青霉素生产工艺.docx
《青霉素生产工艺.docx》由会员分享,可在线阅读,更多相关《青霉素生产工艺.docx(10页珍藏版)》请在冰点文库上搜索。
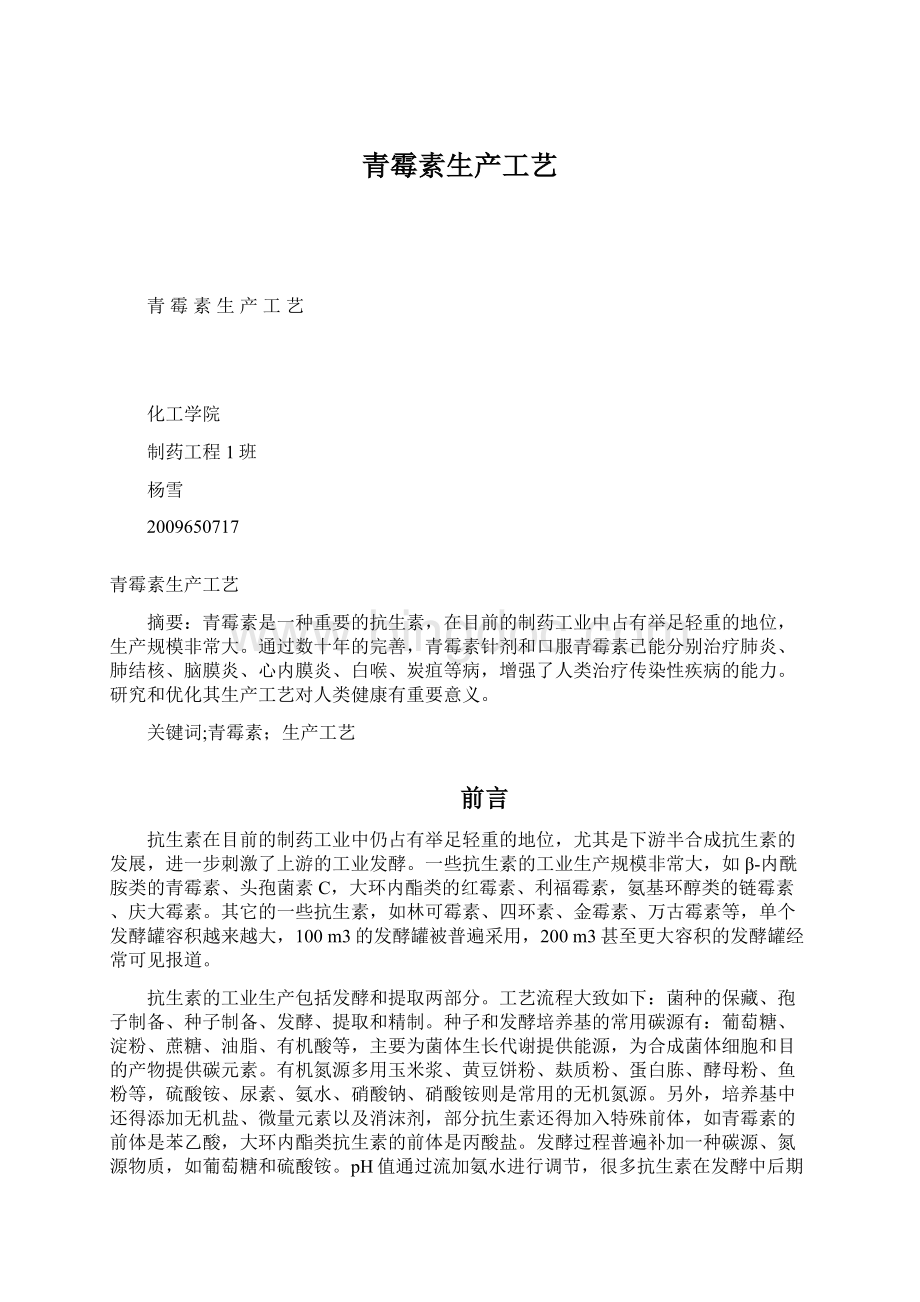
青霉素生产工艺
青霉素生产工艺
化工学院
制药工程1班
杨雪
2009650717
青霉素生产工艺
摘要:
青霉素是一种重要的抗生素,在目前的制药工业中占有举足轻重的地位,生产规模非常大。
通过数十年的完善,青霉素针剂和口服青霉素已能分别治疗肺炎、肺结核、脑膜炎、心内膜炎、白喉、炭疽等病,增强了人类治疗传染性疾病的能力。
研究和优化其生产工艺对人类健康有重要意义。
关键词;青霉素;生产工艺
前言
抗生素在目前的制药工业中仍占有举足轻重的地位,尤其是下游半合成抗生素的发展,进一步刺激了上游的工业发酵。
一些抗生素的工业生产规模非常大,如β-内酰胺类的青霉素、头孢菌素C,大环内酯类的红霉素、利福霉素,氨基环醇类的链霉素、庆大霉素。
其它的一些抗生素,如林可霉素、四环素、金霉素、万古霉素等,单个发酵罐容积越来越大,100m3的发酵罐被普遍采用,200m3甚至更大容积的发酵罐经常可见报道。
抗生素的工业生产包括发酵和提取两部分。
工艺流程大致如下:
菌种的保藏、孢子制备、种子制备、发酵、提取和精制。
种子和发酵培养基的常用碳源有:
葡萄糖、淀粉、蔗糖、油脂、有机酸等,主要为菌体生长代谢提供能源,为合成菌体细胞和目的产物提供碳元素。
有机氮源多用玉米浆、黄豆饼粉、麸质粉、蛋白胨、酵母粉、鱼粉等,硫酸铵、尿素、氨水、硝酸钠、硝酸铵则是常用的无机氮源。
另外,培养基中还得添加无机盐、微量元素以及消沫剂,部分抗生素还得加入特殊前体,如青霉素的前体是苯乙酸,大环内酯类抗生素的前体是丙酸盐。
发酵过程普遍补加一种碳源、氮源物质,如葡萄糖和硫酸铵。
pH值通过流加氨水进行调节,很多抗生素在发酵中后期流加前体,对提高产量非常有益。
抗生素发酵绝大多数为好氧培养,必须连续通入大量无菌空气,全过程大功率搅拌。
发酵液的预处理,一般加絮凝剂沉淀蛋白,过滤去除菌丝体,发酵滤液的提取常用溶媒萃取法、离子交换树脂法、沉淀法、吸附法等提纯浓缩,然后结晶干燥得纯品。
现在来介绍一下青霉素的生产工艺。
青霉素概述
青霉素是抗生素的一种,是指从青霉菌培养液中提制的分子中含有青霉烷、能破坏细菌的细胞壁并在细菌细胞的繁殖期起杀菌作用的一类抗生素,是第一种能够治疗人类疾病的抗生素。
青霉素类抗生素是β-内酰胺类中一大类抗生素的总称。
但它不能耐受耐药菌株(如耐药金葡)所产生的酶,易被其破坏,且其抗菌谱较窄,主要对革兰氏阳性菌有效。
最初青霉素的生产菌是音符型青霉菌,生产能力只有几十个单位,不能满足工业需要。
