实训模块四.docx
《实训模块四.docx》由会员分享,可在线阅读,更多相关《实训模块四.docx(10页珍藏版)》请在冰点文库上搜索。
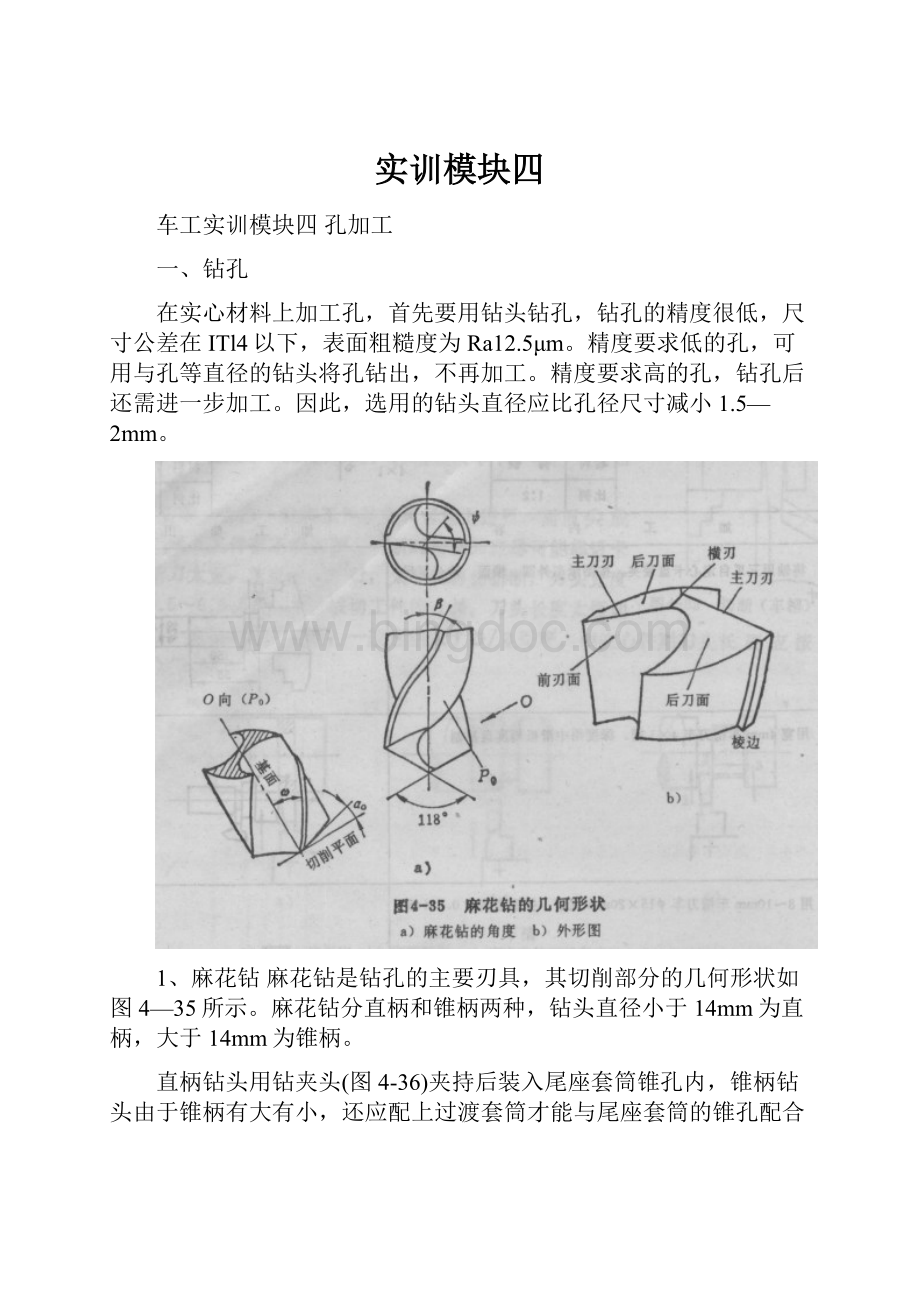
实训模块四
车工实训模块四孔加工
一、钻孔
在实心材料上加工孔,首先要用钻头钻孔,钻孔的精度很低,尺寸公差在ITl4以下,表面粗糙度为Ra12.5μm。
精度要求低的孔,可用与孔等直径的钻头将孔钻出,不再加工。
精度要求高的孔,钻孔后还需进一步加工。
因此,选用的钻头直径应比孔径尺寸减小1.5—2mm。
1、麻花钻麻花钻是钻孔的主要刃具,其切削部分的几何形状如图4—35所示。
麻花钻分直柄和锥柄两种,钻头直径小于14mm为直柄,大于14mm为锥柄。
直柄钻头用钻夹头(图4-36)夹持后装入尾座套筒锥孔内,锥柄钻头由于锥柄有大有小,还应配上过渡套筒才能与尾座套筒的锥孔配合。
如图4-37所示。
2、尾座的工作位置
1)钻孔时尾座中心应对准工件旋转中心,尾座偏位会造成钻孔尺寸扩大。
2)钻孔前尾座套筒伸出长度尽可能短。
3、钻孔的切削速度麻花钻切削速度口,一般为20~25m/min。
计算主轴速度时应根据钻头直径大小来定。
n=1000v/πD
式中n——主轴转速,单位为r/min;
D——钻头直径。
4、钻孔的方法钻孔前工件的端面要车平,或中心处车成凹坑,这样有利于钻头定中心。
开始钻削时钻头很容易产生摆动,如不及时纠正,将会使钻出的孔与外圆不同轴,甚至严重偏位。
减少钻头摆动的方法是在刀架上夹一挡铁,当钻头尖顶处与端面接触产生摆动时,就用挡铁轻轻挡住钻头头部,如图4—38所示。
注意不能挡在钻头中间部,也不可用力太大,挡在后部不起作用,用力太大又会使钻头向一边偏斜同样会造成孔径扩大。
当钻头尖顶部分切入约3/4左右,挡铁应退出。
钻头直径小于5mm时不宜用挡铁。
防止钻头摆动的方法,即在钻孔前在端面上钻一中心孔,也能起到定中心的作用。
钻孔时双手摇动尾座手轮,如图4—39所示。
进给量约0.1~0.3mm/r,钻头直径小容易折断,进给速度应适当慢些。
钻孔时应加切削液,钻孔深度深时排屑有困难,应经常退出清除切屑和冷却钻头。
二、扩孔
