常减压操作规程DOC.docx
《常减压操作规程DOC.docx》由会员分享,可在线阅读,更多相关《常减压操作规程DOC.docx(260页珍藏版)》请在冰点文库上搜索。
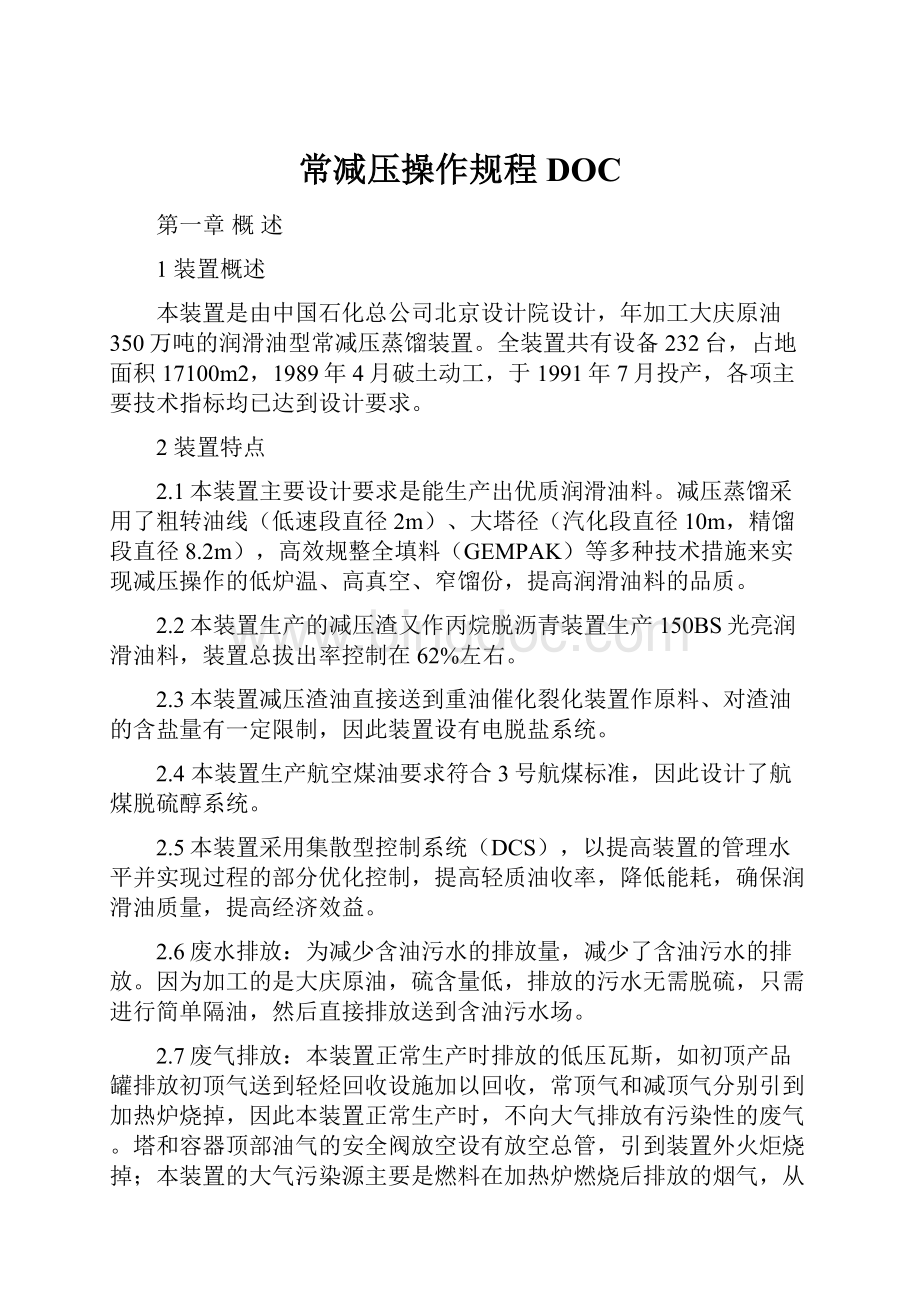
常减压操作规程DOC
第一章概述
1装置概述
本装置是由中国石化总公司北京设计院设计,年加工大庆原油350万吨的润滑油型常减压蒸馏装置。
全装置共有设备232台,占地面积17100m2,1989年4月破土动工,于1991年7月投产,各项主要技术指标均已达到设计要求。
2装置特点
2.1本装置主要设计要求是能生产出优质润滑油料。
减压蒸馏采用了粗转油线(低速段直径2m)、大塔径(汽化段直径10m,精馏段直径8.2m),高效规整全填料(GEMPAK)等多种技术措施来实现减压操作的低炉温、高真空、窄馏份,提高润滑油料的品质。
2.2本装置生产的减压渣又作丙烷脱沥青装置生产150BS光亮润滑油料,装置总拔出率控制在62%左右。
2.3本装置减压渣油直接送到重油催化裂化装置作原料、对渣油的含盐量有一定限制,因此装置设有电脱盐系统。
2.4本装置生产航空煤油要求符合3号航煤标准,因此设计了航煤脱硫醇系统。
2.5本装置采用集散型控制系统(DCS),以提高装置的管理水平并实现过程的部分优化控制,提高轻质油收率,降低能耗,确保润滑油质量,提高经济效益。
2.6废水排放:
为减少含油污水的排放量,减少了含油污水的排放。
因为加工的是大庆原油,硫含量低,排放的污水无需脱硫,只需进行简单隔油,然后直接排放送到含油污水场。
2.7废气排放:
本装置正常生产时排放的低压瓦斯,如初顶产品罐排放初顶气送到轻烃回收设施加以回收,常顶气和减顶气分别引到加热炉烧掉,因此本装置正常生产时,不向大气排放有污染性的废气。
塔和容器顶部油气的安全阀放空设有放空总管,引到装置外火炬烧掉;本装置的大气污染源主要是燃料在加热炉燃烧后排放的烟气,从烟气监测数据可知,其中不含SO2,NOX的排放量低于国家排放标准,对环境质量没有太大的影响。
2.8本装置无废渣产生。
2.9噪声:
经调查,该套装置的噪声污染主要来自加热炉火嘴、泵和风机的电机、空冷器风机。
加热炉火嘴在密闭的罩内操作,噪声低于85分贝。
空冷器风机选用VF-N型风机,叶片为宽叶片,低转速,噪声也在85分贝以下。
电机噪声,对于低于22KWYB型节能电机,其噪声也在87分贝以下,而高于22KW的电机,噪声大于85分贝。
近年来,我装置出于节能降耗方面的考虑,部分机泵改为变频泵,故机泵的噪声也大幅下降,大泵工作的场所均设置了带玻璃看窗的隔音室。
各隔音室内的噪声基本达到了GB12348-90《工业企业厂界噪声标准》中的有关标准。
操作人员除每小时巡回检查10-15分钟外,都在隔音室内检测,减轻了噪声对工人的危害。
