无损检测工艺规程.docx
《无损检测工艺规程.docx》由会员分享,可在线阅读,更多相关《无损检测工艺规程.docx(57页珍藏版)》请在冰点文库上搜索。
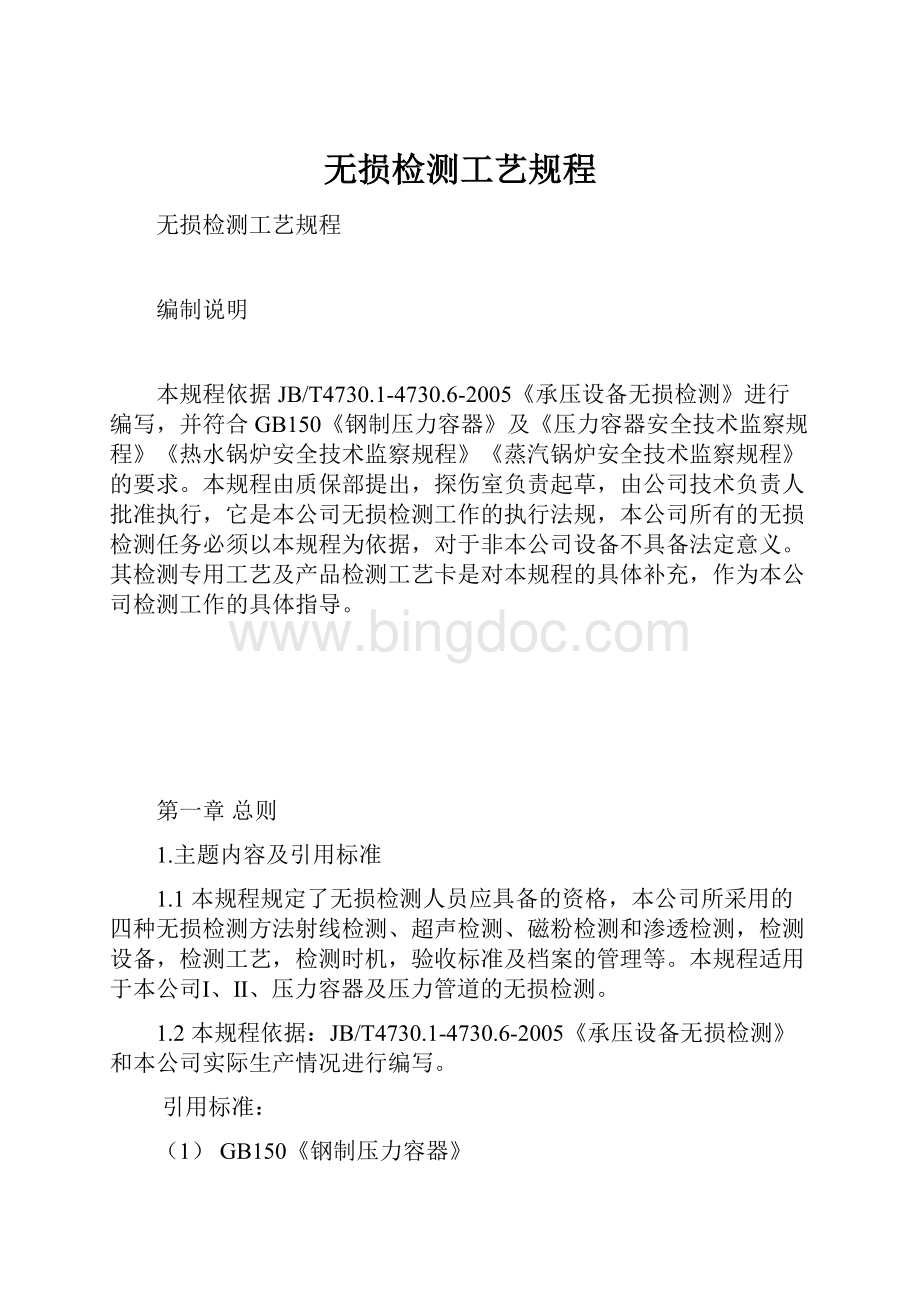
无损检测工艺规程
无损检测工艺规程
编制说明
本规程依据JB/T4730.1-4730.6-2005《承压设备无损检测》进行编写,并符合GB150《钢制压力容器》及《压力容器安全技术监察规程》《热水锅炉安全技术监察规程》《蒸汽锅炉安全技术监察规程》的要求。
本规程由质保部提出,探伤室负责起草,由公司技术负责人批准执行,它是本公司无损检测工作的执行法规,本公司所有的无损检测任务必须以本规程为依据,对于非本公司设备不具备法定意义。
其检测专用工艺及产品检测工艺卡是对本规程的具体补充,作为本公司检测工作的具体指导。
第一章总则
1.主题内容及引用标准
1.1本规程规定了无损检测人员应具备的资格,本公司所采用的四种无损检测方法射线检测、超声检测、磁粉检测和渗透检测,检测设备,检测工艺,检测时机,验收标准及档案的管理等。
本规程适用于本公司Ⅰ、Ⅱ、压力容器及压力管道的无损检测。
1.2本规程依据:
JB/T4730.1-4730.6-2005《承压设备无损检测》和本公司实际生产情况进行编写。
引用标准:
(1)GB150《钢制压力容器》
(2)《热水锅炉安全技术监察规程》
(3)《压力容器安全技术监察规程》
(4)《蒸汽锅炉安全技术监察规程》
(5)GB5616《无损探伤应用导则》
(6)GB/T12604(1-6)《无损检测术语》
(7)GB4792《射线防护基本标准》
(8)《特种设备无损检测人员考核与监督管理规则》
2.检测人员
2.1检测人员必须按《特种设备无损检测人员考核与监督管理规则》取得资格证书,从事与其资格证书相适应的工作。
2.2
2.3检测人员的身体素质,视力须满足JB/T4730.1-2005的要求并定期进行身体检查,并建立个人健康档案。
2.4从事无损检测工作的人员,必须坚持职业道德,抵制降低产品质量的行为,严把质量关。
检测责任师有责任保证标准、法规,工艺的正确实施,并有权拒绝不符合标准,法规要求的任何检测工作。
3.检测方法:
3.1各种检测方法都各有特点,在选用检测方法时应根据图纸及技术文件的要求进行,并应符合GB150及《压力容器安全技术监察规程》《热水锅炉安全技术监察规程》《蒸汽锅炉安全技术监察规程》的要求。
如果选择两种或多种检测方法进行补充检测时,则每种方法的检测结果都应合格,才能算合格,否则应进行返修处理。
3.2压力容器壁厚小于等于38mm时,其对接接头应采用射线检测;由于结构等原因,不能采用射线检测时,允许采用可记录的超声检测。
3.3压力容器壁厚大于38mm(或小于等于38mm,但大于20mm且使用材料搞拉强度规定值下限大于等于540Mpa)时,其对接接头如采用射线检测,则每条焊缝还应附加局部超声检测;如采用超声检测,则每条焊缝还应附加局部射线检测。
无法进行射线检测或超声检测时,应采用其他检测方法进行附加局部无损检测。
