蚀刻技术.docx
《蚀刻技术.docx》由会员分享,可在线阅读,更多相关《蚀刻技术.docx(25页珍藏版)》请在冰点文库上搜索。
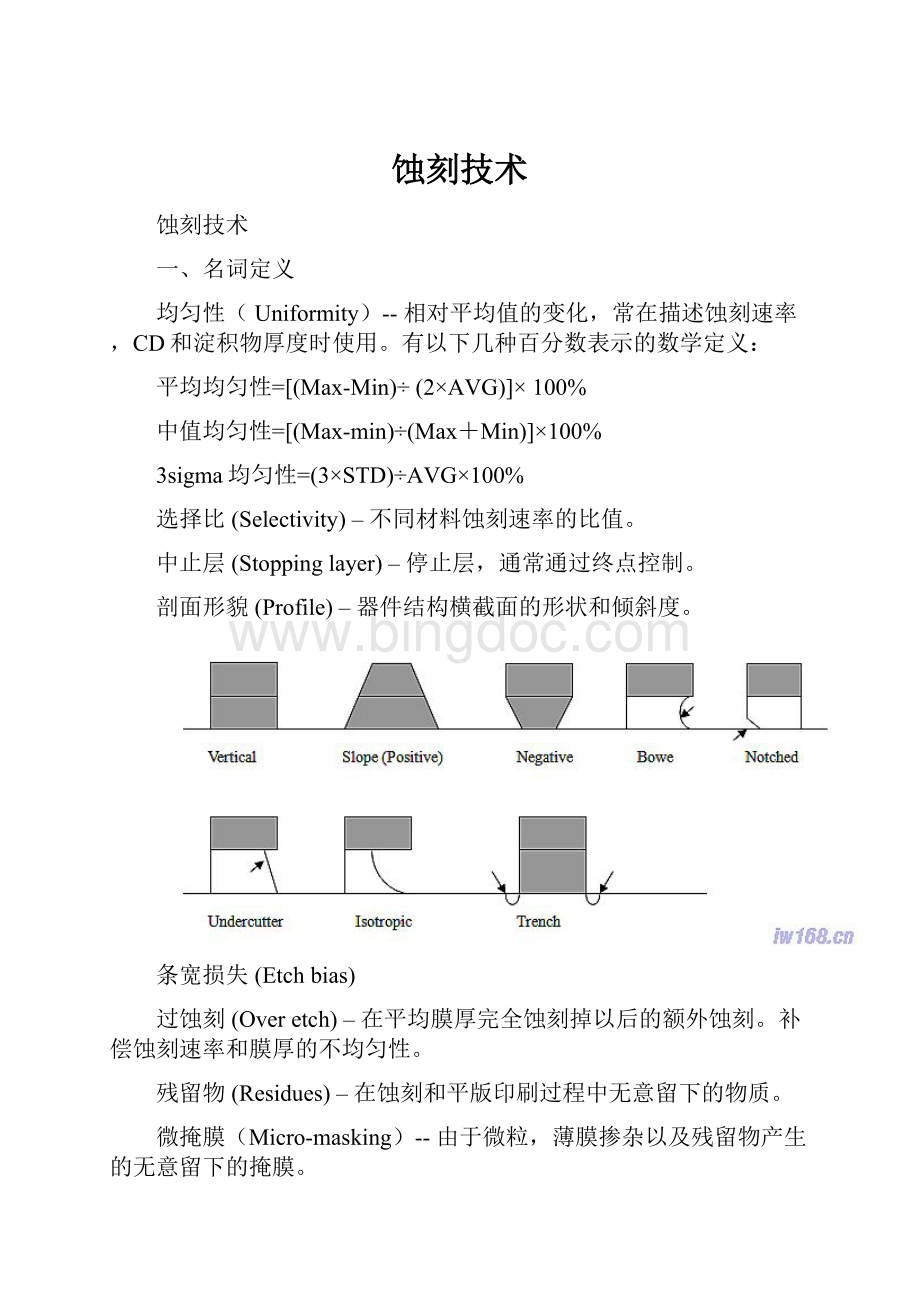
蚀刻技术
蚀刻技术
一、名词定义
均匀性( Uniformity)-- 相对平均值的变化,常在描述蚀刻速率,CD和淀积物厚度时使用。
有以下几种百分数表示的数学定义:
平均均匀性=[(Max-Min)÷ (2×AVG)]× 100%
中值均匀性=[(Max-min)÷(Max+Min)]×100%
3sigma均匀性=(3×STD)÷AVG×100%
选择比 (Selectivity)– 不同材料蚀刻速率的比值。
中止层 (Stoppinglayer)– 停止层,通常通过终点控制。
剖面形貌 (Profile)– 器件结构横截面的形状和倾斜度。
条宽损失 (Etchbias)
过蚀刻 (Overetch)– 在平均膜厚完全蚀刻掉以后的额外蚀刻。
补偿蚀刻速率和膜厚的不均匀性。
残留物 (Residues)– 在蚀刻和平版印刷过程中无意留下的物质。
微掩膜(Micro-masking)--由于微粒,薄膜掺杂以及残留物产生的无意留下的掩膜。
糊胶(Resistreticulation)-- 温度超过150摄氏度时光刻胶产生的燃烧和折皱。
纵横比(Aspectratio)-- 器件结构横截面深度和宽度的比率。
负载(Loading)-- 蚀刻速率依赖于可蚀刻表面数量,可在宏观或微观尺寸下。
纵横比决定蚀刻(AspectRatioDependentEtching/ARDE)--蚀刻速率决定于纵横比。
终点(Endpoint)-- 在一个蚀刻过程中,平均膜厚被蚀刻干净时的时间点。
光刻胶(Photo-resist)-- 作为掩膜用来图形转移的光敏材料。
分辨率(Resolution)--用于测试光学系统把相邻的目标形成分离图像的能力。
焦深(Depthoffocus)– 在焦平面上目标能形成影像的纵向距。
