试模DOE程序含表格.docx
《试模DOE程序含表格.docx》由会员分享,可在线阅读,更多相关《试模DOE程序含表格.docx(12页珍藏版)》请在冰点文库上搜索。
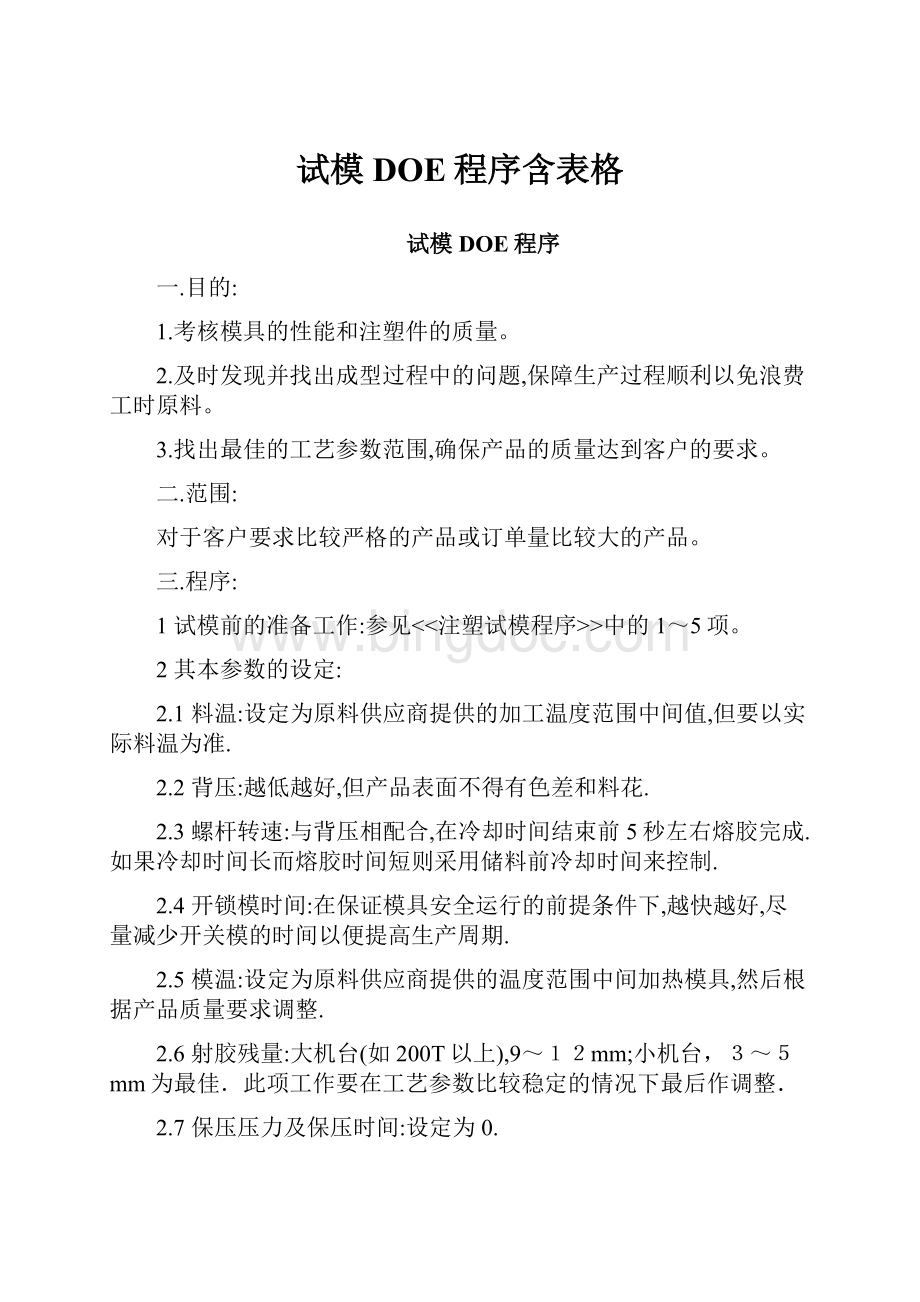
试模DOE程序含表格
试模DOE程序
一.目的:
1.考核模具的性能和注塑件的质量。
2.及时发现并找出成型过程中的问题,保障生产过程顺利以免浪费工时原料。
3.找出最佳的工艺参数范围,确保产品的质量达到客户的要求。
二.范围:
对于客户要求比较严格的产品或订单量比较大的产品。
三.程序:
1试模前的准备工作:
参见<<注塑试模程序>>中的1~5项。
2其本参数的设定:
2.1料温:
设定为原料供应商提供的加工温度范围中间值,但要以实际料温为准.