附加局部检测应包括所有的焊缝交叉部位,附加局部检测的比例为本规程原无损检测比例的20%。
3.4对有无损检测要求的角接接头、T形接头,不能进行射线或超声检测时,应做100%表面检测。
3.5铁磁性材料容器的表面检测应优先选用磁粉检测。
4.检测时机的选择:
4.1对于不同焊接材料的焊接,由于其可焊性的差异,焊接接头结构的不同,存在的淬硬性也就不同,因此对于不同焊接材料的焊接接头应选择不同的检测时机,以确保检测的可靠性。
4.2对焊接接头的检测应在焊后进行。
对有延迟裂纹倾向的材料,至少应在焊后24小时后进行检测。
4.3对于检验热处理工艺性能时应安排在热处理后进行。
4.4对于封头的检测应在冲压成型后进行,否则无效。
5.检测表面的验收
5.1凡是进行无损检测的工件,必须经外观检查合格后方能进行无损检测。
5.2进行检测的工件表面,除应符合标准要求以外,其表面不得存在:
裂纹、气孔、弧坑、咬边和肉眼可见的夹渣等缺陷,焊接接头两侧的飞溅和熔渣,必须清除。
5.3对于进行超声波或表面探伤检查的部件除满足上条规定以外,所有影响检测的锈蚀、防护层和污物都应予以清除,其表面粗糙度应符合标准要求。
5.4对于上述要求不合格的须加以修整,合格后才能进行检测,否则,探伤人员有权拒绝检
测工作。
6.检测档案管理与规章制度
6.1坚持严谨的工作态度,认真学习技术,没有资格的人员不能独立进行检测工作。
6.2认真填写记录报告,严格执行标准规定,不得弄虚作假。
6.3做好档案的保存工作,并根据要求所有的检测档案报告及检测底片保存不少于七年。
7.安全防护管理
7.1无损检测工作由于其一般工作于现场,其检测过程中与电接触,其射线检测具有一定的辐射危害,渗透检测所使用药品为可燃性和具有毒性介质的存在,因此必须注意安全防护管理。
7.2对于射线检测,其工作场地,及防护措施符合GB4792的规定。
7.3对于操作过程必须严格认真执行操作规程及厂内辐射安全的管理规定。
射线检测设备操作规程见附录
第二章无损检测质控程序
2.1本程序由无损探伤室负责实施及控制,并与其他部门配合执行。
2.2根据本公司具体情况制定,目的在于有效的服务于生产,并有助于质保体系运转,对产品质量进行有效监控,并通过对无损检测程序进行质量控制,为焊接工艺的制订与校对,产品焊接结构的内在质量状况提供准确依据。
2.3无损检测责任师负责组织检测人员对材料及焊接接头的检验结果进行评审,并负责对检测人员的技术培训。
2.3.1相关部门负责按检测评审结果对检测产品进行处置。
2.4工作过程
2.4.1无损检测系统控制一览表(表1)
控制环节
控制点名称
控制类别
负责人
接受任务
接收委托
审阅点
探伤专业负责人
探伤前准备
人员资格审查
检查点
检查员
仪器校验
审阅点
无损检测专业负责人
探伤工艺编制
审阅点
无损检测专业负责人
探伤实施
施探表面复查
检查点
无损检测专业负责人
复验扩探
审阅点
无损检测责任工程师
报告签发
报告签发
停点
无损检测责任工程师
2.4.2无损检测质量控制图(图1)
2.4.3质保部根据生产任务情况,技术图样要求、产品及材料工件的原始参数、填写无损检测委托单转到本程序。
