延迟焦化装置主要设备及操作管理.docx
《延迟焦化装置主要设备及操作管理.docx》由会员分享,可在线阅读,更多相关《延迟焦化装置主要设备及操作管理.docx(75页珍藏版)》请在冰点文库上搜索。
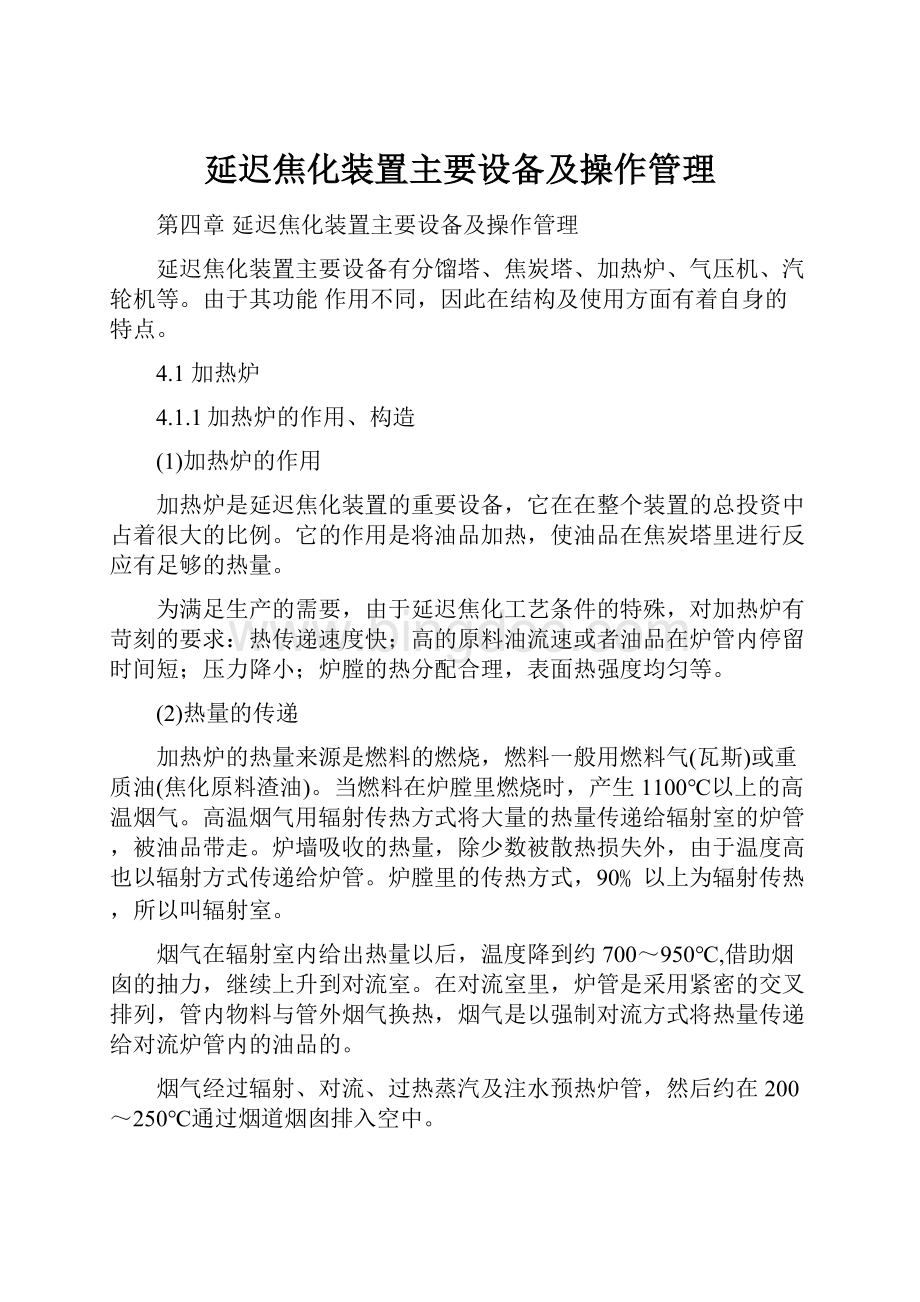
延迟焦化装置主要设备及操作管理
第四章延迟焦化装置主要设备及操作管理
延迟焦化装置主要设备有分馏塔、焦炭塔、加热炉、气压机、汽轮机等。
由于其功能作用不同,因此在结构及使用方面有着自身的特点。
4.1加热炉
4.1.1加热炉的作用、构造
(1)加热炉的作用
加热炉是延迟焦化装置的重要设备,它在在整个装置的总投资中占着很大的比例。
它的作用是将油品加热,使油品在焦炭塔里进行反应有足够的热量。
为满足生产的需要,由于延迟焦化工艺条件的特殊,对加热炉有苛刻的要求:
热传递速度快;高的原料油流速或者油品在炉管内停留时间短;压力降小;炉膛的热分配合理,表面热强度均匀等。
(2)热量的传递
加热炉的热量来源是燃料的燃烧,燃料一般用燃料气(瓦斯)或重质油(焦化原料渣油)。
当燃料在炉膛里燃烧时,产生1100℃以上的高温烟气。
高温烟气用辐射传热方式将大量的热量传递给辐射室的炉管,被油品带走。
炉墙吸收的热量,除少数被散热损失外,由于温度高也以辐射方式传递给炉管。
炉膛里的传热方式,90﹪以上为辐射传热,所以叫辐射室。
烟气在辐射室内给出热量以后,温度降到约700~950℃,借助烟囱的抽力,继续上升到对流室。
在对流室里,炉管是采用紧密的交叉排列,管内物料与管外烟气换热,烟气是以强制对流方式将热量传递给对流炉管内的油品的。
烟气经过辐射、对流、过热蒸汽及注水预热炉管,然后约在200~250℃通过烟道烟囱排入空中。
这么高温度的烟气排空,要带走大量的热量,烟气的温度越高,带走的热量就越多,加热炉的热效率就越低。
所以,如何减少热损失,提高加热炉的效率,对于炉型选用和设计、生产操作与管理都应该引起重视。
(3)加热炉的构造
炼油厂的加热炉型式很多,结构也不一样。
但是,一个完整的加热炉,不管形式如何,大致都由以下部分组成。
