料斗拼装施工工法Word下载.docx
《料斗拼装施工工法Word下载.docx》由会员分享,可在线阅读,更多相关《料斗拼装施工工法Word下载.docx(22页珍藏版)》请在冰点文库上搜索。
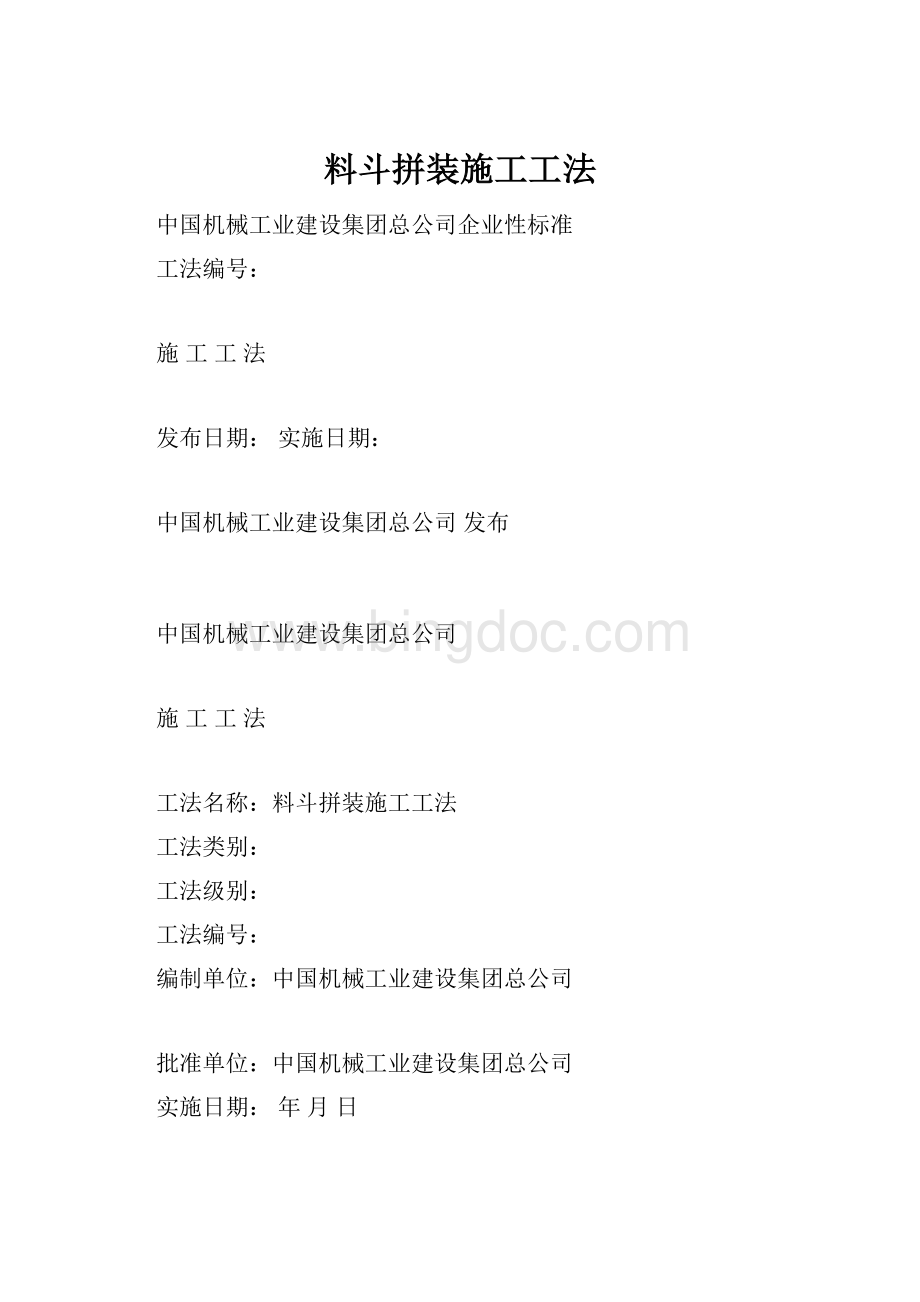
放样时考虑焊接收缩余量以及加工边预留加工余量。
采用数控切割加工时可不进行放样。
构件中的零部件采取100%的套料方式。
4.3放样检查
放样结束,应对照施工详图或加工图对放样样板进行检查。
五、下料
5.1下料设备
材料种类
切割加工设备
钢板
数控火焰切割机、半自动火焰切割机
角钢、方管、
热轧H型钢、圆钢
法因锯床、半自动火焰切割机
数控切割机法因锯床
5.2准备工作
⑴查看下料清单上的材质、规格、数量等,核对材料材质与规格与下料清单是否相符。
材料代用必须严格履行材料代用手续。
⑵查看钢材表面上的质量,如有不平、扭曲、波浪变形、弯曲等缺陷,在下料前应对钢材进行矫正。
5.3钢板切割工艺
⑴将钢板吊至切割平台上,在自动切割时,调整钢板单边两端头与导轨的距离相差在5mm的范围内。
在进行半自动切割时,应将导轨放在被切割钢板的平面上,然后将切割机轻放在导轨上。
使有割炬的一侧面向操纵者,根据钢板的厚度选用割嘴,调整切割直度和切割速度。
⑵根据自动切割及半自动切割方式的不同,调整各把割枪的距离,确定后拖量,并考虑割缝补偿;
在切割过程中,割枪倾角的大小和方向主要以钢板厚度而定,割嘴倾角与割件厚度的关系及切割余量如下表所示:
割嘴倾角与割件厚度的关系
割件厚度
<10
≥10
倾角方向
后倾
垂直
倾角度数
10°
~15°
0°
钢板切割余量表
(单位:
mm)
切割方式
材料厚度
割缝宽度留量
备注
气割下料
≤10
1~2
10~20
2.5
20~40
3.0
40以上
4.0
在进行厚板气割时,割嘴与工件表面保持垂直,待整个断面割穿后移动割嘴,转入正常气割,气割将要到达终点时应略放慢速度,使切口下部完全割断。
⑶根据板厚调整切割参数,切割参数包括割嘴型号、氧气压力、切割速度和预热火焰的能量等,工艺参数的选择主要根据气割机械的类型和可切割的钢板厚度,对未割过的钢板,应试割同类钢板,确定切割参数,同时检查割嘴气通畅性。
如下根据工厂实际设备设施情况而定的工艺参数:
气割参数
割嘴
编号
切割厚度
(mm)
氧气压力
(MPa)
天然气压力(MPa)
切割速度
(mm/min)
2
12-30
0.6-0.7
0.05-0.06
500-600
3
30-40
0.06-0.08
400-500
4
40-100
0.08-0.10
350-550
⑷气割前去除钢材表面的污垢,油脂,并在下面留出一定的空间,以利于熔渣的吹出。
气割时,割炬的移动应保持匀速,割件表面距离焰心尖端以2~5mm为宜,距离太近会使切口边沿熔化,太远热量不足,易使切割中断。
⑸在进行厚板切割时,预热火焰要大,气割气流长度超出工件厚度的1/3。
割嘴与工件表面约成10°
~20°
倾角,使零件边缘均匀受热。
