带螺纹的零件,其螺纹应光整无缺,不许有裂痕、断丝、毛刺等缺陷。
3.7.5装配后的制动器,其各节点应能灵活地转动,不得有卡住现象。
3.7.6带弹性套的制动轮联轴器,其弹性套的橡胶材料性能应符合设计要求,弹性套与制动轮上的孔,其配合应符合设计要求。
3.7.7制动器主弹簧和副弹簧,应经过三次全压试验后不得有永久变形,不合格者不准使用。
3.7.8使用调整螺钉,应使两个制动带与制动轮的间隙相等。
3.8齿轮
3.8.1齿轮轮缘和轮壳的壁厚差不得超过5mm。
3.8.2齿轮加工后的缺陷要求。
3.8.2.1齿面及齿沟不允许焊补,齿轮运动精度不高于8级,在一个齿的外形上(包括齿沟)缺陷数目不多于1个,其深度不超过模数的20%,绝对值不大于2mm,径向细长缺陷的宽不大于1mm,长不大于0.8模数,绝对值不大于5mm;
且距离齿轮的端面不超过宽的10%,在一个齿轮上有这种缺陷的齿数不超过3个时,可作为合格,但应将缺陷的边缘磨钝。
3.8.2.2轴孔内不允许焊补,但允许有不超过总面积10%的轻度(肉眼看不大明显)的缩松及单个缺陷不超过表4的数值;
缺陷的边缘应磨钝。
表4
齿轮直径(mm)
缺陷面积(mm2)
相邻间距(mm)
≤500
≤25
≤20%壁厚
>50
≤3
>500
≤50
>60
3.8.2.3端面处缺陷(不包括齿形端面)允许焊补的范围按表5规定执行。
表5
缺陷面积(cm2)
处数(一个加工面上)
≤2
≤15%壁厚
≤15%壁障
3.8.2.4齿面、齿沟不准有裂纹,也不允许焊补。
3.8.3齿面热处理硬度的要求。
3.8.3.1对于软齿面齿轮,小齿轮应不低于HB240,大齿轮应不低于HB190。
两者硬度差不小于HB30。
3.8.3.2对于软硬组合齿面,小齿轮应不低于HRC45,大齿轮不低于HB270。
3.8.4开式齿轮齿面粗糙度,当法向模数小于或等于8mm时,为
;
当法向模数大于8mm时,为
对于减速器内齿轮齿面粗糙度,当法向模数小于或等于8mm时,为
当法向模数8mm时,为
3.8.5齿轮的制造精度,对于开式齿轮和减速器内齿轮分别不低于JB179规定的9级精度和不低于8-7-7HK级精度。
3.9减速器
3.9.1减速器体的铸造应符合铸造的技术要求,并经过时效处理以消除内应力。
3.9.2渐开线齿轮啮合的接触斑点百分值按表6的规定,不准采用锉齿的方法来达到规定的接触面积。
表6
齿轮类别
测量部位
精度等级
7
8
9
接触斑点百分数不应小于
圆柱齿轮
齿高
齿长
45
60
40
50
30
3.9.3渐开线齿轮的最小侧间隙按表7规定。
表7
结合形式
Ⅰ
Ⅱ
中
心
距
50以下
50~80
80~120
120~200
200~320
320~500
500~800
800~1250
1250~2000
2000~3150
3150~5000
最
小
侧
间
隙
0.085
0.105
0.130
0.170
0.210
0.260
0.340
0.420
0.530
0.710
0.850
0.670
1.060
1.400
1.700
Ⅰ—标准保证侧隙;
Ⅱ—较大保证侧隙。
3.9.4渐开线齿轮的顶间隙按表8规定。
3.9.5封闭减速器前,两减速器体的接合面(包括瓦盖处)均需涂一层液体密封胶,但禁止放置任何衬垫。
外流的密封胶必须除净。
3.9.6装配好的减速器,接合面间的间隙,在任何处都不应超过0.03mm,并保证在运转时不漏油。
3.9.7轴承孔镗出后,两减速器体结合面不得再行加工或研磨,且不准有倒锥现象。
表8
齿轮压力角
标准间隙c
最大间隙
20°
标准齿
0.25mn
1.1c
mn—齿轮的法向模数。
