铸钢脱氧知识详细讲解.docx
《铸钢脱氧知识详细讲解.docx》由会员分享,可在线阅读,更多相关《铸钢脱氧知识详细讲解.docx(6页珍藏版)》请在冰点文库上搜索。
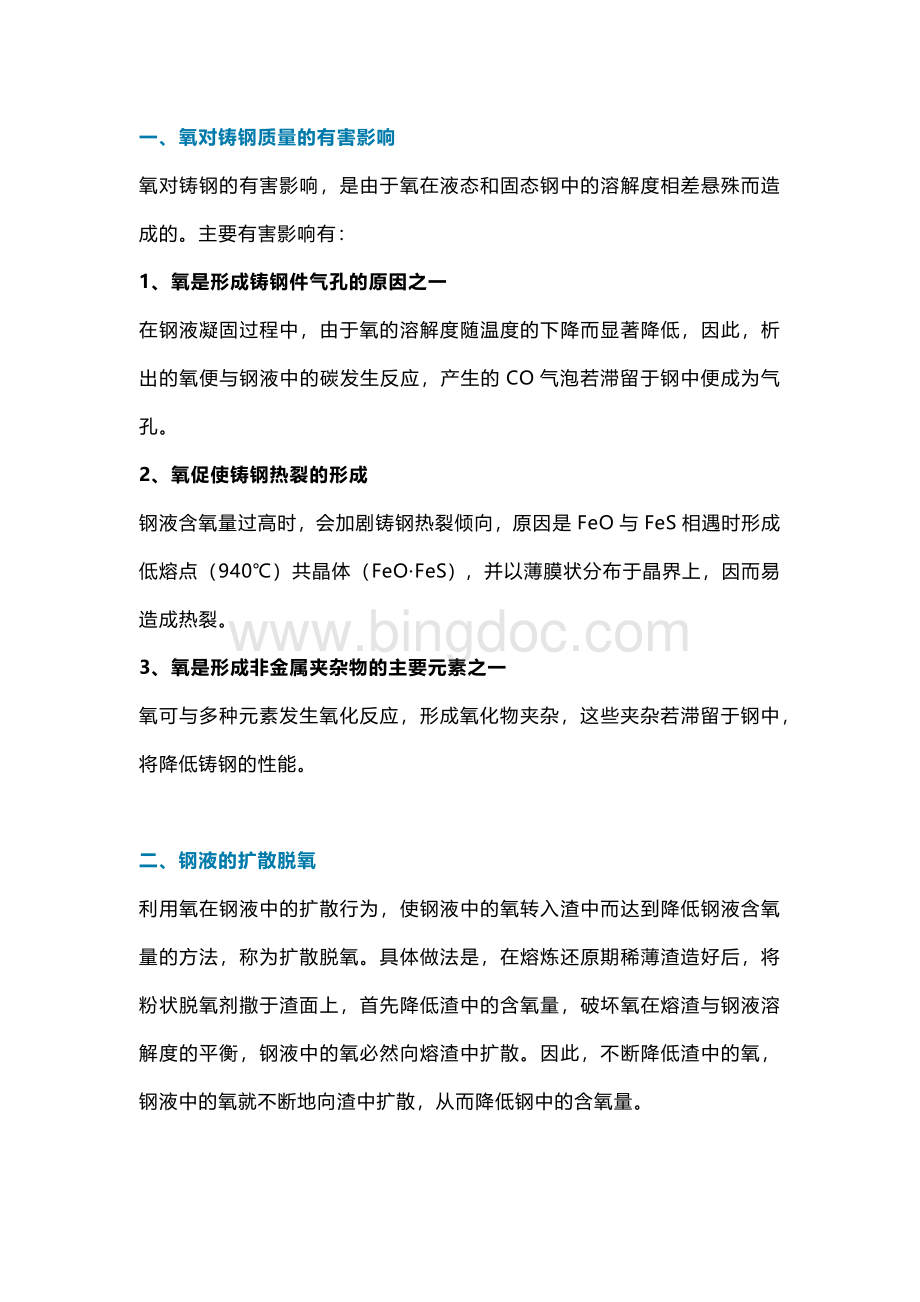
一、氧对铸钢质量的有害影响
氧对铸钢的有害影响,是由于氧在液态和固态钢中的溶解度相差悬殊而造成的。
主要有害影响有:
1、氧是形成铸钢件气孔的原因之一
在钢液凝固过程中,由于氧的溶解度随温度的下降而显著降低,因此,析出的氧便与钢液中的碳发生反应,产生的CO气泡若滞留于钢中便成为气孔。
2、氧促使铸钢热裂的形成
钢液含氧量过高时,会加剧铸钢热裂倾向,原因是FeO与FeS相遇时形成低熔点(940℃)共晶体(FeO·FeS),并以薄膜状分布于晶界上,因而易造成热裂。
3、氧是形成非金属夹杂物的主要元素之一
氧可与多种元素发生氧化反应,形成氧化物夹杂,这些夹杂若滞留于钢中,将降低铸钢的性能。
二、钢液的扩散脱氧
利用氧在钢液中的扩散行为,使钢液中的氧转入渣中而达到降低钢液含氧量的方法,称为扩散脱氧。
具体做法是,在熔炼还原期稀薄渣造好后,将粉状脱氧剂撒于渣面上,首先降低渣中的含氧量,破坏氧在熔渣与钢液溶解度的平衡,钢液中的氧必然向熔渣中扩散。
因此,不断降低渣中的氧,钢液中的氧就不断地向渣中扩散,从而降低钢中的含氧量。
扩散脱氧常用的粉状脱氧剂有;碳粉、硅铁粉、硅钙粉、铝粉、碳化钙粉等。
这些脱氧剂中的C、Si、Al、Ca等元素进入渣层后便于(FeO)发生还原反应,如:
脱氧产物进入炉气或被熔渣吸收,因此,扩散脱氧不污染钢液。
但由于扩散脱氧是在渣与钢液界面上进行,氧由钢液中向渣中扩散需要的时间较长,因此,生产效率低,能耗高。
三、钢液的沉淀脱氧
沉淀脱氧是将块状的脱氧剂直接加入钢液中,脱氧剂与(FeO)发生沉淀反应而脱氧。
沉淀脱氧又称强制脱氧,沉淀脱氧法脱氧产物的排除,影响脱氧效果。
按脱氧产物的形成时间划分,脱氧产物可分为:
一次脱氧产物——在炉内或包内加入脱氧剂后立即形成的脱氧产物;
二次脱氧产物——已脱氧的钢液在其冷却至液相线之前所形成的脱氧产物;
三次脱氧产物——在液相线与固相线之间凝固时所形成的脱氧产物。
这三类脱氧产物统称为内生脱氧产物。
研究表明:
一次脱氧产物具有聚集、长大和上浮的有利条件,故绝大部分能排出钢液。
二次、三次脱氧产物均不能排出铸件,特别是三次脱氧产物是钢液在凝固过程中产生的,常滞留于枝晶之间,对铸钢质量具有决定性影响。
铸钢中所看到的氧化物夹杂,绝大多数是三次脱氧产物。
(一)包内沉淀脱氧机理