⑹为了防止气割变形,操作过程中应注意以下几个方面:
⑺在钢板上切割不同尺寸的工件时,应先切割小件,后割大件;
⑻窄长条形板的切割,长度两端留出50mm不割,待割完长边后在割断,或者采用多割炬的对称切割的方法。
⑼直条切割时应注意各个切割割嘴的火焰强弱应一致,否则易产生旁弯。
5.4数控切割质量控制
⑴切割过程中,应随时注意观察影响切割质量的因素,保证切割的连续性。
⑵工艺参数对气割的质量影响很大,常见的气割断面缺陷与工艺参数的关系如下所示:
气割表面缺陷和原因分析
缺陷类型
产生原因
图示说明
切割面粗糙
a.切割氧压力过高
b.割嘴选用不当
c.切割速度太快
d.预热火焰能量过大
切割面缺口
a.切割过程中断,重新起割衔接不好
b.钢板表面有厚的氧化皮、铁锈等
c.切割机行走不平稳
切割面内凹
b.切割速度过快
切割面倾斜
a.割炬与板面不垂直
b.风线歪斜
c.切割氧压力低或嘴号偏小
切割面上缘呈珠链状
a.钢板表面有氧化皮、铁锈
b.割嘴到钢板的距离太小,火焰太强
切割面上缘熔化
a.预热火焰太强
b.切割速度太慢
c.割嘴离板件太近
切割面下缘粘渣
a.切割速度太快或太慢
b.割嘴号太小
c.切割氧压力太低
5.5切割件检验指标
⑴气割完毕后,应对钢材切割面进行检查,其切割面应无裂纹、夹渣和大于1mm的缺棱,检查方式为外观检查。
⑵气割完毕后,应在切割件上注明工程名称、零件编号。
⑶切割后零件的外观质量应作为常规项目进行检查,如切割后零件的外形尺寸、断面光洁度、槽沟、断口垂直度、坡口角度、钝边高度、局部缺口、毛刺和残留氧化物;
气割后零件的允许偏差如下表所示:
气割的允许偏差
(单位:
项目
允许偏差
备注
零件宽度,长度
±
2.0
手工、半自动
1.0
数控切割
切割面平面度
0.05T,且不大于1.5
割纹深度
0.2
局部缺口深度
与板面垂直度
不大于0.025T
条料旁弯
不大于3
坡口角度
2.5°
钝边
⑷无论是利用数控切割进行主材下料或利用半自动切割进行小件加工、坡口加工,切割断面上深度超过1mm的局部缺口、深度大于0.2mm的割纹以及断面残留的毛刺和熔渣,均应给予焊补和打磨光顺。
⑸主材切割完毕后,应进行标识,内容包括:
工程名称、构件编号、构件规格、构件材质及所属钢板的炉批号。
六、焊接工艺
6.1基本要求
6.1.1焊接坡口形式及焊接要求:
焊接坡口形式及焊接要求应符合设计及图纸要求的相关条款要求。
6.1.2焊接质量:
焊接的质量应符合《钢结构工程施工质量验收规范》(GB50205-2001)及《建筑钢结构焊接技术规程》(JGJ81-2002)、《结构钢焊接标准》(AS/NZS1554.1:
2004)
的要求。
6.2焊工
从事焊接施工的焊工根据其从事的焊接方法,应该具备《建筑钢结构焊接技术规程》(JGJ81-2002)或者《锅炉压力容器压力管道焊工考试与管理规则标准》或者《焊工技术考核规程》(DL/T679-1999)等标准相应资格的人员。
焊接方法
资格
熔化极气体保护焊GMAW
GMAW
6.3焊接设备
