特种加工及机械制造工艺与产品质量期末复习.docx
《特种加工及机械制造工艺与产品质量期末复习.docx》由会员分享,可在线阅读,更多相关《特种加工及机械制造工艺与产品质量期末复习.docx(24页珍藏版)》请在冰点文库上搜索。
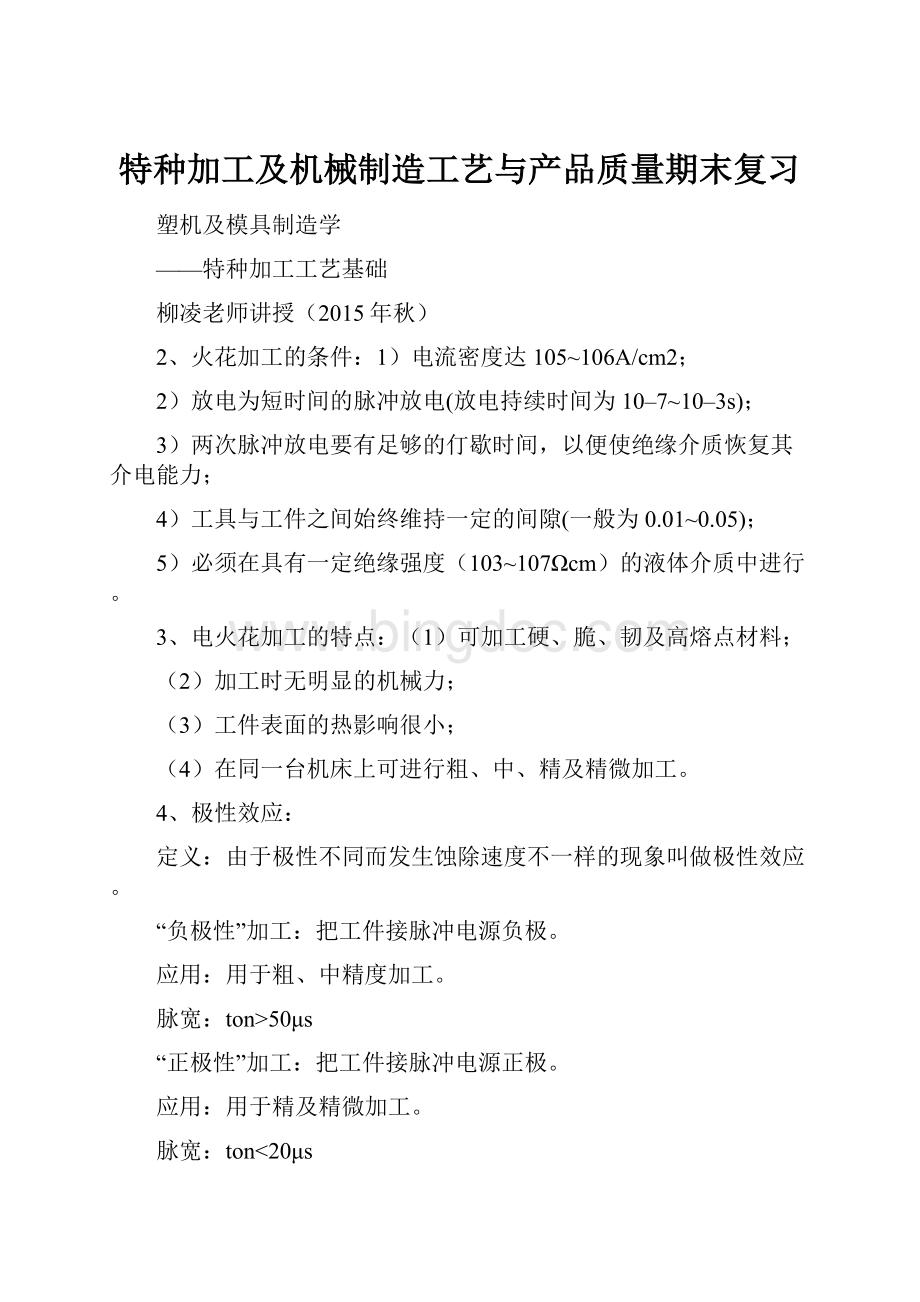
特种加工及机械制造工艺与产品质量期末复习
塑机及模具制造学
——特种加工工艺基础
柳凌老师讲授(2015年秋)
2、火花加工的条件:
1)电流密度达105~106A/cm2;
2)放电为短时间的脉冲放电(放电持续时间为10–7~10–3s);
3)两次脉冲放电要有足够的仃歇时间,以便使绝缘介质恢复其介电能力;
4)工具与工件之间始终维持一定的间隙(一般为0.01~0.05);
5)必须在具有一定绝缘强度(103~107Ωcm)的液体介质中进行。
3、电火花加工的特点:
(1)可加工硬、脆、韧及高熔点材料;
(2)加工时无明显的机械力;
(3)工件表面的热影响很小;
(4)在同一台机床上可进行粗、中、精及精微加工。
4、极性效应:
定义:
由于极性不同而发生蚀除速度不一样的现象叫做极性效应。
“负极性”加工:
把工件接脉冲电源负极。
应用:
用于粗、中精度加工。
脉宽:
ton>50μs
“正极性”加工:
把工件接脉冲电源正极。
应用:
用于精及精微加工。
脉宽:
ton<20μs
6、工作液的要求与作用
工作液的一般要求:
(1)绝缘
(2)燃点高(3)无毒(4)稳定(5)价廉
作用:
(1)介电作用;
(2)压缩放电通道,提高火花放电能量密度;
(3)帮助电蚀产物的抛出和排除;
(4)冷却工具与工件。
7、排屑措施:
(1)冲油;
(2)工具电极定期自动抬起;
(3)增大脉冲停歇时间;
(4)降低加工平均电流。
二、影响加工精度的主要因素
强化极性效应措施:
1、正确选择加工极性:
(1)采用窄脉冲精加工时应选用正极性加工;
(2)采用较长脉冲进行粗、中加工时则应选用负极性加工。
2、选用合适的材料作工具电极
工具电极材料应选用:
(1)稳定性好;
(2)损耗小;(3)可加工性好。
电极材料的一般要求:
(1)价廉、易获得;
(2)易成形;
(3)成形变形小,具有一定强度;(4)电加工性能好(加工稳定性高、电极损耗小)
3、建立炭黑保护层
形成黑炭保护层的条件:
(1)在煤油中采用负极性加工;
(2)尽量增大脉冲宽度,降低脉冲电流幅值;
(3)在保证加工稳定而不产生异常放电的前提下,尽量缩短脉冲停歇时间。
3.2型腔模电火花加工
一、型腔模电火花加工的工艺特点与工艺方法:
1、工艺特点:
(1)要求电极损耗小,以保证型腔模的成形精度;
(2)成形过程蚀除量大,要求加工速度快;
(3)粗加工后的侧面修光较难,必须更换精加工电极或利用平动头进行侧面修光。
2、工艺方法选择
(1)单电极平动加工法。
加工步骤:
①先用高效低损耗电规准进行粗加工,使其基本成形;
②利用平动头使工具电极作平面平行运动,按粗、中、精的顺序逐级改变电规准,同时依次加大平动头的平动量,以补偿前后两次加工规准之间的放电间隙差及表面修光量,实现型腔侧面逐级修光,完成整个型腔模的加工。