随后找到了适合于深层培养的橄榄型青霉菌,即产黄青霉(P.chrosogenum),生产能力为100U/ml。
经过X、紫外线诱变,生产能力达到1000-1500U/ml。
随后经过诱变,得到不产生色素的变种,目前生产能力可达66000-70000U/ml。
青霉素是抗生素工业的首要产品。
青霉素的特点
青霉素类抗生素是β-内酰胺类中一大类抗生素的总称,由于β-内酰胺类作用于细菌的细胞壁,而人类只有细胞膜无细胞壁,故对人类的毒性较小,除能引起严重的过敏反应外,在一般用量下,其毒性不甚明显,但它不能耐受耐药菌株(如耐药金葡)所产生的酶,易被其破坏,且其抗菌谱较窄,主要对革兰氏阳性菌有效。
青霉素G有钾盐、钠盐之分,钾盐不仅不能直接静注,静脉滴注时,也要仔细计算钾离子量,以免注入人体形成高血钾而抑制心脏功能,造成死亡。
青霉素类抗生素的毒性很小,是化疗指数最大的抗生素。
但其青霉素类抗生素常见的过敏反应在各种药物中居首位,发生率最高可达5%~10%,为皮肤反应,表现皮疹、血管性水肿,最严重者为过敏性休克,多在注射后数分钟内发生,症状为呼吸困难、发绀、血压下降、昏迷、肢体强直,最后惊厥,抢救不及时可造成死亡。
各种给药途径或应用各种制剂都能引起过敏性休克,但以注射用药的发生率最高。
过敏反应的发生与药物剂量大小无关。
对该品高度过敏者,虽极微量亦能引起休克。
注入体内可致癫痫样发作。
大剂量长时间注射对中枢神经系统有毒性(如引起抽搐、昏迷等),停药或降低剂量可以恢复。
内服易被胃酸和消化酶破坏。
肌注或皮下注射后吸收较快,15~30min达血药峰浓度。
青霉素在体内半衰期较短,主要以原形从尿中排出。
药理作用
青霉素药理作用是干扰细菌细胞壁的合成。
青霉素的结构与细胞壁的成分粘肽结构中的D-丙氨酰-D-丙氨酸近似,可与后者竞争转肽酶,阻碍粘肽的形成,造成细胞壁的缺损,使细菌失去细胞壁的渗透屏障,对细菌起到杀灭作用。
对革兰阳性球菌及革兰阳性杆菌、螺旋体、梭状芽孢杆菌、放线菌以及部分拟杆菌有抗菌作用。
青霉素对溶血性链球菌等链球菌属,肺炎链球菌和不产青霉素酶的葡萄球菌具有良好抗菌作用。
对肠球菌有中等度抗菌作用,淋病奈瑟菌、脑膜炎奈瑟菌、白喉棒状杆菌、炭疽芽孢杆菌、牛型放线菌、念珠状链杆菌、李斯特菌、钩端螺旋体和梅毒螺旋体对该品敏感。
该品对流感嗜血杆菌和百日咳鲍特氏菌亦具一定抗菌活性,其他革兰阴性需氧或兼性厌氧菌对该品敏感性差。
该品对梭状芽孢杆菌属、消化链球菌、厌氧菌以及产黑色素拟杆菌等具良好抗菌作用,对脆弱拟杆菌的抗菌作用差。
青霉素通过抑制细菌细胞壁四肽侧链和五肽交连桥的结合而阻碍细胞壁合成而发挥杀菌作用。
对革兰阳性菌有效,由于革兰阴性菌缺乏五肽交连桥而青霉素对其作用不大。
青霉素在中国的发展
1953年5月,中国第一批国产青霉素诞生,揭开了中国生产抗生素的历史。