①辐射室辐射室也称为炉膛,这是燃料燃烧和辐射放热(或油品吸热)的地方,辐射室排列着供油品加热用的炉管,炉管的编号顺序一般都是人下向上编排,即最下面的一根为第一根。
炉管两端由管板和固定吊挂支撑,管板、吊挂因炉型结构不同而不同。
②对流室对流室也称对流段,是高温烟气对流放热(或油品吸热)的地方。
立式炉和无焰炉都把对流室放在辐射室的顶上,对流室排列着供油品加热的对流炉管,对热蒸汽管和注水预热管,靠各式管板固定在对流室内。
炉体从外表看,对流定比辐射室体积小得多。
但是,内部排列着密密麻麻的炉管,目的是强化对流传热,降低烟气温度,提高炉的热效率。
③燃烧器燃烧器也称火嘴,是加热炉提供热量的部件,各种气体(或液体)燃料通过各式火嘴来燃烧发热。
火嘴是根据炉型、燃料种类和每个火嘴提供热量的多少而选择的。
如图4-1-1~图4-1-3所示。
④烟道及烟囱烟道和烟囱是加热炉烟气集合和排放的地方,立式炉和无陷炉的烟道烟囱均放在对流室的上面。
烟囱的粗细和高度是根据烟气量和烟气阻力来设计的。
⑤弯头及弯头箱每根炉管之间是靠弯头连结的,目的为了换管和检修方便。
根据炉管尺寸、材质、流向以及生产条件选择合适的弯头型号规格,一般焦化加热炉的辐射炉管回弯头是25级的,材质是铬钼合金,如图4-1-4所示。
回弯头系列中按压力分为25Mpa、65Mpa、100Mpa三种通径有60、89、102、114、127、152、219mm七种,壳体材质有ZG25、30CrMoA、Cr2Mo、Cr5Mo四种。
回弯头的代号表示方法为:
级数——转向(90°或180°)——通径——管心距——侧管规格。
如:
25——180°——φ127——215,即是25级、180°转向、通径127㎜、管心距215㎜。
又如65——90°——φ102,即是65级、90°转向、通径102㎜的回弯头。
90°异径变头表示方法为25——90°——φ152/127,180°焊接弯头表示方法为25——180°——φ102——203(焊)。
四联弯头表示为25——φψҨ102——172(四联).