关键尺寸(Criticaldimensions-CD)-- 一个最小特征图形的绝对尺寸,包括线宽、间隙、或者关联尺寸。
去边(Edgebeadremoval-EBR)--去胶边的过程,通常在涂胶后将溶剂喷在硅片的背面或前边沿上。
前烘(Soft-bake)--在涂胶后用来去除胶溶剂的温度步骤。
曝光(Exposure)--把涂胶后的硅片,暴露在某种形式的射线下,以在胶上产生隐约的图像的步骤。
PEB(Post-exposure-bake)—曝光以后消除胶里的由衬底反射引起的胶里的驻波的温度步骤。
显影(Development)--在曝光以后分解胶产生掩膜图案的过程。
后烘 (Hard-bake)—用来去除残留溶剂,增加胶的沾着力和耐腐能力,在显影后完成,可以包括DUV固胶。
化学蚀刻(Chemicaletching)-- 根据化学反应机理,气态物质(中性原子团)与表面反应,产物必定易挥发,也称为等离子蚀刻。
等离子增强蚀刻(Ion-enhancedetching)—单独使用中性原子团不能形成易挥发产物,具有一定能量的离子改变衬底或产物;具有一定能量的离子改变衬底或产物层,这样,化学反应以后能生成挥发性物质,亦称为反应离子蚀刻(RIE)。
溅射蚀刻(Sputteretching)--具有一定能量的离子机械的溅射衬底材料。
蚀刻速率(Etch rate)--材料的剥离速率,通常以?
/min,?
/sec,nm/min,um/min为单位计量。
各向同性蚀刻( Isotropic etch)-- 蚀刻速率在所有方向都是相同的。
各向异性蚀刻(Anisotropic etch)--蚀刻速率随方向而不等。
二、Clamping 和 拱形电极
1.Clamping:
目的
为什么夹紧硅片?
通过提高硅片到下电极的热量交换来控制硅片温度。
2.Clamping:
clamp设计
用弹簧把硅片压至下电极。
通过高压氦气(8~14Torr)喷入到硅片和下电极之间,从硅片传导热量。
热量传导同氦气压力成正比,和硅片--下电极间距成正比。
下电极凹槽确保氦气的均匀扩散。
氦气压力由UPC自动控制(压力控制单元)。
3.为什么使用氦气?