截至2001年年底,中国的青霉素年产量已占世界青霉素年总产量的60%,居世界首位。
生产方法
天然青霉素与半合成青霉素生产方法完全不同。
天然青霉素
青霉素G生产可分为菌种发酵和提取精制两个步骤。
①菌种发酵:
将产黄青霉菌接种到固体培养基上,在25℃下培养7~10天,即可得青霉菌孢子培养物。
用无菌水将孢子制成悬浮液接种到种子罐内已灭菌的培养基中,通入无菌空气、搅拌,在27℃下培养24~28h,然后将种子培养液接种到发酵罐已灭菌的含有苯乙酸前体的培养基中,通入无菌空气,搅拌,在27℃下培养7天。
在发酵过程中需补入苯乙酸前体及适量的培养基。
②提取精制:
将青霉素发酵液冷却,过滤。
滤液在pH2~2.5的条件下,于萃取机内用醋酸丁酯进行多级逆流萃取,得到丁酯萃取液,转入pH7.0~7.2的缓冲液中,然后再转入丁酯中,将此丁酯萃取液经活性炭脱色,加入成盐剂,经共沸蒸馏即可得青霉素G钾盐。
青霉素G钠盐是将青霉素G钾盐通过离子交换树脂(钠型)而制得。
半合成青霉素
以6APA为中间体与多种化学合成有机酸进行酰化反应,可制得各种类型的半合成青霉素。
6APA是利用微生物产生的青霉素酰化酶裂解青霉素G或V而得到。
酶反应一般在40~50℃、pH8~10的条件下进行;近年来,酶固相化技术已应用于6APA生产,简化了裂解工艺过程。
6APA也可从青霉素G用化学法来裂解制得,但成本较高。
侧链的引入系将相应的有机酸先用氯化剂制成酰氯,然后根据酰氯的稳定性在水或有机溶剂中,以无机或有机碱为缩合剂,与6APA进行酰化反应。
缩合反应也可以在裂解液中直接进行而不需分离出6APA。
青霉素浓缩法
利用青霉素特异性地杀死野生型细胞、保留营养缺陷型细胞的方法。
青霉素能抑制细菌细胞壁的合成,所以只能杀死生长繁殖中的细菌,而不能杀死停止分裂的细菌。
在只能使野生型生长而不能使突变型生长的选择性液体培养基中,野生型被青霉素杀死,而突变型则不被杀死,从而淘汰野生型,使突变型得以浓缩。
可适用于细菌和放线菌,是营养缺陷型突变体筛选的常用方法之一。
不良反应
青霉素是各类抗生素中毒副作用最小的,因为其作用机理在于破坏细胞壁形成过程和结构,而人体没有细胞壁。
青霉素对人体基本没有药理毒性,但大剂量青霉素也可能导致神经系统中毒。
青霉素的副作用主要原因在于青霉素的提纯不足,其中的杂质容易使人体过敏。
⒈过敏反应:
青霉素过敏反应较常见,在各种药物中居首位。
严重的过敏反应为过敏性休克(Ⅰ型变态反应)发生率为0.004%~0.015%,Ⅱ型变态反应为溶血性贫血、药疹、接触性皮炎、间质性肾炎、哮喘发作等,Ⅲ型变态反应即血清病型反应亦较常见,发生率为1%~7%。
过敏性休克不及时抢救者,病死率高。