焊接机械及其附属设备、工具、个人保护用具的种类、性能均应满足焊接方法和作业安全的要求。
6.4焊接材料的管理
6.4.1焊接材料在入库前前必须根据制造厂提供的质量证明书进行验收,并检查包装无破损、受潮或雨淋等现象,才能作为合格品入库。
6.4.2焊接材料必须保存在通风良好和干燥的室内仓库中,焊丝均应放置在离墙面和地面距离不小于300mm的架子上。
6.5焊接施工
6.5.1焊接前焊接区域的清理及装配质量的检查:
焊接前应清理焊接区域内的水分、油污、氧化皮等影响焊接质量的物质,并打磨露出良好金属光泽。
6.5.2焊接顺序以及焊接位置:
焊接时应合理调整工件位置,尽量采用平焊或横焊位置焊接。
焊接应按使构件产生焊接变形和焊接残余应力最小的次序焊接。
焊接过程中应注意检查变形情况,并根据变形情况调整焊接顺序。
焊接顺序把控的原则是:
多层多道,对称焊接。
6.5.3层间温度控制:
⑴应用范围:
层间温度控制在多层多道焊接过程中实施(平焊、横焊)。
⑵层间温度范围:
层间温度应控制在250℃以内,但不得低于最低预热温度,一般控制在100℃至250℃。
⑶层间温度控制方法:
上一层焊接完工后,使用熔点为246℃控温粉笔在测温点标记,如标记未熔化则可继续施焊,如标记熔化则必须等焊道冷却后方允许进行下一层施焊;
或采用红外测温仪进行层间温度控制。
-50~750℃
常用层间温度测量仪器
⑷记录:
焊工通过在焊缝测温点用测温笔(或红外测温仪)标识并应在焊接施工记录上进行记录。
⑸检查:
质检人员负责对层间温度控制实施过程进行检查,采用控温粉笔或其它测温工具复测层间温度。
并检查焊接施工记录与实际相符度。
6.5.4预热:
构件定位焊接与正式焊接前,应对厚板(﹥25mm)进行焊前预热:
⑴采用火焰或电加热预热;
⑵预热范围应在坡口两侧,宽度应为焊件施焊处厚度的1.5倍以上,且不小于100mm;
⑶最低预热温度参照下表
钢板厚度
﹤25
25≤t≤40
40﹤t≤60
60﹤t≤80
t﹥80
预热温度
Q235
/
60℃
80℃
100℃
Q345
140℃
备注:
“/”表示不需预热;
钢板厚度单位为mm。
6.5.5焊接工艺参数:
焊接时应根据焊接工艺评定确认的焊接方法、焊接材料以及焊接位置选择相应的焊接参数。
6.5.6焊接操作:
⑴焊接时应避免在焊道以外的母材上引弧、熄弧,防止损伤母材。
在焊道中引熄弧时,引熄弧位置应错开25mm以上。
引弧应采用回焊手法,熄弧应填满弧坑。
⑵焊接时应满足焊接要求中规定的焊缝尺寸要求,焊接时应采用多层多道焊接,严禁宽幅摆动焊接,最大摆动幅度不得大于25mm;
典型多层多道焊接的焊缝
⑶盖面焊接时应充分填满弧坑、焊道(包括引、熄弧板部位)。
6.5.7焊接中的清理:
⑴焊接中的电弧终止处的焊坑,在重新起弧前清除焊渣等并确认焊缝无焊接缺陷。
⑵进行多层焊接时,须清除前一道焊缝的焊渣以及焊道内的飞溅、杂物后才能实施下道焊接。
并用捶击的方式减小焊接应力。
⑶直线焊接时应注意保持焊接速度均匀,避免焊缝凹凸不平的发生。
6.5.8反面清根:
反面清根用碳弧气刨实施,碳刨深度要达到露出正面焊道良好的熔敷金属,清根深度尽可能和宽度相近。
气刨清根后应清理熔渣并用砂轮打磨修整坡口符合施焊要求。
6.5.9焊接端部的处理和引弧板、引出板:
T型接头、角接接头和对接接头主焊缝的两端应设置引弧板和引出板,引弧板和引出板的材质应与母材一致,坡口形式与被焊焊缝相同。
引弧板和引出板的规格:
厚度不应小于6mm,长度不小于50mm,引出长度不小于25mm。
规范加设引弧板
加劲板,节点板等角焊缝T型接头当端部采用包角焊法时可以不设置引弧板和引出板。
6.5.10焊后清理:
⑴焊接完成后,焊接部分的焊渣用铲刀或凿子清除,周边的飞溅用铲刀或打磨清除,高强度螺栓摩擦面和需油漆的表面的飞溅要彻底清理干净。
⑵焊接完成后,引熄弧板须用气割将其割除。
割除时要注意不要伤及母材,应在偏离母材端面3mm至5mm的地方切割。
切割采用手工火焰切割实施,并用砂轮修磨平整。
不得用锤击落引弧板和引出板。
6.6焊接检查
6.6.1外观质量要求:
焊缝外观一般采用目测,裂纹的检测应铺以5倍的放大镜并在合适的光照条件下进行,必要时可采用磁粉进行探伤检查。
对接焊缝及完全熔透组合焊缝尺寸允许偏差(mm)
项目
图例
一、二级
三级
对接焊缝余高C
B<20:
0~3.0
B≥20:
0~4.0
0~5.0
对接焊缝错边d
d<0.15t,
且≤2.0
且≤3.0
部分焊透组合焊缝和角焊缝外形尺寸允许偏差(mm)
焊脚
尺寸hf
hf≤6:
0~1.5
hf>6:
角焊缝余高C
注:
1hf>8.0mm的角焊缝其局部焊脚尺寸允许低于设计要求值1.0mm,但总长不得超过焊缝长度10%。
二级、三级焊缝外观质量标准(mm)
检验方法
二级
未焊满(指不满足设计要求)
≤0.2+0.02t,且≤1.0
≤0.2+0.04t,且≤2.0
每100mm焊缝内缺陷总长≤25.0
根部收缩
长度不限
咬边
≤0.05t,且≤0.5;
连续长度≤100.0,且焊缝两侧咬边总长≤10%焊缝全长
≤0.1t,且≤1.0,长度不限
弧坑裂纹
不允许
允许存在个别长度≤5.0的弧坑裂纹
电弧擦伤
允许存在个别电弧擦伤
接头不良
缺口深度0.05t,且≤0.5
缺口深度0.1t,且≤1.0
每1000.0焊缝不应超过1处
表面夹渣
深≤0.2t,长≤0.5t且≤20.0
表面气孔
每50.0焊缝长度内允许直径≤0.4t,且≤3.0的气孔2个,孔距≥6倍孔径
表内t为连接处较薄的板厚。
所有等级焊缝表面不得有裂纹、焊瘤等缺陷。
一、二级焊缝不得有有表面气孔、夹渣、弧坑裂纹、电弧擦伤等缺陷,且一级焊缝不得有咬边、未焊满、根部收缩等缺陷。
6.6.2焊缝内部质量检查:
6.6.2.1无损检测应在外观检测合格后进行。
6.6.2.2对于全熔透焊缝,按照《建筑钢结构焊接技术》(JGJ81-2002)中7.3.3条执行。
一级焊缝应进行100%UT检测,内部缺陷评定等级不低于《钢焊缝手工超声波探伤方法和探伤结果的分级》(GB11345-89)标准规定的BⅡ级。
焊缝UT检测
