压铸模具设计制作标准.docx
《压铸模具设计制作标准.docx》由会员分享,可在线阅读,更多相关《压铸模具设计制作标准.docx(23页珍藏版)》请在冰点文库上搜索。
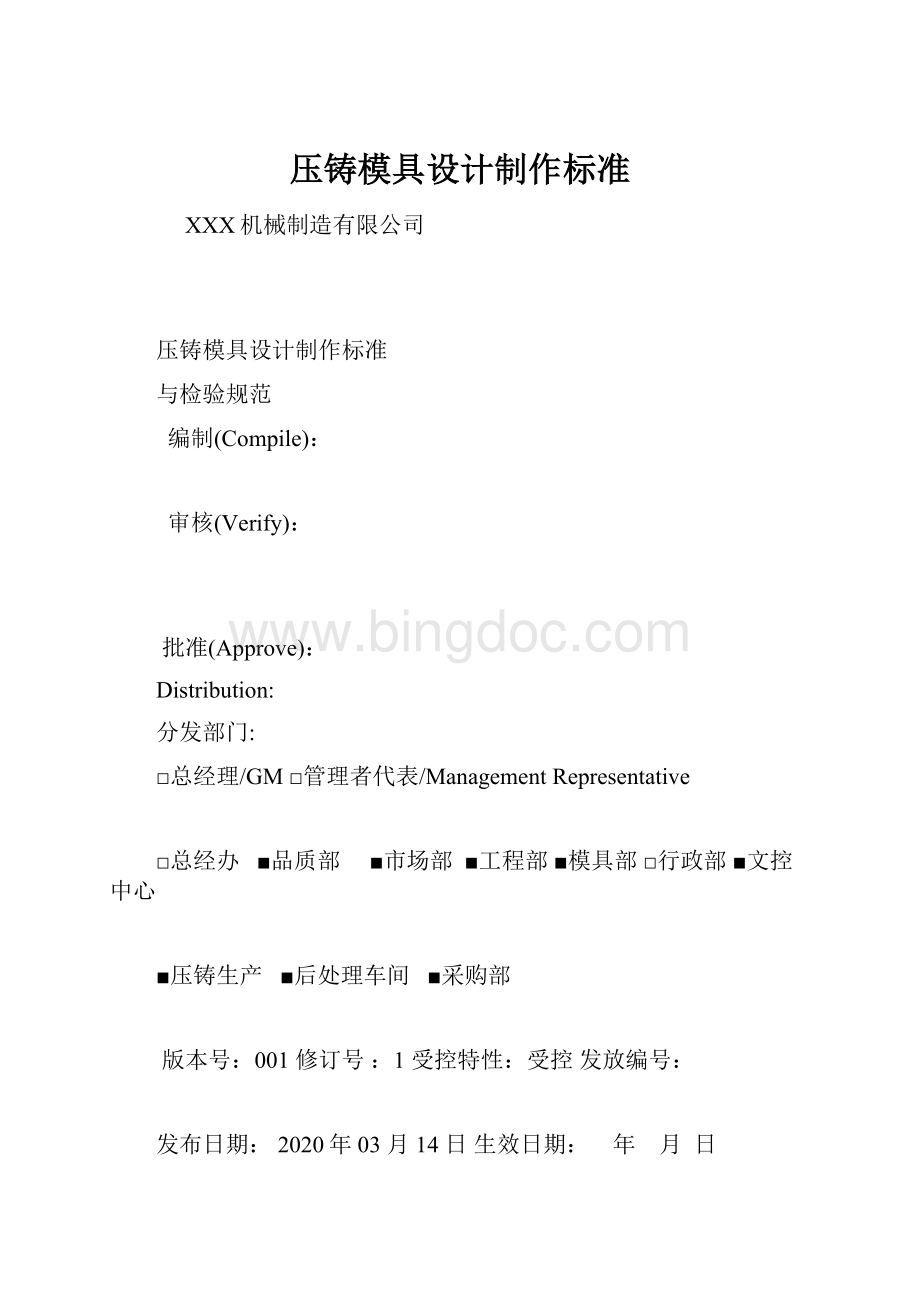
压铸模具设计制作标准
XXX机械制造有限公司
压铸模具设计制作标准
与检验规范
编制(Compile):
审核(Verify):
批准(Approve):
Distribution:
分发部门:
□总经理/GM□管理者代表/ManagementRepresentative
□总经办■品质部■市场部■工程部■模具部□行政部■文控中心
■压铸生产■后处理车间■采购部
版本号:
001修订号:
1受控特性:
受控发放编号:
发布日期:
2020年03月14日生效日期:
年月日
一、目的
1.按本公司的压铸机规格尺寸设计模具与压铸机配合尺寸,防止干涉;
2.模具各部件制作标准化,便于生产使用装拆,缩短了换模时间。
二、适用范围
本公司模具设计制造和外协厂商。
三、模具结构
图1:
模具的构造和构成部件
备注:
模具构造和构成部件中的17在大模具(800T及以上机台)中需追加.