因此,一旦发生必须就地抢救,立即给病人肌注0.1%肾上腺素0.5~1ml,必要时以5%葡萄糖或氯化钠注射液稀释作静脉注射,临床表现无改善者,半小时后重复一次。
心跳停止者,肾上腺素可作心内注射。
同时静脉滴注大剂量肾上腺皮质激素,并补充血容量;血压持久不升者给予多巴胺等血管活性药。
亦可考虑采用抗组胺药以减轻荨麻疹。
有呼吸困难者予氧气吸入或人工呼吸,喉头水肿明显者应及时作气管切开。
青霉素酶应用意义不大。
⒉毒性反应:
青霉素毒性反应较少见,肌注区可发生周围神经炎。
鞘内注射超过2万单位或静脉滴注大剂量青霉素可引起肌肉阵挛、抽搐、昏迷等反应(青霉素脑病),多见于婴儿、老年人和肾功能减退的病人。
青霉素偶可致精神病发作,应用普鲁卡因青霉素后个别病人可出现焦虑、发热、呼吸急促、高血压、心率快、幻觉、抽搐、昏迷等。
此反应发生机制不明。
⒊二重感染:
用青霉素治疗期间可出现耐青霉素金葡菌、革兰阴性杆菌或白念珠菌感染,念珠菌过度繁殖可使舌苔呈棕色甚至黑色。
⒋高钾血症(低钾血症)与高钠血症:
如静脉给予大量青霉素钾时,可发生高钾血症或钾中毒反应。
大剂量给予青霉素钠,尤其是对肾功能减退或心功能不全病人,可造成高钠血症。
每日给予病人1亿单位青霉素钠后,少数病人可出现低钾血症、代谢性碱中毒和高钠血症。
⒌赫氏反应和治疗矛盾:
用青霉素治疗梅毒、钩端螺旋体病或其他感染时可有症状加剧现象,称赫氏反应,系大量病原体被杀灭引起的全身反应。
治疗矛盾也见于梅毒病人,系由于治疗后梅毒病灶消失过快,但组织修补较慢,或纤维组织收缩,妨碍器官功能所致。
副作用
1青霉素类的毒性很低,但较易发生变态反应,发生率约为5%~10%。
多见的为皮疹、哮喘、药物热、严重的可致过敏性休克而引起死亡。
2大剂量应用青霉素抗感染时,可出现神经精神症状,如反射亢进、知觉障碍、抽搐、昏睡等,停药或减少剂量可恢复。
3使用青霉素前必须作皮肤过敏试验。
如果发生过敏性休克,应立即皮下或肌内注射0.1%肾上腺素0.5ml~1ml,同时给氧并使用抗组胺药物及肾上腺皮质激素等。
(注:
由于青霉素过敏性反应实为杂质引起的,所以目前有部分进口高纯度青霉素无需皮试,可直接使用)
4肌注钾盐时局部疼痛较明显,用苯甲醇溶液作为稀释剂溶解,则可消除疼痛。
(2005年,国家药监局发文禁止苯甲醇作为青霉素溶剂注射使用。
)
口服后的人体反应
口服后吸收迅速,约75%-90%可自胃肠道吸收,食物对药物吸收的影响不显著,它的蛋白结合率为17%-20%,血消除半衰退期(t1/2)为1到1.3小时,服药后约24%-33%的给药量在肝内代谢,6小时内46%-68%给药量以原型药自尿排出,尚有部分药物经过胆道排泄,严重肾功能不全患者血清半衰期可延长至7小时。
血清透析可清除青霉素,腹膜透析则无清除该品的作用。
过敏急救措施