回弯头的选用是根据加热炉的操作温度、压力等级标准而定。
回弯头压力、温度等级如表4-1-1所示。
弯头箱是弯头集中的长方箱,立式炉辐射弯头箱在两侧,无焰炉弯头箱在中间。
目的为了检修拆卸弯头方便。
⑥炉墙和钢架钢架固定在基础上,构成炉体的主要框架,炉体的一切重量完全通过钢架支撑在基础上,除炉管外钢架是加热炉耗钢较多部分,所以,合理选择炉型是节约投资的关键。
炉墙是用耐火保温材料(砖)砌挂在钢架上的,它有保温密封的作用。
加热炉的热量损失大小与炉墙的砌筑质量关系很大。
一般要求炉墙严密保温性能好,热损失不大于5﹪左右为佳。
表4-1-1回弯头压力、温度等级
公称压力Py
回弯头和
堵头材质
压紧螺栓支
承架的材质
介质工作温度/℃
410
450
475
500
525
550
操作压力/Mpa
2.5
ZG25
35Cr
2.5
2.0
1.4
30CrMoA
Cr2Mo
Cr5Mo
30CrMoA
3.5
2.5
3.8
3.8
2.5
2.5
1.6
1.6
6.5
ZG25
35Cr
6.5
5.0
3.5
30CrMoA
Cr2Mo
Cr5Mo
30CrMoA
6.5
5.0
7.0
7.0
4.0
5.5
5.5
4.0
4.0
2.8
2.8
10.0
Cr2Mo
Cr5Mo
30CrMoA
10.0
10.0
8.0
8.0
6.0
6.0
4.0
4.0
⑦辅助设备加热炉除上述主要组成部分外,还有确保安全以及借供操作检修方便的一些辅助设备。
如防爆孔、看火孔、爬梯、平台、烟道挡板及调节手柄等。
(2)立式管式加热炉
立式管式加热炉是焦化装置用的较多的一种炉型,结构如图4-1-5所示。
立式炉的炉膛为长方形,辐射炉管排列在靠近炉墙的两侧,火嘴等到距离的分布在炉底中心线的两侧,为了提高辐射能力及避免两侧火焰互相干扰,还在炉底中心线上(即两排火嘴之间),用耐火砖砌有一道高约1.3~1.5m的花墙。
从图4-1-5看出,物料在立式炉辐射室的流向,都是上进下出,然后集合在一起去焦炭塔。
从外表看,这种流程不必要,既耗费钢材,又消耗动力。
但是,仔细分析一下却不然。
从炉膛燃烧热量分配角度看,立式炉火嘴虽在下面,但高温烟气却在上面大量伟热,下面是以辐射炉墙传热为主。
换句话说,就是辐射室的上部热量大,下部热量少。
从热传递的道理讲,是希望温度较低的油品首先在高温区吸热较好。
由于温度差(热传递的推动力大),在相同流量和时间内油品所获得的热量就多,热利用也就好。
据上述分析可知,这种流程的好处是:
①上进下出的流向可以保证油品在单位时间里取得最多的热量,满足焦化工艺过程中对加热炉传递速度的要求。
②上进下出的流向,可以保证油品在高速状态下经过临界反应区,单吸热而少发生反应,避免加热炉出口几根炉管和转油线结焦。
生产实践证明,第七根至炉出口到转油线这一段结焦很薄,有时还不结焦。
立式炉设计在我国已系列化,根据热负荷的大小有800、1000、1200GJ/h等多种,由于立式炉具有供热能力大,操作方便,容易调节,金属耗量少,占地面积小,投资少等优点,发展很快,应用较广。
立式炉设计参数如表4-1-2所示。
(3)无焰板式燃烧炉(无焰炉)