图2:
模具顶出系统构成部件
四、模具与压铸机配合结构尺寸
4.1.选用标准料管时模具与压铸机配合尺寸见下图;
4.2.模具与压铸机配合压板槽,拉杆孔,模具总厚相关尺寸见下图;
注:
800吨及800吨以上必须做封底版(特殊情况需提出)
五、外模结构
5.1.每副模具固定模和活动模的模架顶部和底部(天侧和地侧)各做2个吊环孔,左右侧有位置也需加上,需设于模具的重心上(每半模),吊环平面必须安装到位与模面平齐,吊装时不允许干涉水管,装模时吊起的倾斜角度不能大于5°,以利于吊装时的安全。
吊环规格表
5.2.钻吊环孔时,需先做5mm深的避空孔。
如下图所示
5.3.冷却水管和恒温油管接头螺纹为PT1/4;PT3/8。
所有的冷却水管、油管必须全部装配上,同时用5BAR气压进行测试,不能漏水漏油。
模架上用IN1&OUT1(IN2&OUT2……)标识(含点冷、直通冷却、恒温油管)。
5.4.模架上水管过孔直径壁空至少N+10mm;模架上顶针过孔直径壁空N+2mm。
5.5点冷却水管要求编号,并在冷却塔上安装阀门,控制每只点冷却的进水和出水。
普通水管螺纹接头用PT1/4并在模具图上标明。
5.6.模具模号、产品料号、模具尺寸、模具重量、制造日期、厂商标记,需刻在铭牌上用四颗螺丝锁紧在模架上或直接翻砂在模架易识别处。
5.7.如下是苏州精密铸造有限公司模具铭牌。
(模具,模架送到铭牌必须装好)铭牌尺寸:
120X70X1.5mm
5.8.为防止生产过程中模具铭牌掉落,故铭牌安装后固定铭牌的螺丝不能超出模架平面,所以每套模具都要在动模架操作侧中间位置开一个125X75X3mm的槽,以方便安装铭牌。
在操作侧的模脚上必须刻上产品料号,清晰可见。
5.9.固定外模及活动外模需制作4个敲模孔。
5.10.外模四周加工撬开槽。
5.11.浇口套必须加装冷却水,冷却环厚度10MM以上,水管孔为PT1/4,冷却环热套装配,与外模装配。
5.12.跨距大于150MM时都应考虑加支撑。
支撑柱直径(或宽)不小于50MM,尽可能靠近压射变形位。
5.13.大型模具(配合压铸机在800吨及以上的)地侧要加模脚支撑。
(所有模具支撑脚不得用圆柱支撑,需要用铸铁方形支撑;安装时不得有干涉,特殊模具无法制作时需要提出)
5.14.四根导柱用螺丝锁紧在固定模架上,同时导柱要加工排屑槽,导柱顶端要做成带20度斜度的锥形状。
【见下图所示】
【导柱安装图示】【斜导柱避空区域图示】
5.15斜导柱在动模架的避空区域要至少10mm以上。
【见上图所示】
5.16模架外发订制时,所有孔和螺牙都要加工出来;包括:
顶针过孔,水管孔,吊环孔,敲模孔,螺丝过孔,锁零件的螺丝孔,固定油缸支撑板的螺丝孔,倒拉孔等。
模架厂同时要提供导柱,导套,复位杆,顶针板导柱导套,支撑柱,这些配件。
其中需要特别说明的是,支撑柱要比模脚高,具体高多少见下表。
六、内模
6.1内模材料来料时,要求供应商标注清楚正反面。
6.2.模仁加工后热处理前做去应力处理。
真空淬火热处理硬度:
500吨及以上模具为HRC46°-48°,500吨以下模具为HRC48°-50°(具体按图纸标识为准)。
精加工后按模具工艺具体规定再做去应力处理。
根据材料规格表;
6.3.省模和抛光按客户要求的粗糙度和模具出模方向执行。
6.4.型腔最小圆角R0.5,最小拔模斜度1°~2°。
