材料成型及控制工程课程设计14MnNb分离器焊接生产工艺设计.docx
《材料成型及控制工程课程设计14MnNb分离器焊接生产工艺设计.docx》由会员分享,可在线阅读,更多相关《材料成型及控制工程课程设计14MnNb分离器焊接生产工艺设计.docx(23页珍藏版)》请在冰点文库上搜索。
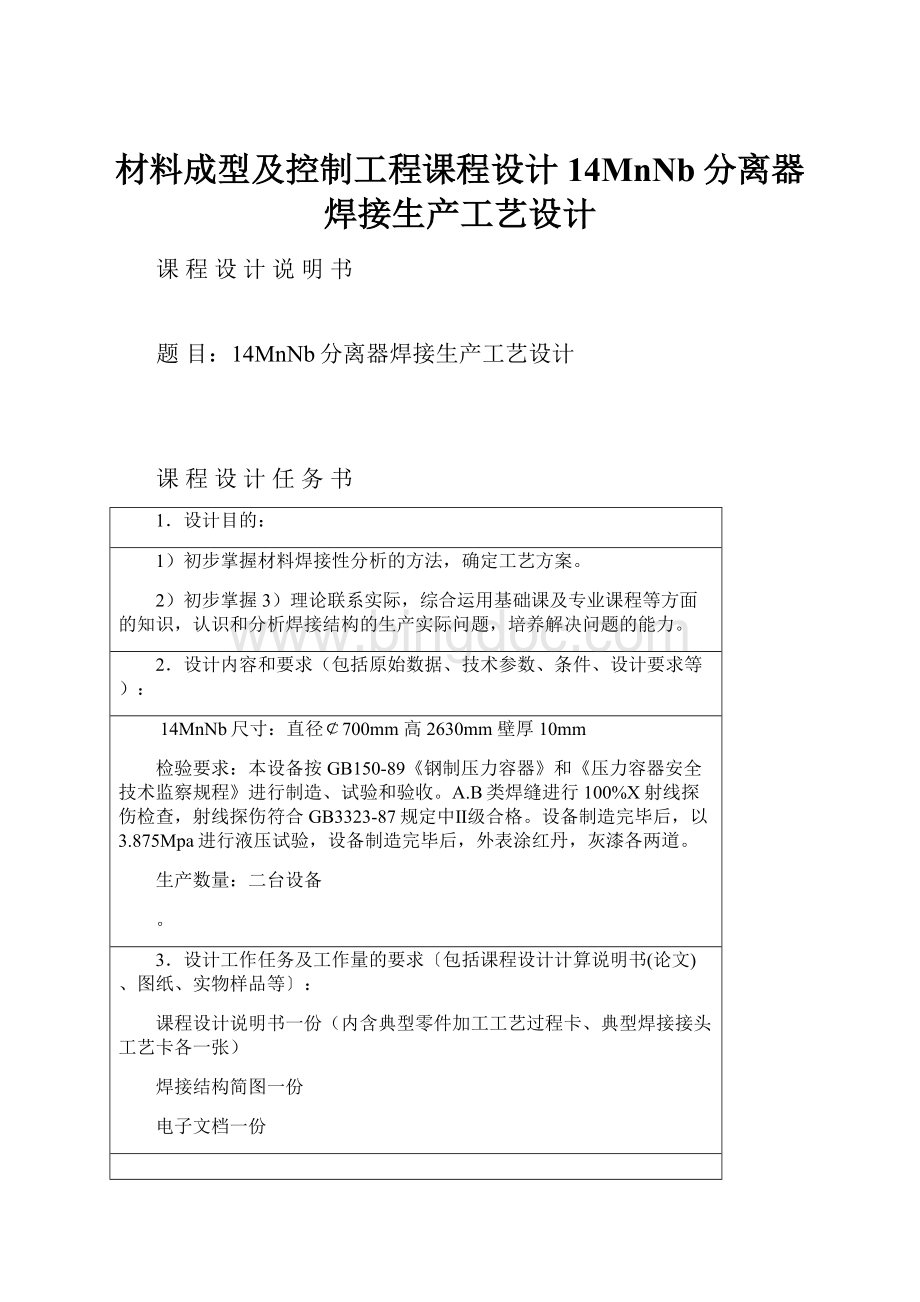
材料成型及控制工程课程设计14MnNb分离器焊接生产工艺设计
课程设计说明书
题目:
14MnNb分离器焊接生产工艺设计
课程设计任务书
1.设计目的:
1)初步掌握材料焊接性分析的方法,确定工艺方案。
2)初步掌握3)理论联系实际,综合运用基础课及专业课程等方面的知识,认识和分析焊接结构的生产实际问题,培养解决问题的能力。
2.设计内容和要求(包括原始数据、技术参数、条件、设计要求等):
14MnNb尺寸:
直径¢700mm高2630mm壁厚10mm
检验要求:
本设备按GB150-89《钢制压力容器》和《压力容器安全技术监察规程》进行制造、试验和验收。
A.B类焊缝进行100%X射线探伤检查,射线探伤符合GB3323-87规定中Ⅱ级合格。
设备制造完毕后,以3.875Mpa进行液压试验,设备制造完毕后,外表涂红丹,灰漆各两道。
生产数量:
二台设备
。
3.设计工作任务及工作量的要求〔包括课程设计计算说明书(论文)、图纸、实物样品等〕:
课程设计说明书一份(内含典型零件加工工艺过程卡、典型焊接接头工艺卡各一张)
焊接结构简图一份
电子文档一份
课程设计任务书
4.主要参考文献:
5.设计成果形式及要求:
设计说明书一份;零件加工工艺卡一张;焊接工艺卡一张。
焊接结构简图一份(用AutoCAD绘制);
说明书计算机打印,装订成册
6.工作计划及进度:
2007年12月24日~12月25日:
收集资料,复习与补充相关的知识。
2007年12月26日~12月29日:
材料焊接性分析,确定工艺方案。
2008年1月2日~1月5日:
确定焊接结构生产工艺流程、确定产品主要零件的加工工艺及检验。
1月7日~1月12日:
绘制焊接结构简图;确定部件的装配工艺及焊接工艺;典型工装的方案设计;检验设计。
1月14日~1月18日:
编制课程设计说明书、答辩及成绩考核。
系主任审查意见:
签字:
年月日
目录
…………………………………………………………………………………2
1.1焊接结构工艺性审查………………………………………………………2
2母材焊接性分析及试验方法……………………………………………………3
2.1母材的成分及性能…………………………………………………………3
2.2母材的焊接性特点……………………………………………………………4
2.3母材的焊接工艺要点…………………………………………………………4
2.4母材焊接性试验内容及方法………………………………………………5
2.5焊接工艺评定…………………………………………………………………9