对于装置内其他各类地点的噪声检测结果,均达到了GBJ87-85《工业企业噪声控制设计规范》中有关标准。
2.10本装置为降低能耗,采用了一系列先进技术使装置能耗控制在11.53千克标油/吨原油以下。
3装置组成
本装置主要有以下几部分组成:
电脱盐系统、初馏和常压系统、航煤脱硫醇系统、减压分馏系统、水除氧及蒸汽发生系统、加热炉烟气余热回收系统。
4原料来源
原油由大庆油田东油库、东二库和南Ⅱ-Ⅰ油库供给,东油库入我厂原油线,管线公称直径250mm,管线长13km,管线内存油550t,正常输油7000t/d,最大输油量可达9000t/d;南Ⅱ-Ⅰ油库入我厂原油线公称直径250mm,11.9km,管线内存油500t,正常输油7000t/d,最大输油量可达7500t/d,两条原油线最大可输送原油16500t/d。
油田在北油库附近设有原油计量站,进行原油计量。
两条输油线由东、南油库直接入我厂原油中间罐或输入原油稳定万米罐储存,经管线由东向西进入装置内泵-1/1.2处。
5主要产品及付产品
5.1主要产品:
初顶汽油、常顶汽油、常一线(航煤或分子筛料)、常二线、常三线、常四线、减顶油、减一线、减二线、减三线、减四线、减五线、热渣油、冷渣油。
5.2付产品:
初顶瓦斯、常顶瓦斯、减顶瓦斯。
第二章生产方法及工艺路线
1生产方法及反应机理
常减压蒸馏是原油加工的第一道工序。
本装置是根据原油中各组份的沸点(挥发度)不同用加热的方法从原油中分离出各种石油馏份。
其中常压蒸馏蒸馏出低沸点的汽油、煤油、柴油等组份,而沸点较高的蜡油、渣油等组份留在未被分出的液相中。
将常压渣油经过加热后,送入减压蒸馏系统,使常压渣油在避免裂解的较低温度下进行分馏,分离出润滑油料、催化料等二次加工原料,剩下减压渣油。
2工艺流程简述
2.1装置流程简述:
原油泵-1/1.2抽87单元11#.12#罐的原油,到装置内经过两路换热,到电脱盐罐经过脱盐、脱后原油从容-1出来经过四路换热后进入塔-经过闪蒸,塔-1顶出重整料,不凝气到炉-1烧掉或去原油稳定,塔-1底油经泵-2/1.2抽出,经过四路换热到310度后到常压炉被加热到365度左右出来进入常压塔第四层上方,经过常压塔精馏后,塔顶油汽经过冷凝冷却后的汽油一部分打入塔顶,一部分作为常顶汽油出装置,不凝气到常压炉烧掉,然后从上到下侧线依次馏出常一线、常二线、常三线,常四线直接被抽出。
其中并设有一个顶回流,两个中段回流(常一中、常二中),常底油经过泵-3/1.2抽出到减压炉加热到395度左右后进入减压塔第四层上方,减压塔底吹入蒸汽。