1、 脱氧反应 即脱氧剂与(FeO)的化学反应;
2、 脱氧产物的形核、聚合长大、上浮和排出。
整个过程都伴随着热力学和动力学作用。
研究证明,采用强脱氧剂脱氧时,脱氧产物可迅速排出钢液,如脱氧产物Al2O3虽为固态颗粒,但其排出速度很快。
脱氧产物的排出速度主要取决于脱氧剂的种类,而与脱氧产物的状态及其尺寸无明显关系。
特别是用铝脱氧时,在出钢过程中加入铝1~2min,钢中的氧便与铝形成Al2O3并排出。
其原因是,Al2O3与钢液的润湿性差和相间张力大(2N/m)。
此外,钢液流入钢包时,有足够的搅动,使脱氧产物因碰撞而聚合长大,同时搅动也使钢液和熔渣剧烈运动,促使脱氧产物被熔渣捕获或粘附于包衬表面。
(二)沉淀脱氧用脱氧剂介绍
沉淀脱氧用脱氧剂应具有强的脱氧能力,其脱氧产物不溶于钢液,并易于从钢液中排出。
1、元素的脱氧能力 研究证明:
脱氧元素对氧的亲和力越大,其脱氧能力越强,钢中的溶解氧就越低。
元素的脱氧能力,一般随温度的降低而提高。
通常说钢中的含氧量是指总氧量,它包括溶解氧和化合氧。
所以,元素的脱氧能力只反映其降低钢中溶解氧的能力,而降低化合氧的能力,则与脱氧产物的化学组成和物理特性、钢液温度及动力学因素等有关。
当脱氧元素的含量为0.1%时,各元素的脱氧能力由强到弱排序为:
Ca>RE>Zr>Al>Ti>B>Si>C>V>Cr>Mn。
脱氧元素在一定含量范围内,随其含量的增加,与其相平衡的氧含量对应降低,但是,当脱氧元素超过这一含量后,随着脱氧元素含量的增加,相应的平衡氧含量反而增大,这说明并非脱氧剂加入愈多,钢液中的溶解氧就降低的多。
2、单元素脱氧剂介绍
⑴ Mn 锰是较弱的脱氧剂,是常用的脱氧剂之一。
⑵ Si 硅是较强的脱氧剂,是常用的脱氧剂之一,其脱氧产物SiO2是高熔点的固体质点,能被钢液所润湿,排出较为困难。
感应炉内用硅脱氧时,氧的降低速度是较快的,硅加入后5~10min,氧含量便可降至最低值。
包内用硅脱氧的速度与炉内基本相同。
⑶ Al 铝是最常用的强脱氧剂,感应炉熔炼时加入铝0.1%,铝脱氧后仅在3~4min内,钢中的溶解氧便降至0.01%以下,包内脱氧时,出钢前先将铝加入包内,然后出钢,出钢后2~3min内,钢液中的氧含量便可降至0.02%以下。
出钢后由于钢液温度的降低,铝的脱氧能力提高,这样钢液在包内镇静时,钢液中的氧含量仍能缓慢的下降。
⑷ Ca 钙是很强的脱氧剂,也是强的脱硫剂,但由于钙的气化而显著降低其脱氧效果。
为克服其缺点,必须降低其蒸气压,Si、Al不仅能降低钙的蒸气压,而且还可提高钙的溶解度。
用硅钙合金脱氧,还可改善夹杂物的形态成为球状,因而改善钢的性能。