无焰板式燃烧炉(无焰炉)如图4-1-6所示。
由图4-1-6可知,火嘴排在两边构成炉墙,气体燃料通过喷嘴在26400个小孔里燃烧,形成极短的火焰,把火嘴砖加热烧红,从而炉墙就成了两个均匀的发热面,达到理想的传热效果。
我国第一座大型无焰炉是1964年在大庆石油化工总厂建设投产,其他炼油厂也相继建成和投产。
实践证明,无焰炉结构简单、省钢材、占地面积小、效率高、无噪音、操作方便、调节灵活。
立式管式加热炉及无焰炉的炉管排列及油品流向,各套装置不一样,见图4-1-7至图4-1-9。
但总的指导思想都是从传热、热分配均匀、增加炉管表面热强度、减少结焦角度出发。
表4-1-2立式炉原设计参数表
序号
1
2
名称
辐射
对流
注水
过热蒸汽
辐射
对流
注水
过热蒸汽
介质
进口温度/℃
出口压力/Mpa
炉管尺寸(外径*壁厚*有效长度)/㎜
炉管数/根
炉管面积/㎡
炉管材质
渣油
390/5
510/5
φ102*10
*11480
76
Cr5Mo
渣油
230/10
370/4
φ102*10
*11480
152
10号
软化水
60/25
250/25
φ60*4
*11480
112
10号
蒸汽
120/2
220/2
φ102*8
*11480
10
10号
渣油
390/25
510/5
φ127*10
*11480
72
330
Cr5Mo
渣油
230/10
370/4
φ127*8
*11480
96
440
10号
软化水
90/28
250/25
φ60*6
*11480
56
120
10号
蒸汽
150/10
220/10
φ127*8
*11480
8
36
10号
加热炉公称能力/(MJ/h)
效率/﹪
炉膛温度/℃
66944
77.2
880
60777
冷油流速/(m/s)
1.53
1.1
烟囱(内径*高)/㎜
φ1650*1590
4.1.2加热炉的操作
4.1.2.1烘炉
凡是新建加热炉或炉膛经过大修、翻新、改造的,在开工前都要进行烘炉。
(1)烘炉的目的
烘炉的目的是为了缓慢除去炉墙砌筑过程中积存的水分,并使耐火胶泥得到充分烧结。
否则这些水分不去掉,开工时炉温上升很快,水分要急剧蒸发汽化,会造成砖缝膨胀裂纹,耐火胶泥脱落,甚至于炉墙倒塌。
(2)烘炉的操作
事先应当做好烘炉的准备,对炉体应做全面的检查,包括:
对施工质量进行验收;检查炉墙砌筑(砖缝、烟道、膨胀缝)情况;检查炉墙及保护层的质量如何;检查炉管、回弯头、堵头、顶丝、花板、吊板、防爆门、看火孔及火嘴安装情况;准备好燃料油或瓦斯的供应工作;准备好点火工具及消防安全器材;炉管及管线贯通完毕。
完成以上几项工作后,然后按烘炉升温曲线一步步地进行。
烘炉升温曲线如图4-1-10所示。
烘炉过程中要严格执行升温曲线,防止超温超压,要严格控制每个阶段的升温和降温速度,在降温过程中要作好焖炉,烘炉结束后要认真检查耐火胶泥有无裂纹、脱落,炉管管架有无变形,基础是否下沉等。
4.1.2.2点火
加热炉的点火是开炉生产的第一步,点火前后准备工作很重要。
(1)准备工作
①关好人孔、防爆门、回弯头箱门,根据平常开炉经验和季节气候变化调好烟道挡板,约开一半为宜。