1、立即停药,平卧,就地抢救,采用头低足高位。
2.皮下注射0.1%盐酸肾上腺素0.5-1毫升,儿童酌减,每隔半小时可再皮下注射0.5毫升,直至脱离危险期。
3.心脏停跳者,行心脏胸外按压术或心内注射0.1%盐酸肾上腺素1毫升。
4.吸氧,呼吸抑制时口对口人工呼吸,并肌肉注射尼可刹米或山梗菜碱等呼吸中枢兴奋剂。
喉头水肿影响呼吸时行气管切开术。
5.用氢化考的松200毫克,或地塞米松5-10毫克加入50%Glucose40毫升中静脉注射,或加入5-10%Glucose500毫升中静滴。
6.根据病情需要可用血管活性药物如多巴胺,阿拉明等。
7.纠正酸中毒及组织胺药物的应用。
8.注意保暖,防止感冒,要做好护理记录,不要搬动。
9.可针刺人中,内关,印堂,合谷,涌泉等急救穴位。
10.可用艾条灸内关,合谷,涌泉,关元,中脘等穴位。
发酵工艺过程青霉素的发酵工艺过程
青霉素生产流程:
(1)生产孢子的制备
将砂土保藏的孢子用甘油、葡萄糖、蛋白胨组成的培养基进行斜面培养,经传代活化。
最适生长温度在25~26℃,培养6~8天,得单菌落,再传斜面,培养7天,得斜面孢子。
移植到优质小米或大米固体培养基上,生长7天,25℃,制得小米孢子。
每批孢子必需进行严格摇瓶试验,测定效价及杂菌情况。
(2)种子罐和发酵罐培养工艺
种子培养要求产生大量健壮的菌丝体,因此,培养基应加入比较丰富的易利用的碳源和有机氮源。
青霉素采用三级发酵
一级种子发酵:
发芽罐.小罐,接入小米孢子后,孢子萌发,形成菌丝。
培养基成分:
葡萄糖,蔗糖,乳糖,玉米浆,碳酸钙,玉米油,消沫剂等。
通无菌空气,空气流量1:
3(体积比);充分搅拌300-350r/min;40~50小时;pH自然,温度27±1℃。
二级发酵罐:
繁殖罐.大量繁殖。
玉米浆、葡萄糖等。
1:
1-1.5;250-280r/min;pH自然,25±1℃;0-14h。
三级发酵罐:
生产罐。
花生饼粉(高温),麸质粉、玉米浆、葡萄糖,尿素,硫酸铵,硫酸钠、硫代硫酸钠,磷酸二氢钠,苯乙酰胺及消泡剂,CaCO3等。
接种量为12~15%。
青霉素的发酵对溶氧要求极高,通气量偏大,通气比控制0.7~1.8;150-200r/min;要求高功率搅拌,100m3的发酵罐搅拌功率在200~300Kw,罐压控制0.04~0.05MPa,于25~26℃下培养,发酵周期在200h左右。
前60h,pH5.7~6.3,后6.3~6.6;前60h为26℃,以后24℃。
发酵过程控制
反复分批式发酵,100m3发酵罐,装料80m3,带放6-10次,间隔24h。
带放量10%,发酵时间204h。
发酵过程需连续流加补入葡萄糖、硫酸铵以及前体物质苯乙酸盐,补糖率是最关键的控制指标,不同时期分段控制。