2.4.3.1本程序负责人在接受任务委托后,负责组织检测人员着手任务的研究及准备工作。
2.4.3.2质保部负责组织检验员对材料及焊接产品的外观质量验收确认合格后,出具无损检测委托单转到本程序。
2.4.4检测准备
2.4.4.1无损检测责任师负责组织无损检测工艺的制订,审核并保证其正确实施。
2.4.4.2检测工艺的编制人员必须是由国家认证合格的并具备相应Ⅱ级或以上资格的人员,其通用工艺规程必须经厂级技术负责人批准才能实施执行。
2.4.4.3建立无损检测人员的培训、资格档案和检测设备的购置、维护档案记录,并定期进行仪器的校准检修。
2.4.5检测表面的复查
2.4.5.1本程序接到无损检测委托单后,由本程序负责人或其指定的检测人员进行表面复查。
2.4.5.2检测表面的质量必须符合有关标准、文件及检测技术条件的要求,且不影响对检测结果的评定,否则检测人员拒收并通知有关部门。
2.4.6检测的实施
2.4.6.1全过程应执行检测工艺并认真填写检测原始纪录,绘制检测位置简图。
2.4.6.2注意过程中的安全防护操作,防止射线辐射对人体的危害,注意检测器材的安全保管,防止使用过程的污染及防火。
2.4.7检测结果的评审
2.4.7.1无损检测责任师组织具有相应Ⅱ级及以上资格的检测人员对检验结果进行评审。
2.4.7.2进行评审的检测结果必须是符合JB/T4730.1-4730.6-2005标准或其他相关标准要求。
2.4.7.3对评审结果不符合标准要求的,进行产品的扩充检测后,填写焊接不合格检测处置单和检测缺陷传递单,传递到质保部,由质保部与生产车间协商进行返修处置,并做好检测评审纪录。
2.4.8扩检与复检
2.4.8.1对局部射线检测或超声检测的焊接接头,若在检测部位出现超标缺陷时。
则应时行不少于该条焊接接头长度10%的,且不小于250mm的补充局部检测;如仍不合格,则应对该条焊接接头全部检测。
2.4.8.2对返修部位的复检根据附录E执行。
2.4.9检测报告的填写、审核与签发
2.4.9.1经检测评审合格后,并开具无损检测合格通知单,通知车间进行下序工作。
并进行检测报告的填写,报告人员根据评审纪录和检测纪录认真填写。
2.4.9.2填写好的报告经审核人审核签字后。
最后由无损检测责任师进行核定签字。
2.4.9.3在报告的审核及核定过程中如发现问题,则重新进行检测结果的评审复验。
2.4.9.4核定合格后的报告,一式三份,一份留存入档,两份由质保部存入产品档案及提交用户。
2.4.10检测档案内容:
a:
无损检测委托单b:
焊接不合格检测处置单
c:
无损检测合格通知单d:
无损检测报告
e:
无损检测位置简图f:
无损检测工艺卡
g:
底片
第三章射线检测工艺规程
1.主题内容及工艺范围
1.1本工艺具体规定了射线检测对象、方法、人员资格、设备、检测技术及验收标准的基本要求。
1.2本工艺根据JB/T4730.2-2005的要求及我公司具体情况制订,适合用于2-50mm的钢制水压设备A、B类对焊接缝及钢管的对接焊缝射线检测,并符合《容规》及GB150《蒸规》《热
规》的要求。