氦气是惰性的,她具有很高的导热性。
4.Clamp所用的材料
a.陶瓷(氧化铝)--Ceramic(Alumina)
陶瓷是使用最普遍的一种材料,它很耐用、易加工,不会严重沾污硅片。
它在处理不当时极易破碎,所以在接触硅片表面时,被认为不如一些聚合物材料理想。
b.阳极氧化铝(Hard anodized Aluminum)
早期clamp材料用于Rainbow,它不如陶瓷耐用,在耗尽层阳极氧化处理后,通过溅射会沾污硅片。
c.VESPEL(Insert)
迄今为止,大多数对于VESPEL clamp的尝试都不令人满意,VESPEL在某些工艺条件下会变热和变形。
5.Clamping :
氦气冷却设计
a. 开环氦气
不可自动调整
控制或了解硅片--电极间隙的压力很困难
b. 闭环氦气控制
自动控制压力(UPC)
较好的工艺控制,在加工过程中能够确定clamp流速,在压力控制需要很低流量时,UPC难以稳定。
c. 半闭环氦气控制
自动压力控制
clamp流速在加工期间不能被精确测知
UPC稳定性在高流速下大为提高
6.Clamping:
clamp的特性
Clamp的印痕
理想的clamp会在加工过程中在硅片上留下同心圆印痕。
同心圆印痕的要求:
硅片对中性良好
clamp尺寸合适
差的clamp印痕常常伴随着差的蚀刻速率均匀性或者产生糊胶。
通常,反应室关闭后clamp应当定中心,这是在反应室内无硅片的情况下抽真空后通过多次改变上、下电极的间距来完成的。
7.Clamp漏率/clamp流量
Clamp漏率与多种工艺问题有关,对六英寸闭环配置的有些情况已经被确定下来了。
当有问题时,凭经验对多晶和二氧化硅系统在设定为13T的工艺时,流量应当小于10sccm,这相当于1000~1500mT/min的漏率。
当clamp漏率的影响和一些工艺参数被确定,许多时候clamp都被怀疑有问题,但是又得不到证明。
所有的高clamp漏率并不说明clamp有问题。
Edge(硅片边缘),下电极,硅片对中和硅片的不同都影响clamp的漏率。
8.Clamp降压
加工后氦气冷却区域必须在clamp升起前降压。
在4500或者配有低于室温电极的反应室内,clamp只有在排除反应室内剩余蚀刻气体后才能从硅片上升起。
否则,聚合物会沉积在下电极,最后影响工艺。
9.clamp相关的问题
增加工艺复杂性
增加硬件复杂性
Clamping的不可重复性:
Clamp印痕伴随着工艺逐渐漂移
Clamp与clamp的不同造成漏率变化
硅片温度的不均匀性,难以得到均匀的蚀刻形貌
Clamp边蚕食硅片可用区域
Clamp造成工艺硬件与硅片表面接触。
10.拱形电极:
目的
为什么采用拱形电极:
减少下电极与硅片间距的变化。
由于氦气压力会压弯硅片,所以硅片中心的问题(硅片与下电极大于硅片边缘,这导致关键的等离子参数不均匀),把电极做成拱形的,可以使变化减到最小。
提供均匀的硅片温度控制。
11.拱形电极:
发展
a. 平坦的不作阳极处理的电极
Kapton(卡普顿〈聚酰亚胺薄膜〉)难以应用
中心 --边蚀刻剖面不均匀
b. 平坦的HAA电极
中心 --边蚀刻剖面不均匀
对聚合物淀积敏感
c. 拱形Kapton
Kapton难以应用
最佳拱高难以达到
对糊胶敏感
d. 拱形HAA
最佳拱高难以达到
对糊胶敏感
对聚合物淀积敏感
e. 拱形—刻槽HAA
最佳拱高通过预先设计的实验达到
糊胶大大排除
对聚合物沉积敏感
三、SIO2特性
1.SIO2描述
Item
Description
分子描述
二氧化硅是由一个硅原子与两个氧原子共价结合而成。
电阻率