2.2背压:
越低越好,但产品表面不得有色差和料花.
2.3螺杆转速:
与背压相配合,在冷却时间结束前5秒左右熔胶完成.如果冷却时间长而熔胶时间短则采用储料前冷却时间来控制.
2.4开锁模时间:
在保证模具安全运行的前提条件下,越快越好,尽量减少开关模的时间以便提高生产周期.
2.5模温:
设定为原料供应商提供的温度范围中间加热模具,然后根据产品质量要求调整.
2.6射胶残量:
大机台(如200T以上),9~12mm;小机台,3~5mm为最佳.此项工作要在工艺参数比较稳定的情况下最后作调整.
2.7保压压力及保压时间:
设定为0.
2.8模具:
对模具的前期准备工作要求比较高,所有与模具有关的外观缺陷如顶高顶白拉模粘模走胶不平衡等问题解决以后再进行下一步程序.
注:
以上基本参数的设定要以调校经验比较丰富的技师为基础.调校的目的是保证工艺参数的稳定性.
3最佳注射时间:
3.1注塑压力——注射时,在螺杆头部(计量室)建立的熔体压强。
为了确保注塑机的注塑速度达到及保持所要求的数值,注塑压力数值的设定必须足够。
注射压力是重要生产参数之一,它决定着螺杆的前进和后来模具填充的情况,假如注射压力太低,熔料进入模具时所产生的阻力便相对的很大,使注射速度不能保持在设定的水平,结果是射胶时间长了,所以设定注塑压力时某数值应较熔料所产生的阻力高15bar左右。
例:
注塑一件产品,设定50%注塑速度,在注塑压力为140bar.,注射时间为0.87秒内完成成型过程,请问最佳注射压力数值是多少?
注塑速度
注射压力
注射时间
50%
140bar
0.87sec
50%
120bar
0.87sec
50%
100bar
0.89sec
最佳
50%
90bar
0.90sec
下限
50%
85bar
0.99sec
注:
1)在最佳的注射压力设定情况下,注射周期时间的变化应不超过0.06秒,如超过这个范围,表示压力不稳或塑化不良。
2)理论上,注射时最好多找几个组合,选择一个最佳值,不要一次用较大的注塑压力成型特别是一模多腔产品,当因某种原因而塞住未注塑的话,每个型腔压力相对陡增,是对模具和机器相应会有不同程度的损伤。
3.2注射速率——单位时间内注入模腔中熔体的容积。
注射速度是重要注射参数之一,对许多工艺因素起影响,随速率的提高,充模压力提高,可以维持熔体有较高的温度,流体的粘度低,流道阻力损失小;相反,过高的充填速度会增加压力损失,造成熔体不稳定流动发生弹性湍流或熔体速度头的冲击,造成胀模飞边现象。
总的来说,注射速度必须保证流变数据中对指定材料所允许的剪切速率和最短流动长度,必须保证由剪切而产生的热效应和剪切效应不超过聚合物物理性质和剪切强度所允许的程度。
例:
注塑一件成品,先试用50%速度,稍高一点的注塑压力,尝试做一个图表(不需要任何保压压力及保压时间)
注射速度
注射时间
注射压力
产品质量
20%
1.3sec
75bar
缺料,缩水
30%
1.06sec
85bar
不稳定,有水波纹,流纹
40%
0.92sec
92bar
GOOD
50%
0.87sec
100bar
GOOD
60%
0.83sec
110bar
GOOD
70%(下限)
0.80sec
118bar
GOOD
80%
0.77sec
125bar
毛刺,披锋
从上表可以看得出,不同的注射速度可得出不同得注塑参数,可容易找出注射速度的上/下限值,聚合物材料和金属等其他材料相比,最大特征是力学性能强烈地依赖于温度和力的作用时间,根据高聚物流变学理论,加工过程的影响因素为:
应力、形变、形变速率与粘度之间的关系以及影响这些关系的要素,如温度、压力、时间及分子结构,分子量大小。
剪切应力随剪切速率提高按指数定律增加,而粘度却随剪切速率或剪应力的增加按指数方程下降,生产实践表明,不同加工方法有不同的剪切速率范围,在验证设定的注塑压力,注塑速度对塑料粘度的影响,可依据以下数据计算。
注塑速度(%)
剪切率(1/sec)
相对粘度(barsec)
10
0.28
3188
20
0.55
1680
30
0.85
1161
40
1.11
950
50
1.37
806
60
1.61
715
70
1.89
656
80
2.08
638
90
2.33
590
100
2.50
562
注:
相对粘度=注射压力*剪切率;剪切率=注射时间的倒数.
3.3工艺调整步骤:
3.3.1利用Hi~Hi;Hi~Low;Low~Low;Low~Hi原则找出最初的工艺条件范围:
Hi~Hi:
从最大的压力和最快的速度开始往下调整,直到产品外观OK.
Hi~Low:
从最大的压力和最慢的速度开始往上调整,直到产品外观OK.
Low~Low:
从最小的压力和最慢的速度开始往上调整,直到产品外观OK.
Low~Hi:
从最小的压力和最快的速度开始往下调整,直到产品外观OK.
从以上步骤中找出速度和压力范围.
3.3.2找最佳工艺条件范围:
3.3.2.1利用3.3.1中的速度和压力范围,按3.2程序步骤从低压低速往高速高压调校,记录此时的速度和压力.
注:
压力是以注塑机的表压,而不是设定的压力.
3.3.2.2按3.2程序计算相对粘度并制作图表,从中找出最佳的注射时间及最佳的粘度.
4找出最佳的保压时间及保压力:
4.1保压时间:
无论采用何种模式的转压方式,正确设定转压点是至为重要的,如要获得最佳的生产状态必须确保转压前已有95~98%的射胶量被注入模腔。
若过早转压(模腔的熔料少过95%的射胶量)则需要利用保压压力把较多的熔料推进模腔,很容易产生披锋和填充不满的成品,同时成品品质的稳定程度亦较差,相反地,若是转压太迟(模腔地熔料已过多98%的射胶量)成品便会被压缩过大,形成很多部位有披锋和内应力过高,甚至脱模困难。
(1)切换点的控制,注射油压准确地切换到保压油压,需有一个缓冲过程,即有注射油压之前应将速度减慢,减小惯性,控制每次复位的精度。
(2)有足够时间切换保压及排走模腔内气体。
正确设定保压时间可以获得最佳效果的成品,所以设定保压数值和时间是注塑参数决定的重要项目,步骤如下:
1)首先把注塑的保压时间设为0;
2)然后把保压时间设为0.5秒,并连续成型4-5模;
3)度量产品的重量并计算出平均值;
4)每次把保压时间增加0.5秒,并重复以上的过程直至产品的平均重量已经没有变化。
例:
保压时间(秒)产品重量(克)
从下表可知在保压为3.5秒时,重量已稳定下来。
HoldTime(sec)
PartWeight(g)
4.0
7.52
3.5
7.52
3.0
7.51
2.5
7.46
2.0
7.42
1.5
7.38
1.0
7.32
0.5
7.03
0.0
6.74
4.2保压压力的设定
保压压力对制品密度有很大影响,在保压阶段,制品重量随保压时间加长而逐步上升,但达到一定时间后重量不再增加,模腔压力近于等速下降,当保压压力切除后,模内压力迅速度地下降,但保压压力太大,将会使产品内应力增大,一般来说,保压压力为注射压力的20-70%。
例:
保压压力(bar)
产品重量(g)
10
35
20
36
30
37.5
40
38.2
50
38.4
60
38.45
70
38.5
80
38.5
90
38.5
4.3保压压力和保压时间的最佳设定
(2)
根据不同的保压时间和保压压力的最佳组合设定。
保压时间
重量
保压压力
30
35
40
45
50
1.0
12.82
12.87
12.92
12.94
13.02
1.5
12.87
12.90
12.94
12.98
13.06
2.0
12.92
12.94
12.98
13.02
13.08
2.5
12.96
12.98
13.02
13.06
13.12
3.0
13.02
13.06
13.12
13.16
13.20
通过以上得出每次的重量值,找出最佳组合(至少20模取样数据)
5找出最佳的冷却时间
注塑循环冷却是为了保证模具内熔化的塑料充分地固化,注塑件便不会在顶出时变形。
影响冷却时间的两个因素:
1)被加工的热塑性塑料的固化时间。
2)模具内冷却管道的设计。
冷却时间
产品温度
产品尺寸
产品质量
16sec
54℃
/
OK
14sec
54℃
/
OK
12sec
55℃
/
OK
10sec
59℃
/
OK
9sec
65℃
/
OK
8sec
72℃
/
OK
由上表可以得知,冷却12sec为最佳化选择。
*1.模具进出水温度应在<3℃左右。
2.冷却时间越短,产品出模后表面温度越高。
6找出最佳的锁模力
6.1首先把注塑机的锁模力数值调至最高,然后进行正常的全自动或半自动生产。
6.2分别量度三次模件的毛重,并计算毛重的平均值。
6.3把锁模力数值降低5吨,待生产情况稳定下来,重复第2程序,找出毛重的平均值。
6.4再把锁模力数值调底5吨,并重复第2程序。
6.5重复第4程序直至毛重的平均值显著地增加。
6.6把获得的数据以下列表式的方式列出。
锁模力(吨)
一模毛重(克)
100
96
95
96
90
96
85
96
80
96
75
96
70
96
65
96
60
95.8
55
95.5
50
96
45
97
40
99
35
102.87
根据以上综合的调校分析,可定出模具/注塑机/原料三者组合的最佳参数。
上限
中心值
下限
料温℃
注塑压力bar
注射速度%
保压压力bar
保压时间sec
冷却时间sec
锁模力Ton
7.试模文件及记录要求:
7.1.试模通知:
《转模转色生产通知单》是提醒试模组及相关人员做好相应的准备工作以便能够合理的安排试模工作,其中内容包括要求试模部门、模具编号、塑件编码、试模日期、试模用料、试模样板数量、试模类别、试模成本、试模状况、模具资料等信息。
7.2.试模报告:
试模完成后,需由试模组出具试模报告,《塑胶模情况报告表》反映试模过程中出现的各种情况,包括模具注塑情况和塑件缺陷情况,并注明试模单号、模具编号、塑件名称、试模原因、试模次数、试模日期、塑件批号、试模机器等详细信息。
试模报告要以工程报告的形式记录,且每一次的工艺条件都要按上面的步骤进行,最后找出一个最佳的成型工艺条件范围.
7.3工艺条件记录:
试模过程中所有的工艺条件/产品重量全部记录,并将找出的最佳工艺条件范围记录作为以后生产的标准成型条件.
7.4样品保存:
每找出一种工艺条件都要将样品保存,作为以后正式生产的参考.
四.相关程序及表格:
4.1《注塑试模程序》
4.2《转模转色生产通知单》
4.3《塑胶模情况报告表》
4.4《模具DOE测试表》