1.2.1本工艺实施过程中在满足标准的前提下,必须遵照产品设计图样的技术要求规定。
1.2.2对特殊检测工件以及本工艺范围外的检测,必须制订相应的工艺措施,在保证检测结果的准确性的前提下进行。
1.2.3射线检测专用工艺及具体产品工艺卡为本工艺具体补充,其规定更明确,作为检测实施过程中的具体指导。
2.人员要求
2.1检测人员必须经技术培训,应按照《特种设备无损检测人员考核监督管理规则》进行考核,取得资格证书,方能承担与资格证书技术等级相适应的无损检测工作。
2.2射线检测人员未经矫正或经矫正的视力应不低于1.0,从事评片的人员每年检查一次视力。
3.安全防护
3.1在检测的实施工作中,应遵循时间、距离及屏蔽的三大防护方法,全过程控制射线防护的安全,并符合GB18871、GB1635和GB18465的规定。
3.2现场进行X射线检测时,应按GB16357的规定划定控制区和管理区,设置警告标志,检测人员应佩带个人计量仪。
4.检测设备、器材和材料
4.1本公司现有设备见表《1》
4.1.1设备的选用:
根据工件材料密度、形状、厚度尺寸选择。
为保障设备的使用寿命,必须严格执行操作规程,选择的透照规范尽量在选择使用的X光机额定电压的80%内。
4.2胶片:
根据JB/T4730.2-2005要求,一般选用T3型胶片,我公司基本选用爱克发胶片,也可选用相同类型胶片。
4.2.1无论选用任何类型胶片,但其暗室处理的配方必须与所用胶片配套。
4.3增感屏:
采用铅箔增感屏,前后均为0.03mm。
4.3.1胶片和增感屏在透照过程中应始终贴紧。
4.3.2增感屏的表面应保持光滑清洁,无污染损伤,变形。
4.4观片灯
4.4.1观片灯的主要性能应符合JB/T7903的有关规定。
4.4.2观片灯的最大亮度应能满足评片的要求。
4.5黑度计(光学密度计)
4.5.1黑度计可测的最大黑度应不小于4.5,测量值的误差应不超过+0.05。
4.5.2黑度计至少每6个月校验一次。
校验方法可参照JB/T4730.2-2005附录B的规定进行,黑度片应每隔两年校验一次。
4.6像质计
4.6.1底片影像质量采用线型像质计测定。
线型像质计的型号和规格应符合JB/T7902的规定,JB/T7902中未包含的丝径、线号等内容,应符合HB7684的有关规定。
4.6.2像质计的材料、材料代号和不同材料的像质计适用的工件材料范围应符合JB/T4730.2-2005表2的规定。
5.检测表面制备
5.5.1检测表面制备见总则第5条的规定
6.检测时机
6.1检测时机见见总则第4条的规定
7.检测工艺和检测技术
7.1透照布置
7.1.1透照方式应根据工件特点和技术条件的要求选择适宜的透照方式。
在可以实施的情况下应选用单壁透照方式,在单壁透照不能实施时才允许采用双壁透照方式。
典型的透照方式见下图1
图1
7.1.2透照方向透照时射线束中心应垂直指向透照区中心,需要时也可选用有利于发现缺陷的方向透照。
7.1.3一次透照长度应以透照厚度比K进行控制。
不同级别射线检测技术和不同类型对接焊
接接头的透照厚度比应符合表1的规定
射线检测技术级别
A级、AB级
B级