在实心材料上钻孔,Φ25mm以下的孔一次钻出,Φ25mm以上的孔钻削时较费力,一般钻孔后再将孔扩大,例如钻削Φ40mm孔,直接钻较困难,可以先钻Φ20~Φ25mm的孔,然后再用Φ40mm的钻头将孔扩大。
扩孔时比较省力,但进给速度也不能过快,否则易造成钻头在尾座套简内打滑。
三、车孔
车孔的方法可以加工通孔、阶台孔和盲孔,见图4—40所示。
车孔尺寸公差等级能达到IT8一IT9,表面粗糙度为Ra6.3~1.6μm。
1、内孔车刀内孔车刀分为通孔车刀与不通孔车刀两种,如图4—41所示。
其切削部分的几何形状与外圆车刀基本相似,不同的是后角较大,一般磨成双后角或圆弧状,以免与孔壁相碰。
内孔车刀的刀杆应按径大小选择,安装时,应对准中心,精加工时可略高一些,刀杆伸出长度略长于被加工孔,刀杆应与内孔轴心线平行,一般安装后应在工件内孔前后移动一次,观察有无碰擦。
2、车通孔通孔的车削方法与车外圆相似,车削前检查毛坯孔尺寸,根据加工余量确定车削次数和吃刀量ap。
通过试切削的方法准确地定吃刀量,以保证孔径的尺寸公差。
(1)孔试切削的步骤孔试切削的步骤如图4—42所示。
1)开动机床将车刀刀尖向孔壁靠拢,当刀尖与孔壁相擦时,横向不动,纵向退出。
2)将中滑板刻度进到所需要的吃刀量位置。
3)试车孔,试车长度约2mm左右。
4)测量试切部分的孔径尺寸。
5)根据试切尺寸重新调整吃刀量或不调整。
试切的过程要反复进行,直至试切尺寸符合要求时,才可纵向进给。
车通孔的内孔车刀要长于工件长度,可在车刀上划线作为退刀标记,也可听声音辨别车刀是否已不切削。
(2)车孔切削用量的选择车孔切削用量选择基本与车外圆一样,粗车在机床及刀具的刚性允许条件下,吃刀量。
,尽可能选大些,精车为得到较小的表面粗糙度,ap适当取小些,一般0.1—0.3mm。
(3)孔的测量方法
1)常用的测量方法是用内卡钳在钢直尺或千分尺上量取尺寸后,再用内卡钳测量孔径尺寸,这种方法比较简便,适用性较广,但测量的精确度完全由操作者的测量技巧所决定,如测量技巧熟练,用内卡钳测量孔径误差可小于0.03mm。
2)操作的方法是将千分尺上的读数调整到孔径尺寸的最小极限,然后锁紧以防尺寸变动。
千分尺用左手握住,右手握内卡钳,如图4-43所示。
内卡钳应调整到与千分尺测量面轻微相擦,不能过紧或过松,否则都会影响测量的准确程度。
3)内卡钳在孔内测量时,应作前后和左右的摆动,摆动量一般为2—3mm,测量姿势如图4-44所示。