最大优点:
只需一个成型电极,一次装夹定位。
缺点:
棱角加工精度难于保证。
二、电极设计与制造
1、电极材料的选择:
电极材料的要求:
①具有良好的电火花加工性能;
②易于加工制造成型;
③来源丰富,价格便宜。
目前应用最多的是石墨和紫铜
紫铜特点:
(1)组织致密;
(2)适用于形状复杂、轮廓清晰、精度要求较高的塑料模。
缺点:
(1)机械加工性差,难以成形磨削;
(2)由于密度大、价格贵,不宜作大、中型电极。
石墨电极特点:
(1)容易成型;
(2)密度小,适宜作大、中型电极。
缺点:
(1)机械强度差,电极制造精度难以保证;
(2)精加工时损耗较大,也容易引起电弧之类的非正常放电,使工件烧伤。
此外,铜钨合金、银钨合金也是较理想的电极材料,但价格贵,只用于特殊型腔加工。
2、电极设计
(1)结构形式的确定。
①整体式电极:
适用于尺寸大小和复杂程度都一般的型腔加工。
分为两种形式:
I、有固定板:
用于尺寸较大,形状较复杂、采用多孔冲油或排气的情况;
II、无固定板:
用于型腔尺寸小,形状简单,只用单孔冲油或排气的情况;
②组合式电极:
适用于一模多腔的情况。
特点:
I:
可以大大提高加工速度;
II.简化各型腔之间的定位工序,提高定位精度。
③镶拼式电极:
适用于型腔尺寸较大,或型腔形状复杂,分块才容易制造的电极。
(2)电极尺寸的确定
1)电极水平尺寸(即电极与主轴进给方向垂直的尺寸):
a=A±kb
式中:
a——电极水平方向的名义尺寸;
A——图样上型腔的名义尺寸;
K——与型腔尺寸注法有关的系数;
b——电极单边缩放量。
b)K值的选择原则:
①当图中型腔尺寸完全标注在边界上(即相当于直径方向尺寸)时,k取2;
②一端以中心或非边界线的基准(即相当于半径方向尺寸)时,k取1;
③对于图样上型腔中心线间的位置尺寸以及角度值,电极上相对应的尺寸不增不减,K取0。
④对于圆弧半径,亦按上述原则确定。
2)电极垂直方向尺寸(即电极与主轴进给方向平行的剖面尺寸):
l=L±k´Δ´
式中:
l——电极垂直方向的有效加工尺寸;
L——型腔深度方向的尺寸;
Δ´——加工时的放电间隙与电极损耗要求电极端面的修正量;
k′——与尺寸注法有关的系数,如线性尺寸的K=1。
其中电极端面修正量为:
Δ´=γ–δ精
式中:
γ——电极端面损耗的总量;
δ精——最后精加工时的放电间隙。
注:
(a)上述电极尺寸的确定,均考虑了型腔的抛光余量。
(b)电极各尺寸的公差范围,取型腔相应尺寸允许公差的1/2∽1/3。
3)电极总高度:
型腔加工的电极总高度H必须根据工艺需要,电极使用次数以及装夹要求等因素确定,即:
H=L+L1+L2
式中:
H——除装夹部分之外的电极高度;
L——电极加工一个型腔的有效高度;
L1——当加工的型腔位于另一个型腔中时需增加的高度;
L2——考虑加工结束时,电极夹具和固定板不与模块或压板发生碰撞而应增加的高度。
侧面修光方法的改进
1、用平动头修光侧面存在的问题:
(1)由于平动头是使电极上各点以恒定速度做圆周运动,电极平动靠向短边时加工量较小,而电极平动靠向长边时加工量较大,由此易产生加工量的不均匀,因此当短边已经修光时,长边尚未修光。
(2)由于电极装夹的刚性不足,因此电极的运动轨迹实际上并不成圆形,严重时同样会造成某些侧面修不光。
(3)用液压主轴头时,电极平动同时伴随着上下运动,因此加工侧面容易产生皱纹,某些部位还会引起加工不到的情况。
(4)现有平动头,在调节偏心量时,凭眼睛观察,凭经验进行手动调节。
这样的调节效率低,调节量很难适当。
还有些平动头需要在停车后进行调节,操作更为麻烦。
2、改进措施:
(1)增加运动刚性;
(2)采用非等速平动运动;
(3)振据间隙状态自动调节偏心量;
(4)实现电极低损耗、高速的型腔电火花加工(即用一挡精规准实现型腔加工)
3.3电火花线切割加工
特点:
1、无需制造成形电极;
2、能加工高硬、高脆性材料;
3、电极丝损耗极小,加工精度高;
4、生产效率高,模具使用寿命长。
(一)线切割机床加工工艺的一些般规律
1、提高生产率的主要途径:
(1)增大脉冲电压幅值;
(2)增加脉冲宽度;
(3)减少脉冲间隔时间;
(4)适当增大脉冲电源的功率;
2、影响加工表面粗糙度的几个因素:
(1)导丝轮及其轴承磨损使精度变差,由此产生高低条纹,严重影响了加工表面粗糙度;
(2)电极丝移动不平稳,有振动;
(3)电极丝绕提太松,张力不够;
(4)脉冲电源电参数选择不当,拉弧现象太多;
(5)铜丝损耗过大,变细了的钢丝在导轮内窜动;
(6)进给速度调节不当,加工不稳定。
3、保证加工精度的措施:
(1)保持恒定的放电间隙,为此应力求脉冲电源电压波动愈小愈好;
(2)电极丝和工作台的垂直度要好;
(3)提高机床的制造精度;
(4)减小电极丝的振动。
4、工作液
要求:
(1)工作液应有一定的介电能力;
(2)有较好的冷却性能;
(3)有较好的洗涤性能;
(4)有较好的去游离能力和灭弧能力;
(5)有好的防锈性能;
(6)无毒、无害。
5、电极丝
1)电极丝材料选择原则:
(1)有良好的耐蚀性,有利于提高加工精度;
(2)有良好的导电性,有利于提高回路效率;
(3)有效高的熔点,有利于大电流加工;
(4)有效高的抗拉强度和良好的直线性,有利于提高使用寿命。
2)常用电极丝材料:
黄钢丝、钨丝、钢丝、钨铜丝。
3.4模具的仿形加工
(二)仿形触头
1、要求:
(1)触头的倾斜角应小于靠模工作面上的最小斜角;
(2)仿形触头头部半径R应小于靠模工作面上的最小半径;
(3)仿形触头的形状还应与铣刀形状相适应。
2、仿形触头直径D的确定:
D=d+2(a+e)
式中:
d——铣刀直径(mm)
a——型腔加工后需留的钳工修正量;
e——由于触头偏移的修正量。
e值的大小必须在机床上经过实测才能确定,并在修正后才进行仿形加工。
精仿时,一般取e=0.06~0.1mm
第四章机械制造工艺与产品质量
4.1概述
一、机械加工工艺系统
1、系统概念:
系统是由几个相互作用和相互依赖的要素组成,并且是具有特定功能的整体。
2、生产系统:
生产系统分为三个阶段:
①决策和控制;②设计和发展;③制造
机械加工工艺系统包括:
机床、夹具、刀具、工件。