此为硅钙合金脱氧的突出优点。
⑸ Ti 钛是较强的脱氧剂,脱氧能力强于硅而弱于铝。
其脱氧产物因钛含量不同而不同。
当Ti<0.2%时,脱氧产物是TiO2或Ti3O5。
Ti的脱氧产物尺寸为16~18μ,近似球状,并均匀地分布在晶粒内部。
另外,Ti在钢液中还可形成高度弥散的TiN,其尺寸为4~14μ,可作为非自发结晶核心,而细化晶粒。
TiN还可防止铸钢件产生脆性断口。
当Ti含量为0.06%时,沿晶界会形成片状共晶硫化物而降低钢的冲击韧性。
因此,钛脱氧时,钢中适宜的钛含量为0.02~0.06%。
通常为防止AlN对铸钢件性能的不良影响而采用钛代替铝终脱氧。
⑹ Zr 锆是极强的脱氧剂,在1650℃时,锆的脱氧能力强于铝,只需加入少量的锆终脱氧,便可获得氧含量极低的钢。
锆的脱氧产物为直径3μ的小球。
Zr脱氧时形成的ZrN,可作为非自发结晶核心,细化晶粒,同时还可防止脆性断口。
⑺ RE 也是良好的脱氧剂。
稀土金属通常是镧(La)系元素的总称。
La、Ce、Pr、Nd四个元素与铸钢生产较为密切,稀土的脱氧能力强于Zr、Al、Ti,接近于Be,而稍低于Ca、Mg。
采用稀土脱氧有如下特点:
① 脱氧反应的同时伴随有脱硫反应。
RE能同时与O、S反应,生成稀土氧化物、稀土硫化物和稀土氧硫化物,同时降低钢中的氧和硫。
② 稀土氧化物、硫化物熔点高、密度大、质点小,不易排出而滞留于钢中。
③ 稀土金属的突出优点是,使钢中夹杂物球化,而有利于提高钢的性能。
3、常用复合脱氧剂介绍
⑴ 硅锰合金复合脱氧 Mn是弱脱氧元素,Si是较强脱氧元素,Si、Mn配合使用,可获得良好的脱氧效果,如使用硅锰合金复合脱氧剂。
生产中常用“先加锰铁后加硅铁于炉内”的复合脱氧法,也可获得较好的效果。
⑵ 硅锰铝合金复合脱氧 Si和Mn可提高Al的脱氧能力。
采用硅锰铝复合脱氧剂时,无论在炉内或包内脱氧,效果均好。
生产中常用“先锰铁后硅铁”炉内预脱氧,再用铝包内终脱氧,效果也很好。
⑶ 铝硅铁合金复合脱氧剂 Al—Si—Fe合金的化学成分见下表:
代号
化学成分(%)
Al
Si
C
S
P
Fe
≤
Al50
48~52
16~20
0.50
0.050
0.050
余
Al45
>45
20~30
0.50
0.050
0.050
余
Al35
>35
>20
0.50
0.050
0.050
余
Al25
>25
>25
0.50
0.050
0.050
余
Al—Si—Fe合金的外观成银灰色,较脆易破碎。
密度约4.17g/cm3,熔点约1000℃左右。
常采用块状炉内预脱氧,粉状包内终脱氧。