在青霉素的生产中,让培养基中的主要营养物只够维持青霉菌在前40h生长,而在40h后,靠低速连续补加葡萄糖和氮源等,使菌半饥饿,延长青霉素的合成期,大大提高了产量。
所需营养物限量的补加常用来控制营养缺陷型突变菌种,使代谢产物积累到最大。
(1)培养基
青霉素发酵中采用补料分批操作法,对葡萄糖、铵、苯乙酸进行缓慢流加,维持一定的最适浓度。
葡萄糖的流加,波动范围较窄,浓度过低使抗生素合成速度减慢或停止,过高则导致呼吸活性下降,甚至引起自溶,葡萄糖浓度调节是根据pH,溶氧或CO2释放率予以调节。
碳源的选择:
生产菌能利用多种碳源,乳糖,蔗糖,葡萄糖,阿拉伯糖,甘露糖,淀粉和天然油脂。
经济核算问题,生产成本中碳源占12%以上,对工艺影响很大;糖与6-APA结合形成糖基-6-APA,影响青霉素的产量。
葡萄糖、乳糖结合能力强,而且随时间延长而增加。
通常采用葡萄糖和乳糖。
发酵初期,利用快效的葡萄糖进行菌丝生长。
当葡萄糖耗竭后,利用缓效的乳糖,使pH稳定,分泌青霉素。
可根据形态变化,滴加葡萄糖,取代乳糖。
目前普遍采用淀粉的酶水解产物,葡萄糖化液流加。
降低成本。
氮源:
玉米浆是最好的,是玉米淀粉生产时的副产品,含有多种氨基酸及其前体苯乙酸和衍生物。
玉米浆质量不稳定,可用花生饼粉或棉籽饼粉取代。
补加无机氮源。
无机盐:
硫、磷、镁、钾等。
铁有毒,控制在30µg/ml以下。
流加控制:
补糖,根据残糖、pH、尾气中CO2和O2含量。
残糖在0.6%左右,pH开始升高时加糖。
补氮:
流加酸酸铵、氨水、尿素,控制氨基氮0.05%。
添加前体:
合成阶段,苯乙酸及其衍生物,苯乙酰胺、苯乙胺、苯乙酰甘氨酸等均可为青霉素侧链的前体,直接掺入青霉素分子中。
也具有刺激青霉素合成作用。
但浓度大于0.19%时对细胞和合成有毒性。
还能被细胞氧化。
策略是流加低浓度前体,一次加入量低于0.1%,保持供应速率略大于生物合成的需要。
(2)温度
一生长适宜温度30℃,分泌青霉素温度20℃。
但20℃青霉素破坏少,周期很长。
生产中采用变温控制,不同阶段不同温度。
前期控制25-26℃左右,后期降温控制23℃。
过高则会降低发酵产率,增加葡萄糖的维持消耗,降低葡萄糖至青霉素的转化得率。
有的发酵过程在菌丝生长阶段采用较高的温度,以缩短生长时间,生产阶段适当降低温度,以利于青霉素合成。
(3)pH
合成的适宜pH6.4-6.6左右,避免超过7.0,青霉素在碱性条件下不稳定,易水解。
缓冲能力弱的培养基,pH降低,意味着加糖率过高造成酸性中间产物积累。
pH上升,加糖率过低不足以中和蛋白产生的氨或其他生理碱性物质。
前期pH控制在5.7~6.3,中后期pH控制6.3~6.6,通过补加氨水进行调节。
pH较低时,加入CaCO3、通氨调节或提高通气量。