1、生产纲领
产品生产纲领Q(台/年)
零件生产纲N=Q×n(1+α%)(1+β%)
式中:
N——零件的年生产纲领(件/年);
Q——产品的年生产纲领(台/年);
n——每台产品中所含零件的数量(件/台);
α%——备品率;
β%——废品率,与企业的生产条件有关(一般为0.5~1%)
重要概念:
1)工序:
一个工人或一组工人在一定工作地点对一个工件或几个工件连续工作的顺序。
导套加工工艺(材料:
20)
工序号
工序名称
工序内容
1
下料
按尺寸52mm×115mm切断
2
车外圆及内孔
车端面保证长度113mm,钻32mm孔至30mm,车45mm外圆至45.4mm,倒角车3×1退刀槽至尺寸
镗32mm孔至31.6mm,镗油槽,镗33mm孔至尺寸,倒角
3
车外缘倒角
车48mm的外圆至尺寸,车端面保证长度110mm,倒内外圆角
4
检验
5
热处理
按热处理工艺进行,保证渗碳层深度0.8~1.2mm,硬度58~62HRC
6
磨内外圆
磨45mm外圆达图样要求,磨32mm内孔,留研磨量0.01mm
7
研磨内孔
研磨32mm孔达图样要求,研磨圆弧
8
检验
2)工位:
采用转位(或移位)夹具、回转工作台,或在多轴机床上加工时,工件在机就上安装后,要经过若干个位置依次进行加工,工件在机床上所占据的每一个位置上所完成的那部分工艺过程就称为工位。
3)工步:
是在加工表面不变、切削工具不变,切削用量不变的条件下所连续完成的那部分工艺工程。
4)走刀:
是切削工具在加工表面上切削一次所完成的那部分工艺过程。
5)安装:
是指工件在机床上(或在夹具中)定位后加以夹紧的过程称为安装。
4、零件的机械加工工艺卡片
内容:
①工序简图;
②详细说明该工序的每个工步的加工内容、工艺参数;
③操作要求;
④设备和工艺装备。
工序简图的内容:
定位表面、夹紧表面、工序尺寸、工序公差、
表面间的形位公差、技术要求等。
工艺规程主要作用:
1)指导生产和主要技术文件;
2)生产准备工作和生产管理工作的主要依据;
3)新建工厂的原始资料;
4)有利于积累、交流和推广行之有效的生产经验。
4.2工件的装夹
一、基准及其分类
1、设计基准——是设计图样上采用的基准,即标注设计尺寸的起点。
2、工艺基准——是在工艺过程中所采用的基准。
工艺基准按用途分为:
①工艺基准;
②定位基准;
③测量基准;
④装配基准。
1)工序基准——是在工序图上用以确定该工序所加工表面加工后的尺寸、形状、位置的基准。
它是某一工序所需达以的加工尺寸(即工序尺寸)的起点。
2)定位基准——工件在装夹过程中用作定位的基准。
(用定位表面来体现出来)
3)测量基准——测量时所采用的基准
4)装配基准——是装配时用来确定零件或部件在产品中相对位置所采用的基准
分析基准注意事项:
(1)作为基准的点、线、面在工件上不一定具体存在;
(2)基准可以是点、线、面。
①粗基准——在加工的最初工序中,只能用毛坯上未经加工的表面作为基准,这种定位基准叫粗基准。
②精基准——在以后的工序中,则使用已加工的表面作定位基准,这种定位基准称为精基准。