3.9.8减速器体接合面处外边缘的不重合差不得超过下列数值:
减速器总中心距小于或等于500mm时,不大于2mm;
减速器总中心距大于500~1000mm时,不大于3mm;
减速器总中心距大于1000mm时,不大于4mm。
3.9.9减速器以不低于工作转速无负荷转动时,在无其它外音干扰的情况下,在壳体剖分面等高线上,距减速器前后左右1m处测量的噪声,不得大于85dB(A)。
3.9.10减速器应在厂内进行空载跑合试运行,在完成以上项目的检验后,用70目网过滤减速器清洗出的杂质,在温度为120~135℃下烘干1h,冷却20~30min以后的称重不得超过表9所列的清洁度指标。
表9
减速器总中心距(mm)
250
350
400
500
600
650
750
850
1000
杂质含量不大于(mg)
70
100
150
200
380
800
3.10LT型调速器
3.10.1固定座锥形制动工作面的粗糙度为
,热处理硬度不低于HRC35~45;
加工后的锥度误差不得超过±
0.25°
3.10.2活动锥套的摩擦面的斜向圆跳动的公差值不大于相应直径的1/2000。
3.10.3压缩弹簧应经过试验,合格后方能使用。
3.10.4活动锥套材料用铸件时,在半径相等不加工的外表面部分的壁厚不均匀差,应不大于2mm;
并应进行动平衡试验,合格后才能使用。
若用焊接件时,其焊缝质量必须满足;
图纸上的要求。
3.10.5角形杠杆和轴销,其材料不低于A5;
带螺纹部分其螺纹应无裂痕、断扣、毛刺等缺陷。
3.10.6摩擦制动带与活动锥面必须紧密贴合,固定螺钉头埋入深度必须符合设计要求,锥面经加工后,其锥度误差不得超过±
3.10.7制动带与固定支座锥面装配后的实际接触面积不得小于75%。
3.10.8装配后,左右锥套的轴向移动应相等,摆动飞球角形杠杆其动作应灵活,不得有卡住现象。
3.11仪表式高度指示器
3.11.1指示精度不低于2%。
3.11.2应具有可调节定值极限位置、自动切断主回路及报警功能。
3.11.3高度检测元件应具有防潮、抗干扰功能。
3.11.4具有纠正指示及调零功能。
3.12负荷控制器
3.12.1复合式负荷控制器的功能应满足下列要求:
a.系统精度不低于5%,传感器精度不低于0.5%;
b.当负荷达到110%额定启闭力时,应自动切断主回路和报警;
c.接收仪表的刻度或数码显示应与起闭力相符;
d.当监示两个以上吊点时,仪表应能分别显示各吊点启闭力;
e.传感器及其线路应具有防潮、抗干扰性能。
3.12.2弹簧式负荷控制器,应满足下列要求:
a.系统精度不低于8%,压力弹簧工作精度不低于2%;
b.采用圆柱形弹簧时,必须按设计要求进行弹簧试验;
c.采用蝶形弹簧时,必须进行单片及分组试验,并将试验数据提供用户,便于安装时调整;
d.当负荷达到110%额定启闭力时应自动切断主回路电源,并发出报警信号。
3.13机架
3.13.1机架上面各部件的垫板(如轴承座、电动机座、减速器座、制动器座等)必须进行加工,加工后的平面度误差不大于0.5mm。
各加工面之间相对高度误差不大于0.5~1mm。
3.13.2机架上主要受力处(如定滑轮支座、平衡滑轮支架、卷筒轴承支座)的焊缝为二类焊缝,其余接缝为三类焊缝,焊缝质量应符合
201的有关规定。
3.13.3机架各翼板和腹板焊接后的允许偏差应符合表10的规定。
表10
序号
项目
简图
偏差允许值Δ(mm)
1
板梁结构件翼板的水平倾斜度
(1)箱形梁
(2)Ⅰ字板梁
(此值均在长筋处测量)
2
箱形板梁Ⅰ字板梁翼缘板的平面度
箱形梁或Ⅰ字梁腹板的垂直度
(此值在长筋板或节点处测量)
箱形梁或Ⅰ字梁翼缘板相对于梁中心线的对称度
箱形梁或Ⅰ字梁腹板的平面度