3主要零件的加工制造………………………………………………………13
3.1筒体的加工制造……………………………………………………………13
3.2封头的加工制造:
……………………………………………………………14
3.3法兰的加工制造……………………………………………………………15
3.4接管的加工制造………………………………………………………………15
4部件的装配及焊接工艺………………………………………………………16
4.1装焊阶段的工艺选择……………………………………………………………16
4.2各部件的装配、焊接工艺………………………………………………………17
5产品质量检验………………………………………………………………………21
……………………………………………………………21
………………………………………………………………21
……………………………………………………………22
…………………………………………………………………23
6液压试验……………………………………………………………………………24
7气密性实验……………………………………………………………………24
8总结……………………………………………………………………24
参考文献……………………………………………………………………………25
1绪论
焊接工艺焊接工艺作为一种重要的金属加工工艺,在现代工业中占有十分重要的地位,广泛应用于国民经济建设的各个行业,在生产和建设中发挥着极其重要的作用。
此次焊接工艺设计的目的是初步掌握材料焊接性分析的方法,确定焊接工艺方案;初步掌握焊接结构的零件加工、装配、焊接等工艺规程的编制方法;理论联系实际,综合运用基础课及专业课程多方面的知识去认识和分析焊接结构的生产问题,培养解决问题的能力。
1.1焊接结构工艺性审查:
此次生产设计的容器为分其制造按GB150—89《钢制压力容器》和《压力容器安全技术监察规程》等标准进行制造、试验和验收,A、B类焊缝要进行100%X射线探伤检查,射线探伤要符合GB3323—87规定中的Ⅱ级合格。
设备制造完毕后,以3.875Mpa进行液压试验,设备制造完毕后,外表涂红丹,灰漆各两道。
从图纸上可看出,该分离器为圆筒形壳体,其基本结构主要由以下几大部分组成:
筒体、封头、法兰、法兰盖、密封元件、接管和支座等,该设备结构设计合理,主要加工手段为焊接,焊接接头主要是对接、角接,焊缝质量易于保证,焊缝布置合理,施焊方便,有利于焊后检验,具有良好的工艺性。
2.母材(14MnNb)焊接性分析及实验方法:
2.1母材(14MnNb)的成分及性能:
(1)简述:
14MnNb钢是以微量铌替代部锰发展起来的屈服强度345MPa级的低合金高强度钢。
该钢性能相当于16Mn钢。
但C和Mn含量都比16Mn钢低。
其用途除同于16Mn钢外,还可用于使用温度在-20—450含碳量限制在0.2%以下,属于低合金钢中的热轧钢,这类钢价格便宜而且具有满意的综合力学性能和加工工艺性能。
这类钢的基本成分为:
C≤0.2%,Si≤0.55%,Mn≤1.5%。
含Si量超过0.6%后对冲击韧度不利,使脆性转变温度提高,含C量超过0.3%和含Mn量超过1.6%后,焊接时经常出现裂纹,同时在热轧板上还会出现脆性的贝氏体组织,因此为了保证这类钢具有较好的焊接性和缺口韧性,它的σs受到了一定的限制。
这类钢在热轧状态下的σs一般限制在343MPa的水平。
(2)14MnNb钢的化学成分见表2-1所示:
表2-114MnNb钢的化学成分(%)
钢号
C
Si
Mn
Nb
Mo
Cr
V
S
P
14MnNb
0.12~0.18
0.20~0.60
0.80~1.20
0.015~0.050
/
/
/
≤0.045
≤0.050
14MnNb钢中由于Nb的强化作用有可能适当的降低钢中的的含碳量,对改善材料的焊接性和韧性都是有利的,这类钢的特点是屈强比高,另外Nb可以提高钢的热强性,因此这类钢适合制造压力容器。
(3)冶金工艺
冶炼:
可采用平炉,氧气转炉或电炉冶炼
轧制:
开轧温度11120-12502.2母材的焊接性特点:
(一)焊缝中的热裂纹:
①具有较好的抗热裂性能;②但当材料成分不合格,或因严重偏析使局部碳、硫含量偏高时Mn/S比就可能低于要求而出现热裂纹;③硫对形成热裂纹起直接作用,钢中的C、Si、Ni促进有害作用,Mn抵消有害作用。
(二)冷裂纹:
(1)淬硬倾向与冷裂倾向的关系:
热轧钢的淬硬倾向比低碳钢的淬硬倾向大,并且随着钢材强度级别的提高淬硬倾向逐渐增大。
(2)当量与冷裂纹倾向的关系:
冷裂倾向→淬硬倾向→化学成分→碳的作用.通过一些经验性的碳当量公式来粗略地估计不同钢材的冷裂倾向。
热轧钢碳当量都比较低,除环境温度很低或钢板厚度很大,一般情况下其裂纹倾向都不大。
(3)影响区的最高硬度值与冷裂倾向关系:
为了避免产生对冷裂敏感的淬硬组织,可将热影响区的最高硬度控制在某一刚好不出现冷裂纹的临界值;反过来也可根据测得的热影响区的最高硬度值来判断材料的冷裂倾向和确定预热温度。
(三)再热裂纹:
C-Mn和Mn-Si系热轧钢对再热裂纹不敏感。
(四)层状撕裂:
层状撕裂的产生不受钢种和强度的限制,它主要发生于厚板结构中(在热影响区甚或远离热影响区的母材中)。
在低碳钢、热轧、正火钢中都可能发生层状撕裂。
(五)热影响区的性能变化:
(1)过热区脆化:
焊接接头温度高发生了奥氏体晶粒的显著长大和一些难熔质点(如氮化物或碳化物)的溶入。
溶入的难熔质点在冷却过程中,来不及析出会使材料变脆;过热粗大的奥氏体冷却下来会转变成魏氏体、粗大的马氏体及塑性很低的铁素体、高碳马氏体和贝氏体的混合组织和M-A组元。
热轧钢:
①焊接线能量过大,导致冷速过慢,使韧性降低;焊接线能量过小,使韧性降低;②过热区性能的脆化与钢材化学成分有关,以COD值表示断裂韧性的大小。
③0.17C-1.1Mn钢O℃时,没有出现脆性,在试验温度降低时,因受线能量影响而表现出韧性下降。
(2)热应变脆化:
①产生在热影响区中发生过塑性变形同时受热温度在ACl以下、尤其最高加热温度在200-400℃的区间。
②这种脆化是由于氮原子聚集在位错周围,对位错造成钉扎作用所造成的。
③发生在固溶氮含量较高的低碳钢和强度级别不高的低合金钢中。
2.3母材焊接工艺要点:
(1)坡口加工、装配及定位焊
坡口加工可采用机械加工,也可采用火焰切割或碳弧气刨。
在坡口两侧约50mm范围内,应严格去除水、油、锈及污物等。
焊件的装配间隙不能过大,避免强力装配定位。
为防止定位焊焊缝开裂,要求定位焊焊缝应有足够的长度(一般不小于50mm),对厚度较薄的板材不小于四倍板厚。
定位点固焊应选用与焊接同类型的焊接材料,也可选用强度等级稍低的焊条或焊丝。
定位焊的顺序应能防止过大的拘束,允许工件有适当的变形,焊点或点固焊缝应对称均匀分布。
定位焊所用的电流可稍大于焊接时的焊接电流。
(2)预热和焊后热处理
强度级别高或厚度较大的结构件焊前应预热,焊后进行热处理。
如焊后不能及时进行热处理,应立即在200-350热轧及正火钢焊接对焊接方法的选择无特殊要求,手工电弧焊、埋弧自动焊、气体保护焊、电渣焊、压焊等焊接方法都可采用。
可根据产品的结构、板厚、使用性能要求及生产条件等选择。
其中,手工电弧焊、埋弧自动焊、CO2气体保护焊是热轧及正火钢常用的焊接方法。
2.4母材焊接性试验的内容及方法:
1)工艺焊接性实验:
(1)14MnNb钢焊接热裂纹敏感性试验方法:
可调拘束裂纹试验法,如图2-1所示:
试件尺寸为10mm×80mm×350mm钢板,把试件装在试验装置上,使用选好
经烘干后按规定的工艺参数(焊条直径:
4mm、焊接电流:
170A、电弧电压:
24~26V、焊接速度:
150mm/min)进行焊接,可采用TIG重熔,按图所示,从A点到C点进行焊接,当电弧到B时,在试件一端加压力P,使试件按模块的曲率发生强制变形,此时电弧到C点后熄弧,通过变换不同曲率半径摸板,可使焊缝金属产生不同应变量(ε)其拉伸应变量的大小按下式计算:
ε=
×100%R为曲率半径,当ε达某一临界值时,在焊缝和热影响区就会出现裂纹,随ε值增大,出现裂纹的数量、长度都会增加,从而可得一系列的数据作为评定热裂纹敏感性的指标,其中εCr、Lmax、BTR等都是反映热裂纹敏感性的一个特性指标,而CST能综合反映材料的冶金因素和工艺因素对热裂纹倾向的影响。
(2)冷裂纹:
图2-2插销试验及试棒尺寸
(3)焊接再热裂纹敏感性实验方法:
斜Y形坡口再热裂纹试验法,所用的试件形状和尺寸与冷裂纹试验完全相同,试验的程序和要求也基本与冷裂纹试验一样,只是为防止冷裂纹,应在焊前预热,焊后经检查无裂纹后再进行消除应力处理,处理的工艺参数一般为500-700℃,2小时然后进行裂纹检测,以裂与不裂为标准。
(4)层状撕裂实验法:
Z向拉伸实验法,利用钢板厚度方向(即Z方向)的断面收缩率来评定钢材的层状撕裂敏感性。
试件的制取及其形状尺寸见图2-3.同常规拉伸试验一样,对试件进行试拉试验,得出Z向断面收缩率作为层状撕裂的评定指标。
标准见表2-3.