减顶设有两级抽真空系统,减顶油汽经过一级予冷器和一级抽空器和二级予冷器及二级抽空器,不凝气到常压炉烧掉,冷却下来的油水经减顶油水分液罐(容-6)分出的油经泵送出装置,减压塔沿塔壁至上而下依次馏出减一线、减二线、减三线、减四线、减五线,各侧线(除减五线)经过气提塔在由各泵抽出到各换热器进行换热,冷却最后送出装置,减压塔经过泵-21/1.2抽出。
经过两路换热,一部分热料去重催、焦化,另一部分经过冷却做冷渣送出装置。
2.2各岗位流程说明:
2.2.1常压岗位:
45℃原油从输转87单元11#、12#罐进装置,经原油泵-1/1.2分两路进行换热,泵前注入破乳剂。
注入量为占原油20ppm,浓度为2%。
一路原油与E-1(常顶气)换热到68℃;与E-2(常二线)换热到76.6℃;与E--3(减顶回流)换热到86.9℃;与E-4(减三线)换热到94.1℃;与E-5(常一线)换热到101.4℃;与E-6(减渣油)换热到120.3℃。
二路原油与E-14(常顶气)换热到68℃;与E-15/1~3(常顶循)换热到104.6℃;与E-16(常二线)换热到112.3℃;与E-17(减二线)换热到120.6℃。
两路原油混合换热后温度为120℃,注入冷凝水注入量为5%(占原油),经混合阀充分混合后,进入电脱盐罐(V-1),将原油中水和盐分别脱到0.1%(重)及2.5毫克/升以下。
脱后原油117.4℃分成四路进行换热,一路脱后原油与E-7(常二线)换热到138.2℃;与E-8(减二线)换热到152.6℃;与E-9/1.2(减三线)换热到169.5℃;与E-10/1~4(渣油)换热到239.8℃。
二路脱后原油与E-11/1.2(减一中)换热到162.7℃;与E-12/1.2(常二线)换热到203℃;与E--13/1.2(减渣)换热到239.7℃。
三路脱后原油与E-18(渣油)换热到137.8℃;与E-19(常四线)换热到153℃;与E-20(减四线)换热到173℃;与E-21/1.2(减二线)换热到202.9℃;与E-22(减二中)换热到222.7℃;与E-23(减三线)换热到240.3℃。
四路脱后原油与E-24/1.2(渣油)换热到140.1℃;与E-25(减五线)换热到125℃;与E-26(常三线)换热到172.2℃;与E-27/1.2(渣油)换热到194.2℃;与E-28/1.2(常二中)换热到231℃;与E-29(常四线)换热到239.1℃。
四路脱后原油升温到230℃合为一路进入初馏塔(C-1)汽化段。
原油在塔内闪蒸,从初馏塔顶馏出的油气约120℃,与采暖水(E-44/1~4)换热,(非采暖季节停用E-44/1~4),油气改走空冷(KN-5/1~5)油气冷凝到77℃,进入初顶回流罐(V-2)。
油气经分离后,液相用初顶回流泵(P-4/1.2)打回初馏塔顶作回流,其余油气继续由初顶空冷器(KN-1/1~3)、初顶后冷器(N-1)冷却到40℃,进入初顶产品罐。
液相用初顶产品泵(P-5)送出装置作重整原料。