特殊指定的除外。
6.5.模芯上有镶件必须线割时,必须预先打穿丝孔,当跨距大于200mm时,穿丝孔要做2个。
6.6.按本公司要求在内模表面指定位置刻上标记、产品料号、产品材质、批量管制章、模穴编号及环保标记。
(具体按产品要求)
6.7.在内模侧边基准角刻上材质及模具编号。
6.8.内模若有镶针,需提供两套备用镶针和一份相应的图纸(具体按模具技术协议)。
6.9.内模分型面高出模架分型面尺寸见下表,内外模安装间隙<0.1mm。
(模具在变形情况下不能有干涉。
)
6.10.内模吊环孔要便于内模装卸,吊环螺孔最小为M16(具体根据模具大小来定)。
6.11.内模最小厚度及渣包距模仁边的最小单边距,如下图所示(注:
有分流锥的一侧应适当放大)。
具体根具产品结构定。
七、滑块
7.1.滑块材料采用H13电渣重熔钢或指定的热作模具钢材料(如Dievar;DAC55),滑块座材料采用H13或P20钢,如果浇道从滑块座进入,则滑块座也采用H13电渣重熔钢或指定的热作模具钢材料。
7.2.尽量采用油缸抽芯,如果抽芯距离小于50mm或滑块投影面积较小时可采用斜导柱抽芯。
7.3.滑块使用标准油缸抽芯
7.3.1.选用的油缸必须满足前进和后退的整个距离,防止发生机械故障;滑块压缸直径φ80MM以上,行程超过60以上,必须留20mm缓冲行程。
7.3.2.油压滑块必须采用防水型行程开关,耐高温电线,开关尽量装在机械面侧上,勿装在分模面上,其位置调节好后要能保持固定;所有油缸必需采用哈呋连接;油压缸快速接头必需做90度转角接头,接头规格为PT1/2。
所有油缸安装尺寸需要按照下表执行制作。
7.3.3.滑块上必需做限位柱(如下图)
7.3.4.所有油缸支架必需做定位销
7.3.5.定模油缸需安装止逆阀
7.3.6.油缸抽芯的楔紧块单边斜度10°。
7.3.7每个油缸必须配一套油缸密封圈
7.4.滑块若使用斜导柱时
7.4.1.250T以上斜导柱直径最少φ30MM。
7.4.2.斜导柱角度:
15-20°。
7.4.3.楔紧块单边斜度17°-22°。
7.4.4.必须有回位装置,起到回位作用。
7.5.抽芯距离需避开顶针的干涉。
7.6.必须设置轨道使滑块在其上滑动,轨道材料为P20或H13钢,热处理HRC48~52,嵌合在模架上,用螺钉锁紧。
滑块座与导轨磨擦面需表面淬硬。
轨道槽高最小15MM、深6MM,滑块宽度超过150MM以上者,中央必须增加辅滑道和耐磨板。
7.7.滑块必须有楔紧块。
楔紧块用H13或P20钢,热处理硬度HRC48-52,与滑块的整个宽度贴合,用螺钉连接在模架上。
不同吨位的模具,楔紧块到模架的边缘最小距离见下表。
7.8.抽芯与楔紧块的楔合长度至少超过抽芯的2/3,抽芯与模芯的楔合长度至少超过50mm,根部留25-30mm直身位,单边斜度2-3°,特别指定的除外。
楔紧块到模架边缘最小距离表
7.9.设计时考虑滑块上的抽芯要作到不拆卸桥式连接的油缸就可以取下,抽芯与滑块座的连接采用嵌合式螺钉连接。
如下图所示:
7.10.排气块尽量采用单个渣包单个排气,排气必需做表面淡化处理。
八、型芯,镶件
8.1.用H13型芯或SKD61顶针做型芯。
8.2.型芯的定位不采用简易的螺钉锁紧,该方法仅用于不重要的小型芯上。
轴向浮动在0.02以内。