二氧化硅是绝缘体,它的典型电阻率是1024~1016 Ω/cm,与之相对应铝的电阻率是3×10-6Ω/cm,硅的电阻率是10-2~10-4Ω/cm。
自然种类
二氧化硅的自然形式有石英、沙、或者暴露在大气中的硅表面上的薄天然氧化层。
理解
二氧化硅薄膜是可预知的、可重复制造的和可理解的。
在硅片上生产SIO2薄膜的技术是可以实现的,能够精确控制膜厚、密度和深入理解Si/SIO2分界面。
2.二氧化硅在VLSI中的应用
Item
Description
Gate Oxide
栅二氧化硅
薄绝缘层(~150Å),热生长二氧化硅分隔MOS晶体管中的源漏沟道和(多晶硅)栅。
Field Oxide
场二氧化硅
厚(~4000Å)热生长二氧化硅常用来确定和隔离硅片的有源区。
Spacer Oxide
侧墙二氧化硅
厚CVD二氧化硅常用来确定MOS沟道的宽度和减少热载流子效应
InterlevelDielectric
金属间绝缘介质
厚(~7500Å)CVD二氧化硅(BPSG或TEOS),常用来绝缘衬底和金属化层。
Passivation Oxide
钝化二氧化硅
厚CVD二氧化硅,常作为金属间绝缘介质分隔金属线,确定压焊孔。
Planarization Oxide
平坦化二氧化硅
二氧化硅层,用于降低由于多层布线造成的表面高低不平的形貌。
3.Oxide 制造
Item
Product
Purpose
characteristic
TOX
硅暴露在高温(~1100℃)氧化蒸气(H2O或O2)中,氧气与硅反应生成SIO2表面层,SIO2的厚度由温度和时间精确控制。
HTO质量最高,通常用在栅氧和场氧层次。
TOX是最稳定、纯净和均匀的二氧化硅(便宜),FAB通常收集热二氧化硅的SPC和均匀性数据,热二氧化硅是蚀刻的最慢的氧化物。
HTO
在约900℃下氧化物LPCVD(低压CVD)形成。
反应式:
SiH2Cl2 +2N2O→ SIO2 +2N2 +2HCl
HTO薄膜的优点是薄膜质量高(相似于TOX),同时均匀性极好。
缺点是高的淀积温度可能造成下层薄膜出问题及衬底掺杂区杂质扩散。
通常,HTO常用作第一层绝缘材料(接触孔蚀刻)或spacers蚀刻。
蚀刻速率略大于TOX。
低温氧化硅
LTO
随着在约400℃下,APCVD(常压CVD)工艺而形成。
反应式:
SiH4 + O2→ SIO2 + 2H2
LTO薄膜用于金属间绝缘介质,钝化层,或者作为侧墙层(以前)。
通常LTO用作衬底/栅多晶层和掺杂绝缘层(如BPSG)之间的过渡层。
LTO的缺点是:
薄膜在没有致密化步骤的情况下质量较差,薄膜保型性好,因此不宜用于平坦化。
由于LTO是在低温下淀积的,薄膜性质通常不是很紧密,对针孔也很敏感,这就需要一个淀积后的高温致密工序(~900℃)。
TEOS
在700℃左右LPCVD工艺。
有很强的保型性(甚至好于LTO),用于spacers和金属间绝缘介质。
同样在平坦化中伴随SOG薄膜一起使用。
蚀刻速率略大于TOX。
PECVD
PECVD(等离子体增强CVD)二氧化硅利用等离子体激起反应。
这样在低衬底温度下可得到高淀积数率及相对于在相同温度下淀积的APCVD或LPCVD薄膜的好的台阶覆盖。
低的淀积温度和好的台阶覆盖使PECVD薄膜成为理想的金属间绝缘介质。
它的淀积温度必须保持在450℃以下,以防止铝膜中主要问题的产生(钉、小丘)。
PECVD二氧化硅不如TOX或HTO紧密,在结构上也不如TOX或HTO均匀一致,因此它蚀刻的较快。
BPSG/PSG
BPSG或PSG在反应室中通过加掺杂物(P或不加B)淀积而成。
淀积的二氧化硅作为湿气的扩散阻挡层和碱性离子的吸收器,在应力、台阶覆盖方面显示了良好的性质。