图2-3Z向拉伸试验
表2-3抗层状撕裂标准分类
级别
含硫量%
Z向断面收缩率%
备注
ZA级
ZB级
ZC级
ZD级
≤0.01
≤0.008
≤0.006
≤0.004
未规定
≧15—20
≤25
≤30
一般应≧15%
一般
良好
优异
2)使用焊接性能实验:
(1)焊接接头力学性能实验:
1)拉伸实验,主要目的是测定焊缝或焊接接头的强度和塑性且可发现断口上的某些缺陷,如夹扎物、未焊透或白点等。
2)焊接接头弯曲实验,目的是测定焊接接头的塑性和致密性,,同时反映出焊接接头各区域的塑性差别,暴露焊接缺陷和考核熔合区的质量,弯曲实验分面弯、背弯和恻弯三种,也可将试样弯至规定弯曲角度后检查有无裂纹,,以评定接头区域的韧性。
3)冲击实验,用于测定接头的冲击韧度和缺口敏感性,是评定材料断裂韧度和冷作时效敏感性的指标之一,冲击实验分U型缺口和V型缺口冲击实验。
(2)焊接接头抗脆断性能实验:
1)韧脆转变温度的确定,随实验温度的降低,金属材料由韧性状态过度到脆性的温度称韧脆转变温度,将V型缺口冲击试样冷却到不同温度进行系列冲击实验可确定韧脆转变温度。
2)焊接接头断裂韧度实验,金属材料在弹性加载下发生的破坏一般为脆性断裂,断裂韧度是表示材料阻止脆性断裂的性能,常用的断裂韧度参数有KIC、、COD等。
3)焊接接头疲劳实验,试验方法有旋转弯曲试验法和轴向疲劳试验法,并分为高周疲劳和低周疲劳,疲劳实验是采用一定的应力循环特性的载荷进行多次反复加载试验,测得使试样破坏所需的加载循环次数N,将破坏应力与N绘成疲劳曲线,可获得不同循环下的疲劳强度及疲劳极限。
2.5焊接工艺评定:
(1)焊接工艺评定用试件:
a、对接焊缝试件及坡口形式、尺寸如图2-4所示:
图2-4对接焊缝试件
b、角焊缝试件,尺寸如图2-5所示,板材角焊缝试件尺寸如表2-4所示:
图2-5角焊缝试件
表2-4板材角焊缝试件尺寸:
/mm
翼板厚度T1
腹板厚度T2
≦3
T1
>3
≦T1但不小于3
注:
焊角高为T2
(2)试样的截取及数量:
1)对接焊缝试样,对接接头力学性能试验有拉伸、弯曲、冲击三项试验。
a、拉伸试样按图2-6所示形状制作:
图2-6拉伸试件
b、
横向弯曲试样
纵向弯曲试样
图2-9
焊逢上的余高或垫板应用机械法去除,试件受拉伸表面平齐,尽可能的保留焊缝两侧中至少一侧的母材是原始表面。
2)角焊缝试件:
a、角焊缝试件只作外观检查和金相检验,取4个试样,焊缝的起始和终止位置应位于焊缝的中部,每一个试样取一个面进行金相检验。
b、对角焊缝进行外观检查,其表面不得有裂纹,未熔合缺陷.然后取样,并对试样受检面进行机械加工的磨光,直至清晰的分辨出焊缝和热影响区。
c、宏观金相试验合格的标准是焊缝根部应焊透,焊缝金属和热影响区不得有裂纹和未熔合,角焊缝两焊脚高之差不宜大于3mm。
(3)检验和合格标准:
1)拉伸试验,应按GB/T228-1987规定的程序对拉伸试样进行拉伸强度试验,合格标准为:
a、试样母材为同种钢号时,每个试样的抗拉强度应不低于母材钢号标准值的下限。
b、试样母材为两种钢号时,每个试样的抗拉强度应不低于两种钢号标准值下限的较小值。
c、当采用两片或多片试件时,每片时样的抗拉强度都应符合上述规定。
单片试样如果断在焊缝或熔合线以外的母材上,其最低值不得低于母材钢号标准值下限的95%。