“六点定位原理”——采用六个按一定规则布置的支承点,限制工件的六个自由度,使工件在机床或夹具中占有正确的位置,即称为“六点定位原理”。
四种定位:
①完全定位——将工件六个自由度完全限制的定位;
②不完全定位——没有完全限制工件自由度的定位;
③欠定位——应该限制的自由度没有被限制的定位;
④过定位——多个支承点重复限制同一个自由度的情况。
消除过定位途径:
1)提高定位基面之间以及定位元件工作表面之间的位置精度;
2)采用自位支承的结构,消除定位元件限制某个或两个坐标轴转动方向自由度;
3)定位元件沿某一坐标轴移动来消除其限制沿该坐标轴移动方向的自由度;
4)改变定位元件结构。
四、定位误差分析计算(重点)
定位误差——同批工件在夹县中定位时,工序基准位置在工序尺寸方向上的最大变动量,称为定位误差,以△dw表示。
引起定位误差的原因:
1)由基准不重合误差引起的定位误差
定位尺寸——定位基准到工序基准间的尺寸。
基准不重合误差△bc—等于定位基准到工序基准间的尺寸(简称定位尺寸)的公差。
设定位尺寸为L,则△bc=2△L=TL
式中:
△L——尺寸L的偏差;
TL——尺寸L的公差。
注意:
由△bc引起的定位误差△dw,应取其在工序尺寸方向上的分量(投影),
即△dw=△bccosβ
式中:
β——定位尺寸与工序尺寸方向间的夹角。
2)由基准位置误差引起的定位误差。
基准位置误差△jw——定位基准在夹具中的位置的最大变动量称为基准位置误差。
同样,△jw在加工工序尺寸方向上的分量(投影),就是△jw引起的定位误差,
即:
△dw=△jwcosγ
式中:
γ——基准位移方向与工序尺寸方向间的夹角。
△jw的大小:
①当工件直径最大为d时,外园中心在0处;
②当直径最小为时,工件要下移,直至与V形块接触为止。
此时园周上的A点下移到A1处,相应地外园中心0移到01处,因此定位基准位置的变动量,即为定位基准位置误差△jw。
由图未几何关系得到
Td
△jw=OO1=AA1=————(要求背)
2sinα/2
讨论:
①当Td一定时,随α增加△jw减少;
②当α=180º时,△jw=Td/2,此时为平面定位;
③当α一定时,随Td增加△jw增加。
2、定位误差的分析计算:
△dw=△bccosβ±△jwcosγ
当△bc和△jw的方向相同时取“+”号,相反时取“-”号。
4.3尺寸链原理(重点)
要求:
①掌握尺寸链定义;
②画尺寸链;
③判断封闭环,增减环;
④解决尺寸链的方法。
一、概述
1、尺寸链的定义和组成:
尺寸链——在零件加工或机器装配过程中,由相互关联的尺寸彼此首尾相接形成的封闭尺寸组,称为尺寸链。
工艺尺寸链——在零件加工过程中,由同一零件有关工序尺寸所形成的尺寸链,称为工艺尺寸链。
装配尺寸链——在机器设计和装配过程中,由有关零件设计尺寸所形成的尺寸链,称为装配尺寸链。
尺寸链的环——组成尺寸链的每一个尺寸,称为尺寸链的环。
尺寸链的环分为:
封闭环、组成环
封闭环——在零件加工过程或机器装配过程中最终形成的环(或间接得到的环)称为封闭环。
组成环——尺寸链中除了封闭环以外的各环称为组成环(一般来说,组成环的尺寸是由加工直接得到的)。