②引瓦斯赶空气,采样分析含氧量小于1﹪,否则点火易回火,甚至爆炸伤人,损坏设备。
③如果用燃料油,可事先加热至80~90℃左右,脱干净水,并启动燃料油泵循环,在寒冷的北方要特别注意燃料油的伴热线保持畅通。
④炉管通汽扫净,准备进油。
(2)点火方法
加热炉点火不同于平时点火那么简单,要遵守一定的操作方法和点火步骤:
①向炉膛吹蒸汽赶瓦斯向炉膛吹蒸汽赶瓦斯先要严格检查炉前瓦斯总阀门是否关严,把各火嘴的瓦斯阀门也关死,打开炉膛两边的来火蒸汽阀门,向炉膛大量吹汽,把炉膛内残留或因阀门不关串进来的瓦斯全部赶走。
这样,不易因空气和瓦斯混合达到爆炸极限而遇火发生爆炸。
炉膛吹汽赶瓦斯是否干净,应当采样分析或者以烟囱冒汽为准,吹汽时间长短应根据具体情况而定,一般约10~15min。
②点瓦斯火嘴点瓦斯火嘴时应稍开二次风门,把用柴油浸透的棉纱缠成点火棒点着,由点火孔送入火嘴前,缓慢开火嘴瓦斯的小阀门,看到着火后,再开大瓦斯阀,取出点火棒,关好点火孔门,然后适当调节瓦斯、风门。
③点油火嘴点油火嘴时应稍开二次风门,放净雾化蒸汽中的凝结水,再慢开油阀、蒸汽阀,使燃料油雾化喷出,迅速把点火棒点着送到火嘴前,从看火也前看到点着后再适当调节油、汽配比。
油火嘴一般比瓦斯火嘴难点,有时几次点不着,或点着冒大火等。
其原因可能有:
刚开炉时,炉膛温度低,特别是寒冷的北方冬季开炉时更突出;燃料油带水或油温太低黏度大,雾化不好;油和蒸汽的配比不当,给汽过大易来,给汽太小又容易喷油冒大火。
所以,开炉点火时,一般是先点瓦斯嘴(指有燃料气的地方),等炉膛温度上升时,再来瓦斯火点油火。
④点火应注意安全无论点什么火嘴,点火操作时人不能面对火嘴,要侧着身子,以免回火伤人。
⑤点火顺序立式炉和无焰炉的火嘴数量都很多,而且根据加热炉的升温速度也不能一下全点着。
所以,在逐渐升温增加火嘴的时候,要两边一样多,先点两头后中间,对称交错点火为宜,目的是为了保证从开工点火起,不要因炉管或部件受热不均而影响使用寿命。
4.1.2.3正常操作及调节
加热炉进料流量和出口温度是延迟焦化的重要工艺指标,它直接影响到整个装置的产品质量、产率、处理能力和开工周期。
所以,要想实现装置长周期安全平稳生产,必须保证加热炉进料量和出口温度的平稳。
加热炉的进料量和进料温度是靠进料油泵出口压力和分馏塔底的温度平稳来保证的;靠操作人员的高度责任心,严格的岗位责任制和过硬的基本功来实现的。
为此必须做到燃料正常燃烧,加强检查和及时细心调节。
(1)燃料的正常燃烧
燃料燃烧的好和坏,给人的直观感觉是火焰。
火焰是燃料正常燃烧的标志火焰好是正常燃烧的标志。
但是,正常燃烧并不完全等于火焰好,要想达到火焰好,在正常燃烧的基础上还要做很大努力才能实现。
(2)火焰好坏的判断方法
火焰好坏的判断是:
燃烧完全,炉膛明亮清晰,炉墙炉管表面没有显著明暗阴影;瓦斯火陷呈蓝白色,油火焰呈淡黄色;火焰高度一致,不干扰、不偏斜,不打圈、不扑炉管,做到多嘴、短焰、齐火苗;烟囱冒烟无色或淡蓝色。
(3)正常燃烧的影响因素
①燃料性质的变化。
随着燃料油馏分的轻重或燃料气的贫富组成的变化,都会影响燃料燃烧发热量,从而影响炉温的波动;
②燃料压力变化。