2)弯曲试验,应按GB/T232-1988规定的程序对弯曲试样进行弯曲试验,试验市时,应将焊缝的中心轴线对准弯轴轴线,使焊缝和热影响区都在试样的受弯部分,横向和纵向面弯时,应将焊缝的正面对着弯横间距放置,使其弯曲时受拉,背弯时,则使焊缝的背面受拉,侧弯时,发现表面有焊接缺陷,应将缺陷较大的侧面为弯曲试样的受拉面。
合格标准按JB4708-2000的规定。
3.各主要零件的加工制造方法:
3.1筒体的加工制造:
(1)放样、划线:
包括展开、放样、划线、打标记等环节,筒节的划线是在钢板上划出展开图,当在普通三辊卷扳机上弯卷时,几乎是纯弯曲作用,可不考虑钢板弯卷时的伸长量。
筒节展开长按:
L=πDm=π(Di+S)计算,
其中:
L——筒节展开长mmDi——筒节内径mm
Dm——筒节平均直径mmS——板厚mm
(2)下料切割:
采用数控等离子弧切割机切割下料。
(3)筒节卷制:
大部分化工容器的筒节都是用板料在卷扳机上卷制的。
1)卷扳机的种类:
按辊子数目卷扳机分三辊和四辊两种,但因辊子的布置和移动方式不同又可分多种形式,常用对称三辊卷扳机。
2)筒节卷制过程:
a、预弯,筒节的板端常在压力机上预弯,也可在三辊卷扳机上加垫板预弯。
b、卷筒,板料入辊时要保证筒节的母线于辊轴的轴线相平行,卷制大直径的筒节时,若伸出辊子外边的弧段较大,需用吊车将伸出的弧段吊起。
c、筒节纵缝组焊,一些刚度大的筒节可直接在卷扳机上定位焊后卸下。
d、矫圆,纵缝焊接后应对筒节矫圆,在卷扳机上进行。
3)筒节的基本成型工序为:
用矫正机进行矫正)
3.2封头的加工制造:
椭圆形封头如图3-1所示:
图3-1椭圆形封头
椭圆形封头毛坯尺寸的计算:
椭圆半轴长的近似计算公式:
椭圆形基本成型工序为:
材检——号料——等离子弧切割(切割时留余量5mm)——整体冲压成形——钻孔——酸洗表面——渗透探伤
采用3000t水压机一次冲击成型。
3.3法兰的加工制造:
法兰的结构尺寸如图3-2、表3-1所示:
凹凸面管法兰
法兰的4.部件的装配及焊接工艺:
4.1装焊阶段的工艺选择
表4-1
4.2各部件的装配、焊接工艺
1.筒体的环向、纵向焊接
采用型号为FZ-100的头尾架式翻转机装配,翻转机如图4-1所示:
图4-1环焊缝装配示意图
装配中,可用螺栓撑圆器、间隙调节器、筒式万能夹具和单缺油压顶圆器等辅助工具和有关量具来矫正、对中、对齐。
采用单面全焊透对接接头形式,如图4-2所示:
图4-2对接接头
1)材料:
14MnNb2)焊接位置:
平焊
3)焊接方法:
埋弧焊
4)焊接材料:
焊丝H08MnA 焊剂HJ350
5)焊接参数:
焊接电流550~570A电弧电压36~40V
焊接速度28~32m/h焊丝直径2.4mm
6)设备型号:
MZ1-1000埋弧焊机
2.封头与筒体的装配
采用型号ZT-100的焊接回转台装配。
回转台如图4-3所示:
图4-3回转台
采用对接接头:
1)焊接方法:
采用MAG焊
2)焊接工艺参数:
焊接电流:
310~320A电弧电压:
26~27V
焊接速度:
7~9mm/s焊丝直径1.6mm
3)设备型号:
NB-500熔化极MAG焊机
法兰与接管的装配
在焊接变位器上进行两者都用夹紧器夹紧先定位焊再环焊。
要控制法兰平面相对接管轴线垂直度偏差不大于1%且不大于3mm,接管伸出高度误差不大于5mm。
采用带钝边双J形坡口,如图4-5所示:
图4-5带钝边双J形坡口
1)焊接方法:
采用MAG焊