用1m长平尺检查:
在受压区1/3的区域内,f≤0.75,且在相邻筋板间凹凸不超过一处:
其余区域内f≤
3.14滑动轴承
3.14.1在轴承摩擦表面上,不许有碰伤、气孔、砂眼、裂缝及其它缺陷。
3.14.2过盈配合的轴衬,一般用机械办法压入,如用锤打入时,中间需垫以铜或软铁,严禁用锤直接打在衬套上。
3.14.3油沟和油孔必须光滑,铲去锐边和毛刺,以防刮油。
3.14.4轴颈与衬套的接触角应在60°
~120°
范围内,接触面积每1cm2范围内不得少于1个点。
3.14.5轴颈与衬套的顶间隙应符合表11的规定,倾向间隙一般为顶间隙的50%~75%。
表11
轴颈直径(D)
顶间隙
0.07~0.14
80~20
0.08~0.16
120~180
0.10~0.20
180~260
0.12~0.23
260~360
0.14~0.25
3.15滚动轴承
3.15.1轴承在装配前必须用清洁的煤油洗涤,然后用压缩空气吹净。
不得用破布、棉纱擦抹,但如包装纸未破坏、润滑油未硬化、防锈油在有效防锈期内,同时轴承又是用于干油润滑时,则轴承可以不洗涤,即可进行装配,装配后注入占空腔65%~80%清洁的润滑油。
3.15.2已装好的轴承,如不能随即装配,应用干净的油纸遮盖好,以防铁屑、砂子等侵入轴承中。
3.15.3带过盈配合的轴承,在装配前将轴承放入90~100℃的油槽中加热,轴承要悬挂干油中,不许直接与油槽的底部或壁接触。
也可以用冷却轴颈的方法安装轴承。
装配时应用无冲击负荷的机械装置进行装配,不得用锤直接打在轴承圈上。
3.15.4轴承轴承的安装面,必须先涂一层清洁的油再进行装配。
3.15.5轴承必须紧贴在轴肩或隔套上,不许有间隙。
3.15.6轴承座圈端面与压盖的两端必须平行,当拧紧螺栓后必须均匀贴上,不许有部分间隙,如图样上规定有空隙时,四周必须均等。
装配好的轴承,应转动灵活。
3.15.7无论用何种方法拆卸轴承,作用力必须由小到大均匀地作用在过盈的座圈上,绝对禁止用锤直接打击轴承的座圈。
3.16启闭机的组装
3.16.1产品一般应在工厂进行组装(如果设备较大,工厂组装有困难,也可放到现场进行组装),出厂前应作空载模拟试验。
3.16.2所有零部件必须经检验合格,外购件、外协件应有合格证明文件方可进行组装。
3.16.3各零部件就位准确后,拧紧所有的紧固螺栓,弹簧垫圈必须整圈与螺母及零件支承面相接触。
3.16.4制动器的铰轴不应有锈住现象,制动轮和闸瓦之间的间隙应符合要求。
3.16.5快速启闭机的离心式调速器的制动锥面和闸瓦之间的间隙应四周均匀,其初始值为0.75mm。
3.16.6制动器和离心式调速器其摩擦面不应有油污,其接触面应均匀,并不得少于全面积的75%。
3.16.7制动轮和闸瓦之间的间隙应符合表12的规定。
3.16.8减速器加油前,应进行清洗检查,减速器内润滑油的油位应与油标尺的刻度相符,无油标尺时其油位不得低于大齿轮最低齿的齿高,但亦不应高于两倍齿高。
减速器应转动灵活,其油封和结合面处不得漏油。
表12
型号
允许值
制动轮直径(mm)
300
短行程TJ2
0.4
0.5
0.7
长行程JC2
0.8
液压电磁
液压推杆
3.16.9电机与减速器联接的高速轴径向跳动不大于GB1184附表4中8级。
3.16.10固定钢丝绳用的螺钉和卷筒上的螺孔的螺纹,均应完好无损,螺栓上应有防松装置。
3.16.11钢丝绳表面应涂防锈油脂,不应有腐蚀、硬弯、扭结和被压或被砸成扁平状等缺陷,其型号、长度均应符合图纸规定,并应具有出厂合格证。
如无合格证应切下一段长1500mm左右的钢丝绳,作单丝的抗拉强度试验,其强度应符合设计要求。
3.16