燃料压力的变化说明进炉的燃料量发生变化,对同一燃料热值而言,发热量就要变化,也引起炉温波动。
③燃料中的杂质及是否带水。
如果燃料油带水会使火焰冒火星、喘息,甚至熄火,同时因水发生汽化而吸热,火焰温度降低,燃烧速度下降;如果燃料气带油,由于油的汽化燃烧也造成火焰不好,同时在相同的喷嘴孔径情况下,油进入炉膛容易使炉内满膛大火,严惩时将影响安全生产。
④燃料和空气的混合。
立式炉无论烧油还是烧瓦斯,均需适量的雾化蒸汽,使瓦斯与空气混合良好。
配汽量过小雾化不好,火焰尖端发软发飘无力,呈暗红或黄色,燃烧不完全;配汽量过大,火焰发白,短小有力,容易灭火,浪费燃料和蒸汽。
无焰炉烧的是高压瓦斯,故不用配汽,靠瓦斯的高速喷射携带空气达到混合的目的。
⑤入炉空气量的变化。
燃料燃烧的三要素之一是氧气充足,氧气用量平时是以入炉空气量来衡量的。
入炉空气量太小,燃烧不完全,炉膛发暗,火焰发红;入炉空气量过大,炉膛虽呈淡黄色,但火焰上烟气乱窜,炉管氧化脱皮厉害。
入炉空气量是通过几门和烟道貌岸然挡板开度大小来调节的。
除此之外,还受外界气温风力大小变化的影响,炉漏风更为明显。
4.1.2.4调节方法与主要工艺指标的分析
(1)加热炉进料量和炉子出口温度的关系
在正常操作的情况下,应当保持进料量平衡。
进料量大小与处理量高低有关,大幅度的提量或降量,除特殊情况外是不允许的。
如果想控制循环比不变,分馏塔底温度由于焦炭塔的预热和切换等操作可能发生变化,这时若要保证炉出口温度平衡,除了搞好正常燃烧外,必须适当暂时的降一点进料量。
否则就会出现炉出口温度烧不上去,火焰加大,炉膛温度升高等不良倾向。
如果想保持进料量和炉出口温度不变,只有用改变循环比的办法,保证分馏塔底温度不变来达到。
(2)炉膛温度和炉出口温度的关系
炉膛温度一般指烟气离开辐射室的温度,也叫火墙温度。
燃料燃烧产生的热量,在炉膛内是通过传导、辐射和对流三种方式传给炉管内油品,其中辐射热量占90﹪左右,传热量的大小与炉膛温度和管壁温度有关。
辐射室传热公式为
Q=19.623ψA辐[(T/100)4-(Ø/100)4]+4.187hA辐(T-Ø)kJ/h
式中Q——辐射室总传热量,kJ/h;
ψ——系数,与炉型、火焰情况、炉管排列等有关;
A辐——辐射室炉管外表面,㎡;
T——炉膛膛浓度,K;
Ø——炉管温度,K;
h——对流给热系数,kJ/(㎡·h·℃)。
从公式可以看出,在辐射室内辐射传热量大小与炉膛温度四次方和炉管壁温度四次方之差成正比。
简单地讲炉膛温度高,辐射室的辐射和对流传热量就大。
所以,炉膛温度变化曲线与炉出口温度变化曲线一致。
炉膛温度高低,在进料温度和流量不变的情况下,主要由燃料量和火焰调节好坏决定的。
有时因调节火焰不当,致使炉膛温度某一点升高或下降,就是这个道理。
从数学公式角度看,炉膛温度越高越好。
但是,不能无限提高炉膛温度。
炉膛温度过高,辐射炉管表面热强度(每平方米炉管表面积每小时所传递的热量)过大,引起管壁温度升高,炉管易于结焦,同时进入对流室烟气的温度也过高,对流炉管也容易变形烧坏。
另外由于炉管结焦造成传热系性能(传热系数)大大下降,要达到相同加热炉出口温度有必要使炉膛温度更高,这样形成一个恶性循环,对焦化炉长周期运转十分不利。