气相经瓦斯分液罐(V-17)分液后送出装置回收轻烃。
当轻烃装置停运时,瓦斯引到本装置加热炉作燃料。
初馏塔第10层(或12层)用初馏侧线泵(P-6/1.2)抽出与常一中返塔管线合并送到常压塔第33层塔盘上。
初馏塔底拔头油,温度约为226℃,经初底泵(P-2/1)抽出再次分两路换热。
一路拔头原油E-30/1.2(常二中)换热到260.9C;与E-31(渣油)换热到270C;与E-32(渣油)换热到275.7C;与E-33(减四线)换热到279.9C;与E-34/1.2(渣油)换热到309.5C。
二路拔头原油与E-35/1.2(减二中)换热到251.5C;与E-36(渣油)换热到259C;与E-37/1.2(减二中)换热到276.4C;与E-38(常四线)换热到280.4C;与E-39/1.2(渣油)换热到309.8C;与E-53(减五线)换热到312.8C;
两路拔头原油换热到309C,然后分四路进入常压炉(F-1),经过对流和辐射炉管,加热到365C,后进入常压塔(C-2)进料段。
常压塔顶馏出的110C油气,与原油换热(E-1、E-14),油气冷却到86C进入常顶回流罐(V-4).经油气分离及分水后,液相用常顶回流泵(P-7/1.2)抽出打回到常压塔顶作塔顶回流.从V-4出来的未凝油气继续经空冷器(KN-2/1.2)和后冷器(N-2)冷却到40C,进入常顶产品罐(V-5),经分水后由常顶产品泵(P-8)送出装置作为轻裂解料,不凝油气送到F-1作燃料气。
常压塔设有47层塔盘及一个常二中填料段,顺次从第34层、23层、15层(或13层、11层)及第9层(或第7层)抽出常一线、常二线、常三线、常四线、,抽出温度分别为170C、260C、322C、345C,其中常一、二、三线分别进入常压汽提塔(C-3)的上、中、下段进行汽提,汽提出的轻组分分别返回常压塔.常一线汽提是用常三线作重沸器热源、常二、三线用蒸汽汽提。
常一线泵(P-9/1.2)从汽提塔抽出常一线油,经与E-5(原油)换热到130C注入少量空气后送入内部装有13X铜分子筛的脱硫醇反应器(反-1/1.2)进行脱硫醇反应.经过脱硫醇后的常一线油顺次通过与E-41(伴热水)换热及KN-3,冷却到45C后进入脱硫醇中间罐(V-14),再用航煤脱硫醇泵(P-30/1.2)抽出.经过航煤脱色罐(V-8/1.2),玻璃毛过滤器(滤-1/1.2),和陶瓷过滤器(滤-2/1.2)送往装置外3#航煤储罐.
常二线泵(P-10/1.2)从汽提塔抽出常二线油,依次经E-12/1.2、E-7、E-16、E-2(原油)换热后,进入空气预热器(KY-1),与加热炉燃烧用的空气换热,然后送出装置.在开工期间,KY-1未启用时,常二线油也可走空冷器(KN-4/1.2)冷却到60C送出装置,作为轻柴油.