(4)车孔应注意事项
1)工件不可夹得过紧,以防夹变形。
2)工件外圆应用划针找正,以保持孔与外圆同轴。
3)车孔时一般应同时车出端面,以保持孔与端面习
4)孔口应去除毛刺或锐边倒钝。
(5)车通孔操作实例。
见表4—3。
表4-3车通孔操作实
序号
加工简图
加工内容
1
一、按图示装夹工件
用Φ18mm钻头钻通孔
用90°车刀车端面,车出即可
第一次车孔径D为Φ20mm
钻头直径=[20一(1.5~2)]mm=18~18.5mm
2
二、车内孔,按练习顺序反复练习
3
三、孔口用内孔车刀倒角
3、车阶台孔
(1)阶台孔车刀的选择和安装车阶台孔用不通孔车刀,刀杆粗细应根据孔径和阶台面的大小,要保证车内阶台面时刀杆不与孔壁相碰,主偏角Ar>90°,如图4—45所示。
(2)阶台孔的车削方法一般先车小孔,再车大孔,如阶台孔大小相差悬殊,可以大小孔都粗车,然后精车。
1)内阶台面的车削方法粗车内孔的末次进刀接近终止位置时,车刀应作横向进给,将内阶台面基本车平整。
精车孔,纵向进给至终止位置时,刀尖已切入内端面,见图4—46a,此时,立即改为横向进给,车内阶台面,见图4—46b。
2)阶台孔深度的控制方法常用的方法是利用床鞍作粗加工定位,精加工控制孔深的尺寸公差可利用小滑板刻度作微量调整。
操作的方法是摇动小滑板,使车刀刀尖逐渐靠近工件端面,当刀尖与工件端面相接触时,车刀横向退出,将床鞍刻度调整到零位,作为起始位置。
刻度的终止位置即所需要的孔深尺寸。
如孔深30mm,床鞍刻度的终止位置即第30格。
(刻度每格为lmm)由于刻度有一定误差,一般在车削时应留有余量,约比实际尺寸短0.5~lmm,然后通过测量,按实际尺寸,利用小滑板刻度作微量修正。
3)阶台孔深度的测量方法阶台孔深度要求不高的可用钢直尺测量,孔径尺寸较小或精度较高的可用游标卡尺测量,如图4-47所示。
表4-4车台阶孔操作实例
序号
加工内容
加工简图
1
工件用三爪自定心卡盘装夹,装夹长度的工件总长的1/3左右,用划针找正后夹紧.
车Φ200+0.10mm孔至尺寸.
偏刀由里向外车出端面.
2
粗车Φ300+0.05mm阶台孔至庐Φ29.5,孔深15mm车至14.5m
3
精车Φ300+0.05mm孔至尺寸,同时车出内阶台面,控制孔深15mm孔口去除锐边