所以,在延迟焦化装置正常生产中如果炉膛温度上升的快,表明炉管结焦严重,应该引起注意。
当然炉管结焦不完全是因为炉膛温度高造成的,还与局部过热、炉管排列、油品流向、原料性质等多种因素有关。
加热炉炉膛温度不但是生产的主要指标,也是设计中的重要工艺参数,通常设计人员是根据加热炉热负荷和炉管材质而计算规定的。
所以,操作过程中,不能长期超过规定指标。
一般焦化立式炉炉膛温度800~850℃左右,无焰炉在750~780℃左右。
(3)注水量与炉膛温度的关系
焦化加热炉一般采用注水的方法来提高油品在炉管内的流速,缩短停留时间,减少结焦。
注水有增加流速、缩短停留时间、减少结焦的好处;但也有增加加热炉负荷、压力降等缺点。
注水量的大小与焦化原料性质、处理量、设备负荷有关。
所以注水量大小要选择合适,大体为处理量的2﹪左右。
炉膛温度在其他条件不变时,随着注水量的增加而要提高。
因为1kg35℃的水加热到500℃,需要热量为3347kJ/kg。
如果注水量为每小时1500kg,那么需要热量为5020MJ/h,约占有效热负荷的10﹪。
由于不适当提高注水量引起炉膛温度升高也是炉管结焦的一个因素。
炉管结焦后,管径变小,油品流速增加,压力降也要增加。
在保证进料量不变情况下,注水压力也必须上升。
为此,从注水压力上升速度也可以判断炉管结焦程度。
在设计规定的加热炉辐射炉管入口压力范围内时,还可以继续生产,当超过压力(或安全阀定压)时,就得停工,或者降辐射进料量,或者降注水量。
(4)风门开度与全炉热效率的关系
燃料燃烧是燃料中的碳和氢的氧化过程,产生二氧化碳、水,并放出热量。
1kg的燃料完全燃烧需用的理论空气量视燃料的组成不同、种类不同,其计算公式也不同。
理论计算空气量不能保证完全燃烧,实际上入炉空气量总比理论计算值大一些。
二者之比叫做空气过剩系数,常以a表示。
a=L实际/L理论
式中L实际——实际入炉空气量(质量),kg空气/kg燃料;
L理论——理论计算的空气量(质量),kg空气/kg燃料。
从公式中看到过剩空气系数a有大于1,等于1或者小于1三种情况。
在正常的情况下过剩空气系数总是大于1的,但过剩空气系数太大有如下的缺点:
①进炉空气太多,炉膛、火焰温度下降,炉出口温度烧不上去。
②烟气量增加,带走热量也增多,降低了全炉热效率,又浪费了燃料。
③炉管容易氧化脱皮、管子损失加快。
空气是由火嘴的一、二次风门进入的,进入量的多少,是由炉膛负压(或烟道挡板开度)及风门开度的大小决定的。
由此可见,风门和烟道挡板开度与加热炉热效率有关,操作中不能随便调节风门,特别是烟道挡板更不能乱调乱动,应该看准再调。
4.1.3加热炉炉管的烧焦
4.1.3.1炉管结焦的判断
炉管结焦的判断方法是凭实际操作经验和查仪表的记录指示。
具体情况如下:
①炉管的局部结焦可以从炉管表面颜色不一样来判断。
结焦的地方,由于焦炭、盐垢的传热系数小,而使炉管表面温度高,颜色发暗红色,或者有一些灰暗的斑痕,而其他地方炉管则呈黑色。
发现这种局部结焦时,就要注意多观察多检查,把局部结焦的炉管左右火嘴的火焰适当调小,防止继续发展。