纵向焊接接头
K≤1.03
K≤1.01
环向焊接接头
K≤1.11)
K≤1.01
1)对100mm<D0≤400的环向对接接头(包括曲率相同的曲面焊接接头),A级、AB级允许采用K≤1.2。
7.1.4小径管环向对接焊接接头的透照布置
小径管采用双壁双影透照布置,当同时满足下列两条件时应采用倾斜透照方式椭圆成像
a)T(壁厚)≤8mm
b)g(焊缝宽度)≤D。
/4。
椭圆成像时,应控制影像的开口宽度在1倍焊缝宽度左右。
不满足上述条件或椭圆成像有困难时可采用垂直透照方式重叠成像。
7.1.5小径管环向对接焊接接头的透照次数
小径管环向对接焊接接头100%检测的透照次数:
采用倾斜透照方式椭圆成像时,当T/D≤0.12时相隔90透照2次。
当T/D﹥0.12时相隔120或60透照3次。
垂直透照重叠成像时,一般应相隔120或60透照3次。
由于结构原因不能进行多次透照时,可采用椭圆成像或重叠成像方式透照一次。
鉴于透照一次不能实现焊缝全长的100%检测,此时应采取有效措施扩大缺陷可检出范围,并保证底片评定范围内黑度和灵敏度满足要求。
7.2射线能量
7.2.1X射线照相应尽量选用较低的管电压。
在采用较高管电压时,应保证适当的曝光量。
对截面厚度变化大的承压设备,在保证灵敏度要求的前提下,允许采用超过规定的X射线管电压。
但管电压增量不应超过50KV。
7.3射线源至工件表面的最小距离
7.3.1由于本公司产品射线检测技术等级为AB级,所选用的射线源至工件表面的距离
AB级射线检测技术:
ƒ≥10d·b2/3
7.3.2采用源在内中心透照方式周向曝光时,只要得到的底片质量符合7.11.2和7.11.3的要求,值可以减小,但减小值不应超过规定值的50℅.
7.3.3采用源在内单壁透照方式时,只要得到的底片质量符合7.11.2和7.11.3的要求,ƒ值可以减小,但减小值不应超过规定值的20℅.
7.4曝光量
7.4.1X射线照相,当焦距为700mm时,曝光量的推荐值为15mA·min:
当焦距改变时可按平方反比定律对曝光量的推荐值进行换算.
7.5曝光曲线
7.5.1对每台在用射线设备均应作出经常检测材料的曝光曲线,依据曝光曲线确定曝光参数.
7.5.2制作曝光曲线所采用的胶片.增感屏.焦距.射线能量等条件以及底片应达到的灵敏度.黑度等参数均应符合本部分的规定.
7.5.3对使用中的曝光曲线,每年至少应校验一次.射线设备更换重要部分或经较大修理后应及时对曝光曲线进行校验或重新制作.
7.6无用射线和散射线屏蔽
7.6.1本公司采用金属增感屏.铅板等适当措施,屏蔽散射线和无用射线,限制照射场范围.
7.6.2对初次制定的检测工艺,或使用中检测工艺的条件.环境发生改变时,应进行背散射防护检
查.检查背散射防护的方法是:
在暗盒背面贴附“B”铅字标记,一般铅字的高度为13mm、厚度为1.6mm,按检测工艺的规定进行透照和暗室处理.若在底片上出现黑度低于周围背景黑度的“B”字影像,则说明背散射防护不够,应增大背散射防护铅板的厚度.若底片上不出现“B”字影像或出现黑度高于周围背景黑度的“B”字影像,则说明背散射防护符合要求.