二级焊缝应进行抽查,抽检比例应不小于20%,内部缺陷评定等级不低于《钢焊缝手工超声波探伤方法和探伤结果的分级》(GB11345-89)标准规定的BⅢ级。
6.7焊接缺陷的返修
⑴焊接缺陷的修补要领:
产生焊接缺陷时,根据缺陷种类采用下列方法实施修补:
缺陷种类
修补要领
裂纹
针对裂纹,采用正确的检查方法(超声波探伤,渗透探伤等)确认其长度、位置,在裂纹两端钻止裂孔(距裂纹端部50mm处),再用碳弧气刨清除裂纹(包括其两端延长50mm的范围),并检查(渗透探伤)确认裂纹清除干净后再实施焊补。
并分析裂纹产生的原因,制定预防措施。
未熔合
夹渣
气孔
在发现缺陷的部位及其两端各20mm的范围内用碳弧气刨清除后再进行焊补。
咬边
深度不超过0.05t且在1mm以下:
用砂轮打磨修整。
深度超过0.05t且超过1mm以上:
用砂轮打磨或碳弧气刨清除,然后进行焊补。
余高过大
弧坑
焊接缝不整齐
打磨修整或用碳弧气刨清除后进行焊补。
未焊满
补焊至所要求的焊接质量。
⑵其他要求:
①外观的缺陷的修补,用FCAW(焊丝直径φ1.2mm)进行修补焊接。
②裂纹等内在缺陷的修补,应在原预热温度的基础上进行100℃以上的预热,且不低于正式焊接的预热标准温度以上的条件下进行。
③修补焊接前将待焊接区域清理干净符合施焊要求。
⑶报告:
发生重大的焊接缺陷时,须向监理工程师报告,并与监理工程师协商后返修,并应制定修补方案和防止类似缺陷再发生的措施。
6.8控制焊接变形及焊接残余应力的工艺措施
6.8.1对焊接坡口,参照国家标准《气焊、焊条电弧焊、气体保护焊和高能束焊的推荐坡口》GB/T985.1-2008,根据接头板厚、焊接方法、接头型式、施工经验,选择经济合理、容易保证焊接质量和有益于控制焊接收缩变形的坡口形式,通过工艺评定掌握预留和控制,控制焊接变形和收缩应力。
6.8.2坡口加工和装配时,控制坡口加工精度和装配间隙,使坡口大小和填充量一致;
组装时调平装配平台,使用必要的装配和焊接胎架、工装夹具、工艺支撑,将变形削减并调整至单一方向,同时根据预定的焊缝截面及母材的规格,预置焊接收缩余量,控制焊接变形。
6.8.3在同一构件上焊接时,应尽可能采用热量分散、对称分布的方式施焊;
先焊会有明显收缩的接头,后焊会有较小收缩的接头,应在尽可能小的拘束下焊接;
对于接点复杂的构件,尽可能采用分块制作、整体拼装和焊接的方法进行制作,以减少和降低焊接变形与焊接应力。
6.8.4严格执行工艺要求的预热工艺要求、焊接工艺要求、焊接顺序要求等。
七、料斗整体试装
7.1预拼装目的
⑴本着保证现场能够顺利地进行整机安装,在构件制作完毕后特进行工厂预拼装;
⑵通过对构件的预拼装,可以更好的掌握构件的制作精度,并及时对超标构件进行修整处理,同时分析偏差的产生原因,以便在后续构件的加工过程中进行有效的预防与控制;
⑶通过对预拼装结果的记录、传递,从而确保现场能够顺利进行拼装,并有力保障工程的顺利实施。
7.2预拼装原理
根据合同内容要求,结合本工程的构件的结构特点,现按照设计蓝图尺寸进行构件立面预拼。
根据绘制好的框架地样线,结合构件的实际结构情况,进行预拼装胎架的搭设。