BPSG和PSG薄膜在淀积后可以在高温下流动以平整表面和减少缺陷(在这方面BPSG优于平时感,它可以在较低温度下回流)。
通常BPSG用作硅片衬底上或多晶线上的钝化层因对其平坦化比其它薄膜有另外的优点,它的保形性不如TEOS或LTD,故表曾会在表面流动。
BPSG的蚀刻数率依赖于掺杂程和致密化程度度,随着掺杂浓度增加,蚀刻数率也增加;密度减小,蚀刻数率增加。
掺杂不均匀性将导致蚀刻不均匀性。
4.二氧化硅选用的考虑事项
a. 薄膜的保形性 stepcoverage
b. 淀积温度temperature
c. 绝缘介质一致性 isolation
d. 能否回流reflow
e. 薄膜稳定性stability
f. 应力stress
g. 湿度扩散阻挡层 moisture
h. 折射率refractive
i. 反射率reflective
j. 蚀刻速率etchrate
5.蚀刻蚀刻数率会在以下情况增加:
a.密度减小
b.淀积温度降低
c.掺杂浓度增加
均匀性最好在均质膜(特别是TOX)上测试以避免淀积不均匀对蚀刻均匀性的影响。
淀积二氧化硅的特性
淀积物
Plasma
SiH4+O2
TEOS
SiCl2H2+N20
温度(℃)
200
450
700
900
成分
SiO1.9(H)
SIO2(H)
SIO2
SIO2(Cl)
台阶覆盖
不保形
不保形
保形
保形
热稳定性
游离H
致密
稳定
游离Cl
密度(g/cm3)
2.3
2.1
2.2
2.2
折射率
1.47
1.44
1.46
1.46
应力(109dyn/cm2)
3C-3T
3T
1C
3C
绝缘强度(106v/cm)
3-6
8
10
10
蚀刻数率(?
/min)
400
60
30
30
H2O:
HF=100:
1
四、二氧化硅蚀刻机理
1.化学蚀刻
定义:
通过与气态或液态物质的反应蚀刻固体。
化学蚀刻由三步组成:
a. 反应物吸附在固体表面上
b. 产物形成,
c. 产物解吸
吸附是气态分子沾在固体上,压力、温度和粘附系数都影响吸附速率。
吸附物与固体化合形成产物,温度、反应速率和吸附速率控制产物形成速率。
产物从衬底表面解吸出来,解吸要求产物具有挥发性。
产物挥发性取决于粘附系数、压力和温度。
不易挥发的产物会在表面形成产物层而阻止进一步蚀刻。
例:
ResistASHING、干法去胶
SIO2在HF酸中湿腐
由于吸附速率、产物形成速率和产物解吸速率与方向无关,所以化学蚀刻是各向同性的。
等离子体化学活性对比:
增加速率增加
增加压力变化
增加间距 ----
增加惰性:
活性 减小
增加CF4:
CHF3增加
增加硅片湿度增加
化学蚀刻的一般影响:
注意:
蚀刻速率、选择比、各向异性和其它蚀刻参数是由复杂的等离子体/衬底相互作用而确定的。
下列趋势一般是正确的,但在特殊蚀刻应用时应当特别小心。
a. 增加化学活性:
蚀刻速率增加。
b.增加化学活性:
影响选择比变化。
SIO2蚀刻增加化学活性,减小选择比。
c.增加化学活性:
减小各向异性。
2.物理蚀刻
定义:
离子轰击蚀刻,物理蚀刻可比作一个微观风镐,高能离子冲击破坏晶体键,瓦解各个原子。
气体被电离(用TCP或RF),正离子向硅片加速,离子/衬底碰撞可能造成:
a. 晶体键断裂
b. 表面原子完全移位
c. 从衬底溅散掉。
电磁吸引力把离子垂直驱向衬低,掩膜表面和垂直表面(侧壁)没有暴露在轰击下,因此,全部蚀刻具有方向性(各向异性)。
例:
溅射
离子束铣削
物理蚀刻对比
增加功率增加
增加惰性、活性增加
增加压力减小
增加CF4、CHF3 --
增加间距--