组成环按其对封闭环的影响又可分为:
增环——凡该环变动(增大或减小)引起封闭环同向变动(增大或减小)的环称为增环。
减环——由于该环的变动(增大或减小)引起封闭环反向变动(减小或增大)的环称为减环。
尺寸链简图——将相互联系的尺寸组合从零件或部件的具体结构中单独抽出,画成尺寸链的简图。
二、尺寸链的分类
1、按尺寸链的形成和应用场合
1)工艺过程尺寸链——零件按加工顺序先后所获得的各工序尺寸构成的尺寸链。
2)装配尺寸链——在机器原装配关系中,由直接影响封闭环
精度的相关零、部件尺寸所构成的尺寸链。
3)工艺系统尺寸链——零件在工艺系统中由机床、夹具、刀具和工件等有关尺寸构成的尺寸链。
以上三种尺寸链统称为工艺尺寸链
2、按尺寸链各环的几何特征和所处空间位置
1)直线尺寸链——直线尺寸链由彼此平行的直线尺寸所组成。
2)角度尺寸链——尺寸链各环均为角度。
如垂直度、平等度等位置关系的尺寸链也是角度尺寸链。
3)平面尺寸链——同时具有直线尺寸和角度尺寸的尺寸链。
其平面尺寸链的方程式为:
4)空间尺寸链——组成环位于几个
不平行平面的尺寸链。
3、按尺寸链间相互联系形态分
1)独立尺寸链——尺寸链所有环都只属于一个尺寸链,其变化不会影响其它尺寸链。
2)并联尺寸链——这种尺寸链由两个或两个以上尺寸链通过公共环联系起来。
并联尺寸链可分为:
(1)公共环是各尺寸链的组成环
(2)公共环在一个尺寸链中是封闭环,而在另一个尺寸链中是组成环。
D尺寸链的方程式可表示为:
D0=D1+D2–D0=C0+D2–D3=(C1–C2)+D2–D3
三、尺寸链的计算方法(极值法)
1、极值法计算尺寸链
1)各环基本尺寸的计算。
校核该结构能否保证间隙A0为
0.05~0.75mm。
其方程为:
A0=A3–(A2+A1+A4)
由此可见,当组成环为任意数目时,
其基本尺寸的方程为:
四、工艺尺寸链的计算
五、装配尺寸链
装配尺寸链的封闭环——是装配精度或技术要求。
装配尺寸链的组成环——在装配关系中,对装配精度要求发生直接影响的那些零件的尺寸和位置关系,就是装配尺寸链的组成环。
2、装配尺寸链组成的最短路线(最少环数)原则(重点)
3、达到装配精度的几种方法:
(1)完全互换法;
(2)调整法;
(3)分组装配法;
(4)修配法。
(二)装配尺寸链的完全互换法
完全互换法——是通过控制零件的加工误差来保证装配精度的一种装配方法。
优点:
装配工作简单,生产率高,有利于组织装配流水线,便于采用协作方式组织生产,同时也有利于维修工作。
公差分配的一般原则:
1、当组成环属于标准件尺寸时(例如轴承环或挡圈的厚度等),其公差大小和分布位置在相应的标准中已有规定,是已定值。
2、在并联尺寸链中,如果有一组成环是几个不同装配尺寸链的公共环时,其公差大小和公差带位置应根据对精度要求最严的那个装配尺寸链确定。
3、在确定各待定组成环公差大小时,可根据具体情况选用不同的原则。
在处理直线尺寸链时(原则):
1)若各组成环尺寸相近,加工方法相同,可优先考虑等公差分配原则;
2)若各组成环加工方法相同,但基本尺寸相差较大,可考虑使用等精度分配原则(即尺寸大的公差大些,尺寸小的公差小些);