7.7像质计的使用
7.7.1像质计一般应放置在工件源侧表面焊接接头的一端(在被检区长度1/4左右位置),金属丝应横跨焊缝,细丝置于外侧.当一张胶片上同时透照多条焊接接头时,像质计应放置在透照区最边缘的焊缝处.
7.7.2像质计放置原则
a)单壁透照规定像质计放置在源侧.双壁单影透照规定像质计放置在胶片侧.双壁双影透照规定像质计可放置在源侧,也可放置在胶片侧.
b)单壁透照中,如果像质计无法放置在源侧,允许放置在胶片侧,
c)单壁透照中像质计放置在胶片侧时,应进行对比试验,对比试验方法时在射源侧和胶片侧各放一个像质计,用与工件相同的条件透照,测定出像质计放置在源侧和胶片侧的灵敏度差异,以此修正应识别像质计丝号,以保证实际透照的底片灵敏度符合要求.
d)当像质计放置在胶片侧时,应在像质计上适当位置放置铅字“F”作为标记,“F”标记的影像应与像质计的标记同时出现在底片上,且应在检测报告中注明.
7.7.3原则上每张底片上都应有像质计的影像.当一次曝光完成多张胶片照相时,使用的像质计数量允许减少但应符合以下要求:
a)环形对接焊接接头采用源置于中心周向曝光时,至少在圆周上等间隔地放置3个像质计.
b)一次曝光连续排列的多张胶片时,至少在第一张.中间一张和最后一张胶片处各放置一个像质计.
7.7.4小径管可选用通用线型像质计或附录F(规范性附录)规定的专用(等经金属丝)像质计,金
属丝应横跨焊缝放置。
7.7.5如底片黑度均匀部位(一般是邻近焊缝的母材金属区)能够清晰地看到长度不小于10mm的连续金属丝影像时,则认为该丝是可识别的。
专用像质计至少应能识别两根金属丝。
7.8标记
7.8.1透照部位的标记由识别标记和定位标记组成。
标记一般由适当尺寸的铅(或其他适宜的重金属)制数字.拼音字母和符合等构成。
7.8.2识别标记一般包括:
产品编号.对接焊接接头编号.部位编号和透照日期。
返修后的透照还应有返修标记,扩大检测比例的透照应有扩大检测标记。
具体标识方法见附录C。
7.8.3定位标记一般包括中心标记和搭接标记。
中心标记指示透照部位区段的中心位置和分段编号的方向,一般用十字箭头表示。
搭接标记是连续检测时的透照分段标记,可用符合“↑”或其他能显示搭接情况的方法表示。
7.8.4标记一般应放置在距焊缝边缘至少5mm以外的部位,所有标记的影像不应重叠,且不应干扰有效评定范围内的影像。
7.9胶片处理
7.9.1本公司采用手工冲洗方式处理。
7.9.2胶片处理一般应按使用说明书的规定进行。
7.10评片要求
7.10.1评片一般应在专用的评片室内进行。
评片室应整洁、安静、温度适宜,光线应暗且柔和。
7.10.2评片人员在评片前应经历一定的暗适应时间.从阳光下进入评片的暗适应时一般为5min~10min;从一般的室内进入评片的暗适应时间应不少于30s。
7.10.3评片时,底片评定范围内的亮度应符合下列规定:
a)当底片评定范围内的黑度D≤2.5时,透过底片评定范围内的亮度应不低于30cd/m2.