胎架搭设完毕,按一定顺序在胎架上相应的放置实际构件。
构件放置完毕,对应地样线进行调整对位,以保证现场能够顺利地进行安装。
7.3拼装准备
在料斗项目中,为检验制作的精度,验证制作工艺和验收方案,以便及时调整、消除误差,并确保构件现场顺利安装,减少现场特别是高空安装过程中对构件的安装调整时间,保障工程的顺利实施,工厂将对构件进行工厂预拼装。
⑴.核对各待预拼装构件号,验证构件的制作精度,发现问题及时修整。
⑵预拼装主要工器具要求见下表所示:
序号
设备名称
数量
1
25吨行车或者
25吨汽车吊
1台
构件吊装
CO2焊机
焊接
经纬仪
测量定位
水准仪
5
线锤
6
20m钢尺
7
5m钢尺
8
直尺
9
全站仪
10
焊接检验尺
测量坡口、间隙
11
千斤顶
构件位置微调
12
角磨机
外观处理
13
手动扳手
螺栓预紧
14
花篮螺丝
30
构件微调
(3)人员及分工要求:
人员类别
人数
拼装工
焊工
辅助工
技术人员
(4)预拼装的场地情况:
制作构件场地分为两部分,一部分为预拼装场地,另一部分为构件堆放场,堆放的所有构件下部需垫置枕木。
(5)胎架设计
结合结构的实际情况,采用槽钢制作一个简易水平胎架即可,高度约300mm。
7.4预拼工艺流程
7.4.1拼装工艺流程:
根据构件的结构特点及实际加工情况,确定如下所示的工艺流程:
地样线的绘制
搭设胎架
地样线的检查
地样线调整
构件按序就位
尺寸检查校核
构件修整
片体拆分下胎
胎架检查、验收
NO
OK
7.4.2预拼装的实施:
根据预拼装的原理及预拼装工艺流程,确定预拼装按以下步骤进行实施。
⑴地样线的绘制
根据设计蓝图,绘制总框架地样线,地样线如下图所示。
完成上道工序后,将各控制点的X、Y坐标在地样上标识出来,并用油漆在地上画出,并以文字形式进行说明,以方便质检及验收。
⑵胎架搭设
根据地样线,采用槽钢搭设一个简易的水平胎架即可,高度为300mm。
⑶构件按照顺序就位即可
八、检查、验收
8.1工程质量检查
为了确保工程产品质量符合标准要求,严格按照相关质量管理体系的要求对制作过程及成品质量进行检查,确认合格后按照检验批、分项工程报施工质量验收单位验收。
8.2产品检查
⑴.内部检查
在制作过程及构件制作完成后,以施工详图为标准,依据设计要求和《钢结构工程施工质量验收规范》(GB50205-2001)在公司内部进行检查,并形成检查记录后报监理工程师和总包单位。
⑵.构件的外形尺寸、焊接质量检查、构件外观质量检查应在构件镀锌前完成。
⑶.验收检查
验收检查是以中机重工内部检查记录为依据,接受专业监理工程师及总包单位、业主、独立试验机构等相关方的检查。
8.3焊缝的无损检测
⑴对设计要求的全熔透焊缝,公司内部应根据设计要求,依据《钢焊缝手工超声波探伤方法和探伤结果的分级》(GB11345-89)进行超声波检测或者磁粉检测。
⑵焊缝的无损探伤应形成超声波探伤记录应出具超声波探伤报告。
⑶焊缝的无损探伤检测人员应具备相应的从业资质,超声波检测设备应经国家认可机构鉴定合格并在其有效期内使用。