3)若各组成环加工方法不同,则应采用实际可行性分配原则。
(即加工难、尺寸大,公差分配就大,反之宜然)。
4、各组成环公差带的位置一般可按入体原则标注,但要保留一组成环作为协调环,其公差带的位置由装配尺寸链确定。
(协调环通常选易于制造并可用通用量具测量的尺寸)。
5、为便于应用标准量规,应使组成环公差数值(协调环除外)尽可能符合“公差与配合”国家标准。
机械加工工艺规程的制订
四、定位基准的选择原则(重要)
(一)精基准选择原则:
1、“基准重合”原则;
2、基准统一原则;
3、互为基准原则;
4、自为基准原则。
(二)粗基准选择原则:
1、若工件必须首先保证某重要表面的加工余量均匀,则应选该表面为粗基准;
2、在没有要求保证重要表面加工余量均匀的情况下,若零件上每个表面都要加工,则应以加工余量最小的表面作为粗基准;
3、若工件有的表面不需要加工时,应以不加工表面中与加工表面的位置精度要求较高的表面为粗基准;
4、选作粗基准的表面,应尽可能平整和光洁;
5、粗基准在同一尺寸方向上通常只允许使用一次。
但当毛坯是精密铸件或精密锻件时,可重复使用某一粗基准
五、工艺路线的拟定
(一)表面加工方法的选择
1、考虑因素:
1)各加工表面所要达到的精度、表面粗糙度、硬度;
2)工件的结构形状和加工面的尺寸;
3)生产类型;
4)车间现有设备情况;
5)各种表面加工方法所能达到的经济加工精度和表面粗糙度等。
2、表面加工方法选择原则:
1)所选加工方法的经济精度、表面粗糙度应与加工表面的要求相适应;
2)所选加工方法应能保证加工表面的几何形状精度和表面相互位置精度;
3)所选加工方法应与零件材料的可加工性相适应;
4)所选加工方法应与生产类型相适应;
5)所选加工方法应与本厂现有生产条件相适应。
(二)加工顺序的安排(重要)
1、切削加工工序的安排:
1)先加工基准表面,后加工功能表面;先加工平面后加工内孔表面;
2)先加工主要表面,后加工次要表面;
3)先安排粗加工工序,后安排精加工工序;
优点:
①可使粗加工时夹紧力引起的弹性变形,切削热引起的热变形以及粗加工后内应力重新分布引起的变形,都可通过精加工得到消除
②可及时发现毛坯上的缺陷,以免继续精加工不合格的毛坯;
③可避免精加工表面受到损伤;
④机床设备可得到合理使用。
特殊情况:
①对于加工精度要求不高的零件,可将粗精加工安排在一起进行;
②对重型零件,可在一台机床上进行粗、精加工。
2、热处理工序的安排
作用:
改善材料的性能和消除内应力
1)对改善金相组织和加工性能的热处理工序(如退火、正火等),应安排在机械加工之前;
2)对于提高零件表面硬度的热处理工序(如淬火、渗碳淬火等)一般安排在半精加工之后,精加工之前;对于渗氮,因其氮化层较薄,经渗氮后的磨屑余量小,故一般安排在粗磨之后精磨之前进行;
3)对于除内应力工序(如人工时效、退火等)一般安排在粗加工之后,精加工之前。
3、检验工序的安排
1)在粗加工结束之后,重要工序之前;
2)零件从一个车间转到另一个车间之前;
3)特种性能(磁力探伤、密封性)检验之前和零件全部加工结束之后。