②多数炉管结焦在炉辐射进料量和其他指标不变时,炉膛各点温度逐渐升高,使炉管颜色发暗红、阻力降增加,注水压力上升;或者炉膛温度升高,炉辐射出口温度步去,焦炭塔顶温度下降、焦炭质量不合格。
如果温度反应不灵,证明温度控制热偶保护套管结焦严重。
出现这种大量严重结焦时,就应该停工烧焦。
若还要坚持生产,那就应该降量,增加循环比,认真参考其他各点的温度(25根炉管温度,焦炭塔底的温度)、焦炭质量来控制加热炉出口温度。
4.1.3.2空气——蒸汽烧焦的原理
炉管内的结焦(焦炭和盐垢),在高温下和空气接触燃烧,利用蒸汽控制烧焦的速度并带走多余的热量,防止局部过热、保护炉管。
同时,由于空气、蒸汽和燃烧的气体以较高速度在炉管内流动,将崩裂和粉碎的焦粉和盐垢,一同带出炉管。
空气——蒸汽法清焦的原理流程如图4-1-11所示。
4.1.3.3烧焦
①烧焦的准备工作停加热炉,350℃后熄火,用1Mpa蒸汽吹扫炉管内存油,放掉压力和冷凝水拆卸炉管堵头(预测结焦较厚的几根炉管堵头),检查焦厚,做好数据记载和分析,为清焦和烧焦作参考。
装上仪表,给上堵头,改好烧焦流程,准备好燃料、工业风、蒸汽。
炉管正工烧焦前,有时采用热水泡焦冲洗。
用热水先冲洗,然后再烧焦有很多优点,既回忆了烧焦速度,又处长了炉管的寿命,就根据具体情况适当选择水冲洗的条件。
②点火升温准备工作完成后,点火以50℃/h升温,到炉膛温度时,再以300℃升温到500℃左右。
③在炉膛达到550℃以前可以大量吹汽,把脱落崩裂的焦粒带走,防止在通风的时候堵管。
④在炉膛达到550℃时,减少吹汽量,少量开始通风。
每半小时左右关掉风阀,大量给汽吹扫一次。
⑤经反复多次通风吹扫,慢速烧焦、焦粉减少,炉管温度可升高到660℃,适当开汽通风,加大风量。
从储焦场见到盐垢焦块直径不大于7㎜以上时,说明风量较大,烧焦速度太快,容易堵管,应减少风量。
⑥经过中速烧焦,炉管内的结焦大部分烧完,但还可能有些硬焦不好烧。
这时应当再提炉膛温度到630℃左右(最高不大于650℃),加大风量,减少蒸汽,进行快速烧焦,直到烧完为止。
空气——蒸汽清焦炉温曲线如图4-1-12所示。
4.1.3.4烧焦和烧焦已净的判断方法
(1)烧焦正常的判断
通风后,炉管温度由低到高,自通风方向炉管颜色稍微变红,并逐步前移,这说明炉管内焦炭已经烧着。
如果呈暗红色或桃红色,说明通风量太大,应当减少风量加大吹汽量。
烧焦速度以每次烧1~2根为宜,不要太快,烧焦速度用风量控制。
所以烧焦过程中要严格控制风量和蒸汽量配比及通风时间,通常司炉工都用风阀、汽阀的开度大小来灵活掌握,做到心中有数。
从储焦场看到吹出焦块粉直径小于7㎜,冒出的烟汽发黑并夹带大量的粉末。
(2)烧焦的异常现象和判断
司炉工对烧焦工作应特别细心。
这个工作看起来很简单,如果没有一定实际经验,碰到以下问题就很难解决。
①通风后焦烧不着判断方法是通风时间长炉管不变色,出口无焦粉、温度不上升。
原因可能是:
通风量小、通汽量大;炉膛温度低,焦没有达到燃烧温度;炉管结焦坚硬,含盐多;风压不足,风量不够。
②炉管内焦烧一半就灭了判断方法是炉管暗红一半再不前移了。
这种现象容易在