常三线泵(P-11/1.2)从汽提塔抽出常三线油,经过E-40(常三热虹吸重沸器)提供汽提热源,然后与E-26(原油),E-42(除盐水),E-45(伴热水),再经冷却器(N-3)冷却到60C送出装置,作为75SN中型润滑油料。
常四线泵(P-12/1.2)从常压塔第9层(或第7层)抽常四线油,先与E-38、E-29、E-19(原油)、E-46(采暖水)换热,然后经冷却器(N-4)冷却到70C,送出装置,作为催化裂化原料。
为了取走全塔的过剩热量,常压塔设有:
顶回流,顶循回流,常一中,常二中,取热比例:
10:
20:
35:
35.
顶循回流从第44层经常一中泵(P-13/1.2))抽出,温度为132C,经与E-15/1~3(原油)冷却到83.8C,返回塔46层塔盘上。
常一中从31层塔盘经常一中泵(P-14)抽出,温度为204C.经与蒸-1、蒸-3换热发生P=1.0MPa及P=0.4MPa的蒸汽后温度降为154C返回常压塔33层塔盘上。
常二中从第22层塔盘经常二中泵(P-15/1.2)抽出温度为288C,与E-30/1.2、E-28/1.2(原油)换热,温度降为154C返回常压塔常二中填料段上部.
常压塔底油温度为355C.用常底泵(P-3/1.2)抽出,分四路送入减压炉(F-2),在辐射段入口注入P=1.0MPa的蒸汽约1530kg/h,经加热到395C,进入减压塔(C-4)的进料段进行减压蒸馏。
常压塔底油温度为355C,用常底泵(P-3/1.2)抽出经过炉-2加热到395C,进入减压塔(C-4)的进料段进行减压蒸馏。
2.2.2减压岗位
减压塔按湿式蒸馏设计.塔底吹入汽提蒸汽,减二、三、四用蒸汽汽提,以保证产品的闪点合格并适当调整馏分宽度。
减压塔顶出来的油气55C、3.33KPa先进入予冷器(N-5/1~4),将大部分蒸汽及可凝油冷凝下来,予冷器采用12C深井水冷却,从予冷器出来的未凝油气和蒸汽为19.5C,进入一段蒸汽喷射器(抽-1/1.2)由2.53KPa增压到16.80KPa进入一级冷凝器(N-6/1.2),N-6/1.2的冷却水是利用N-5/1~4排出的深井水,从N-6/1.2出来的32C的不凝气和水蒸气进入二级蒸汽喷射器(抽-2/1.2),增压到106.66KPa,然后进入二级冷凝器(N-7/1.2)中将大部分蒸汽冷凝下来,不凝气引到加热炉烧掉.在予冷器,一级冷凝器和二级冷凝器中冷凝下来的凝缩油和水,通过大气腿流入减顶分水罐(V-6)中进行油水分离,分出的减顶油用顶油泵(P-24/1.2)送出装置作柴油组分.减顶分水罐排出的水排入含油污水管网及电脱盐注水泵(P-25/1.2)入口做电脱盐注水。
减一线油130C,从减压塔顶部填料段下面的集油箱中抽出,用减一线泵(P-16/1.2)抽出.经过E-3(原油),E-43/1.2(除盐水)换热后分成两路.一路做为减一线油送出装置做裂化原料;另一路继续经冷却器(N-8),冷至50C,返回减压塔顶做减顶回流。
减二线油270C,从减压塔第13层(或15层)塔盘馏出进入减二线汽提塔.汽提出的轻组分及水蒸汽返回减压塔.汽提过的减二线油用减二线油泵(P-17/1.2)抽出,依次与E-21/1.2、E-8、E-17原油、E-51(采暖水)换热,最后经冷却器(N-9)冷至60C送出装置作200SN(或150SN)润滑油料。
减三线油338C,从减压塔第5层塔盘馏出,进入减三线汽提塔,汽提出的轻组分及水蒸汽返回减压塔,汽提过的减三线油用减三线泵(P-18)抽出,与E-23、E-9/1.2、E-4(原油)换热后,进入冷却器(N-10)冷至60C送出装置,作500SN(或400SN)原料。
减四线油358C,从减压塔净洗油填料段下面的集油箱馏出,进入减四线汽提塔,汽提出的轻组分及水蒸气返回减压塔.汽提过的减四线油用减四线泵(P-19/1.2)抽出,大部分返回减压塔,通过喷头喷在净洗填料段的上方做为净洗油;另一部分依次与E-33、E-20(原油)、E-47(采暖水)换热,最后进入冷却器(N-11)冷至60C送出装置,作为650SN(或150料)原料。
减五线油370C,从减压塔靠近汽化段之上集油箱流入减五线中间罐,再用减五线泵(P-20/1.2)抽出,分送两处.一路作为过汽化油返回到常压塔底泵(P-3/1.2)入口,经减压炉返回减压塔汽化段;第二路经E-53(拔头油)、E-25(原油),进入冷却器(N-12)冷至90C送出装置,作为催化裂化原料.