增加硅片温度 --
物理蚀刻的一般影响
注意:
蚀刻速率、选择比、各向异性和其它蚀刻参数通常决定于变化着的复杂的等离子体/衬底的相互作用。
下列趋势一般是正确的,但在特殊蚀刻应用时应当特别小心:
a. 增加物理蚀刻:
蚀刻速率增加
b. 增加物理蚀刻:
影响选择比变化
c. 增加物理蚀刻:
增加各向异性
3.聚合反应
1) 定义:
碳氟化合物、含氯氟烃和光刻胶都对聚合物链形有作用,聚合物链淀积在衬底表面形成阻碍蚀刻的层。
2) F:
C比率
聚合速率可通过F:
C比率模拟、增大比率、减少聚合反应、减小比率、增大聚合反应。
举例:
4500利用CF4和CHF3控制F:
C比率,因此增加CF4:
CHF3的比率,也就减少了聚合反应。
3) 聚合反应机理:
聚合物通过等离子反应形成
CF4+e-→ CF3+F+e- 和 CHF3+e- → CF3+H+e-
及
CF3+e- → CF3+F- 或 CF3+H → CF2+HF
然后,聚合碳氟化合物链通过n(CF2)→(CF2)n产生。
聚合速率同样受控于离子轰击(又决定于惰性气体流量和功率)和滞留时间(又决定于压力、总流量和间距)。
4) 作用:
SIO2工艺最佳化要求精密平衡F:
C比率,聚合反应影响蚀刻速率、选择比、剖面形貌。
聚合反应对选择比要求很严格,但是过度的聚合反应会使profile倾斜,或者在极端情况下,会完全阻止蚀刻。
4500使用高能量离子轰击把F:
C比率减至极小,这样就获得了最大的选择比。
5) 聚合反应对比:
增加功率 减小
增加压力 增加
增加流量减小
增加CF4:
CHF3减小
增加硅片温度减小
增加O2减小
6) 聚合反应的一般影响:
注意:
蚀刻速率、选择比、各向异性和其它蚀刻参数通常决定于变化着的复杂的等离子体/衬底的相互作用。
下列趋势一般是正确的,但在特殊蚀刻应用时应当特别小心:
a. 增加聚合反应:
减小蚀刻速率
b. 增加聚合反应:
增加选择比
c. 增加聚合反应:
使profile倾斜
4.工艺机理 各向异性
三个主要机理:
离子轰击、聚合反应和腐前胶刻面形貌控制各向异性。
离子轰击:
a. 蚀刻反应只有在离子轰击存在时才大量发生。
b. 离子轰击垂直于硅片表面。
c. 蚀刻各向异性程度很高。
5.离子辅助蚀刻
定义:
蚀刻过程是化学和物理蚀刻作用的叠加,离子辅助蚀刻在某些应用场合可以提高蚀刻速率和各向异性。
1) 离子轰击在蚀刻中的作用
除衬底溅射外(如前“物理蚀刻”所述),离子轰击起双重作用,它清洗水平聚合物表面,增加能量以激活衬底和反应物(自由基、F或CF3)之间的反应。
见图,氩气比氦气重得多,故被选为SIO2蚀刻的离子源。
这个作用是关键性的,没有高能量离子轰击SIO2在CF4/CHF3等离子体中不会蚀刻。
2) 例:
4500中SIO2蚀刻
Si与XeF2和Ar+束蚀刻
6.SIO2蚀刻工艺机理:
蚀刻速率
1) 化学反应
回顾化学蚀刻要求反应物吸附在硅片表面和产物解吸,因为SIO2同碳氟化合物蚀刻,反应物是典型自由基F或CF3。
CF4+e- → CF3+F+e-
自由基是典型的易化学反应的、易与邻近表面结合的。
典型产物是SiF4、CO和CO2,例如
4CF3+3SIO2 → 3SiF4+2CO2+2CO
一个易理解的SIO2衬底表面会在CF3吸附后出现。
2) 离子轰击
阳极电离的氩气表面、激活吸附的CF3(或F)和衬底之间的反应。
Si-O键的强度是200Kcal/mol,大于2倍的Si-Si键的强度—80Kcal/mol。
没有离子轰击,反应(及蚀刻)就会终止。
在离子轰击下,CF3基团就能够穿透SIO2表面,继续蚀刻,见图。