b)当底片评定范围内的黑度D>2.5时,透过底片评定范围内的亮度应不低于10cd/m2。
7.10.4底片评定范围的宽度一般为焊缝本身及焊缝两侧5mm宽的区域。
7.11底片质量
7.11.1底片上,定位和识别标记影像应显示完整、位置正确。
7.11.2底片评定范围内的黑度D应符合下列规定:
AB级:
2.0≤D≤4.0;
用X射线透照小径管或其他截面厚度变化大的工件时,AB级最低黑度允许降至1.5;
7.11.3底片的像质计灵敏度
单壁透照、像质计置于源侧时应符合JB/T4730.2-2005表5的规定;双壁双影透照、像质计置于源侧时应符合表6的规定;双壁单影或双壁双影透照、像质计置于胶片侧时应符合JB/T4730.2-2005表7的规定。
7.11.4底片评定范围内不应存在干扰缺陷影象识别的水迹、划痕、斑纹等伪缺陷影像。
8.钢制承压设备熔化焊对接焊接接头射线检测质量分级
8.1范围:
本条适用于厚度为2mm-50mm的碳素钢、低合金钢、奥氏体不锈钢制承压设备熔
化焊对接焊接接头射线检测质量分级。
8.2缺陷类型
对接焊接接头中的缺陷按性质可分为裂纹、未熔合、未焊透、条形缺陷和圆形缺陷共五类。
8.3质量分级依据
根据对接接头中存在的缺陷性质、数量和密集程度可分为Ⅰ、Ⅱ、Ⅲ、Ⅳ级。
8.4质量分级的规定
钢制承压设备熔化焊对接焊接接头射线检测质量分级应见底片评片工艺(附录D)
9.检测报告
9.1检测过程中应做好原始记录,包括日期、编号、检测位置、工件名称、规格尺寸、透照方式及参数并绘出位置简图。
9.2底片评定合格后,出具检测报告,检测报告和底片至少要保存七年。
第四章超声检测工艺规程
1.主题内容与适用范围
1.1本规程规定了超声检测人员资格、仪器、探头、试块、检测范围、方法和质量分级等。
1.2本规程采用A型脉冲反射式超声波探伤仪对金属材料制承压设备用原材料.零部件和焊接接头进行检测。
2.引用标准和规程
2.1《压力容器安全技术监察规程》
2.2GB150-98《钢制压力容器》
2.3JB/T4730.1-4730.6-2005《承压设备无损检测》
2.4JB/T7913-1995超声波检测用钢制对比试块的制作与校验方法
2.5JB/T9214-1999A型脉冲反射式超声探伤系统工作性能,测试方法
2.6JB/T10061-1999A型脉冲反射式超声波探伤仪通用技术条件
2.7JB/T10062-1999超声探伤用探头性能测试方法
2.8JB/T10063-1999超声探伤用1号标准试块技术条件
3.检测人员应符合本《规程》中总则的有关规定
4.检测设备
本公司现使用的是汕头超声仪器厂生产的CTS-22A和CTS-26A两台设备。
4.1探伤仪采用A型脉冲反射式超声波探伤仪。
其工作频率范围为0.5MHZ-10MHZ,仪器至少在荧光屏满刻度的80℅范围内呈线性显示。
探伤仪应具备有80dB以上的连续可调衰减器,步进级每档不大于2dB,任意相邻12dB误差在±1dB以内,最大累计误差不超过1dB。
水平线性误差不大于1%,垂直线性误差不大于5℅其余指标应符合JB/T10061的规定。
4.2探头
(1)晶片有效面积除另有规定外一般不应超过500mm2,且任意一边不大25mm.
(2)单斜探头声束轴线水平偏离不应大于2。
,主声束垂直主方向不应有明显的双峰。
4.3超声探伤仪和探头的系统性能
4.3.1在达到所探工件的最大检测声程时,其有效灵敏度余量应不小于10dB。
4.3.2仪器和探头的组合频率与公称频率误差不得大于±10%。
4.3.3仪器和直探头组合的始脉冲宽度(在基准灵敏度下):
对于频率为5MHZ的探头,宽度不大于10mm;对于频率为2.5MHZ的探头,宽度不大于15mm。
4.3.4直探头的远场分辨力应大于或等于30dB,斜探头的远场分辨力应大于或等于6dB。
4.3.5仪器和探头的系统性能应按JB/T9214和JB/T10062的规定进行测试。
4.4试块
4.4.1标准试块应采用与被检工件相同或近似声学性能的材料制成,该材料用直探头检测时,不得有大于φ2mm平底孔当量直径的缺陷。
4.4.2标准试块尺寸精度应符合JB/T4730.3-2005的要求,且其他制造要求应符合JB/T10063和JB/T7913的规定。
4.4.3现场检测时,允许采用其它形式的等校对比试块,其反射体的形状、尺寸和数量应符合JB/T4730.