减压塔底渣油370C,从减底油泵(P-21/1.2)抽出,分两路与原油换热,一路为E-39/1.2、E-31、E-10/1~4、E-18;另一路为E-34/1.2、E-32、E-36、E-13/1.2、E-27/1.2换热后两路合并温度为160C,分出少量作为本装置的自用燃料供F-1、F-2使用,其余大部分继续与脱前原油E-6换热,接着与E-48换热(脱盐注水)换热,E-50(采暖水)换热后渣油温度为98C,可直接送出装置.非采暖季节,采暖水换热器停用,渣油改走冷却器(N-13/1.2)冷至98C送出装置作催化裂化料.减压渣油在与电脱盐注水换热后温度为125C,直接分出一部分送至焦化装置。
减压塔设有两个中段回流,减一中用泵(P-22)从第18层塔盘抽出,温度为214C.经蒸-2/1.2中发生P=1.0MPa蒸汽之后,再与E-11/1.2(原油)换热温度为300C与E-37/1.2、E-35/1.2、E-22(原油)换热后温度降为236C,返回减压塔第11层塔盘上。
为了减轻初馏塔,常压塔和减压塔塔顶部馏出物对设备和管线的腐蚀并使初顶油,常顶油腐蚀检验合格,本装置设有塔顶注水泵(P-26/1.2)向上述三塔顶注水注氨。
本装置设有仪表冲洗油泵(P-32)一台,从航煤脱硫醇中间罐(V-14)抽出部分常一线油作仪表冲洗油.
2.2.3司炉岗位
加热炉:
拔头油经换热到309C,分四路进入炉-1对流室,从对流室下来到辐射室上方出来被加热365C,去常压塔蒸馏。
常压重油355C经泵-3/1.2到炉-2对流室下部然后到辐射室,最后从辐射室上方出来到减压塔蒸馏,减压炉对流室还分别给1.0MPa蒸汽和0.4MPa蒸汽加热,中间1.0MPa蒸汽,上下0.4MPa蒸汽,分别加热到250C、400C,分别作为加热炉烧火蒸汽、消防蒸汽、减压抽真空蒸汽及各塔吹汽,炉-1.2用的燃料油是本装置的减压渣油经换热,从E-6/1.2阀前160C经过控制阀PRCA-502.一路:
经过炉-1油表FQ-503和控制阀PRC-103到炉-做烧火燃料,另一路经过炉-2油表FQ-504和控制阀PRC-129到炉-2做烧火燃料,多余燃料经过回流油表F-1(FQ-505)、F-2(FQ-506)、最后合走返回到塔-4下部。
炉-1.2烧火用的燃料气(高压瓦斯)是从气体分馏一车间来到装置内E-52/1加热后到容-12高压瓦斯罐脱油、脱水出来经过总压控PRCA-502分二路.一路经过炉-1控制阀FRC-123去炉-1做烧火燃料,另一路经过炉-2控制阀FRC-209去炉-2做烧火燃料。
从容-3出来的不凝气(低压瓦斯)经过E-52/2加热到容-17脱油、脱水后,一部分到原油稳定做乙烯原料,另一部分和熔来的不凝气合走到加热炉低压瓦斯火嘴烧掉,炉-1还有一个真空火嘴烧的是从减顶来的不凝气体.
烟气余热回收系统流程:
从常、减压炉排出的大约300~380C热烟气,经过顶部烟道,进入重合烟囱的一侧下行,进入双向翅片空气预热器(空予-2)与空气换热,烟气温度降到160C,被引风机抽出送入重合烟囱的另一侧排空,空气经吸风道被鼓风机送到热油式空气预热器(空予-1).再进入翅片管空气预热器.被预热约230C,分别进入常、减压加热炉燃烧器供火嘴燃料燃烧用.