3) 聚合反应
如上述,碳氟化合物链形成阻挡层减慢或中止蚀刻(这些链在选择比上起了非常重要的作用)。
蚀刻速率对比:
增加功率增大
增加压力变化
增加间距 ---
增加CF4:
CHF3减小
增加惰性:
活性增大
增加硅片温度增大
7.工艺机理:
各向异性
1) 聚合反应
聚合物在垂直表面上的建立比水平表面容易得多(见“离子辅助蚀刻”)。
随着聚合反应强度增加,越来越多的聚合物沿着侧壁逐渐淀积产生正倾斜的斜度。
腐前胶剖面Preetch Resist Profile
理想的胶刻面是垂直的,由于SIO2:
胶选择比比较高,轻微的正的胶倾斜度也可以,较斜的胶或resist foots会产生一个正斜度。
2) 各向异性对比:
增加功率更垂直
增加压力减小垂直
增加间距---
增加CF4:
CHF3更垂直
增加惰性:
活性更垂直
增加硅片温度更垂直
8.工艺机理:
选择比
1) 两个主要机理:
离子轰击和聚合反应控制选择比
2) 聚合反应
聚合物在硅表面淀积比在SIO2表面淀积容易得多。
氧气(来自SIO2)同聚合物链反应形成易挥发的CO或CO2。
这样,聚合物链在SIO2表面上形成之前就被破坏了。
硅没有内部氧源,不能破坏聚合物链,这样,聚合物容易覆盖硅表层,这就是SIO2:
Si选择比机理。
3) 离子轰击
离子轰击是用来维持SIO2蚀刻必要的,清除表面聚合物抵消了聚合物淀积在选择比上的益处。
这一点在蚀刻中通常是正确的,两个(或更多)效应必须适当平衡以达到目的。
这里相冲突效应是离子轰击和聚合作用,都起到了关键性作用。
4)选择比对比:
增加功率减小
增加压力增大
增加间距 ---
增加CF4:
CHF3增大
增加惰性:
活性减小
增加硅片温度减小
9.工艺机理:
均匀性
均匀性通过等离子体和硬件之间复杂的相互作用确定。
均匀性可以用不同参数测出,最常用的是蚀刻速率和CD(profile)。
设计参数影响均匀性:
1) 径向设计:
Lam反应室是径向设计的,就是说,气流从中心流出,硅片在中心弓形突出。
2) 气流缓冲(见前章)
3) 工艺参数影响均匀性:
a. 气流/压力:
气流影响滞留时间,这是蚀刻物活性和聚合物反应程度的关键。
理想的气流应当均匀地通过硅片,因此,反应室设计成径向的,这样硅片边缘的气流必定高于硅片中心。
b. 硅片温度:
硅片温度均匀性是由clamping/helium冷却系统控制的。
通常,均匀的温度可以被维持,因此,为了补偿其它的不均匀性,有时希望中心和边缘的温度失衡。
c. 离子轰击:
等离子体是通过硅片和填充的氦形成的电容耦合到下电极的阻抗正比于距离。
氦气冷却引起硅片弓形,产生中心与边缘的不同阻抗。
低阻抗边缘接受的离子轰击多于高阻抗中心。
五、其他
1.二氧化硅蚀刻的四个基本机理:
是化学蚀刻、物理蚀刻、聚合反应和离子辅助蚀刻。
蚀刻速率、各向异性、选择比和均匀性分别与这些机理的相互作用有关。
2.4500:
低频二氧化硅蚀刻
1) 400KHZ与1356MHZ相比较:
离子电压
高能量离子轰击对于氧化蚀刻是必要的。
高频等离子体驱动使离子处于等离子势能,因为离子迁移时间大大多于一个简单波的周期时间:
1/freq=7.4 ×10-8 (s)。
(见3.3等离子体基本原理)低频等离子体靠输运外场(近似于电极电压)来驱动离子,因为离子迁移时间小于一个波的周期时间,离子峰压值不是靠等离子体来调节的.
2) 优点
这样就产生了扩散的等离子体;具有一定能量的离子应当指向硅片,却指向了反应腔壁,同样,二氧化硅辐射需要聚合物,聚合物的聚集会改变等利息、等离子体的势能.等离子体势能(由此,离子能量)的改变会改变蚀刻结果.等离