2)焊接工艺参数:
电弧电流:
150~155A电弧电压:
19~20V
焊接速度:
5~7mm/s焊丝直径0.89mm
3)设备型号:
NB-500熔化极MAG焊机
4.上封头与接管的焊接
采用带钝边单边V形坡口,如图4-6所示:
图4-6带钝边单边V形坡口
1)焊接方法:
用MAG焊,
2)焊接工艺参数为:
焊丝直径:
1.6mm电弧电压:
27~28V
电弧电流:
360~370A焊接速度:
6~8mm/s
3)设备型号采用NB-500熔化极MAG焊机。
5.支座的焊接
接头形式如图4-7所示:
图4-7角接接头形式
1)焊接方法:
采用MAG焊
2)焊接工艺参数:
焊接电流:
310~320A电弧电压:
26~27V
焊接速度:
7~9mm/s焊丝直径1.6mm
3)设备型号:
NB-500熔化极MAG焊机
5.产品质量检验
a.检查项目:
(1)外观检验:
1)容器本身、对接焊缝、接管等角焊缝等部位的裂纹、过热、变形、泄露等,以肉眼或5~10倍放大镜检查裂纹;2)内外表面的腐蚀和机械损伤;3)紧固螺栓;4)支座检查。
(2)结构检查:
1)筒体与封头的连接处;2)封头、开孔、支座、角接、法兰、法兰盖和接管等。
(3)几何尺寸检查:
1)纵环焊缝对口的错边量、棱角度;2)焊缝余高、角焊缝的焊缝厚度与焊脚尺寸;3)同一断面最大直径与最小直径;4)封头表面凹凸量、直边高度和直边部位的纵向皱折;5)容器的铅垂度。
b.所用设备
手电筒、5~10倍放大镜、反光镜、内窥镜、0.5Kg尖头手锤、直尺、钢卷尺、样板、游标卡尺、塞尺、焊缝检查尺等。
c.检验程序
(1).产品总体尺寸:
1)机械加工面的自由尺寸允许偏差按GB/T1804中的m级;2)非机械加工面自由尺寸允许偏差按GB/T1704中的c级;3)壳体直线度允差不大于壳体长度的1%,任意2000mm长筒段的偏差不得大于2mm;4)对接管的标高偏差为±6mm,伸长长度允许偏差为±5mm;5)法兰的螺栓孔应与壳体主轴线或铅垂线跨中布置;6)接管法兰面应垂直于接管或壳体的主轴中心线,接管法兰应保证法兰面的水平或垂直,其偏差均不得超过法兰外径的1%,且不大于3mm。
(2).接头尺寸:
1)焊缝余高,A、B类焊接接头焊缝余高
=0~15%
,且≤4,
=0~1.5,焊缝宽度允差≤4mm;2)C、D类接头焊角高K图样无规定时,取焊件中较薄之厚度,补强圈焊角高度取补强圈厚度的70%,且不大于8mm。
(3).主要零部件尺寸
①封头尺寸检测:
a)封头成形后其最小壁厚度应不小于其名义厚度减去钢板负偏差;b)封头直边部分的纵向皱褶深度应不大于1.5mm。
②筒体:
a)A、B类焊接接头的对口错边量b,对于A、B类来说应≤
;b)在焊接接头环向形成的棱角E,用弧长等于1/6内径且不小于300mm的内样板或外样板检查,其E值不得大于
且不大于5mm。
③法兰几何尺寸:
a)法兰密封面为凹凸面形式时,凹面与凸面的外径公差按GB/T1801的规定,孔为H12,轴为h12;b)螺栓通过孔中心圆直径和相邻两螺栓通过弧长的允差为±0.6mm,任意两螺栓通过孔弧长的允差为±1.5mm;c)上述规定外的未注公差按GB/T1804的m级规定。
④管口方位及尺寸:
a)容器的管口方位均以设计管口方位为准;b)管口沿设备轴向的定位尺寸符合图样的基准;c)管口沿设备轴向的定位尺寸与基准之间的度数,应符合图样;d)检测管口沿设备周向的定位尺