3工艺流程图和物料平衡图
3.1带控制点的工艺流程图(见附页)
3.2装置物料平衡图
物料平衡(年开工8000小时)表3-1
序号
物料名称
收率%重
数量
备注
千克/时
吨/日
X104吨/年
1
2
3
4
5
6
7
一
原料
1
原油
100.00
437500
10500
350.00
2
含水
0.06
263
6.3
0.21
3
合计
100.06
437763
10506.3
350.21
二
产品
1
初顶气
0.35
1513
36.31
1.225
去原油稳定装置
2
常顶气
0.05
219
5.26
0.175
瓦斯去加热炉
3
初顶油
4.0
17500
420
14.0
重整原料
4
常顶油
2.0
8750
210
7.0
加氢裂化料
序号
物料名称
收率
%(重)
数量
备注
千克/时
千克/时
千克/时
5
常一线
6.8
29750
714
23.8
3号航煤
6
常二线
14.5
63438
1522.51
50.75
0#柴油,生产-10#柴油时收率9.5%
7
常三线
4.0
17500
420
14.0
75SN或重柴油
8
常四线
4.2
18375
441
14.7
生产-10#柴油时催化料收率9.0%
9
减顶气
0.05
219
5.26
0.175
瓦斯去常压炉
10
减顶油
0.15
656
15.74
0.525
柴油组分
11
减一线
4.6
20125
483
16.10
裂解料生产150SN+400SN时收率3.3%
12
减二线
11.0
48125
1155
38.5
200SN或150SN
13
减三线
5.5
24062
577.49
19.25
500SN生产400SN时收率7.0%
14
减四线
3.7
16188
388.51
12.95
650SN生产150SN+400SN时收率3.5#
15
减五线
1.8
5687
136.49
4.55
催化原料
16
减渣油
37.8
165393
3969.43
132.3
去焦化、重催、动力站装置
17
合计
100
437500
10500
350.0
三
拔出统计
1
轻质油收率%
27.3
119438
2866.51
95.55
计算到常二线
2
最大中性润滑油收率%
24.2
105875
2541
84.7
3
常压拔出率%
35.5
155313
3727.51
124.25
4
减压拔出率%
26.25
114843
2756.23
91.875
5
总拔出率%
61.75
270156
6483.74
216.125
第三章工艺技术指标
1原辅材料
本装置加工原料为大庆原油,其主要元素是碳、氢、氧,其中碳的含量占83-87%,氢含量占11-14%,两者合计达96-99%,其余的硫、氮、氧及微量元素总共不过1-4%。
2三剂使用
2.1催化剂
本装置生产的航煤馏分按3号航煤规格设计,大庆原油馏出的航煤馏分,硫性硫含量在12-20PPM之间,因此需要经过脱硫醇工序,本装置采用国内已成熟的13X铜分子筛氧化脱硫醇工艺,使航煤馏分在130℃,反应空速为3时-1(重时空速)下,通入少量空气进行氧化脱硫醇,脱硫醇后,为使产品消光值达到<0.02的要求或赛比≥25,还需要经过脱色罐脱色,罐内装有活性碳。
产品经过玻璃毛过滤器和陶瓷过滤器过滤后送出装置。
装置使用催化剂型号:
13X铜
使用催化剂规格:
Ф4.5×5
使用地点:
反应器-1/1.2
填装量:
15.7M3
2.2破乳剂
本装置设有电脱盐系统,其原理是原油在一定的温度下,注入20x10-6(占原油)浓度为2%的破乳剂、水5%(占原油)在混合器的作用下使其充分混合,进入一定容积的容器内,在高压电场的作用下,原油中的小水滴聚结成大水滴,靠油水密度差将原油中的水和溶解在其中的盐同时分离的过程。
常减压装置加工出来的二次加工原料中要求含盐量≯5.0mg/l。
3产品及付产品的性质、用途规格去向
初顶瓦斯走低压瓦斯线,去原油稳定,做乙烯原料,另外V-17(低压瓦