8.3.型芯根部保持R0.5。
8.4.形成通孔的型芯碰穿面让开0.1mm,以免合模时压伤。
8.5.拔模斜度单边0.5度,图纸许可时可以大一些。
8.6.异形镶件必须在外面加上虚拟的四方块,2D用双点画线清晰的表达出四方块的大小和异形镶件在四方块中的位置,3D在3D图上把此四方块做出来与之相结合。
重点强调:
做完后互相检查,正确后才下发。
8.7.其他考虑:
8.7.1.小于ø3的孔不铸造出来,可设置引针孔用加工的方法钻
出。
除非长度小于直径便可铸出。
8.7.2.动模的型芯是否容易顶出。
8.7.3.型芯和滑块是否可以安装冷却水。
8.7.4.避免型芯在浇口处被冲刷。
九、顶出系统
9.1.顶出必须加装后退限止块最少4只及顶出前限位,前限位必须保证顶针板不压坏点冷却。
9.2.顶出板后退限止块不能和压铸机的顶出杆发生干涉。
9.3.回位销比分模面高0.1mm。
9.4.顶针板底板倒拉孔900T以上做6个倒拉孔,900T以下做4个倒拉孔。
9.5.顶针的大小:
尽可能大一点,通常情况下,最小选ø4mm(除特殊情况)
Ø6mm以下的顶针采用双节顶针
用SKD61的标准顶针,如:
ø4,ø5,ø6,ø8,ø10,ø12,ø16,ø20
9.6.顶出距离:
顶出铸件离开最高点至少10mm。
除非特殊要求。
对薄壁件,顶针尽量不要布在面上,尽量布在筋上。
9.7.型腔上顶针孔
直径8mm以下的孔,间隙为0.02—0.03mm
直径8mm以上的孔,间隙为0.03—0.05mm
配合段25—30mm
孔间的模具钢壁厚至少4mm,尽可能10mm。
重要点:
顶针孔和顶出板必须保持垂直,所有模具顶出板要设置导柱和导套,顶针和顶针孔保持在一条直线上,型腔热处理后采用线切割加工顶针孔。
顶针不能与顶针孔的避空位接触。
9.8.顶出板用M12的螺钉紧固,间隔距离不大于150mm。
9.8.所有的顶针尾部必须编号,编号顶针1,2,3,4,,,N(如图),浇道处顶针加十字,字母由公司指定,如顶针为非标类型的,需提供顶针备品两套,并提供图纸一份(顶针与顶针孔的配合公差使用H7配合)。
顶针编号图
十、冷却水管(含油管)
10.1.尺寸:
10.1.1.直通冷却:
用ø10mm的或ø12mm水冷(油冷)通道,PT1/4螺纹连接。
10.1.2.点式冷却:
点冷采用专用点式冷却管,点冷却水管使用快速接头。
10.2.冷却水到型腔的距离,到型腔和复杂的滑块表面以及浇道为:
25mm,到顶针孔、螺钉孔的距离可以为10mm,型腔转弯或尖角处必须大于40mm。
10.3.型芯冷却,尽可能的采用直通冷却,根据型芯的大小和距浇道的位置决定。
10.4.冷却水进出口采用集中汇流,便于拆装,进水口加小阀门,要避开连接螺钉、顶针,统一连接到模具上方的集中排水器上。
10.5.
集中冷却水
10.6.分流锥的冷却水管,分流锥的冷却水管到分流锥表面的距离为20mm—25mm,浇口部位的冷却水管的进水管位于料饼的正下方,浇口套与分流锥必须要有定位。
分流锥的冷却水
十一.其他注意事项
11.1.在分流锥和渣包上刻上压铸原材料牌号。
11.2.模具有形状相同或对称的镶件,抽芯等必须设计防呆结构,动定模芯不能设计为正方形。
此标准为基础性技术指导文件,如在设计和制造过程中遇到特殊技术问题,具体情况具体分析,用最佳的方案解决。