pH上升时,加糖或天然油脂。
一般直接加酸或碱自动控制,流加葡萄糖控制。
(4)溶氧
溶氧<30%饱和度,产率急剧下降,低于10%,则造成不可逆的损害。
所以不能低于30%饱和溶氧浓度。
通气比一般为1:
0.8VVM。
溶氧过高,菌丝生长不良或加糖率过低,呼吸强度下降,影响生产能力的发挥。
适宜的搅拌速度,保证气液混合,提高溶氧,根据各阶段的生长和耗氧量不同,对搅拌转速调整。
(5)菌丝生长速度与形态、浓度
对于每个有固定通气和搅拌条件的发酵罐内进行的特定好氧过程,都有一个使氧传递速率(OTR)和氧消耗率(OUR)在某一溶氧水平上达到平衡的临界菌丝浓,超过此浓度,OUR>OTR,溶氧水平下降,发酵产率下降。
在发酵稳定期,湿菌浓可达15~20%,丝状菌干重约3%,球状菌干重在5%左右。
另外,因补入物料较多,在发酵中后期一般每天带放一次,每次放掉总发酵液的10%左右。
有丝状生长和球状生长两种。
前者由于所有菌丝体都能充分和发酵液中的基质及氧接触,比生产率高,发酵粘度低,气/液两相中氧的传递率提高,允许更多菌丝生长。
球状菌丝形态的控制,与碳、氮源的流加状况,搅拌的剪切强度及稀释度相关。
(6)消沫
发酵过程泡沫较多,需补入消沫剂。
天然油脂:
玉米油;化学消沫剂:
泡敌。
少量多次。
不适在前期多加入,影响呼吸代谢。
青霉素的发酵过程控制十分精细,一般2h取样一次,测定发酵液的pH、菌浓、残糖、残氮、苯乙酸浓度、青霉素效价等指标,同时取样做无菌检查,发现染菌立即结束发酵,视情况放过滤提取,因为染菌后pH值波动大,青霉素在几个小时内就会被全部破坏。
青霉素的提炼工艺过程
青霉素提纯工艺流程简图:
青霉素不稳定,发酵液预处理、提取和精制过程要条件温和、快速,防止降解。
1.预处理
发酵液结束后,目标产物存在于发酵液中,而且浓度较低,如抗生素只有10-30Kg/m3,含有大量杂质,它们影响后续工艺的有效提取,因此必须对其进行的预处理,目的在于浓缩目的产物,去除大部分杂质,改变发酵液的流变学特征,利于后续的分离纯化过程。
是进行分离纯化的一个工序。
2.过滤
发酵液在萃取之前需预处理,发酵液加少量絮凝剂沉淀蛋白,然后经真空转鼓过滤或板框过滤,除掉菌丝体及部分蛋白。
青霉素易降解,发酵液及滤液应冷至10℃以下,过滤收率一般90%左右。
(1)菌丝体粗长10µm,采用鼓式真空过滤机过滤,滤渣形成紧密饼状,容易从滤布上刮下。
滤液pH6.27-7.2,蛋白质含量0.05-0.2%。
需要进一步除去蛋白质。
(2)改善过滤和除去蛋白质的措施:
硫酸调节pH4.5-5.0,加入0.07%溴代十五烷吡啶PPB,0.7%硅藻土为助滤剂。
再通过板框式过滤机。
滤液澄清透明,进行萃取。
3.萃取
青霉素的提取采用溶媒萃取法。
青霉素游离酸易溶于有机溶剂,而青霉素盐易溶于水。
利用这一性质,在酸性条件下青霉素转入有机溶媒中,调节pH,再转入中性水相,反复几次萃取,即可提纯浓缩。
选择对青霉素分配系数高的有机溶剂。
工业上通常用醋酸丁酯和戊酯。
萃取2-3次。
从发酵液萃取到乙酸丁酯时,pH选择1.8-2.0,从乙酸丁酯反萃到水相时,pH选择6.8-7.4。
发酵滤液与乙酸丁酯的体积比为1.5-2.1,即一次浓缩倍数为1.5-2.1。
为了避免pH波动,采用硫酸盐、碳酸盐缓冲液进行反萃。
发酵液与溶剂比例为3-4。
几次萃取后,浓缩10倍,浓度几乎达到结晶要求。
萃取总收率在85%左右。
所得滤液多采用二次萃取,用10%硫酸调pH2.0~3.0,加入醋酸丁酯,用量为滤液体积的三分之一,反萃取时常用碳酸氢钠溶液调pH7.0~8.0。
在一次丁酯萃取时,由于滤液含有大量蛋白,通常加入破乳剂防止乳化。
第一次萃取,存在蛋白质,加0.05-0.1%乳化剂PPB。
萃取条件:
为减少青霉素降解,整个萃取过程应在低温下进行(10℃以下)。
萃取罐冷冻盐水冷却。
4.脱色
萃取液中添加活性炭,除去色素、热源,过滤,除去活性炭。
5.结晶
萃取液一般通过结晶提纯。
青霉素钾盐在醋酸丁酯中溶解度很小,在二次丁酯萃取液中加入醋酸钾-乙醇溶液,青霉素钾盐就结晶析出。
然后采用重结晶方法,进一步提高纯度,将钾盐溶于KOH溶液,调pH至中性,加无水丁醇,在真空条件下,共沸蒸馏结晶得纯品。
直接结晶:
在2次乙酸丁酯萃取液中加醋酸钠-乙醇溶液反应,得到结晶钠盐。
加醋酸钾-乙醇溶液,得到青霉素钾盐。
共沸蒸馏结晶:
萃取液,再用0.5MNaOH萃取,pH6.4-4.8下得到钠盐水浓缩液。
加2.5倍体积丁醇,16-26℃,0.67-1.3KPa下蒸馏。
水和丁醇形成共沸物而蒸出。
钠盐结晶析出。
结晶经过洗涤、干燥后,得到青霉素产品。
参考文献
【1】陈阳,王锦玲,黄维国,等.甲磺酸去铁胺对抗庆大霉素耳毒性的实验研究.听力学及言语疾病杂志,1999,7:
138-139.
【2】孙爱华,林顺涨,叶青,等.缺铁条件下青霉素耳毒性作用的实验观察.听力学及言语疾病杂志,2001,9
(2):
74-76.
【3】周本忠,孙爱华,王胜国,等.缺铁性贫血治疗前后听性脑干反应的变化.临床耳鼻咽喉科杂志,2001,4(15):
173-175.
【4】王复周(译).人体生理学.北京:
科学出版社,1991,242.
【5】何玉英.青霉素类抗生素使用中应注意的一些问题.中国临床医生,2002,30(9):
52.
【6】胡晓镭,胡彻.几种常用青霉素类抗生素的配伍禁忌.现代诊断与治疗,2002,13(3):
188.
【7】王贤才(译).临床药物大典.青岛:
青岛出版社,1994,1057-1058